So give maniflow a ring, you'll pay less on postage toowould you ever sell this exhaust as this is what i want to do, but i dont have the time ...
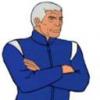
1962 Mk1 Rebuild
#211
Posted 03 June 2012 - 03:16 PM
#212
Posted 03 June 2012 - 03:27 PM
So give maniflow a ring, you'll pay less on postage too
would you ever sell this exhaust as this is what i want to do, but i dont have the time ...
the cut of valve one? you can buy them ready made??
thanks
#213
Posted 03 June 2012 - 03:43 PM
#214
Posted 03 June 2012 - 05:39 PM
if you read the post you quoted..... he had it made by them
It wasn't modified my Maniflow it was modified the Nobel specialist who sorted the cooling and exhaust systems for him.
#215
Posted 03 June 2012 - 07:46 PM
That way, you can start up and drive quietly to work without irritating everyone, then come home again with a super loud exhaust, never been able to find a bypass valve though!
#216
Posted 28 October 2012 - 11:54 PM

It took a long time at the bodyshop but then again, this car needed extensive work. Lots of sheetmetal replaced - front fenders, inner wings, front panel, rear quarters, rear valence, and door skins.
The quality of the paintjob is pretty high:

I wanted to do a bright green (seriously considered 70's Porsche Viper green at one point) but finally settled on this.

Now onto the final assembly....
#217
Posted 29 October 2012 - 10:06 AM
#218
Posted 29 October 2012 - 03:22 PM
#219
Posted 10 December 2012 - 12:41 PM

#220
Posted 10 December 2012 - 12:47 PM
#221
Posted 10 December 2012 - 03:44 PM
Funny you should ask. Let's begin with the re-assembly....Love it, any more updates?
The first step was to prepare my workspace. I now had a 2-car garage but still no good workbench. Just before the Mini returned I resolved to change that by designing and building my own workbench/welding table. I'm tired of working on the floor! I don't plan to work on anything too large and since space is at a premium I settled on a 4'x2' countertop of 1/2"-thick steel. I picked up a lot of good ideas for the design from the Miller welding forum and designed the thing in Solidworks. I was pleased to find some adjustable leveling casters that can also act as permanent solid rubber feet. It took a few more weekends to build than I planned but the thing is great. I should have made one years ago.




With the workbench complete and the garage cleaned up, I got the Mini up on jackstands and removed Nick's trolley. Now the real work could begin, kinda. I'm actually holding off on going all-out until I have a vendor come look the car over as-is. I am currently looking for a car-wiring expert who can assist in the design and build. I figured it would be easier to have everything disassembled when they come to look the car over. Hopefully that will happen soon. In the meantime I am doing everything else that I can, even if it is just little stuff:


One of the next items and one that seemed like it would be a slamdunk was to install the radiator fan into the lefthand inner wing duct. Since Nick installed a set of new inner wings (and front fenders and front clip), there was now a grid of painted steel bars in the way, whereas before there was nothing.

I tried to just trim out the center to make way for the motor to protrude through into the left front wheel well. That still wasn't enough so I had no choice but to remove the entire grid. Don't worry - I painted and sealed any sheetmetal I cut. I didn't spend this much time and money to let this car start rusting away without a fight.



Here you can see the door card has been installed along with the kickplate, door latch mechanism and the door pocket trim.

The door check strap is installed on both sides now.

Next came the headlight mounting rings which are normally secured with screws. I'm not a big fan of using screws on sheetmetal. I know they work well enough but it seems like a great way to break through the paint and let rust get a foothold. During the initial build-up of the car I switched to nuts and bolts in a number of locations including here. Simultaneous access to both sides of the fasteners can be tricky so I've decided to go with rivnuts wherever possible.

A rivnut is 'permanent' nut that you distort into sheetmetal holes. Once installed you don't need to prevent the nut from spinning. Just install the bolt and you are done.

Here's the installation tool. The process is similar to traditional riveting.

The end result is clean and easy to work on.

I used rivnuts here to mount the rectifier/regulator to the front firewall.

Now on to the front subframe. My Mini is an early one and would normally rely on the twin sets of small bolts to secure the tops of the turrets to the front bulkhead. That's not so easy on this car now since the rollcage was installed. The bar passes right over the top of the outer bolt hole. I've resorted to this:

I've drilled out the bolt holes in the center of the subframe turret to accept a Grade 8, 5/8" diameter bolt. I drilled out the bulkhead to allow use of the spacer made from steel tubing. This will prevent crushing of the bulkhead. I then fashioned spreader plates/washers for top and bottom. And just for good measure I'm using the normal small bolt on the inside hole. Can't hurt, right?


Speaking of the front subframe, here you can see my incredibly rusty example. I had Gerald Dale in the UK build this one for me. He included all this usual strengthening tricks and lightens it in a few areas. I asked him to not bother powdercoating it since I have some more mods to do to it. It sure looks ugly in the meantime.

I did a test install and without the weight of the engine in it, the bolt holes in the turrets failed to line up with the bulkhead holes. Nothing is ever easy on this car. After some headscratching I finally enlarged an existing hole on either side of the turrets and inserted a length of 1/2" allthread. With a few turns of the nuts I was able to flex the turrets apart just the few fractions of an inch needed. Hopefully that won't be necessary when the R1 engine is in place.

Although I had the entire exhaust coated in a black ceramic material last year, the header got completely scratched up during the run-up to the first drive. I had the header redone by Jet-Hot and although they claim reduced underhood temperatures and a bit more power, I did it to increase the life of the thing. It is a custom piece and therefore not easily replaced. And since it came from England I can only assume it would rust at any moment if left untreated.

This shot just shows off a nice detail that Nick handled for me. He smoothed out the transition from the lower dash panel where it meets the rollcage front downtube. It almost looks like the car came this way from the factory.
Edited by Joe250, 10 December 2012 - 03:53 PM.
#222
Posted 10 December 2012 - 07:30 PM
#223
Posted 11 December 2012 - 11:43 AM
#224
Posted 11 December 2012 - 01:26 PM
I had a question about the exhaust tho, what is the bypas valve and pipe part of the exhaust for?
Edited by freshairmini, 11 December 2012 - 01:26 PM.
#225
Posted 11 December 2012 - 03:52 PM
Your mini is amazing. The quality of paint job is literally the best I've ever seen, proper mile deep shine and a brilliant blue!
I had a question about the exhaust tho, what is the bypas valve and pipe part of the exhaust for?
Thank you for that. Nick did a really nice job on the paint. I'm being extra caution working around the car now. Don't want any dings or scratches.
Driving around town I want the car to be reasonably quiet. The bypass valve will normally be closed, so all the exhaust will be forced through the muffler, keeping exhaust noise to a minimum. When I am at the track or out driving in the canyons and having fun, I can use the electronic controller in the car to open the valve as much as I want. This will allow most of the exhaust to skip the muffler and go straight out the RH pipe. That will give slightly more power and a better sound.
1 user(s) are reading this topic
0 members, 1 guests, 0 anonymous users