My learning curve into sheetmetal bodywork continues..................................
Decided to have a go at tidying the scuttle repair I did yesterday. No matter how hard you try, how good your fit-up is, or how slow you mig thin sheet together it always has a mind of its own when it cools I find. Even with the spot weld back & forth technique.
After the scuttle was mig'd in it left a nasty raised seam on the weld. I ground back flush , but it could still be felt, so I did a bit of Googling on mig weld finishing, metal shrinking, panel beating etc, and stumbled accross this
http://www.wolfesmet.../sdiscdemo.htmlSo to cut a long story short, I knocked one up out of a bit of stainless I had lying around and gave it a wurl !!
Takes a bit of practice and a bit of fiddling with the panel beating tools but it seems to work. I'm very happy with the results and the repair panel looks / feels good. A light skim of filler should sort any imperfections out.
Only drawback is the noise. Jeees its loud. Metal on metal at 20,000 rpm. Best not do it when your neighbour is working nightshift. I had earplugs in and muffs over the top
Enjoy................
Here we go, DIY shrinking disc
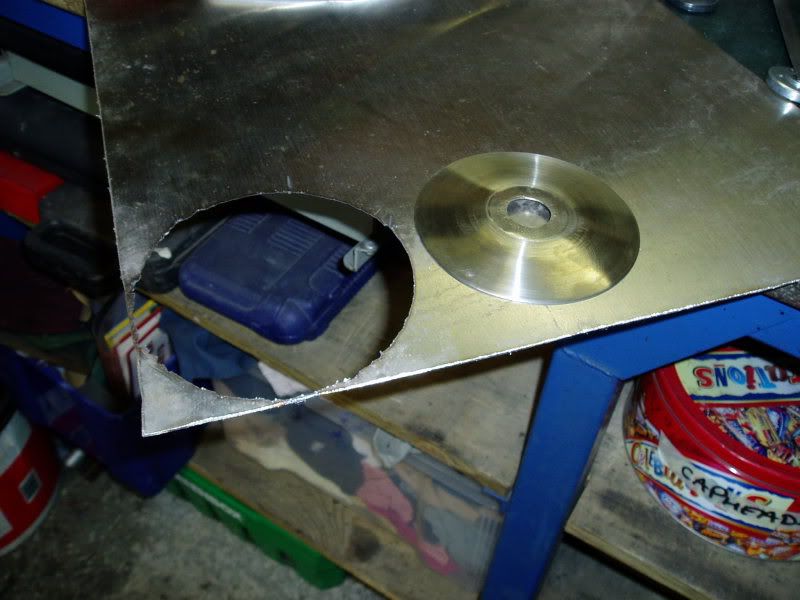
Ready for action
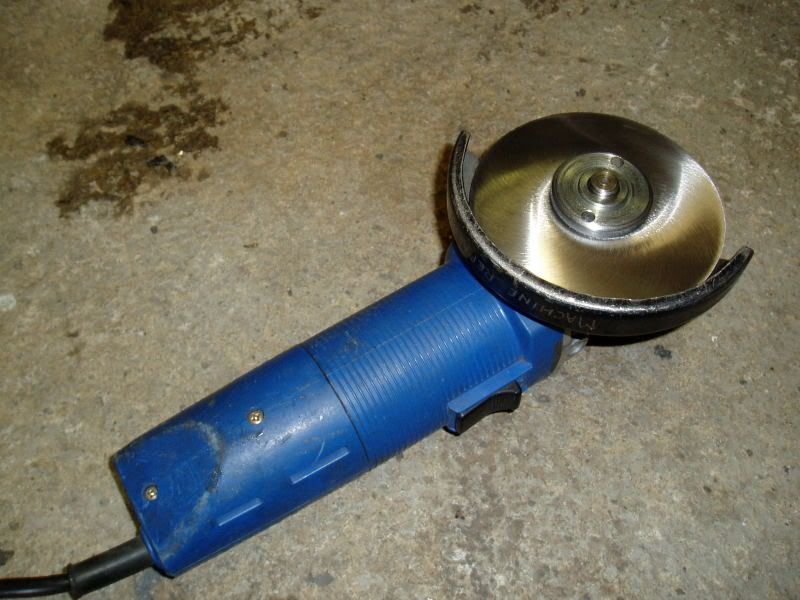
All primered up to keep the rust at bay, with no filler yet ! A few minor imperfections to fill when the time comes and it should sorted.
Edited by lchris21, 27 April 2009 - 03:35 PM.