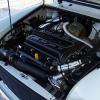
WARNING..... Welding on an SPi/ MPiCar??
#31
Posted 24 November 2013 - 11:31 AM
How would you remove the airbag without cutting the pore by removing the battery?
Basically, I'm picking up an MPI tomorrow and I will be welding on it - we don't seem to have any kind of definitive do or don't here.
#32
Posted 24 November 2013 - 11:48 AM
#33
Posted 26 January 2017 - 01:38 PM
I work as a design engineer for a major manufacturer of ECUs. You WILL NOT kill an ECU by welding as long as its connector(s) are all unplugged. You don't have to physically remove the ECU from the vehicle, and if the ground wire is the only remaining connection, that is ok.
But you MAY kill the ECU by welding if it remains plugged in to the wiring loom. You MAY kill the alternator if that remains connected. Same for stereo system and any other electronic bits.
Removing the battery or fitting a spike suppressor across it GIVES NO PROTECTION WHATSOEVER. The battery can absorb spikes due to welding on its own, and that is not the way that the ECU gets damaged.
Short of not taking precautions to avoid electrostatic charge damage (ESD), poking wiring with the welder, or applying random voltages to the pins to see what happens, there are 3 ways, maybe 4, in which an ECU will be killed, depending on the design of the ECU.
One is by induced high voltage spikes in its wiring, especially from the starting circuit in a proper TIG welder. MIG tends not to produce fast enough spikes to couple much energy into the wiring. If the ECU plugs are disconnected, with or without the earth, this can't happen.
The second is by pulling inputs below ground, as seen by the ECU, which is why the ground wire must always be connected to the most negative part of the system. Remove it alone at your peril. It should ideally NOT be sharing a ground with other things. This condition may happen due to voltage drop through the shell when welding. If the inputs are disconnected by removing the connectors, this can't happen.
The third is by energising sensor inputs with the ECU power off. Can happen but not due to welding per se. Most likely due to inept efforts at "improving" the electrical system.
The fourth, in some cases which are design dependent, is by accidental short of a sensor ground line to a voltage such as the battery. The sensor grounds generally run back to the ECU to achieve accuracy, and a significant imposed voltage will send a high current to ground and melt the tracking on the PCB. Best quality modern ECUs have protection against this condition, but only when the ECU has power applied, because the grounds actually run through low resistance MOSFET switches, which are promptly turned off if high current is detected, and doing that needs power. You can make this protection fail by connecting spurious grounds to the sensors, so don;t ever mess with sensor grounding to try to improve something. Even if you don't blow up the ECU, you will make the sensor less accurate. Not a problem if all ECU connections except ground are removed.
In view of the risk of ESD damage on older, less well designed ECUs, as we are discussing here, it is actually best to handle it as little as possible and just pull out the connectors before welding, having first disconnected the battery.
Disconnecting the battery should NEVER fire an airbag, but modern cars require that you wait 5 minutes after battery disconnection, with the negative lead secured well back so it can't spring back and make contact, before doing any work whatsoever on the airbag system. If you don't wait 5 minutes there may be sufficient charge on the firing capacitor to set it off, and it is certain that in normal handling, removed from the car, the g force needed for actuation will be exceeded and it will go off. Also, NEVER have anyone in the car or within reach of an airbag, e.g. reaching through an open door or window, while the battery is reconnected. I would strongly advise removing all pyrotechnics before welding.
#34
Posted 26 January 2017 - 04:59 PM
So here we are again, churning through an old thread which i'm sure by now someone on this forum would have commented about a fried ECU, blown Airbag etc through welding.
Show us 100% verified proof that welding a car with multiple airbags or even just one, plus cars with multiple ECU, CCU's etc will damage these items. And i mean with them electrically connected, not disconnected.
I have lost count of the cars i have welded with multiple airbags, computers etc. Not one, not a single one has had issues.
As i have previously said our aircraft do get struck by lightning which carries tens of thousands of volts. None of the aircraft computers are affected by said lightning strikes. This also includes our Upper Class seats which are all fitted with Airbags. The only damage i have ever seen in over 37 years of working in the industry is burnt skin, fasteners, damaged Radomes.
On simpler cars like a mini you can get easy access to the battery and alternator so disconnect them. I did this simple task on an SPI but left the ecu connected. Not any issues with that little car after all of the welding i carried out.
Now please anybody at all on this forum or another (please supply a link) that has suffered a defined failure due to welding being carried out on the car, feel free to post on here.
#35
Posted 23 May 2017 - 08:13 PM
better to be safe than sorry ,and im welding a spi ecu all removed
#36
Posted 28 May 2017 - 10:06 PM
Neil, I have designed avionics and know precisely why they do not fail during a lightning strike, or simulated strike to which they are tested. It is because I did my job properly, and the customer could stand the cost. I am now involved in the design of engine ECUs and know the conditions under which they certainly will fail, which is because the protection is only there for ESD during handling, and alternator load dump, nothing else, because that is all that the customer will pay for, and the design team are not allowed to do the job properly.
In temperate climates an airliner is struck by lightning once a year on average, and some of the time the crew do not even know. But the energy coupled into the avionics boxes is far less than what you can get with an unfortunate disposition of ECU, battery and engine grounds and TIG or MIG welder. The welder will kill the ECU by a sustained voltage drop of the wrong polarity, even slightly under a volt, but the lightning strike is, per pulse, almost all over in 200 microseconds or so, although there have been on record strikes of up to 23 consecutive pulses about 100 milliseconds apart, which is what we tested the avionics to.
There is another complication with lightning, between short sharp pulses of 100000 amps there is a fairly steady background current of maybe 100 amps for the entire duration of the sequence. That is what kills people, 100 amps for half a second and you are well and truly dead, usually. The high peak current funnily enough does not in itself kill people, but it would kill avionics if the transient voltages it induces in the wiring were not clamped by Tranzorbs. The 100 amps is a slow waveform and does not couple well into the avionics, so it has no real effect there, which is fortunate as a passive device like a Tranzorb has insufficient energy capacity to deal with it.
An engine ECU will handle the alternator load dump voltage, but only just, on its power terminals. There is generally negligible margin between the peak load dump and the voltage at which component overstress occurs, in fact some designs are pushed so far that components are stressed beyond their ratings and it is merely because they come out of the factory slightly better than spec that the ECU survives. You don't do that in avionics, unless you are Thales, where I was truly shocked to see that they were habitually overstressing components during a lightning strike.
100 amps, or even 20 to 30 from a MIG welder set for thin sheet, of stray current down the wrong ground path for less than a second, and most ECUs are toast. Automotive tat, for that is all that it is, to the disgust of engineers who have to make it so, is many orders of magnitude more vulnerable that properly designed avionics to any form of electrical disturbance other than the very simple threats that it has been designed to withstand. Working for an ECU manufacturer, I know for a fact that modern ECUs are regularly wrecked by people doing daft things on the vehicle, such as jump starting wrongly or welding. The same ECUs are supplied to the US market, where even large trucks use a 12V system, for no comprehensible reason, and they are destroyed more frequently in the lower voltage environment, partly because the starter motor current is very high indeed and there is a serious amount of voltage drop along the battery negative lead.
I am not making this up by the way. Right now (well, before and after the bank holiday) there is an on-going argument with the designer in Luxembourg, because we have identified certain features in the very latest ECU which make it very vulnerable indeed.
So, speaking as one who has deep inside knowledge of both areas, I can state, without fear of being proved wrong, that an automotive ECU can never be regarded as electrically robust, unlike the average avionics box, and should always be unplugged from the harness before welding is carried out. There is however never any need to unbolt it from the vehicle unless it is at risk from sparks or hot metal.
#37
Posted 28 May 2017 - 11:44 PM
They do not avoid storms, just fly straight through them. The most amount of strikes we had to map on one aircraft in one day was 91. The following day I had three A319's in all with multiple strikes. That contract was not one week without us carrying out damage mapping due to lightning strikes and yes over that period the same aircraft. One of many. So there you go with that.
As to ECUs frying when welding has been carried out, I will stand by my statement that as of yet I have not had one ECU die because I have been welding the vehicle in question.
SPI's, BMW,s, Vauxhall,s, VW,s. Not one with any issues.
Any I will not go on with this as it's going round and round. You do your thing I will stick with mine.
#38
Posted 15 March 2018 - 06:03 AM
1. Remove the earth wire to battery and wait 30 mins, we were told that any electrical current would dissipate while waiting
2. Remove steering wheel airbag and store in a cupboard
The truth in reality
1. Earth wire removed waited 5 mins then airbag removed and stored in car.
When car had been repaired earth battery lead re-attached and driven over to repair department to be resprayed
The car would then be retrimmed.
All the years that I worked there no airbag or ecu was ever damaged or deployed through welding.
Amps stamps
Volts jolts
Edited by The Golden Shot, 15 March 2018 - 06:09 AM.
#39
Posted 06 October 2018 - 07:45 PM
Also I disconnect my battery every day will this do any damage I.e to the airbags or seatbelt tensioners ?
1 user(s) are reading this topic
0 members, 1 guests, 0 anonymous users