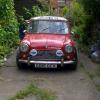
Make Sure Your Core Plugs Are Tight! I Learnt The Painful Way
#1
Posted 12 April 2025 - 09:11 PM
Really embarrassing story to tell, but I don't want anyone making the same mistake
Basically I rebuild an A series engine with the domed freeze/core water plugs. I tapped them in with a drift denting the middle and the seemed to hold fine. I had also added ATV silicoln sealant to the lip
Getting my engine running at 2500rpm with the engine at full temperature, a core plug shot out sending a blast of high pressure scalding coolant all over my bare legs.
Thought I'd be OK, but
Ended up having quite badly blistered legs and needed a fair bit of medical attention.
Having inspected the core plug. It seems I have dented the outside but this hadn't actually made enough of a deformation to secure the plug fully.
So please, give yours a good solid wack home. And make sure those buggers are in tight.
First time doing this for me and I've learnt the hard way.
I just feel so so lucky neither of my kids were standing in front of the car. Doesn't bare thinking about.
Cheers, Luke
#2
Posted 12 April 2025 - 11:00 PM
I hope you pull up OK for this injury.
They do need a few carefully placed hits, belting them actually doesn't expand them, they need to be almost flat.
I clean the recesses in the block very carefully and check them for scores etc, otherwise while they may go in tight, they'll leak.
I also use Loctite 243 (yes, it's a thread locker) on them before fitting as 'insurance' that they won't leak or dislodge.
#3
Posted 12 April 2025 - 11:35 PM
Mine was OK for 4 years and then popped out in a national park where there was no phone reception. Luckily I had a few mini friends with me or I'd have been in for a longer day
#4
Posted 13 April 2025 - 08:02 AM
Thanks for sharing
#5
Posted 13 April 2025 - 09:02 AM
Shooter
Attached Files
#6
Posted 13 April 2025 - 06:11 PM
I hope you pull up OK for this injury.
They do need a few carefully placed hits, belting them actually doesn't expand them, they need to be almost flat.
I clean the recesses in the block very carefully and check them for scores etc, otherwise while they may go in tight, they'll leak.
I also use Loctite 243 (yes, it's a thread locker) on them before fitting as 'insurance' that they won't leak or dislodge.
Thanks Spider,
Could've been a lot worse and definitely a learning point. I'll have to have a look at that loctite, I was tempted to get some for my 3rd motion shaft bearing but never did. Could've killed 2 birds with one stone there.
#7
Posted 13 April 2025 - 06:12 PM
Mine was OK for 4 years and then popped out in a national park where there was no phone reception. Luckily I had a few mini friends with me or I'd have been in for a longer day
Wow that's some heat isn't it!! How was the head gasket after that? Did anything warp?
#8
Posted 13 April 2025 - 06:13 PM
I'm glad you are sort of OK, when I put new core plugs in a recent small bore build I deliberately sort out some brass core plugs from an online company as I presumed they would be softer, as others have said I used a wire brush in a drill to make sure there was good clean fresh metal, I used Hylomar core plug sealant, I used a large ball peen hammer as a dolly hit with another hammer to make the dent, then a socket to flatten out the outer edge.
Shooter
Thanks shooter
I'll invest in a better ball peen I think. That's a great idea, thanks for the tip. If only I'd have seen this picture first haha. Mine didn't look anywhere near like that.
#9
Posted 14 April 2025 - 09:57 AM
i had the same thing on my volvo engine, and it was built by a so called professional! I used chemical metal on them. Been ok for 2 years now. Hylomar is probably the better one.
#10
Posted 14 April 2025 - 10:14 AM
ouch! hope you heal up quick mate
1 user(s) are reading this topic
0 members, 1 guests, 0 anonymous users