About to replace a sill. Atm I dont have access to a spot welder so i will probably have to drill and plug weld.
For the outer lip I see that the most common is to drill the sill and plug weld from the buttom up.
However, I cam across a YT vid shoing someone drilling the lip and plug welding from the top. Looked easion as one is not welding!"upwards" Thoughts?
Or should i splurge on a Vevor cheapo spot welder? Will still have to plug weld som areas as a spot welder wont reach.
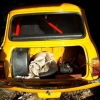
Plug Welding Sills
#1
Posted 29 January 2025 - 01:15 PM
#2
Posted 29 January 2025 - 01:18 PM
personally I can't see it makes any difference which way you do it in terms of strength, assuming the weld goes in right
but I would definitely prefer to weld top down as gravity will be trying to pull the weld pool down before it hardens, you get drips, not to mention you'd be laying on the floor welding upwards which is never ideal
one might argue it would be more tidying up on the top side which on that narrow ledge isn't the easiest thing to do and would be more visible than it would be underneath.. but then again you'll probably have a seam trim on it at the end anyway
that's the outer step seam anyway, further underneath going onto the floorpan you don't get the choice really unless you want to get really particular with measuring and then drilling holes in the right place from above which is just impractical really
you can hire spot welders, but you might struggle with the mains circuit tripping unless you have an industrial rated breaker. and you'd need long arms on it to reach the underside not to mention the rear bins are in the way
I plug welded mine all round, step edge from above, floorpan edge from underneath but with the shell tipped over on its side
Edited by stuart bowes, 29 January 2025 - 01:54 PM.
#3
Posted 29 January 2025 - 01:45 PM
If your paint is good on the quarter panel then plug welding down will cause some damage. HOWEVER if you use something like Frosts Cold front and get it down to the edge of the flange you will minimise any burning and also distortion.
Obviously welding up is not ideal and unless you have got a really decent set of jack stands and jack to get the car up high enough then it really will be uncomfortable.
#4
Posted 29 January 2025 - 04:15 PM
On the outer lip I would weld from the top, always easier, dress up the surface nice and bright and drill your weld through holes and dress off any burrs.
On the floor, again I would weld from the top where possible, often the inner surface of the floor is easier to dress up nice and clean, but not always. You will not get the full length but wll get a good percentage.
As regards marking off the possition for the weld through holes, fit the sill clamping it securely along the outer lip. determine where the weld through can be achieved from the top and drill a small hole at either end of the weld runs right through the sill and the floor. On the inside "join the dots" and drill your weld through holes as required. The areas that cannot be welded from the top will have to be done from underneath.
Dress off all burrs and get the sufaces as clean as possible, start welding from the middle out.
I set my welder high to get a good weld pool and usually cut the weld wire to give a "fresh" end every weld.
#5
Posted 29 January 2025 - 05:19 PM
Wow, thank for the relies. Some really good ideas. Like the 2 small hole line up method.
Again, thanks
Edited by no66, 29 January 2025 - 05:19 PM.
#6
Posted 29 January 2025 - 06:14 PM
To add to this and this is my personal preference for size of plug weld holes.
The quarter panel to sill lip is not really wide enough for 1/4" inch holes so i would go for 3/16th (4.7mm). The hole size you get from the hole punches you find online (normally combined with a Joggling head) are 5/32. Although back in the dim and distant past i used to use this, over time i find for the best and strongest weld a 1/4" hole is the best for plug welding. But again this is dependant on where you are welding.
If you are using a welder like a Clarke 135TE Turbo Mig then max power and at least 8.5 on the wire speed with 0.6mm wire is a must. Lower power than this will just fill the hole and not penetrate the metal below it.
1 user(s) are reading this topic
0 members, 1 guests, 0 anonymous users