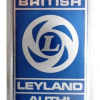
Distributor Machine
#16
Posted 18 November 2024 - 04:36 PM
Ac
#17
Posted 18 November 2024 - 05:02 PM
They invented the dizzy machine so you can service the dizzy and test it. When your making advance curves a coneventional dizzy machine is much to slow and ponderous to use for tweaking advance curves, hence I came up with my own design. As I said you don’t need a machine to be able to test a dizzy, the best test bench you can have is the engine you are actually using it in.
Ac
Actually I have lot's of time and I am not in a hurry but I love to learn new things and also to fabricate gadgets
The engine is in pieces, also the bodywork is paused for winter so I have no "test bed"
And the neighbours will kill me if i run the engine on high rpm
Edited by gaspen, 18 November 2024 - 05:27 PM.
#18
Posted 18 November 2024 - 06:11 PM
Before I got my Distributor Dyno, I tried the drill and lathe then the Mill, but gave up as it was a very slow and clunky way to do it and you couldn't measure dwell, points bounce and other issues. I was also able to compare doing them this way at the time to using the Dyno at the machine shop I was using at the time. The control and accuracy of the Dyno ran rings around doing them on the Mill. I'd never go back to that and gald I bought the one I have.
I find with the Dyno, I can do them so much faster and with a greater degree of accuracy, it also has a vacuum pump with a gauge for doing the Vac. Advance. It's dead easy to disassemble them right there in the Dyno to change weights, stops and springs. I've since made and fitted a module to drive most electronic distributors as well. I wouldn't do them any other way now, it was a good investment.
That's been my experience.
#19
Posted 19 November 2024 - 09:45 AM
You can see my machine in this thread;-
https://www.theminif...d-distributors/
I've generally found the the springs last OK, even many I test now that are circa 40 years old are still in spec. however the other mechanical parts wear, causing the mechanisms to stick or over-advance.
The numbers on the distributor body dictate the curve, the letter suffix indicates a feature of it, eg, it might have a symmetrical or asymmetrical or high lift cam.
The various Lucas and BMC tables will state if the data is in distributor or crankshaft speeds and angles. Most are in distributor but not all, just check carefully before using it.
May I ask you some detail picture of your machine ? I'd like to see how the dizzy is fixed and how it is clutched to the motor's shaft
#20
Posted 19 November 2024 - 05:00 PM
When I bought mine, there were various options, including a small 3 jaw chuck, but I just got it without anything and made 2 drive dogs, one to suit the A type and the other for the A+. You can just see the A one here (sorry, this is all I have on file)
My good friend Steve's machine, while an older unit, it had many bells and whistles. While not visible here, it has a 50mm 3 jaw chuck, similar in design to what you'd find on a lathe;-
#21
Posted 19 November 2024 - 05:46 PM
When I bought mine, there were various options, including a small 3 jaw chuck, but I just got it without anything and made 2 drive dogs, one to suit the A type and the other for the A+. You can just see the A one here (sorry, this is all I have on file)
My good friend Steve's machine, while an older unit, it had many bells and whistles. While not visible here, it has a 50mm 3 jaw chuck, similar in design to what you'd find on a lathe;-
Thanks !
I found these little chucks for bargain. It is 48mm in diameter. Now I am searching for a good 12V DC motor which I can control with a small PWM controller. Probably I will need an adapter to attach the chuck to the shaft.
Képkivágás.JPG 33.32K
0 downloads
#22
Posted 19 November 2024 - 05:54 PM
Thanks !
I found these little chucks for bargain. It is 48mm in diameter. Now I am searching for a good 12V DC motor which I can control with a small PWM controller. Probably I will need an adapter to attach the chuck to the shaft.
I'd suggest using a 3 jaw self centring chuck. Most 4 jaw types are independent.
I'd also suggest fitting a small flywheel to your set up to stabalise the speed. It won't need much and can be incorporated in to the degree wheel.
#23
Posted 19 November 2024 - 06:25 PM
Thanks !
I found these little chucks for bargain. It is 48mm in diameter. Now I am searching for a good 12V DC motor which I can control with a small PWM controller. Probably I will need an adapter to attach the chuck to the shaft.
I'd suggest using a 3 jaw self centring chuck. Most 4 jaw types are independent.
I'd also suggest fitting a small flywheel to your set up to stabalise the speed. It won't need much and can be incorporated in to the degree wheel.
Allright, Boss
Thanks for the advices
#24
Posted 19 November 2024 - 10:49 PM
You will probably need a motor around 500w. It sounds big but it really isn't especially at reduced rpms. A belt drive setup is probably better than direct, it's what most machines did (or a more complicated rubber cone). It is best if you can find a motor and controller which regulates the speed via a tach signal of some kind. You want a three jaw chuck like already mentioned, they are available cheaply too. Also they are usually flexibly mounted so that the distributor doesn't need to be lined up precisely. I would however recommend using a mini distributor drive or making something similar yourself. My machine has a chuck and doesn't hold mini distributors well. I had the same problem when I bought one of the cheap chucks to make a machine. They aren't deep enough to go over the while drive so end up either holding about 2mm on the drive or 2mm on the shaft. The result is that they easily slip in the chuck.
Spider's machine is one of these: https://ingenioes.co...product&info=12 - still available if you have lots of money.
Edited by 68+86auto, 19 November 2024 - 11:14 PM.
#25
Posted 19 November 2024 - 10:53 PM
Do you know if he happens to have a service manual for that model of Syncrograph? I know someone who has been looking for a service manual for a long time. The earlier ones can be found but not those ones.
#26
Posted 19 November 2024 - 11:42 PM
You will probably need a motor around 500w. It sounds big but it really isn't especially at reduced rpms.
Spider's machine is one of these: https://ingenioes.co...product&info=12 - still available if you have lots of money.
If I recall, the motor in mine is around 500W. It has a PWM speed controller that also includes braking to assist with speed regulation and I suspect that's partly why it uses such a size motor to get better sensitivity from it's back EMF on over-run. I also think that's about the minimum size motor you want for the reasons you've laid out.
That is the machine I have but I didn't pay anything like that when I got it ! I looked for years for a used one, contemplated building one and well,,,,,,,
I gotta say, despite it being inexpensive, it's been quite good.
Do you know if he happens to have a service manual for that model of Syncrograph? I know someone who has been looking for a service manual for a long time. The earlier ones can be found but not those ones.
No he doesn't and also wants one. I had to do some repairs to it a few years back and was frustrated by not having info on it.
I dunno if this is any help, the page from the Repco Bible ?
#27
Posted 20 November 2024 - 09:14 AM
#28
Posted 20 November 2024 - 11:50 AM
Just to clarify my knowledge
This machine - as others - shows the Dwell angle around the round-scale with a light on each cylinder. It is a pretty spectacular feature.
The "length" of the light shows the CLOSING degrees of the contacts, as the dark areas are the OPENING degrees, right ?
If the shaft of the dizzy is bent or the cams worn unequally I should see 4 different length lights on the machine.
What if I measure the Dwell with a multimeter on the same dizzy ? Should I see an avarage value or an alternating value ?
It is depends on the sampling rate of the multimeter ?
I think it is a key factor If I go to the direction of the machine building
I have this multimeter on the picture, it has many functions.
herth-buss-95980775-multimeter.jpg 97.27K
1 downloads
Edited by gaspen, 20 November 2024 - 05:01 PM.
#29
Posted 20 November 2024 - 05:31 PM
That should be a nice machine, needs a clean up of course and I * think * the drive belt from the motor is missing but being of the vintage that it is, anything that would be wrong with it would be repairable.
On my machine, yes, the length of the light shows the dwell angle (points closed) and any uneveness in dwell is clearly shown. It can be from a bent shaft, worn bushes, wear between the mainshaft and camshaft or a worn cam. You can also clearly see points bounce.
It's hard to say what any dwell-meter is measuring and they'll only show variations between cylinders at low speeds that you'll see. I prefer analogue meters for this function as you'll see the needle wavering where as with a digital meter it may show fluctuating numbers or it may just take an average over all cylinders.
#30
Posted 20 November 2024 - 07:09 PM
That should be a nice machine, needs a clean up of course and I * think * the drive belt from the motor is missing but being of the vintage that it is, anything that would be wrong with it would be repairable.
On my machine, yes, the length of the light shows the dwell angle (points closed) and any uneveness in dwell is clearly shown. It can be from a bent shaft, worn bushes, wear between the mainshaft and camshaft or a worn cam. You can also clearly see points bounce.
It's hard to say what any dwell-meter is measuring and they'll only show variations between cylinders at low speeds that you'll see. I prefer analogue meters for this function as you'll see the needle wavering where as with a digital meter it may show fluctuating numbers or it may just take an average over all cylinders.
I see. Now it is clear that with a single Dwell meter I can not measure the opening/closing per cylinder.
Another idea to get a circuit diagram for an old machine and manufacture it on circuit board
It looks that one in France is sold now
Edited by gaspen, 20 November 2024 - 07:22 PM.
1 user(s) are reading this topic
0 members, 1 guests, 0 anonymous users