Wow! Love the colours Stuart. It's going to be a real head turner!!!
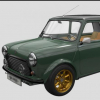
1988 Mayfair Rebuild (998)
#166
Posted 23 April 2023 - 01:37 PM
#167
Posted 23 April 2023 - 05:29 PM
actually slightly darker than that I'll have another go later having discussed a minor bug with the app and finding a workaround
Edited by stuart bowes, 23 April 2023 - 05:29 PM.
#168
Posted 23 April 2023 - 08:35 PM
only ended up with half a car this time? not sure what happened but closed the app already now never mind
that's more like the colour we're thinking of, with the wing mirrors to match the gold accenting maybe, or just body coloured
fogs flushed into the grill not on brackets
and most likely black or body coloured headlight trims, I'm really not a fan of chrome myself (each to their own obvs)
Edited by stuart bowes, 26 April 2023 - 08:24 AM.
#169
Posted 27 April 2023 - 08:47 PM
anyway before I get all carried away and way ahead of myself (^ that was just a bit of fun)
bonnet underside primer / filler / basecoat of highly professional (not) rattle tin white applied
also tweaked the edges a little in places to straighten out some inevitable little kinks and bends from over the years
I did give it another coat after that but forget to picture, it's not so patchy looking now
anyway that's really just to give it a bit of protection in the shed for the next 6 months / year / etc before I actually get round to the real bodywork finishing and paint
to be honest will probably just leave that and spray over it as-is unless any obvious issues arise because the 4 main quadrants will be covered with heat resistant sound deadening stuff anyway most likely. it's the top side that gets the real attention
still can't really believe how good a condition that's in for £50 (if you ignore the 'free' boot door) compared to what I was seeing on ebay for 80+ and a long drive to the arse end of nowhere
Edited by stuart bowes, 12 February 2024 - 06:41 PM.
#170
Posted 27 April 2023 - 10:21 PM
#171
Posted 08 May 2023 - 08:50 PM
Decided to have another go over the wiring loom having read a few more useful bits of info since I rushed blindly into doing it the first time round (doh)
job no 1 find the closest (but still not 100% accurate) wiring diagram to what I have, use the large format printer at work and print it off for a wall poster:
then strip off all the loom tape added before (hours of hard work) and lay it all out ready for modification
new fusebox tidied up from previous so cabling pattern is nice and square (ish) and closer up to the main bundle so it doesn't hang as low on the bulkhead)
did all the mods and continuity tested every single bit, ticking off on the wall chart as I went (checking for shorts as well, a very long drawn out process)
wrapped up the box to hide my not quite as-per spec wiring colour choices
although I will add, at the other ends where I have extended / relocated etc where possible I have kept the right colours from original cabling at the ends where you can still see them, so it looks reasonably original and for ease of working out what's what
wrapped the new relay positions (add the bases once in the car or it won't thread through all the holes)
and then wrapped the rest of everything in the engine bay (inside car bits left as-is, protection not required and lengths may need a little rejigging for a couple of items tbc)
and then all the same again for the much simpler rear loom (wrapped the whole length for ease of pulling through the roof channel)
so.. changes as follows if I can remember them all
- Fusebox replaced with 8way blade box and split up a bit for better distribution
- dim-dip relay deleted already the first time around
- sidelight wiring left standard but snipped back to before the split into two skinny wires and those ones replaced with thicker stuff for the fronts, backs were already decent size cable to all
- dipped beams cut back to single wire before it splits into the two skinny ones, routed through relay, new chunky wiring for power
- same as above for main beams
- same as above for horn (earth added because it was the one-wire version)
- relay added for spots, master on-off switch wiring added, triggered by main beam stalk
- all relays located together
- resistor wire and 12v bypass deleted, will be 12v coil (labelled accordingly in case I forget!)
- remote central locking wiring added in
- radio perm live / switched live / earth / headlight trigger for dimmer / reverse trigger for camera if added (tbc)
- USB socket perm live and earth added front
- USB socket perm live and earth added to rear (probably will branch out into two, one in each bin, just added a connection spur for now over near the battery side))
- High level brake light wiring added
- reverse triggered power added to same location for camera if added (tbc)
- (speaker wiring and camera feed wire would be added down right side channel totally separate obviously)
- got rid of left side fog connections which were never in use anyway
- added horn trigger wire (via relay) to ignition button bundle for when secret switch in wrong position in case that idea gets used
- replaced a couple of old crusty looking earth tags with newly crimped on clean ones, bad earth is the last thing we need causing trouble
- Deleted brake fluid test switch, routed wiring such that oil pressure and low brake fluid now share the orange lamp on the dash in failure, treating as general warning light for both
to my surprise every single bit of that tested correctly with not one single re-do required, by some fluke of luck
however in having the steering wheel connected up I did find that the indicator stalk switches are ropey as all hell and might as well just be replaced to be honest considering how cheap they are (in which case will probably do wiper side as well) The horn press also needed repeated bashing until that started working sort of properly 9 times out of ten, must just be all green and caked up inside
looking at low voltage cut-off boards for the USB power plugs, I wanted them permanent live for when camping or whatever phones etc can be left on charge for a while without ignition on, but it would probably be sensible to add protection against flat battery
Edited by stuart bowes, 09 May 2023 - 11:51 AM.
#172
Posted 10 May 2023 - 05:23 PM
back on the welding today, decided to put the rear OS quarter on partly because at some point I can then get the door skin lined up right and fitted
so.. kurusted, primered, painted the bits that will be hard to get at later:
then obviously because I can't weld through paint, hole punched panel and marked up locations, power filed back to clean metal just for those points (minimum possible for plug welding)
trimmed and clamped in panel
B post lined up fairly well after some gentle rubber mallet persuasion to the door side lip (apologies for blurry sh.t picture)
C post needed tacking and then clamping to pull it into place
B post then finished off
C post more or less finished off (will have another stab at tidying that up later)
and rest of panel plug welded in place with various pushes and pulls and adjusting clamps along the way
all lined up well and no warps that I can detect, feels good to have a nice new panel filling that gaping hole
then I plug welded all along the under/inner edge of the outer sill, forgot to take a pic but it's not massively interesting to see, I had left them undone to allow a bit of flex if necessary
that left just the back end to finish up and close off with a bit of welding:
which I then coated liberally with kurust because it's obviously starting to go a bit, the worst looking bit top right is actually just surface rust though, that was new steel middle of last year
remaining grot there will come under attack from a wire brush and kurusted again, possible some extra welding when getting back to boot floor work later
and of course the corners and edges will all be lavishly smothered with seam sealer anyway in case of small gaps or pinholes which I'm sure there are
Edited by stuart bowes, 12 May 2023 - 03:32 PM.
#173
Posted 11 May 2023 - 09:05 PM
on to the near side at least wanted to get the remains of the old panel off
door post pretty good
window rail much better than the other side but still a couple of minor holes and deformities from pulling apart the old spot welds
wheel arch cleaned up nice but I have left a bit of the old metal on there, mainly I didn't want to thin out the bottom layer too much and this way I get a slightly stronger edge.
When plug welding it back together will turn the welder up and make sure I'm getting penetration right through (did same on other side and seems totally fine)
Unfortunately when tidying up and trimming end of outer sill, I prodded at this bit I always knew was a possible issue and sure enough the screwdriver went through. oh well best to know now
Cut out around the problem area and will weld in a bit of that 1.5 I still have loads left from the boot floor strengthening plates
will clean up that bit on the corner of the wheel arch as well of course, one thing at a time
And finally this edge needs looking at obviously
so I trimmed out the bad bits for now just to get on with same procedure as other side: kurust / primer / paint the bits that are impossible to hit later on with the panel in place
last day off tomorrow and back to work Monday so hopefully will have to time to finish of those small repairs and get this panel on
any spare time after that will be back to working on the boot floor which is almost done now
Edited by stuart bowes, 11 May 2023 - 09:31 PM.
#174
Posted 11 May 2023 - 09:39 PM
#175
Posted 11 May 2023 - 10:59 PM
thanks for the pointer, I don't have a dremel as such but I can crack out the air line die grinder (closest thing to a dremel I have is on a flex drive and has a pedal, it's kind of all bolted to the bench too much agro to move)
before this it's all been internal / structural welds where I'm not as fussed about appearances but the outside stuff does need to be finessed
Edited by stuart bowes, 12 May 2023 - 12:31 AM.
#176
Posted 12 May 2023 - 03:17 PM
first job today fill that hole in the rear toeboard or whatever we're calling it, all fairly self-explanatory
used 1.5mm which is possibly slightly thicker than the original steel ? welder set to 1.2 I didn't want to overdo it. still as you will see I got mostly pretty good penetration
top and bottom looks to be fine, bottom left side I believe I penetrated the outer layer fine but haven't quite latched on to the lip that folds up from the floor. still having got the bottom edge solidly am happy to leave that as is, it's sealed all round anyway
I might give the right (outer) side another go over when I'm welding up the end of the outer sill later
-----
next the repair to the 'bum' section lip, bit trickier that
cut a strip slightly too wide and put a bit of a fold down the middle to get it started
find a piece of metal rod about the right diameter for the bend, use in the vice to hammer around:
then obviously it needs to curve as well so we crack out this magic little tool (stretcher / shrinker, set to stretch in this instance)
work it bit at a time until it's the right shape
point to note it seemed easier to me to do it this way rather than making it out of 2 pieces and having to not only weld an inner corner but then even harder have to tidy it up afterwards
I say 'seemed to me' but I have to give credit to my dad who I consulted first and who pulled that tool out of a box and said use this. In all honesty I didn't know such a thing existed until today lol
anyway.,
cut to size two pieces in my case and weld in, linish, etc
I have highlighted with the red arrow where I think the panel did warp inwards slightly due to welding (despite Colin's very useful instruction I still rushed slightly ahead oops)
I've tried gently moving it by hand and I can tell it will be relatively easy to pull into shape. The plan is, when fitting that rear quarter, weld the other three sides, and then use that new panel to judge how to align / adjust this one clamping and plug welding as I go to pull it into shape, I'm sure it'll work out fine
some additional dremel / linishing to be done at the bodywork prep stage much later on as discussed above, and of course a smear of filler to make it invisible
(by the way I haven't finished with that ugly welding on the boot floor subframe bracket, I'm definitely coming back to tidy that up)
Edited by stuart bowes, 12 May 2023 - 03:35 PM.
#177
Posted 12 May 2023 - 06:42 PM
and finally for today turning attention to this little issue which was the only actual dent / damaged part of the car (apparently a fence fell on it?)
regardless of that the insides look grotty on both sides anyway so those reinforcement plates need to come off
started cutting and swearing at it until it gave way
in doing so found this extra plate welded underneath which i want to say doesn't look like factory welding?
possibly is added strengthening following a repair which is visible from the outside as well. I can just about feel the same on the other side below the corner plate, and there's that long weld I found in the boot from left to right about 6" from the rear, so I'm going out on a limb and saying it's been rear ended and repaired. my guess from the rust etc would be it was early on in the cars life
either way I'll weld in some extra plates in the same way, still got some of that 1.5 left
moving on.. the outside cleaned up relatively well, only a couple of minor little repairs to do
and the inside will be fine I'm sure
Kurusted and primered in and out for now, just to keep surface rust at bay for the short term
which leaves me to rescue this bit which needs straightening out and welding back in
As with the rear end work above, will fit the rear quarter around three sides (door, window, sill + wheel arch) then refit that piece to match up straight with the new panel
Edited by stuart bowes, 12 May 2023 - 06:45 PM.
#178
Posted 13 May 2023 - 12:42 PM
Recovered C post piece and cleaned up with wire brush on grinder, looks alright
Kurusted and used the press to straighten out as much as possible
good enough now for a very slim skimming of filler instead of a big fat wodge
Primered and put aside for later
Edited by stuart bowes, 13 May 2023 - 12:43 PM.
#179
Posted 13 May 2023 - 07:44 PM
onto the nearside rear quarter
prepare the panel with holes for plug welding, plus this extra strengthening piece for the C pillar join (might add one over the other side as well once that corner brace is out)
weld and paint
first fitting of panel
and view from rear showing what work is required to get the back panel to line up (nothing too dramatic)
B post welded and blended in, primered
plug welded around door, window, sill and arch
and then refitted this C pillar piece, welded both sides
not the prettiest but will be completely hidden anyway
chucked some primer on it
on to the rear panel, welded these two points to get at least one section in the right place
then pushed / pulled / hammered / clamped and welded one at a time until happy that the lower section all lines up well (checking from the back side, not worrying too much about the seam itself)
which leaves this piece to get lined up and reconnected another time
Obviously a small filler piece needs to be made for the gap, and that will be reinforced from behind as well, i might actually cut the gap a little wider first to make that a bit easier to fit in, tbc
both parts of the C post need a bit of hammering and/or pulling into straight anyway so I've not plug welded the seam yet.. that's the next job for when I have time to do it with a bit of care and attention getting it close as possible for minimum filler
and that's my week off finished, back to work Monday and baby no.3 due in 3 or 4 weeks so that is probably the last major push now for at least a few months, I might get the odd day or two here and there to flat off some of those welds, proably won't bother with pictures of that as it's pretty boring stuff
Edited by stuart bowes, 13 May 2023 - 07:52 PM.
#180
Posted 13 May 2023 - 08:54 PM
It's good to see you got time to do stuff with 2, I'll be in that boat in a few months!
1 user(s) are reading this topic
0 members, 1 guests, 0 anonymous users