I meant to say what you did with sorting the battery box was fantastic by the way. Great job on that. Enjoying following this.
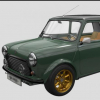
1988 Mayfair Rebuild (998)
#136
Posted 08 November 2022 - 02:32 PM
#137
Posted 08 November 2022 - 03:22 PM
cheers :) it's definitely a kind of home-brew brute force and ignorance method lol but maybe it will be useful for some people to see it can be done with fairly basic tools and it doesn't have to be a massively complicated job
I'm starting to get a lot more confident working with metal, true you can only bend it in the same place a couple of times before being worried it will snap off but at the same time it's easy enough just to cut it off and weld a new bit on.. nothing's ever really ruined as such
Edited by stuart bowes, 09 November 2022 - 02:11 PM.
#138
Posted 14 November 2022 - 06:47 PM
Weather has started to deteriorate and getting dark earlier, so have taken a break from actual repair work very briefly, to build a pavilion sort of gazebo kind of thing - metal framed, solid plastic roof and curtained sides, to shelter the mini from the elements as much as possible
also should work as a kind of low budget spray booth when it gets to that time as well, at least enough to keep the wind off (and floating dust to some degree)
wish I could have an indoor garage set up but there's just too many tools and benches and so on in there (mostly a woodworking garage really which is what I'm a lot more experienced with)
it's not this one but it looks kind of like it, heavier curtains and thicker legs, very sturdy
anyway now that's done and I have wired up a light out there, I can start getting on with the real work again
Edited by stuart bowes, 14 November 2022 - 06:48 PM.
#139
Posted 15 November 2022 - 06:39 AM
Great Project - I have done the same with my Battery Box!
Check out my Youtube Channel as it may help.............. Subscribe if you like terrible jokes and lots of rust
Thanks Kevin
#140
Posted 19 November 2022 - 06:24 PM
finished up the welding on the subframe-wheel arch bracket on the other side
Checked it again with the yard stick more due to obsessiveness than any real risk of it moving at this point
welded all round the battery tray despite previous comments, I decided as it's a big hole (i.e weakness) in the boot floor I'd like to make it as rigid as humanly possible.
That's the welding to the top side of the boot floor done, all bits primered for now pending many hours of future grinding and smoothing over with filler
Next job, finish welding up the reinforcement plates underneath, gas ran out and grinder died so waiting on deliveries now before that can happen
Edited by stuart bowes, 19 November 2022 - 07:39 PM.
#141
Posted 19 November 2022 - 09:56 PM
There is usually small L shaped pieces that go on the corners of the battery box on the underside, they add some strength to the corners to prevent tearing.
Keep up the good work!
#142
Posted 19 November 2022 - 10:23 PM
yeah I wasn't messing about lol, it does look quite top heavy on the weld I know, keep meaning to turn the power up a little and perhaps slow down the wire? but it's penetrating fine totally visible on the other side, I guess it just means more grinding
re: battery box/hole, there are still corner pieces underneath, and the remnants of the old boxes flange which I assume was spot welded in (although quite how i don't know, must have some pretty long old arms on that spot welder..) So i seam welded that old flange down all round, and welded the new flange onto that. so 3 layers of metal around the edges, and 4 at the corners! should be enough
Edited by stuart bowes, 20 November 2022 - 12:51 AM.
#143
Posted 19 November 2022 - 11:23 PM
#144
Posted 21 November 2022 - 09:46 AM
interesting.. that may well be true (I'd rather trust a book than some random info on the internet ..)
still in this case it's still a moot point as the flange is very narrow, and the box doesn't match up exactly with the hole, so in places the flange only overlaps the edge by 3 or 4mm at best, I'd be trying to weld to air
and then I convinced myself it was worth the time consuming work using the reason/excuse above
Edited by stuart bowes, 21 November 2022 - 09:47 AM.
#145
Posted 04 March 2023 - 07:38 PM
Trying to get myself motivated again but still a bit too cold to be outside for long by choice (have done a few necessary repairs on the volvo in the mean time)
decided to start looking at the bonnet - a few rusty areas requiring attention - took out the bracing
actually not too bad really, only one major issue on the bonnet itself (front near side)
the off side looked the same from the inside but doesn't poke through and the outside bare metal only had a tiny pin hole.. so that will just be weld the hole up and kurust the rest I guess. it's not structural and it's very easily replaced in the future (albeit not cheap)
can't see any new bracing parts available separately without buying a whole new bonnet (?) so will do something with those, at least it's not cosmetically important for them to be 'authentic' (that sort of thing doesn't interest me anyway). Might just cut off the rusty ends (grill end) and refit them slightly shortened. Sure it will do the job perfectly fine
Edited by stuart bowes, 04 March 2023 - 08:01 PM.
#146
Posted 23 March 2023 - 10:08 PM
some further work to the bonnet:
cut out the problem area
Beat a piece to shape
clamp and weld
checked it on the car and it's nigh-on perfect match with the other side and gap looks good (possibly a little bit of luck on that front)
turn attention to corners where I drilled out the spot welds, went in a bit too far
So I cut out those bits leaving the ends for alignment
then cut off the rusty front ends
angle grinder wire-brushed as much as possible and rust treated the underneath
which leaves the front end like this (obviously more wire brushing and kurusting to do to the underside of the bonnet)
still deciding if I'm happy to plug weld that back in as-is or add something to the front, which adds strength but potentially a bit of a minefield to keep the shape right exactly and not entirely necessary I don't think. TBC
Edited by stuart bowes, 24 March 2023 - 09:20 AM.
#147
Posted 23 March 2023 - 10:20 PM
Then took another look at what I did with the door and wasn't happy with it. it ended up warped which I almost pulled back to the right shape, but not quite, and then put a LOT of filler on it.. sometimes you have to be willing to take a step back, look again and admit it's no good
clean up and mark out what to keep
Cut it
Clean it up
take 1 x new door skin (which I should have done from the start anyway)
use curve-finder to find shape for future reference
use that to check and modify the piece to fit well
template and cut new panel
fettle to fit
check before welding
tack in
check again
so begins the slow process of welding it bit by bit, letting it cool. welding from inside to make tidying up a bit easier on the outside. it's pretty much perfectly flush but perhaps if anything very slightly recessed in one or two places, which is fine because I can always use a tiny bit of filler
Edited by stuart bowes, 24 March 2023 - 01:23 PM.
#148
Posted 23 March 2023 - 10:24 PM
final thought for the day
I also looked again at the lock release mechanism. it did work, but it was a bit clunky and might rattle around when driving along, also it just looked a bit crud
so I decided to go with a cable operated method
2 x trailer handbrake cables about 1m long found on ebay:
which I'm sure will be more than strong enough and no risk of stretching, plus one end has a very easy method for adjustment
so now I just have to conceive of some basic bracketry for each end
and possibly an extra spring somewhere, if the lock mech and handle spring isn't enough to push the cable back again
possibly this might work by going around the back side of the window track, and being connected to the inner door release bar, making it about as simple as it could possibly be. will play with a few different ideas at some point
with the old door skin removed, I can also very easily fit a bracket for a central locking actuator
Edited by stuart bowes, 23 March 2023 - 11:28 PM.
#149
Posted 29 March 2023 - 07:45 PM
door progress pics
welding from rear and checking from front side
smooth off backside (enough for my liking at least)
smooth off front side
primer on the back and leaving like that for now
finding out low points and filling as appropriate (I did have to deal with a bit of warping but nothing like as bad as the previous attempt)
smoothing off and first attempt at a primer coat
leave to dry and get my dad to cast a fresh pair of eyes over it tomorrow, see what his 2nd opinion is.
I think it needs maybe one or two very minor points raised a little with a tiny bit more filler, another go over with the sander, some putty to smooth over the little cracks, and high build primer should finish it off at a later point
EDIT --- 30/5/24 --- I have adjusted this again and wirebrushed off all the filler because I wasn't happy with it, see later posts around page 25 onwards. the curvature of the donor part from the metro door was casuing the problem and I found a way to correct it
Edited by stuart bowes, 30 May 2024 - 10:46 AM.
#150
Posted 01 April 2023 - 04:46 PM
working on the rest of the door
Removed old skin and wirebrushed edges. came up pretty clean considering (pics halfway through job)
Eagle eyed will notice ive had to chop out one piece of the edge, obviously due to excessive corrosion, templated first, cut out, welded in and flushed off a replacement piece
might need a little swipe of filler to finish cleanly later on but the lock mech will hide most of it
and then obviously kurusted what was left
I'm probably going to do what I did with the A panel - paint the edge (and inner bottom part of the door) with underseal, and the same around the inside edge of the new door skin as well, then fold the two bits together, I reckon that will keep it safe for a good few years because of the waxoyl
I know the window is grotty as f*k I'm not worried about that I have two 'new' (clean and undamaged) ones ready in the shed
Edited by stuart bowes, 01 April 2023 - 10:18 PM.
1 user(s) are reading this topic
0 members, 1 guests, 0 anonymous users