Has anyone had experience installing this panel. I thought I put this up for discussion, cant find it anywhere so I though I would try again.
There are a couple of ways of welding this, overlap panel and plug weld and then stitch weld or seam weld the joints. Could use a but of experience here.
Thanks all

A Post Repair Panel
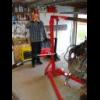
#1
Posted 27 October 2021 - 04:30 PM
#2
Posted 27 October 2021 - 05:16 PM
If you want to do nicely put it on in the correct position, draw a line when you cut the old wing then butt weld the repair panel to the old wing.
#3
Posted 27 October 2021 - 08:03 PM Best Answer
Like this.
#4
Posted 27 October 2021 - 11:35 PM
Awesome guys, thank you very much for the feedback. Invaluable as usual! You have given me a good guide for my second panel. I find that my plug welds are acceptable but I am blowing through the material when I am doing the seem welding. My Lincoln 140 has ABC switch's, the manual says to use C, but it just seems to be too hot. Tried the B setting still get occasional blow through, but it seems to be better, but I do worry about penetration. Am I doing something wrong or is it more or less experience that is not on my side.
Edited by Minirook, 27 October 2021 - 11:35 PM.
#5
Posted 28 October 2021 - 08:39 AM
Awesome guys, thank you very much for the feedback. Invaluable as usual! You have given me a good guide for my second panel. I find that my plug welds are acceptable but I am blowing through the material when I am doing the seem welding. My Lincoln 140 has ABC switch's, the manual says to use C, but it just seems to be too hot. Tried the B setting still get occasional blow through, but it seems to be better, but I do worry about penetration. Am I doing something wrong or is it more or less experience that is not on my side.
Its probably just technique, when welding with a mig on car body work you have to pulse it as trying to draw a long continous seam tends to result in blow through.
#6
Posted 28 October 2021 - 02:04 PM
Thanks for the additional information. Will try and produce a little less heat on the next go around.
Cheers
#8
Posted 28 October 2021 - 08:16 PM
As alluded to, due the thickness of mini panels, butt welds if you a relatively inexperienced welder can end up being a line of blown holes so one of the best methods is to pulse weld.
Pulse welding is essentially a series of overlapping tack welds, but the tack is held slightly longer than normal to enable decent penetration. Once you have got this knack you can end up with welds that look something like this.
The one thing to remember with butt welding is to ensure there is a small gap (approx one mm) to prevent puckering of the weld. So using intergrips will naturally space the panels.
Now to help prevent blowing holes through as well if it still keeps happening (this can be a combination of too much power, not enough wire speed) you can use something like flattened copper pipe clamped against the weld line. This helps to absorb heat helping to minimise distortion but enables you to back fill any holes you may have blown through.
I use standard copper plumbing pipe, split and then flattened out. I also cut some slots in it to enable me to use my intergrips as well.
I normally seam weld most butt joints including mini panels, but pulse welding is a nice alternative to utilise as well.
#9
Posted 28 October 2021 - 11:07 PM
Thanks again guys. I can say that I had no gap in the panels, so on the next panel I will ensure there is a gap to work with. Thanks for the copper pipe idea, as you would expect I do have some different forms of copper in order to repair the holes that were produced, but will lay a piece behind during the process and see if this and the gap can make the experience a little bit more enjoyable.
Eastwood is a great company for information so thanks for that link.
1 user(s) are reading this topic
0 members, 1 guests, 0 anonymous users