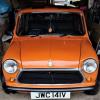
Rollover Jig Tips
#1
Posted 29 September 2021 - 05:52 PM
I bought a second hand rollover jig, that almost identical to the ones supplied by rolloverjig.com
I have managed to get my shell up onto the jig with much annoyance.
I tried to use an engine crane on each end to get the shell to the right height but the design of the jig meant it would get in the way of the crane and would drag the shell in the wrong direction.
I then used a dolly with pallets and packing to raise the shell with the crane then pack out the pallets, remove crane and attach jig.
All great.
Except i now need to adjust the jig to balance it correctly, but I can't easily use my previous method because I would need to lift shell while attached to the jig.
Also, taking it off the jig is a next year problem but I should probably have a tried and tested method to do so.š¤£
Can anyone give me their method of mounting/unmounting a shell. Maybe I can find a way to help me
Cheers
Mike
#2
Posted 29 September 2021 - 06:29 PM
But pallet trucks aren't usually something you have knocking around unless someone can lend you one.
#3
Posted 29 September 2021 - 07:34 PM
With mine i get the shell on axle stands with a thick wooden plank under them. (notched for the battery cable conduit) One set directly under the rear heelboard and then the other under the front floor pan. Bear in mind there is little weight with a bare shell so no damage to the floors.
Now in this position with the axle stands as high as they go i position the jig accordingly. If a little more height is need then some extra blocks of wood can be added.
I only ever do this on my own by the way. Two people would be a bonus but fully doable on your own.
#4
Posted 29 September 2021 - 11:25 PM
I think I used 4 pallets on top of the dolly to get the required height.
Another issue is the frame has a bracing bar between the two ends so I can't rest it fully without removing that before hand
Maybe I'll see if the loading/balancing tool from rolloverjigs.com will fit mine
#5
Posted 30 September 2021 - 02:00 PM
It's fine to leave that off during loading,I always do.
I have the loading tools for mine but thought they were pretty rubbish
#6
Posted 30 September 2021 - 06:58 PM
I never seemed to get mine balanced ? always very hard to turn on your own
#7
Posted 30 September 2021 - 07:16 PM
Possibly throwing a cat among the pigeons here, but can I suggest another approach ?
This is the first time I've shown these.
This possibly doesn't suit every situation, but years back I draw up a roll over jig that I was going to make. When I looked and thought about it, it just wouldn't work too well for me. I made a couple of sets of body stands (sorry for the rubbish photo - rubbish camera !);-
If needing to do a lot of extensive body panel replacement, this may not suit your needs.as the shell does need to be fairly sound.
I have another set of legs that bolt on quite simply that let me tip the shell on it's side too;-
These can be fitted on either side so the body can be turned either way.
The other down side of these is you can't turn the body up-side-down, but I'm yet to find a time when I need to do this, it also needs 2 people to flip the shell. They aren't heavy at all, but just too big to handle.
When I do a build, starting off when stripping the car, I remove the engine and subframes, the stand then goes on at this point and stays on through the whole build - body repairs, blasting (the blaster man loves it), painting, interior fit out, off to the Trimmers (our Trimmer loves them as he doesn't need to bend down to work on the cars and he can move them about easily), engine bay fit out, electricals, steering rack, all the pipe work, absolutely everything up to the point of fitting the subframes, wheels and engine. Certainly, they have made moving the shell around a breeze and with little risk of damage during the builds. I admit here I use a fork lift to get the stand on and off the bodies, but I have also done it of a trolley jack.
I made them so the shell is at 'bench height' and is for the most part, comfortable to work on. The basic stand is on castors, as is the side legs when flipped on it's side. Unlike a roll over jig, for probably 95% of the work, the stand is right out of the way of the work, you don't need an excessively long work space to accommodate the stands at each end and when not in use (that's not been too often !), it packs up flat against the wall.
Cost me about $80 AUD to make 2 stands (and that was just for the castors), I made them mostly from scrap steel. I just couldn't ever do a build without them.
#8
Posted 30 September 2021 - 09:14 PM
When it comes to loading it up I use the engine crane at 45* from the either end and a big lifting strap over the rotisserie bracket.
Edited by Tupers, 30 September 2021 - 09:16 PM.
#9
Posted 30 September 2021 - 10:07 PM
I have one of these jigs and I think it was from this company, I've used it for a couple of MK2 jags so far and its been great, if balanced correctly you can spin it over easily.
To get it on and off I use the loading tool which makes it so easy, the only downside is it takes a bit of winding : https://www.rollover...balancing-tool/
As a Mini shell is very light even if its not balanced exactly right you should still be able to spin it over fairly easily.
Edited by Homersimpson, 30 September 2021 - 10:07 PM.
#10
Posted 01 October 2021 - 07:12 PM
I never seemed to get mine balanced ? always very hard to turn on your own
I build my own. It is a doddle to spin. It really depends on the pivot points in relation with the shells centre of gravity. I made my spindles adjustable and I'm now at the sweetspot.
Can turn it by one hand (if I want to).
#11
Posted 01 October 2021 - 09:37 PM
The shell is light enough it can be rolled over carefully in the slings. This obviously won't work for painting, will probably drop it down onto some pallets after the panelwork so I can move it around with a pallet trolley which I'm lucky to have at home (because I long term borrowed it from work š¤£)

#12
Posted 01 October 2021 - 10:38 PM
I never seemed to get mine balanced ? always very hard to turn on your own
I build my own. It is a doddle to spin. It really depends on the pivot points in relation with the shells centre of gravity. I made my spindles adjustable and I'm now at the sweetspot.
Can turn it by one hand (if I want to).
I agree the one on my MK2 was slightly modified to spread the legs out and hence make the pivot lower as the roof was low in the garage, even with the pivot off set so I could turn the car in the limited height of my garage it was ok to turn on my own, I would imagine a mini would be easy peasy and if its not the pivot must be a long way out.
1 user(s) are reading this topic
0 members, 1 guests, 0 anonymous users