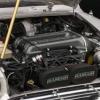
Maintenance Free Ball Joint Kit
#76
Posted 04 September 2020 - 11:38 AM
@paulrockliffe.
I have neen in touch with David and he has said. Only install whats in the kit.
No shims no springs.
He pointed me towards this vid. Skip to 20.30 for ball joints.
https://youtu.be/hJYUM-fvYOA
Cheers
#77
Posted 04 September 2020 - 11:50 AM
Oh great, thanks. I was actually going to email David to ask how best to fit them as - surprise surprise - when my socket arrived yesterday it doesn't fit over the spring. Mind you that video isn't a great help as it quotes the higher torque figure required for the standard ball joints and he torques them up with a spanner, so he's not really got a clue what torque they're set to. Perhaps I just need to get a feel with the wrench and spanner them on tight, I can see that it matters a huge amount on these so long as it's tight enough.
#78
Posted 04 September 2020 - 04:42 PM
Personally as i have put new grease nipples on i am going to push the grease through to make sure they are ok. Then put the ball joint on... Just in case.
#79
Posted 04 September 2020 - 06:09 PM
He pointed me towards this vid. Skip to 20.30 for ball joints.
https://youtu.be/hJYUM-fvYOA
Cheers
That's not a bad video (perhaps a little long winded though that's likely me), however 2 things I did see there;-
I'm not sure I agree with how he held the hub in the vice to install the ball joints. He gripped them 'side to side' over the Bearing Tunnel. I'd suggest using a pair of shaped hardwood timber blocks as soft jaws if holding them that way. I must admit, they are an odd shaped part to hold, I camp them down 'front to back' in the press, using a hardwood block on the back side as it's a poor shape to hold. The timber gives plenty of traction so it doesn't slip.
The other thing was while he did go to some lengths in regards to torquing up the Ball Joint when fitted, he didn't show how he did it. which was a bit out of step with the rest of it as he showed most other aspects quite well.
Maybe some might frown upon this, but, if you really did want to fit a socket to torque them up, as long as your tools and everything else was 'surgically' clean, I see nothing in the world wrong with removing the Blue Clip and the boot, then perhaps fitting a small sheet of plastic wrapping over the joint, including the Hex of it and a little beyond, just to be sure of keeping it all clean, then slipping the Socket on, over the plastic, Torquing up, clean, remove plastic, re-fit Boot and Clip. If doing this, I'll also add that while tempting, I wouldn't recommend using any tools to remove and refit the blue clip, it would be all too easy to hole the boot.
Perhaps this is something the manufacturer could look at, increasing the size of the Hex so a bigger socket is needed that will clear the hardware of the joint. I totally get that they are likely trying to keep it the same as it was and also avoid the need for the fitter to buy yet another tool, but the way they are is possibly inviting trouble.
#80
Posted 04 September 2020 - 06:23 PM
I take those videos with a pinch of salt because having watched quite a few I know his experience is similar to my own and he's doing lots of jobs for the first time so the detail often isn't quite right.
I did have a quick look at removing the blue wire - I'm not sure if you'd correctly describe it as a clip - I didn't try for long, but it does seem like it won't be the easiest job in the world, not sure what tool you'd try really even if it was a good idea. It's tightly wound and is roughly two and a bit full turns. Felt like I would prick at least one of my fingers quite painfully if I tried hard enough to unwind the coil to get it off.
#81
Posted 04 September 2020 - 06:28 PM
The guy doing the repairs has a general mini youtube channel (i am sure most members have come across his vids at some point).
However when i contacted David r. e. fitting the joints he said he is in the process of writing a fitting guide for the joints.
He emailed me saying, in lieu of his fitting guide the video is a brief 'how to' made by someone else and by no means an in depth how to.
#82
Posted 04 September 2020 - 07:13 PM
Yeah, the video shows that you remove what was there and bolt the new ones on easy. It just doesn't show how to get a torque wrench on them given a socket doesn't fit over. I'd probably have just spannered them too, but my biggest adjustable is 36mm vs 37mm for these, so I'm trying to avoid buying another new tool for the job, having already bought the socket.
#83
Posted 04 September 2020 - 10:32 PM
If using an open end spanner/wrench, you can get a decent torque near enough by first practicing with a double nut using a bench vice and your existing torque wrench....hold one end of double nut with the torque wrench, other with the open end and learn what the 60-70 ft-lbs feels like. Repeat on the ball joint.
There are also tricks like taking an open end or combo open end/closed end spanner and using a suitable nut on the other end to then connect the torque wrench to. If you keep it at 90 degrees to the ball joint then the length of the spanner does not change the effective torque at the torque wrench end. Here's a snazzy Motion Pro tool for this:
https://www.motionpr...dapter-08-0380/
Hold your horse right there.
It WILL require an adjusted torque setting as stated in the picture.
You're creating extra leverage. Without any adjustments you ll be overtorqueing it by a lot.
#84
Posted 04 September 2020 - 10:48 PM
If using an open end spanner/wrench, you can get a decent torque near enough by first practicing with a double nut using a bench vice and your existing torque wrench....hold one end of double nut with the torque wrench, other with the open end and learn what the 60-70 ft-lbs feels like. Repeat on the ball joint.
There are also tricks like taking an open end or combo open end/closed end spanner and using a suitable nut on the other end to then connect the torque wrench to. If you keep it at 90 degrees to the ball joint then the length of the spanner does not change the effective torque at the torque wrench end. Here's a snazzy Motion Pro tool for this:
https://www.motionpr...dapter-08-0380/
Hold your horse right there.
It WILL require an adjusted torque setting as stated in the picture.
You're creating extra leverage. Without any adjustments you ll be overtorqueing it by a lot.
Actually, it states NO ADJUSTMENT needed if held at 90 Deg....and adjustments needed if not at 90 Deg. That's the whole point of the adapter part. As I said, this can also be done with a homemade adapter or even using a double up pair of nuts locked to a bolt....then one end in the combo wrench end and one end in the torque wrench/socket. Held to 90 deg and no adjustments needed.
Edited by Tornado99, 04 September 2020 - 11:07 PM.
#85
Posted 05 September 2020 - 03:49 PM
For a short extension like a crow's foot at 90 degrees I believe there would be a theoretical very minor adjustment needed but this could probably be ignored. As the extension held at 90 degrees increases in length the required amount of adjustment would increase. For something like a spanner in the above example I would have thought that the torque setting would need to be compensated, especially if the torque wrench handle is relatively short.
It must be Pythagorus, surely. If the spanner or extension at 90 degrees was the same length as the torque wrench handle the actual turning moment would be the square root of 1+1 which equals 1.4 times the original moment. I think.
#86
Posted 05 September 2020 - 05:14 PM
#87
Posted 05 September 2020 - 05:19 PM
90° is a magic angle...the leverage is the same because, well...Don't think about the hypotenuse and length, just imagine you're torquing a bolt that is slightly higher than the bolt you're actually torquing...It's the same length from left to right...This is a bad explanation, and this video is a bad video, but it proves the point:
#88
Posted 05 September 2020 - 06:25 PM
You've got to be right there. You could pull the handle of the torque wrench straight 'down' in the left hand picture and it would apply turning force to a nut in the spanner jaws without putting any turning force through the torque wrench.
Sure you could do that....but that's not how anyone would use such a setup. Placing a 90 degree force on the torque wrench towards or away from the bolt head will not create more torque over what is set on the torque scale at the bolt head.
This is an old trick of the trade and it works.
#89
Posted 05 September 2020 - 06:50 PM
#90
Posted 05 September 2020 - 07:18 PM
From the previous link, I saw this Pratt & Whitney Standard Practices sheet on this matter:
Attached Files
1 user(s) are reading this topic
0 members, 1 guests, 0 anonymous users