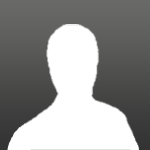
Torquing The Cylinder Head - Concerns!
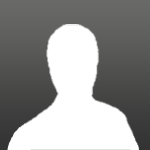
Best Answer postve , 13 February 2020 - 04:13 PM
Whenever I fit a head I start by tightening in the correct sequence to 25 ft.lbs. then I torque again this time to 35 to 40 ft.lbs and then finally to the 48 ft.lbs I always use.
I run through two complete heat cycles and then re-torque in the correct sequence. When doing this final torque-up I back each head nut off by 1/2 a turn before final torque is applied. This is done in the correct sequence and one at a time.
With regards to installing the studs I just put a slight 'nip' on each one.
Thank you Cooperman as I recall seeing your response at some time in the past as above. I will leverage both your feedback and Pops_Guild as I do this again.
It kind of makes sense to dyshipfakta point as the original stud was probably defective - another lesson learned is change the studs if they have a long history to them as the cost is minimal to the effort to remove the same if you break it off in the block or any other situation that one can encounter. Go to the full post

#1
Posted 13 February 2020 - 12:54 PM
I am sure this has been brought up before but wanted to hash this out and get your feedback.
So I have my new stage 3 (subject to all sorts of interpretations) and first time I broke a stud in the block - finally got it removed again at a cost of @120 pds your money.
Anyways, this time I bought a Delco digital torque wrench (cause I don't trust my self with mechanical old skool ones), new studs and arp bolts so I can feel like a pro:)
Big question, what precautions should I take when doing this one again to avoid my earlier screw up and do it right?
- should I tighten the studs in advance with wrench or by hand to the point of counter sync in block?
- I was suggested 45psi on the Calver CST 2001 head;
- Recommended start, warm up, run for a bit, and retorque again - concerned about expansion and over torquing with that one;
- lastly, do all the above and pray to the mini-gods that when I
Push it hard won't spring a leak or bust a stud
As always appreciate the feedback
Phil
#2
Posted 13 February 2020 - 01:10 PM
Torquing the head has to be done in the correct sequence and in two stages, I cant remember the torques off hand but you do one with a lower torque, then again at the final torque. If you have Haynes manual that has it all in there, it is straight forwardly explained in there. The sequence and staging is important.
That’s it done technically but in practise you’d be wise to do the next two stages but some folks do it slightly differently.
Fire the engine up and get it running at full working temp, you don’t need to drive it. Just run it.
Let the engine cool down 100%, must be cold, not warm, cold...overnight to be sure.
When stone cold, Check all the nuts for torque in sequence again.
Should be good to drive now.
After 500miles or so of driving and on a stone cold engine, check them all again in sequence.
Edited by Pops_Guild, 13 February 2020 - 01:11 PM.
#3
Posted 13 February 2020 - 01:38 PM
After 500miles or so of driving and on a stone cold engine, check them all again in sequence.
Definitely agree with this, my head started weeping coolant along the front of the block and a quick re-torque fixed this issue. This was around 600 miles on my rebuild.
#4
Posted 13 February 2020 - 01:41 PM
#5
Posted 13 February 2020 - 02:20 PM
Studs should be hand wound in, some folks also pinch them in but they don’t need or want to be forced.
Make sure the threads in the block are clean and the holes free of debris at the bottom.
#6
Posted 13 February 2020 - 02:25 PM
Studs should be hand wound in, some folks also pinch them in but they don’t need or want to be forced.
Make sure the threads in the block are clean and the holes free of debris at the bottom.
Humm I am wondering if this was what broke the last stud as never checked the well on the bottom of the studs before - thx sir
#7
Posted 13 February 2020 - 02:26 PM
Studs should be hand wound in, some folks also pinch them in but they don’t need or want to be forced.
Torquing the head has to be done in the correct sequence and in two stages, I cant remember the torques off hand but you do one with a lower torque, then again at the final torque. If you have Haynes manual that has it all in there, it is straight forwardly explained in there. The sequence and staging is important.
That’s it done technically but in practise you’d be wise to do the next two stages but some folks do it slightly differently.
Fire the engine up and get it running at full working temp, you don’t need to drive it. Just run it.
Let the engine cool down 100%, must be cold, not warm, cold...overnight to be sure.
When stone cold, Check all the nuts for torque in sequence again.
Should be good to drive now.
After 500miles or so of driving and on a stone cold engine, check them all again in sequence.
Thank you for the details this is extremely helpful!!
#8
Posted 13 February 2020 - 03:12 PM
Studs should be hand wound in, some folks also pinch them in but they don’t need or want to be forced.
Make sure the threads in the block are clean and the holes free of debris at the bottom.
Yep this is good advice. Folks assume they will be but often some crud gets in.
#9
Posted 13 February 2020 - 03:20 PM
I realize not necessary but could not hurt??
#10
Posted 13 February 2020 - 03:44 PM
I run through two complete heat cycles and then re-torque in the correct sequence. When doing this final torque-up I back each head nut off by 1/2 a turn before final torque is applied. This is done in the correct sequence and one at a time.
With regards to installing the studs I just put a slight 'nip' on each one.
#11
Posted 13 February 2020 - 04:03 PM
Don't the ARP head nuts torque to 55lbs?
Above info is spot on, but don't forget to recheck the valve clearances after you retorque the head.
#12
Posted 13 February 2020 - 04:06 PM
Don't the ARP head nuts torque to 55lbs?
Above info is spot on, but don't forget to recheck the valve clearances after you retorque the head.
Agreed as I read before about 55psi and I think that is crazy
#13
Posted 13 February 2020 - 04:13 PM Best Answer
Whenever I fit a head I start by tightening in the correct sequence to 25 ft.lbs. then I torque again this time to 35 to 40 ft.lbs and then finally to the 48 ft.lbs I always use.
I run through two complete heat cycles and then re-torque in the correct sequence. When doing this final torque-up I back each head nut off by 1/2 a turn before final torque is applied. This is done in the correct sequence and one at a time.
With regards to installing the studs I just put a slight 'nip' on each one.
Thank you Cooperman as I recall seeing your response at some time in the past as above. I will leverage both your feedback and Pops_Guild as I do this again.
It kind of makes sense to dyshipfakta point as the original stud was probably defective - another lesson learned is change the studs if they have a long history to them as the cost is minimal to the effort to remove the same if you break it off in the block or any other situation that one can encounter.
#14
Posted 13 February 2020 - 06:44 PM
Cooperman's advice here is, as usualy, very good.
Don't the ARP head nuts torque to 55lbs?
Above info is spot on, but don't forget to recheck the valve clearances after you retorque the head.
Agreed as I read before about 55psi and I think that is crazy
I only every use 45 ft / lb with these. More than that, and it actually distorts the cylinder bores, unless the block wor bored and honed with a torque plate.
This is the factory's advice on the sequence and stages. Note they also recommend that the studs and nuts be Oiled, though, with the ARP Fasteners, they have their own Lube;-
When re-torquing, as Copperman also suggested, I again lube the threads and under the nuts at this time also.
#15
Posted 13 February 2020 - 07:00 PM
Cooperman's advice here is, as usualy, very good.
Don't the ARP head nuts torque to 55lbs?
Above info is spot on, but don't forget to recheck the valve clearances after you retorque the head.
Agreed as I read before about 55psi and I think that is crazy
I only every use 45 ft / lb with these. More than that, and it actually distorts the cylinder bores, unless the block wor bored and honed with a torque plate.
This is the factory's advice on the sequence and stages. Note they also recommend that the studs and nuts be Oiled, though, with the ARP Fasteners, they have their own Lube;-
When re-torquing, as Copperman also suggested, I again lube the threads and under the nuts at this time also.
Got it and printing this as a guide guys, doing so tonight as "bone" cold in Toronto so I can run in garage and warm up as suggested and redo the next day - thanks so much for the piece of mind all!!!
1 user(s) are reading this topic
0 members, 1 guests, 0 anonymous users