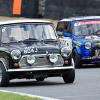
Diff Housing
#1
Posted 06 October 2019 - 04:41 PM
If I get a cheep box without it can I buy one and get it matched? Or is that an impossible /not worth it job? I would of got it rebuilt anyway.
5626 box.
#2
Posted 06 October 2019 - 06:43 PM
The Caps are matched to the Boxes.
Swaps are possible, but you will need to have access to many caps to find one that's close enough and even then, will likely need some machining to get right and leak free.
Given the type of box it is, they don't seem to hard to come by. In the UK, it would be easier and likely cheaper to just find a complete case.
#3
Posted 06 October 2019 - 10:14 PM
Swaps are possible, but you will need to have access to many caps to find one that's close enough and even then, will likely need some machining to get right and leak free.
To give you some idea, I have three 5626 boxes, none of the diff covers are interchangeable.
#4
Posted 06 October 2019 - 11:00 PM
I must confess that when in dire need of getting an engine back into a Mini for an upcoming rally I once used a non-matched diff cover. I had read all about the cover & the 'box casing being a matched unit, but I decided to try. I measured the mis-match and it was, from memory, about 2 thou.
Anyway I reasoned that the huge bearing outer races were not going to distort, So I just fitted it all and clamped it up.
It worked fine and lasted like 'for-ever'.
Don't think I am advocating fitting mis-matched diff covers, but it may not be the massive problem we have all been led to believe. I mean, what is the worst mis-match there could be and what would be the worst case scenario?
#5
Posted 07 October 2019 - 12:05 PM
It did not leak and is still going strong.just go for it.. but check twice. Fit once...
#6
Posted 07 October 2019 - 12:09 PM
Thank you all.
If i took it to a machinist - would it be a difficult job to match up and do a 'proper job' that really would last for-ever? I think i should be able to get this box dirt cheep so if the machining costs £50 then its worth it.
#7
Posted 07 October 2019 - 01:46 PM
It would be a 'bit of a job' to skim the mating faces, the end faces and then re-bore to the correct diameter.
In your case I would get a pair of bearings, or the pre-assembled crownwheel & pinion with the bearing races in place, and do a 'trial fit'. It it all goes together OK then you have saved a lot of money. The mis-match at each end will be very small and a bit of ;liquid gasket' with the actual gaskets when assembling will prevent any leakage.
I don't think you will have a problem, but if at 'trial build' there seem to be bog 'steps', it's not too late to think again.
#8
Posted 07 October 2019 - 02:40 PM
I have done a cooperman many times.....always got away with it.. maybe getting away with it is the key....to me the big issue was / is.. gasket or no gasket and hylomar / silicon or not
#9
Posted 07 October 2019 - 04:50 PM
Thank you all.
If i took it to a machinist - would it be a difficult job to match up and do a 'proper job' that really would last for-ever? I think i should be able to get this box dirt cheep so if the machining costs £50 then its worth it.
Difficult ? IMO, no very easy but you do need to start off with 'the right' cap and the time needed is in clocking them all up. The results can in fact be better than original.
I'm short on time right now, but can throw up some photos later, along with what to look for and how to do it all. I'm no fast worker at all (still learning!) but I can do them in about 2 hrs.
#10
Posted 12 October 2019 - 06:42 AM
I don't have a complete set of photos for this.
Basically, you need a cap to start off with that has the Bearing Tunnels that will when put together, form a circle. You may or may not need a gasket. I remove the Dowels for checking this (and in fact dispense with them all together when doing a Cap Swap). I fit studs to the Gearbox to make this easier when checking a few. Place the Cap on, line up the Tunnels and nip the Nuts. Then measure the Tunnel Diameters on both sides. These need to be 2.998 - 2.9995". If it's tighter than this, it might be worth fitting up a gasket and re-trying or alternatively, if on the small side, re-bore the cap, if on the loose side, it maybe possible to plane back the Cap Gasket Face, though that would be an operation that would be difficult to set up I would think. Not one I've yet done.
When you've found a cap you can live with, bolt it up to the case with the tunnels aligned. You can use some old bearings in there for this and align as close as possible the hole for the Shifter Seal.
Next job is to mount it in the Mill, clocking off the tunnels to get it dead square
Lower Tunnel
Upper Tunnel
This will require some shimming
Then Plane the faces for the Side Covers. Both Sides will need doing
I now do this on all gearboxes. I've found that these sides, when measured top and bottom are all tapered towards the bottom (well, every one I've done so far). This leads to premature wear of the Side Cover Bushes (and Oil Leaks)
Here's a brand new case, with it's matching cap and dowels fitted;-
This is an initial couple of light cuts. You can see that the Cap is in fact wider than the case.
Once the Side Faces have been trued to each part and each other, next job is to flip the Case and clock up the Selector Shaft Tunnel in the Case. Then bore over size the Cap.
(here I have the Cap removed, but is normally done on the Case)
So that brings there tunnels in line, but the Cap size is now oversize. I turn up a Bush and press that in to the Cap. Then Bore the Bush back to the Correct size (1.000")
#11
Posted 12 October 2019 - 11:27 AM
Wow you are certainly a perfectionist Moke Spider - Chris
Great stuff.
#12
Posted 13 October 2019 - 09:47 AM
1 user(s) are reading this topic
0 members, 1 guests, 0 anonymous users