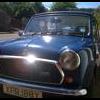
1275 Metro Engine Project
#406
Posted 01 March 2023 - 06:19 PM
#407
Posted 01 March 2023 - 06:32 PM
So before moving on, I fitted my piston stop and check that the TDC mark on the pulley was still correct, rotated clockwise and marked the pulley with a pencil, next anti clockwise and then marked again and the halved the total difference between the two marks, this was still the same as before.
Next, ensuring I applied some copper grease to the bolt ends I fitted the radiator mount), then on went the fan.
And torqued bolts to 10 lb/ft.
On went the radiator and top hose, using some new hardware.
And bottom hose.
Then out came the lifting gear so I could take the engine off of the engine stand.
Almost there
#408
Posted 03 March 2023 - 06:13 PM
Next job - check the CV Pot joints. Although they are brand new and come pre assembled, some of the items being supplied these days leaves a lot to be desired.
So, off with the CV Boot Clip and pop the boot:
Well there's definitely grease in there but not enough as the joint is dry in some of the critical areas.
Also it appears to have separated somewhat as there was a lot of liquid inside:
So I cleaned of the area around the bearings and applied a liberal amount of Lithium Moly CV Grease, packing it into the ball bearings and made sure the sides of the pot were lubricated - sorry no photos as its a messy job!!
I then cleaned up the outsides, popped the boots back on and got my local garage to put on some new clips.
As I still need to grease up the outer CVs I ordered myself a CV Boot Clip Tool and these Jubilee CV Boot Clips these were linked in this thread. This link takes you to Jubilee's site, but you cannot order them from there. So I took the product code for the kit and avoiding eBay (in case I got cheap copies), I ordered them from the bearing boys here.
I also researched CV clamping tools as I did not quite understand them, as the ones I looked at came with two tools, a crimper and what looked like a winding tool. After watching a video I realised that there were a couple of different types of clips. The Jubliee made CV clips only need the crimpiing tool, the other type of clips are a bit like banding wire (for those that have used it) in that you use a winding tool to wind up the excess to tighten the clip and then fold and cut it off. Then crimp it. I only needed the crimping tool.
Job done.
Edited by JonnyAlpha, 04 March 2023 - 11:37 AM.
#409
Posted 03 March 2023 - 06:41 PM
Next job, finish the engine (well apart from a few pre fitting jobs).
As Im running a full NODIS Ignition, I order a Dizzy Blanking Plug
The bracket is the original which I had re zinc plated - not great but it serves a purpose.
Next up I cleaned up the water jacket holes and roughed up the inside lip with a bit of emery, then did the same to the core plugs. I then cleaned them with some Brake Cleaner and using some black RTV and a suitable sized socket, I popped them in.
Before popping on the Pot Joints I thought it would be best to swap the circlips. There was a new one in each of the Pot Joint boxes.
The ones on the Diff should have been changed when the diff was rebuilt but they look as if they are the originals.
And here they are out on the bench, the look a little pitted.
I cleaned up the circlip grooves, to remove any grit.
And then checked the new circlips for fitting, the ones that came with the Pot Joints looked too big:
Someone on FB suggested that they just needed nipping up a bit so I did that (I later found out that these are for the Drive Shafts not the Pot Joints - oops)
I applied some lithium grease to the inside of the seal and to the splines inside the pot joint.
And slid each Pot Joint on, making sure thst the circlips stayed in place.
Almost ready for dropping into the car, just need to sort out all the running gear parts ready for fitting as soon as the engines in place.
Edited by JonnyAlpha, 04 March 2023 - 11:28 AM.
#410
Posted 05 March 2023 - 04:53 PM
Next update, before the engine goes in (which is hopefully this coming weekend, I need to ensure everthing is ready to get the front wheels back on. It's currently still on a couple of castors from when I removed the subframe at the start of this last phase (is there ever a last phase?) of renovation.
The drive shafts were cleaned and re plated ages ago, but I need to change the circlips.
The originals seem in decent condition, but I decided to change them anyway.
All done
One the circlips were in, I applied a small amount of lubricant to the end and slid on the boot.
Next job was to grease the Outer CV Joints.
I have a couple of sets of old CVs, one pair looked OK but in the end I decided on new.
I should have opened the boxes earlier, as I did not realise they came with Castle Nuts, CV Grease and CV Boot Clips, Drive Shaft Circlips, all of which I have bought separately DOH!!
After a quick bit of research on how much grease to use I clamped on of the CVs in a vice with some rubber jaws, I also ensure that I had some thick carboard under the threaded end, to protect the threads. Apparently after finishing I believe I should have cleaned out the CV joint with brake cleaner or the like.
Then I opened a pack and squeezed out the first lot of CV Grease.
I then proceeded to squeeze the grease down through the centre and kept loading the centre and repeating the process, until grease was oozing up through the bearings.
Once I was happy that the bearings were all lubricated, I added a tad more on top centre.
Then after cleaning up the sides, I was ready to insert the drive shaft. Carefully ensuring that the circlip was getting squeezed back into its recess, I located the drive shaft splines onto the splines of the CV.
Then, using a Nylon Hammer, I tapped on the other end of the drive shaft until the sound changed, highlighting that the shaft was fully home in the CV.
Now I could slide the boot into place.
I ordered a CV Clip Clamping Tool which has now arrived so next job will be to fit the Boot Clips.
And then the next one and all complete (less Boot Clips) ready to go.
#411
Posted 18 March 2023 - 09:29 PM
18 March 2023 Update
A few bits and bobs last weekend (when the engine was supposed to go in but it didn't). Basically the weather was terrible, so I spent some slow time checking a few things to ensure when I did get a chance to fit the engine, hopefully there would be no hiccups.
I needed to fit the Subframe Packing Pieces and whilst looking through my parts boxes, I came across a Towing Bolt that needed to be fitted at the same time. After a quick reminder of how it went in and on which side, I installed it.
Hopefully it won't be needed
Then I fitted the packing pieces and tightened up the bolts.
Next job was the Brake Calipers, I needed to get these on because I wanted to nip up all of the Subframe brake lines before the engine goes in.
First of all I had to look at some images online to ID which way around they went i.e. which was LH and which was RH side.
And here's my LH Caliper orientated to the LH Swivel Hub.
After fitting the flexible hose to the caliper and tightening it, I could do up all the Subframe Brake connections.
I then cable tied them to the Tie Bar.
Next I decided to check that I would be able to position the engine correctly using the crane inside the garage.
After positioning the engine on the floor in front of the crane I connected up the lifting gear and moved the crane into position.
Unfortunately the calipers where in the way!!
So I removed the cable ties and bolted the calipers to the swivel hubs (only hand tight as they will need to come off).
Now that I could get the crane legs under the car, I lifted the engine into position.
It all looked very tight so I posted these pictures up on FB.
The following advice came back:
- Remove the radiator
- Turn the lifting brackets around to tilt the engine slightly
- Place a piece of plywood over the subframe to help the Diff slide into position
- Swap the Clutch Slave Cylinder Clevis Pin around
- Leave out one of the WOK bolts or cut a slot in the bolt hole
I switched the clevis pin around and the rest I'll do next week (apart from slotting the WOK bolt hole.
The only other job completed was today and that was to fit a new connector to the Crank VR Sensor.
The connector is called a Junior Power Timer and I bought a male and female one from here
Before soldering on the terminals, I slipped on some heat shrink, but forgot to add the little waterproof bungs!!
I then pushed on the plug cover
And heated up the heat shrink.
WIRING
I also needed to start thinking about the wiring loom, no point having the engine in and not being able to start it.
The more I look into it the more complex it's getting as there are several factors involved.
- I need to source the power for the Fuel Pump
- Convert the Solenoid Wiring for the New Pre Engaged Starter with built in Solenoid
- Wire up the ECU
- Wire up the Coil Pack
Fuel pump seems simple enough, I managed to grab a wiring diagram from the Speeduino Forums and have modified it to remove the Fuel Injection Modules. I have bought a couple of 40 Amp Relays. The 12v can come direct from the battery via a fuse, but I need a fused Ignition Switched Supply for pin 86 on the relay?
For converting the Solenoid, I am opting for Cambiker's method shown in this thread.
https://www.theminif...-motorsolenoid/
The thread is about 7 years old and some of the images are missing so I am going to need an update, as I don't exactly follow how it works.
I have been advised to power the ECU also via a relay and I have also been advised to install a new front loom, due to trying to modify 40 year old wiring, however the guy who built my ECU says why not just install a new starter / charging loom for a fraction of the cost.
#412
Posted 01 April 2023 - 12:29 PM
So, a couple of jibs before the engine could go in the car:
1. Fit the Crank Sensor to the correct distance from the pulley (0.5mm).
2. Fill with oil, staring with Oil Filter, Oil Feed Pipe etc.
3. Fit the Oil Relief Valve.
4. Fit the starter motor (just for testing oil pressure).
5. Rig up an oil pressure gauge.
6. Connect a battery to the starter motor.
7. Run up to check oil pressure.
First up, fitting the crank sensor, in doing this I realised that the damm timing teeth on the timing cover were in the way meaning they would have to come off. I chose not to remove them when I modified the timing cover, as I was going to use them as a reference. Oh well off they came, I clipped them off with a pair of snips.
Then I fitted and adjusted the crank sensor to 0.5mm, as recommended by Stuart Gurr of Vmaxscart.
With the fan on, the modifications I made to re-route the cable seem to have worked.
Next, in preparation for fitting, I removed the radiator and rotated the lifting eyes, which should help the engine to angle backwards which will give a better angle for lowering into the engine bay.
Before running the engine, I double checked whether or not I had set the tappet clearances and I could not find any record that I had, so I set about it. On checking them, it would appear that they were pretty close, but some needed resetting. All set to 0.012".
Next job, fit the oil filter housing.
Took me ages to find the damm gasket, but eventually it turned up
And on it went. No new shiny bolts, so I used the originals.
As directed by several people in the know, to help gain oil pressure, you need to pre fill the Oil Filter.
Then, using my oil can, I filled the oil pipe hole in the filter housing and for good measure I also filled the oil pipe.
Didn't get a pic of the Oil Pressure Relief Bullet Plunger, but here's the cap. I did not have a new washer so I had to use an old one :-( Then on it went.
I also did not get a pic of the lovely DSN braided oil hose but before fitting it, I back filled the hole in the engine block. I had previously prime filled the oil pump when I fitted it. I also back filled the oil hose before fitting it.
Before filling with oil, I had to fit my temp rocker cover and for this I used an old stock rocker cover gasket, which I had been given by my next door neigbour several years ago, her dad used to play with Riley Elfs and minis.
Next job, fill with oil.
This is the Mini Spares High Zinc Oil, which is best for running in the engine.
Next job was to connect up the starter motor. For this I removed my battery from the boot of the car. I connected a new Solenoid the Battery Lead onto the Starter Motor's main 12v terminal, this is the main large terminal that sits on its own and is not connected to the starter.
The -ve terminal of the battery was connected to a head stud using a Jump Lead.
The =ve terminal of the batter was connected to the main 12v terminal on the starter solenoid, also using a jump lead.
I then connected a separate cable to the starter exciter terminal, using a crocodile clip, the other end of this will connect to the extra red cable attached to the 12v main feed on the starter to start the starter motor.
In the picture above you'll see that I have fitted a manual oil pressure gauge union in the oil pressure switch hole. This was borrowed from my 998 as it has an oil pressure gauge on the end that I could use to check oil pressure. I had picked up a separate gauge for this but forgot to buy the pipe work and connectors
You'll also see in the pic above that I have secured the Distributor blanking plug.
Edited by JonnyAlpha, 01 April 2023 - 01:05 PM.
#413
Posted 02 April 2023 - 08:42 AM
You are putting a large amount of time effort and money into this project and it’s looking good, but are you aware of the need to run the cam in properly. Suggest you read Calver ST technical - engine running in on his website, if you haven’t already. Good luck with the completion of the build.
#414
Posted 02 April 2023 - 10:38 AM
You are putting a large amount of time effort and money into this project and it’s looking good, but are you aware of the need to run the cam in properly. Suggest you read Calver ST technical - engine running in on his website, if you haven’t already. Good luck with the completion of the build.
Keith Calver has been a real help throughout this project, from doing a video call with me in Lock Down when I first started to look at modifying the cylinder head myself to finishing off my Cylinder Head and supplying technical advice and top quality parts.
His running in method is what I am going to follow. You have just reminded me to re-read it.
https://www.calverst...in-new-engines/
He doesn't mention running the engine without coolant and re-torquing the head down to avoid coolant leaks? I'll email him on that one.
I am using MiniSpare own high zinc oil, which he mentions for running in, and he also says to change the oil at 100 and 500 miles. I wonder if this should be more high zinc oil at 100 and something like Millers Classic at 500?
#415
Posted 02 April 2023 - 11:26 AM
#416
Posted 02 April 2023 - 03:16 PM
You are putting a large amount of time effort and money into this project and it’s looking good, but are you aware of the need to run the cam in properly. Suggest you read Calver ST technical - engine running in on his website, if you haven’t already. Good luck with the completion of the build.
Keith Calver has been a real help throughout this project, from doing a video call with me in Lock Down when I first started to look at modifying the cylinder head myself to finishing off my Cylinder Head and supplying technical advice and top quality parts.
His running in method is what I am going to follow. You have just reminded me to re-read it.
https://www.calverst...in-new-engines/
He doesn't mention running the engine without coolant and re-torquing the head down to avoid coolant leaks? I'll email him on that one.
I am using MiniSpare own high zinc oil, which he mentions for running in, and he also says to change the oil at 100 and 500 miles. I wonder if this should be more high zinc oil at 100 and something like Millers Classic at 500?
So calver says run engine with NO coolant to seal the head gasket and
run engine with coolant for 20 mins to bed the cam in?
I’ve only done the latter on all the engines I’ve built over 36yrs in the motor trade
#417
Posted 02 April 2023 - 04:25 PM
I said Keith does not mention running with no coolant, I read it somewhere else.So calver says run engine with NO coolant to seal the head gasket andYou are putting a large amount of time effort and money into this project and it’s looking good, but are you aware of the need to run the cam in properly. Suggest you read Calver ST technical - engine running in on his website, if you haven’t already. Good luck with the completion of the build.
Keith Calver has been a real help throughout this project, from doing a video call with me in Lock Down when I first started to look at modifying the cylinder head myself to finishing off my Cylinder Head and supplying technical advice and top quality parts.
His running in method is what I am going to follow. You have just reminded me to re-read it.
https://www.calverst...in-new-engines/
He doesn't mention running the engine without coolant and re-torquing the head down to avoid coolant leaks? I'll email him on that one.
I am using MiniSpare own high zinc oil, which he mentions for running in, and he also says to change the oil at 100 and 500 miles. I wonder if this should be more high zinc oil at 100 and something like Millers Classic at 500?
run engine with coolant for 20 mins to bed the cam in?
I’ve only done the latter on all the engines I’ve built over 36yrs in the motor trade
Edited by JonnyAlpha, 02 April 2023 - 04:30 PM.
#418
Posted 02 April 2023 - 08:27 PM
#419
Posted 03 April 2023 - 12:35 PM
So calver says run engine with NO coolant to seal the head gasket and
You are putting a large amount of time effort and money into this project and it’s looking good, but are you aware of the need to run the cam in properly. Suggest you read Calver ST technical - engine running in on his website, if you haven’t already. Good luck with the completion of the build.
Keith Calver has been a real help throughout this project, from doing a video call with me in Lock Down when I first started to look at modifying the cylinder head myself to finishing off my Cylinder Head and supplying technical advice and top quality parts.
His running in method is what I am going to follow. You have just reminded me to re-read it.
https://www.calverst...in-new-engines/
He doesn't mention running the engine without coolant and re-torquing the head down to avoid coolant leaks? I'll email him on that one.
I am using MiniSpare own high zinc oil, which he mentions for running in, and he also says to change the oil at 100 and 500 miles. I wonder if this should be more high zinc oil at 100 and something like Millers Classic at 500?
run engine with coolant for 20 mins to bed the cam in?
I’ve only done the latter on all the engines I’ve built over 36yrs in the motor tradeI said Keith does not mention running with no coolant, I read it somewhere else.
hi bill, wasnt aimed at you ,
yes ive read the same on another forum about doing both buddy
keep up the great work dude .
#420
Posted 03 April 2023 - 03:23 PM
Don't add coolant/anti-freeze .. just plain water
When? On first run?
5 user(s) are reading this topic
0 members, 1 guests, 0 anonymous users
-
Bing (4)