Nice work Bill!
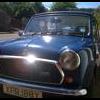
1275 Metro Engine Project
#286
Posted 13 March 2022 - 07:30 PM
#287
Posted 13 March 2022 - 10:14 PM
Nice work Bill!
Thanks Alex
#288
Posted 21 March 2022 - 03:08 PM
A little bit more yesterday, once the weekend visitors dispersed.
Time to clean up the output covers:
That RTV is a right pain to get off. First off came most of the gasket using a sharp Stanley blade. Then some thinners and a brass brush, then more thinners and a tooth brush.
Next job:
Couldn't find any of my Taps so I used a the bolts.
I'll need to clean up all the bolt threads as well.
Then I had to bolt the gearbox down on two lengths of wood and undo the MainShaft nuts as I had to fit the new Pinion Wheel for the 3.1 Diff and the new Standard 29 Tooth Input Gear.
Out with the old 28 Tooth Eco Input Gear.
And in with the new (well Second Hand) 29 Tooth (std) variant.
And here's the 19 tooth Pinion Wheel
Might get the X Pin Diff in this week if I'm lucky!!!
And more news, the head is packaged. Getting sent away to get checked, repair the Rocker Post Threads, valve guides fitted, valve seats cut, measured and skimmed.
When it's back all I'll need to do is paint it.
#289
Posted 26 March 2022 - 11:25 AM
Yesterday I had about an hour in the garage.
After watching the relevant part of the MED Technologies Engineering Gearbox video to remind myself of the exact steps to take (also referring to my Rover Workshop Manual and questions on FB), I cracked on with finishing the Gearbox.
I had already Fitted and Torqued up the MainShaft nuts and New Lock Washers (No pics sorry), so after checking that it was OK to fit the main bearing Retainer plate afterwards and not before I started to measure the gap.
I couldn't work out why I had no shims, but then on checking my Strip Down Video (at about 8:06), I realised that this Gearbox had none fitted originally.
However when rebuilding the gearbox you obviously need to re-check the gap.
After getting advice from John Guess etc, the retainer plate is NOT pre loading the bearing and if the gap is less than 0.005" you don't need to fit any shims. In the MED engineering video they say you need 0.002" gap and there is a note against the shims on the MiniSpares saying 0.001" gap?
Anyway, I'm going with JG and the Rover Manual.
When pressing the plate in by hand I couldn't get a 0.003" feeler gauge in:
And with the screws done up lightly there is only 0.0025" gap:
So no Shims required.
Torqued up the nuts to 18Nm using my Small 'Teng' Torque Wrench.
Next job was to fit the locking tabs and using an adjustable set of grips, bend them over.
Then using a screw driver to start the fold and a small punch, I knocked down the lock washers on the First Motion Shaft Nut Lock Washer and Pinion Nut Lock Washer.
Next job - the Diff.
I blew out all of the bolt holes with an Air Gun and then wipe down and test fitted the Diff.
And that was all I had time for.
Only other news is that I managed to get my Maniflow LCB Stage 2 Manifold (Birthday Present).
That should compliment everything nicely.
Just need to figure out how to connect it up to my Cat Version RC 40 (No Cat fitted - using a Link Pipe).
I'll also need to drill and weld on a Lambda 'AFR' sensor flange into the Manifold :-( Not sure exactly where this needs to go yet.
#290
Posted 02 April 2022 - 02:56 PM
Just got my head back from the Mr Calver (Calver Specialist Tuning).
As you will be aware, if you have read earlier posts, I did all the chamber and porting work but a this was for all intents and purpose a practice head to start out with, I wanted an expert to check it and if found to be OK, get them to do the additional work that I was unable to do.
So Keith, skimmed the Rocker Post side to clean it up, opened up the Port Throats for larger 'Metro' Valves, fitted unleaded inserts in the exhaust valve seats, set the valve spring seat height, fixed a couple of rocker stud threads that had crack, removed the old water bypass, measured the chambers and skimmed the face as required to achieve our target CR of 9.75:1
It would appear that my work on the chambers was pretty spot on, as they measured:
1 - 25.9cc
2 - 25.8cc
3 - 25.8cc
4 - 25.9cc
Keith then asked me to confirm the Piston Deck Height which I measured as:




Bypass hose fitting removed:
I have bought the long version from Minispares.
Valves have been check and a 30 degree cut back applied, lapped and bagged in numbered bags to ensure they go back into the correct chamber.
Still needs a wash / clean up, blowing through with an air line and then a nice coat of paint.
The engine is gloss black and all the pipework will be blue, so I was thinking for the head a gun metal grey or matt black?
In other news, a part that I did not have when I got the gearbox Aqua Blasted needed a clean up. Only used filament brushes but looks ok.
Need to get my act together now as I almost have everything ready to finish the build and implant the engine.
#291
Posted 11 April 2022 - 02:09 PM
So Saturday I managed to get my Gearbox Diff and Output Covers sorted,
I had already worked out the shims needed and was short of 1 x 0.010" shim, so another MiniSpares order!!
Got carried away and ordered 2 x CV Joints and an Alternator as well DOH!!
The first job was to watch a couple of videos and remind myself of the process of fitting and shimming the diff correctly.
I cleaned up the area and cleaned the Diff bearings faces and machined area in the diff housing and cover.
I then placed the DIff in position to engage the pinion gear and slid the diff assembly to right and popped it into place.
I then tried the Classic Mini DIY method and put the RH output cover on, complete with gasket and did up the screws.
This pushes the Diff to the left and sets it in place.
I then had a bit of a time trying to get a confirmed measurement of the gap, one method suggested that I had a 0.0014" gap, therefore this would need shims equating to 0.028" for 0.00" clearance. The suggested clearance for these bearings is between 0.000" - 0.001".
I also tried MED engineerings method of bolting on the Diff housing cover and then butting the LH output cover on dry, again without a gasket and checking the gap with a feeler gauge.
This gave me a measurement of 0.013". This meant that, with the gasket measuring 0.014" with shims equating to 0.028", I would have a 0.001" clearance.
So if I shimmed the gap using shims equating to 0.028", I would have a gap of 0.00" with the first reading, or 0.001" with the second reading?
The problem is shims should be 0.006" and 0.010" as advertised, but they are not. The 0.010" shims I have just received are actually 0.0116":
So three 0.0010" shims measured 0.0325 on my Vernier callipers:
These were my notes:
I had shims of 0.0325" and 0.028", so I opted for the 0.028".
So with everything apart agin, on went the RTV:
This time using hopefully just enough.
Then on went the Diff housing:
Then on went some Loctite 243 and in went the bolts:
And finally all bolted up:
#292
Posted 14 April 2022 - 07:27 PM
Well this afternoon was cleaning the cylinder head time.
Then Jet Washed, to blow out all the crud.
And then some petrol, the push rod holes bizzarely were stil line with old oil.
I then used some thinners, a lot of scraping to get off the last of the paint (should have done this before, but wasn't planning on using this head originally).
Came up OK.
Tomorrow is painting day.
#293
Posted 19 April 2022 - 06:52 PM
So yesterday, using some 320 Wet and Dry I cleaned up the surface rust that had bled through in the valve throats and ports.
This is the kind of thing I am referring to.
Only got these pics after cleaning up the throats etc.
Then today it was paint time, but first a final inspection to ensure everything was clean and a wash down with thinners.
Still some crud coming out, so it was well worth it.
Finally clean, ready to paint.
I coated the bare metal areas not to be painted with vaseline, so the overpainting will wipe off and clean up easily.
Not sure about the area around the thermostat area, might scuff it up and end up painting it.
#294
Posted 27 April 2022 - 04:48 PM
So ,whilst waiting for the cylinder head paint to cure I finished the Gearbox. All that was left was to fit the Speedo housing and Speedo Gears.
Due to a change in DIff ratio, from 3.44 to 3.1 and Drop Gears from Eco Input and Eco Primary to 1:1 ratio, I had to change the Speed Worm Drive cogs to a 7 / 18 setup. Got a second hand set, but it needed cleaning up before use.
Once the Speedo Drive Spindle was cleaned up I gave it an oiling and inserted it into the gearbox.
At first it did not seem to fit? But after rotating the gears it slipped home.
Next I dug out the Speedo Pinion, as the original that came with the Engine was cleaner I swapped them about.
Next in went the pinion
And the nylon bush and cap (this pic was taken before the gasket was in place)
Then after a debate, regarding which product to use to seal the gaskets, on went the Hylomar Blue.
Didn't get a photo but next goes the gasket and plate over the speedo drive and the additional aluminium section that fits to the engine mount,
In the pic above there is a locking plate missing from the Speedo Drive cap, at the time I could not for the life of me find it anywhere. this is the piece here:
After an extensive search around the garage and nearly buying one, it finally turned up
And here it is all clamped in position.
All that's missing now is a Speedo Cable and from the experience I have had of having to replace a broken cable, I think I'll fit it as the engine goes in!!
#295
Posted 27 April 2022 - 05:26 PM
More work, this time the cylinder head.
Annoyingly just after I had completed this AC Dodd released the last of his cylinder head videos, however, with some advice as I was going along from the likes of Turbo Phil via Facebook I got it pretty much on the money.
The main thing is cleaning everything, but I had pretty much done that already.
First up get everything out and ready, that means checking my project spreadsheet to confirm that I have refurbished or bought the parts needed and in which box to find them (sound organised, but storage and accounting used to be my main trade )
Next job line up all the bags with the valve parts in order of fitting.
First job, fit the metal shim that sits in the valve spring recess. If you don't fit this first the it won't go over the valve stem seal.
Next on goes the valve stem seal, with a bit of oil to help. I should have squirted a bi of oil down the valve guides but I did oil the valve stems before fitting.
Next in goes the respective valve.
Next on goes the Top Hat and clamp everything down with the Valve Spring Compressor:
And once compressed fit the collets:
And then release the spring compressor.
It would appear that I didn't fit things in any particular order, I actually did, but before fitting everything I had read that on a Turbo or Supercharged engine it is often practice to omit the stem seals on the exhaust valves, or at lease remove the spring around the stem seals. After doing so I then had contradicting info that they can be left on, so I had to re-do the exhaust valves!!!
Here are all the valves and springs etc in place:
Next it was time to fit the ancillaries.
This is an early 1275 head with the bypass underneath the thermostat housing, the old one was corroded so Keith Calver kindly removed it for me. For a replacement I bought the extra long version (apparently makes fitting the hose easier). This needed some PTFE tape to ensure a water tight seal.
Then hand screwed in, finished with some grips and rag.
After fitting the new 82 degree thermostat I did a trial fit of the housing. First problem, where the top face of the head had been skimmed, the thermostat not sits proud of the recess that it sits in.
The gap above should hopefully get resolved by fitting a couple of gaskets, however in the gasket set, I did not appear to have any, not even in my spares (which I got from a neighbour who used to play around with minis and Hornets).
There was one in these spares (bottom left), but it looked used, so another MiniSpares order :-( and delay.
When fitting any of the studs in the cylinder head, I used some Copper Slip Grease to try and help combat any corrosion caused by the dissimilar metals.
I also dry fitted the Heater Tap Take off and all of the exhaust and inlet manifold studs (again with Copper Grease).
Here's the head almost finished.
Here's what it looked like when I acquired it.
#296
Posted 27 April 2022 - 07:20 PM
looks great

#297
Posted 28 April 2022 - 04:45 PM
Now you've lost all that patina! Great job.
#298
Posted 02 May 2022 - 09:00 PM
So, after a lot of searching, I finally managed to get my hands on a mint condition dual belt Crank Pulley, here it is with the Trigger Wheel.
Here's a quick trial fit (without the Timing Cover).
However, some have found that fitting the Trigger Wheel on top, can cause the Trigger Wheel to foul on the Radiator / Engine Mounting Bracket.
Here is a pic of such a modification.
In the pic above, the timing cover has fouled on the Crank Pulley and caused a groove, this can be prevented by fitting a Speedi Sleeve.
The other issue (that I was aware of) is that the breather will be in the way of the ribbed pulley.
I then fitted the water pump and pulley just to see how the single v pulley lines up, as some people have been having some issues.
I then mocked up the Crank Sensor and as you can see it is too low, this will be resolved by fitting shims (if the trigger wheel stays on top, otherwise it will be OK.
Next job was to fit the cylinder head studs into the block, first though I needed to clean out the threads as I'm pretty sure I forgot to do it previously DOH!
I then got into a large debate on FB regarding whether to put oil on the thread before inserting the stud and how tight it needs to be. In the end I used a smear of oil and used two nuts and a socket / wrench and tightened them up reasonably tight.
Stud above no fully inserted of course
And I could not resist in putting on a gasket and trying out the head, started to come together
#299
Posted 02 May 2022 - 09:56 PM
Nice work Bill, Getting there now! If you need a certain sized thrust washer for the primary gear when you set the clearance give me a shout, I bought about 50 at Riv run
#300
Posted 03 May 2022 - 05:40 PM
Nice work Bill, Getting there now! If you need a certain sized thrust washer for the primary gear when you set the clearance give me a shout, I bought about 50 at Riv run
Will do Alex, I'm sure I'll need some
I have decided that this Month it's 'get the engine in' month. Iv'e listed all the weekends in May and allocated jobs to days, looks good on paper, but I haven't cleared it with the missus
9 user(s) are reading this topic
0 members, 1 guests, 0 anonymous users
-
Bing (8)