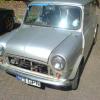
1969 Mini Cooper S @ Mill Road Garage Isle Of Wight
#121
Posted 08 December 2017 - 09:07 PM
Going to be a solid little mini when finished Ben
Nice work mate
#122
Posted 08 December 2017 - 09:17 PM
Love your write ups Ben, very methodical and detailed! Whats that on the subframe, a blue cylinder on a bracket? Flame kit
?
Thanks.
The item on the subframe is the fuel pump.
I did remove it before welding though
You could've put the tools away......
For a lovely looking car to start with, there's some nasty horrors hidden
That will be my first job tomorrow.
I would normally do it before leaving but lost track of time and had to leave quite suddenly.
It is a shame that the panel work wasn't sorted instead of a respray. The structural integrity of the car really was quite shocking. One of the worst I have seen on a Mini that's on the road with an MOT
Going to be a solid little mini when finished Ben
Nice work mate
Cheers Mark.
It will be great to return it back to being safe and preserve it better for the future.
Ben
#123
Posted 09 December 2017 - 06:10 PM
I popped in this morning for a couple of hours to get the new inner sill ready for fitting Monday.
I trimmed some of the mess and patches from the front to allow the panel to be slid in and then clamped it into place
Once it was fitting well, It was then a case of clamping/screwing the new edge to the old and then cutting in the new piece.
Here is the cutting completed
Then take it back off again to clean the edges for welding. There is lots of underseal etc to remove underneath.
Here is what I have now cut out from the front floor/toeboard area
I'm sure more will have to come out but ill wait until the inner sill is in and then work out what will be needed.
Here are the edges to be welded cleaned back ready
Lastly, some zinc paint was sprayed onto the weld edges and areas that will be inaccessible once the sill in in
It's now ready to fit for the final time so ill get that done Monday, sort out the mess at the front and then onto the other side.
Cheers
Ben
#124
Posted 09 December 2017 - 07:19 PM
Just had to trim a little square off the top back edge if I remember rightly
Looking good Ben 👍🏻
#125
Posted 09 December 2017 - 08:26 PM
Just had to trim a little square off the top back edge if I remember rightly
I have had to with these panels in the past but this one is absolutely spot on
Cheers
Ben
#126
Posted 09 December 2017 - 09:38 PM
Looking good Ben
If you spray dynax on top of zinc primer, the dynax will be attracted to the metals and offer even more protection
Just a titbit of techie info...... OK I'll get my coat
It's good to see a proper 69' Mini in bits. Your pics are fantastic, thanks for sharing.
#127
Posted 09 December 2017 - 09:46 PM
just read it all ion one go so far, really good work mate, keeping a proper note on what your doing as ill be doing mine soon!
what make of zinc do you use?
#128
Posted 09 December 2017 - 10:09 PM
Looking good Ben
If you spray dynax on top of zinc primer, the dynax will be attracted to the metals and offer even more protection
Just a titbit of techie info...... OK I'll get my coat
It's good to see a proper 69' Mini in bits. Your pics are fantastic, thanks for sharing.
That's really useful thanks Pete.
No problem sharing, I hope that the pics and info may help others
just read it all ion one go so far, really good work mate, keeping a proper note on what your doing as ill be doing mine soon!
what make of zinc do you use?
I use 2 different Zinc primers and both are unbranded from my paint supplier. Well I say unbranded, they are their own brand so most likely unavailable elsewhere.
The first is a really heavy zinc which I use in box sections and anywhere concealed. I tend not to use it on weld seams, especially where Mig welding as it really interferes with the weld causing some pretty horrific splatter explosions
It's fine with spot welding though..
It's about £15 per aerosol can trade so not cheap but good.
The other is a much lighter zinc content which I use where Mig welding is going to take place, especially plug welding although I do still tend to scrape the paint off through each drilled hole once clamped up before plugging.
I also use it to cover areas of bare metal during the panel work process to keep surface rust from starting.
For example, all of the bare metal on the new rear end panels is coated with it.
Still a good product but much cheaper at around £7 per can trade so I can splash that about a bit more .
Sorry I can't advise you where to get these ones but I used to use Zinc 182 by uPol, SAS zinc spray and weld #2 by uPol. All are good products and easy to get hold of.
Cheers
Ben
Cheers
Ben
Edited by Ben_O, 09 December 2017 - 10:10 PM.
#129
Posted 11 December 2017 - 07:05 PM
Back on with things today.
I didn't get as much done as was planned as I had some customers visiting discussing work etc which is always nice but slows things up somewhat.
First order of the day was to pop the inner sill back in so that I can align and clamp up the stiffener that goes inside the companion bin
Then a quick check that everything was dandy with the fit inside the companion bin
That photo is useful to show why the stiffener is required..
Next up I clamp in the stiffener making sure it is correctly aligned
And then remove the inner sill so that the stiffener can be spot welded into place
Before that can go back in for the final time, I need to fit the closing panel that sits in front of the arch tub
And then back in with the sill
I then spent some time making sure everything was where it was supposed to be and then spent a considerable amount of time and patience butt welding the new inner sill to the existing floor.
Here is the finished article
Then the bracing came out and I checked the door alignment
Relief and satisfaction
Then I spot welded the crossmember back to the floor, had a clean up and a hoover out and splashed some zinc primer over the repairs to keep it nice why I do the rest of the repairs
There is still quite a way to go on this side so here is hoping that the other side is more straightforward. It certainly looks the better side.
Cheers
Ben
#130
Posted 11 December 2017 - 07:34 PM
Of course I did it the hard way 😂
#131
Posted 11 December 2017 - 08:39 PM
Like the idea of fitting the stiffener to the inner sill first makes sense
Of course I did it the hard way
Usually more often than not, when doing inner sills, you end up cutting the bottom of the quarter panel off to replace so of course, access is good.
This is actually the first time I have done it like this and it worked out well.
Cheers
Ben
#132
Posted 12 December 2017 - 04:26 PM
Nice work as always Ben. The door fit looks good I have lost count of the number of restorations I have seen where the bottom of the back edge of the door ends up sitting proud of the quarter panel. Where you not tempted to use a half floor as the front floors looks quite pitted in the photos?
#133
Posted 12 December 2017 - 06:56 PM
Nice work as always Ben. The door fit looks good I have lost count of the number of restorations I have seen where the bottom of the back edge of the door ends up sitting proud of the quarter panel. Where you not tempted to use a half floor as the front floors looks quite pitted in the photos?
Cheers. This side is fine but the door already sticks out at the bottom on the other side so ill try to rectify that when I do that sill.
There is some pitting in the floors but generally, it's just surface rust and the owner of the car would like to retain as much original metal as possible.
Had the metal been too thin, then it would have had to have at least front pans.
Ben
#134
Posted 12 December 2017 - 07:24 PM
Onwards and upwards.
I pushed the back edge of the inner sill over to where it was supposed to be and welded the nut bracing for the heelboard to the inner sill and spot welded the closing panel to the stiffener.
Also the floor to the bottom of the companion bin
Next up, Jacking point.
This was screwed in the correct position to the outer sill and then the whole lot offered up to the car. Then the jacking point was screwed to the inner sill from inside and then the sill removed again to get the position
And then welded
With all welding complete everything was given a coat of zinc ready for the outer sill
Then the outer sill was clamped on
And then spot welded
This end needs closing up
Which is done by welding and then shaping
Then the jacking point is welded to the sill and ground to shape
Next, I repaired the step
Now the fun part.....
I can't tell how much i'm going to have to replace with all the underseal there so it must go
Now I can determine what can stay and what must go, I did some cutting
And then had a clean up of the edges ready for some new metal
The repair pieces need to be made up like a jigsaw. Each piece must be made to fit the next and since the only reasonable datum I have is the floor, then that will be done first.
I marked out on the sheet the repair section
Then a quick cut and fold and then clamp it in
Then tacked in
I want to keep everything loosely in place for now until the rest is made and fitted so the tacks will suffice until the rest is in then ill weld it all up together.
The next piece will be the lower flitch as this will now follow the existing curve of the floor. Once that is made and tacked in, it will be clear what size and shape the toeboard section will need to be.
More tomorrow
Ben
#135
Posted 12 December 2017 - 11:19 PM
How are you spot welding the ends of the sills ?? Do you have really long arms for your machine ??
1 user(s) are reading this topic
0 members, 1 guests, 0 anonymous users