looking good - it should come together quickly now.
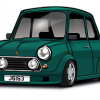
Era Mini Turbo
#166
Posted 10 April 2022 - 06:04 PM
#168
Posted 14 April 2022 - 11:15 AM
Cracking progress, paint looks lovely!
#170
Posted 16 April 2022 - 11:17 AM
you are really making some progress now, good work.
#171
Posted 16 April 2022 - 06:05 PM
Good evening peeps so the spaghetti saga continues managed to get metric female connections locally and remade some pipes got it all temporarily fitted and I thought I had servo mounting bracket cleaned and painted but no so temporary fitted it and new servo and master cylinder all look good very pleased so far.
managed to fine some SS washers
This is a temport fitment as I need to sort out Discs, Hubs, CVs, deiveshafts and callipers
#172
Posted 16 April 2022 - 07:37 PM
PS you are going to paint the brake pedal servo bracket aren't you?Looking good.
#173
Posted 17 April 2022 - 10:22 PM
That's some pipework! I'd make sure that the pipes clear everything. In the 4th from last pic the pipe looks a bit too close to the upper arm nut. I know it's only a temporary fitment but brakes have to be right.
Looking good, it's not easy custom fabrication
Pete
#174
Posted 17 April 2022 - 10:43 PM
Involved pipework.I am not criticising but I am not keen on the male to female connection near the servo.There are double female connectors to do this.Steve,
PS you are going to paint the brake pedal servo bracket aren't you?Looking good.
this is all tempory fitted as need to get hubs Discs and calipart fitted then I will fix properly
#175
Posted 18 April 2022 - 07:00 AM
#176
Posted 03 May 2022 - 09:13 PM
Good evening Peeps a little more done over the Bank holiday 1st sort out some wiring for Power steering, electric windows and central locking wires through door hinge panels.
Got the dashboard out of Hibernation lol and replaced the fuel gauge with an NOS item from Japan
and struggled fitting the bottom rail and then the switch panel several attempts of on and off adjusting the small brackets to align with the holes for the nuts lol
getting there slowly
#177
Posted 03 May 2022 - 10:06 PM
#178
Posted 04 May 2022 - 06:49 PM
What is the fruitbowl for if it's not providing supports for a Mini dash?
#179
Posted 05 May 2022 - 03:47 PM
If I had pin holes in a panel, as long as I could get to both sides to clean properly I would drill a hole to enlarge the pinhole to remove corrosion to good metal, then put copper on the back and weld up the hole, depends how bad they are really, but I have had previous luck doing this method, if the pinhole needs a large hole to remove corrosion I would weld in a small patch, but all this depends on amount of holes vs cost and ease to change the panel.
Example of area I have done this is in the roof gutter after removing the drip rail, but this only had very small areas that needed work.
Great work.
How does using copper help?
Who did your engine rebuild?
#180
Posted 05 May 2022 - 03:50 PM
re: copper - the weld won't stick to it and it acts as a heatsink, which means you don't blow the hole wider with the heat of the arc
also useful when you're trying to weld thin sheet edge to edge (or close to an edge) because welding at the edge of a sheet just makes big holes really easily due to uneven heat dispersal
presumably why a lot of quick weld-up jobs are done with a patch with overlapping edges (not flush)
you can get grips with a forked side (gap for welding in) and a copper side for exactly that purpose https://www.ebay.co....aRoCZYUQAvD_BwE
what I did was get a foot long bit of 20mm copper pipe I had knocking about, hammered a flat end at a slight angle, and hold it up against the back side of the weld area. you can bend it or cut bits off to suit wherever you're working
Edited by stuart bowes, 05 May 2022 - 03:59 PM.
3 user(s) are reading this topic
0 members, 3 guests, 0 anonymous users