Edited by gazza82, 26 November 2016 - 07:24 PM.
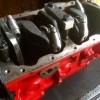
'floating' Thrust Washers
#16
Posted 26 November 2016 - 07:23 PM
#17
Posted 26 November 2016 - 07:48 PM
Edited by OzOAP, 26 November 2016 - 07:52 PM.
#18
Posted 26 November 2016 - 08:46 PM
Edited - never wishing to incite any sort of criticism whatsoever hence my reference 'very highly respected'. For this to be seen as an opportunity to criticise is not only irritating but frankly exhausting - I had hoped to stimulate intelligent conversation that may have bettered my knowledge and understanding. Apologies..best move on!I only replied to the thread as the OP bought me into it. Then to be slated by nobodys makes my piss boil....!
I now see the original post has been edited removing Ian and my name.
Edited by ozz1, 26 November 2016 - 09:10 PM.
#19
Posted 26 November 2016 - 08:51 PM
Years ago I bought a 998 engine that was like this, the centre strap had been machined allowing the thrusts to move. I didn't know any better so I assumed the block was scrap and scrapped it.
It's interesting to hear that I may have wasted a perfectly good block(and then spent several hundred pounds on a replacement!!)
#20
Posted 26 November 2016 - 11:00 PM
Do you Have pictures of how you do it? Just collecting data :)A solution to a problem that doesn't exist....oh, sorry, it does. Apparently on old Triumphs!
#21
Posted 27 November 2016 - 12:17 AM
A solution to a problem that doesn't exist....
Clearly there is a problem ...
#22
Posted 27 November 2016 - 08:15 AM
Clearly there is a problem ...A solution to a problem that doesn't exist....
Please show me...
The only problem I have ever seen with A Series thrust washers is where idiots have fitted them incorrectly.
#24
Posted 28 November 2016 - 07:05 AM
Over the passed 20 years of OAP, I have built more small bore engines than anything else. I have had a lot of my 'competitors" engines in for rebuilds/improvements. Longman, Swiftune, Selby, MED, Slark..All caps modified the same way. Minispares fitting instructions that come with the centre straps just say machine the cap flat. All I can say to everyone out there is, you do it your way, I will continue to do it mine.
Edited by OzOAP, 28 November 2016 - 07:06 AM.
#25
Posted 28 November 2016 - 03:05 PM
OK then ozz1 .. there's your answer.
Take it back to the person that machined it and ask them how to fit the thrust washers properly!
#26
Posted 28 November 2016 - 06:09 PM
This is rather entertaining.
#27
Posted 28 November 2016 - 06:24 PM
This is rather entertaining.
I keep popping in and out to read but have no idea who's right or wrong
#28
Posted 28 November 2016 - 06:36 PM
It's a bit like Game of thrones.
#29
Posted 28 November 2016 - 06:46 PM
My point was if two people at the top of their game do it one way, why do people make a fuss about doing it the other?
I like to understand why things are the way they are, how am I meant to find out if I don't ask questions...
The conclusion I've come too is that the load through the crank is spread through 3 main bearings, so when combined with a film of oil, there is never anywhere near enough friction to result in the pre-suggested gripping and breaking of the tang as it tries to spin, hitting the sharp point left on the cap.
Unless:
clutch cover has way too much pressure.
Or if you had less end float on either side of the centre main bearing than the other mains so when the clutch is engaged the load is only taken up by the central thrust washer until it wears to the same thickness as the others - a scenario that would never happen unless you were an idiot and had very inaccurately filed down a thrust washer in trying to manipulate end float...
In fairness despite seeming counter intuitive, If these guys, Swiftune and MED are doing it - has to be fine otherwise they would spin bearings every 5 minutes...especially mini7 engines which may (??) be using stronger diaphragms and springs too.
Edited by ozz1, 28 November 2016 - 06:53 PM.
#30
Posted 29 November 2016 - 12:47 PM
1 user(s) are reading this topic
0 members, 1 guests, 0 anonymous users