
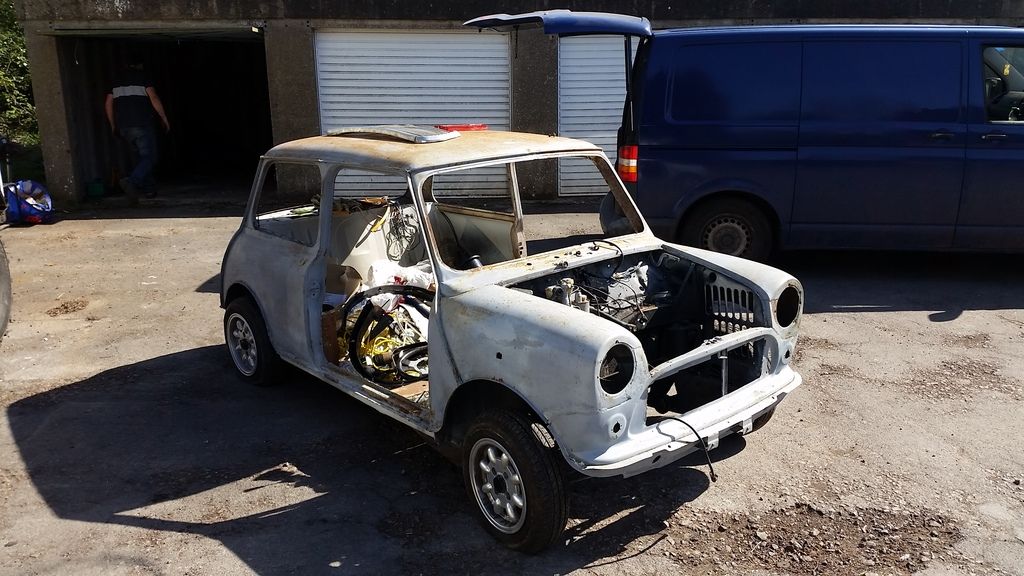
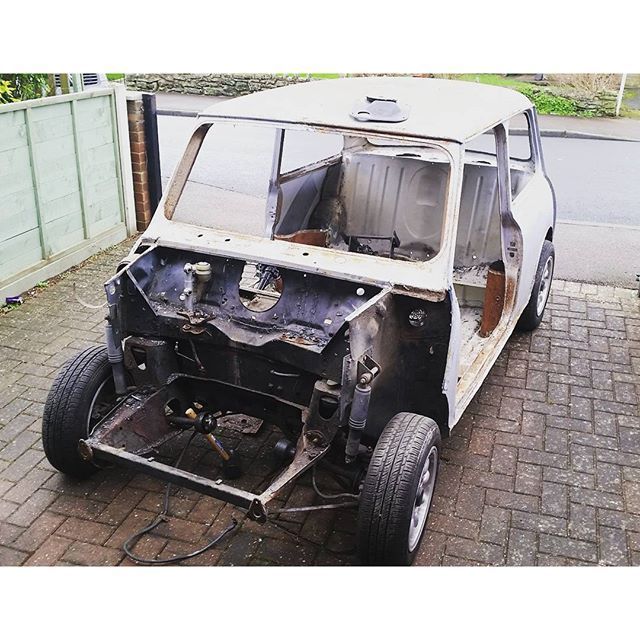
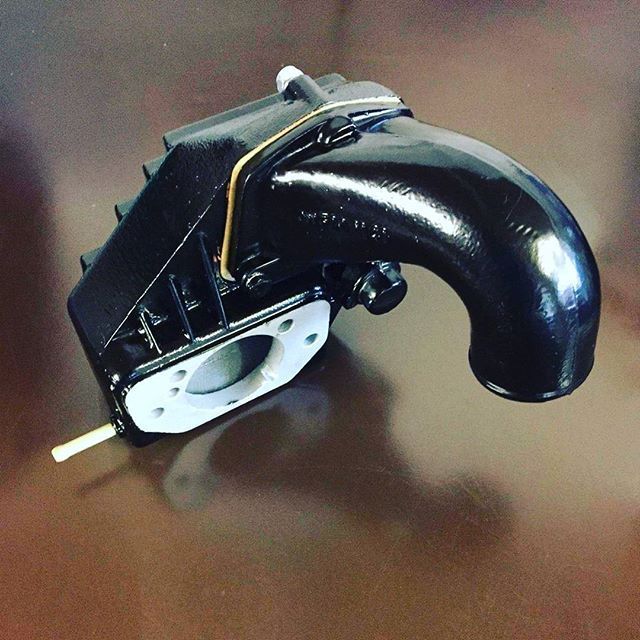
As the car moves forward I will update with the progress.
Thanks
Chris
Posted 17 April 2016 - 09:24 AM
As the car moves forward I will update with the progress.
Thanks
Chris
Posted 01 June 2016 - 12:26 PM
Lastest Update the car was collected by enviro-strip UK (http://www.envirostripukltd.com/) for their stripping process to remove paint and rust!
She will come back nice and clean and rust free but holey!
Edited by chris27989, 01 June 2016 - 12:27 PM.
Posted 07 July 2016 - 10:21 AM
So last week the car arrived back from the dipping process; I thought the dipping was a good process as it has very minimal clean up compared to other paint and rust removal processes like media blasting. The parts there were dipped where shell, doors, boot, subframes, wheels and the new panels that I brought. The panels still were wiped down with thinners and panel wipe first to remove and grime and handling (greasy hand print) marks that happened that we didn't know about (Even though gloves were worn during whole handle process by us this end). Then epoxy primer could be laid down on the parts and panels. The shell is being prepared this week for primer tomorrow. The front subframe was seam welding for extra strength and to hopefully try and stop any water getting between the metal panels that make up the subframe. The shell did come back with a few more holes and bodged repaired (from previous owners) than expected but these panels will be repaired or replaced.
The 3 processes done for the dipping are:
The build is being documented on my Instagram which is chris27989
Thanks
Chris
Posted 07 July 2016 - 02:12 PM
Love seeing things being done properly. Keep up the good work.
Posted 07 July 2016 - 03:35 PM
Posted 08 July 2016 - 12:25 PM
Word to the wise. This stripping process removes paint between the spot weld seams and panel overlaps, very difficult to add the protection back unless the shell is dipped and E-coated.
Posted 08 July 2016 - 01:21 PM
Posted 08 July 2016 - 02:18 PM
E-coat is applied post spot welding. This gets between the seams (electrostaically attracted to all exposed surface) and after top coat and seam sealer does a good enough job of corrosion resistance-it isn't brilliant even from the factory hence our favourite little car propensity to rust.
Dipped shells, unless re-E-coated lose this vital protection. I've seen plenty of resto horror stories with corrosion bleeding out of these areas-on exotic stuff that has been dipped as stating point for 6 figure restoration jobs (Alfas/E-Types). Seeing as the OP is intent on making a proper job of his resto, it'd be remiss not to pass on the info and other peoples experience.
Only way to do it properly is to repeat as closely as possible the factory E-coat. I suspect the people that stripped his shell can do this after it has had all welding repairs completed. For the record, this is one reason why I'd never part with my hard earned for a heritage shell. The corrosion protection is laughable-not even as good as when the cars originally left the factory...
Rota Dip was used on CKD. Full tank E-coat immersion at Longbridge.
Edited by fwdracer, 08 July 2016 - 02:24 PM.
Posted 09 July 2016 - 07:14 AM
Posted 11 July 2016 - 07:29 AM
Spraying the flanges with weld thru zinc primer prior to the spot welding will help massively. Then spray Dinitrol into the closed box sections after the shell has been through the paint booth.
I've done a ground up restoration as you are doing (also on an '86), and the thought of corrosion coming back was enough to drive me to extreme lengths to ensure it didn't, used Dinitrol inside on everything that wouldn't be seen by a spray gun, inside A-pillars, bulkhead cavities etc.
Figured that the extra few kilos in cavity wax would be a small price to pay to ensure I was driving and enjoying it in 10 years time. Good luck with your resto and be assured that you will produce something better mprotected than that which rolled out of Longbridge in '86..
Posted 01 August 2016 - 07:47 AM
Another update.
Started cleaning and decontaminating the shell ready for the epoxy protective coat but after removing the external seam trim panels there was still a small amount of corrosion. So I decided instead of spending hours cleaning the seams and wasting time. I booked the car into the local sandblaster to get all the seams blasted and all the parts that needed a good key for the epoxy coat.
Between making the decision and getting it to the sandblaster I had a day free so started cutting out some of the panels which had holes in; for three reasons
1. I had the free time.
2. Save money on paint as the epoxy is about £20 a litre.
3. Gave the blaster more angles to get to the areas that needed blasting.
Good a few free hours this week before work so the shell is geting flipped over ready for some more paint again to get better angles for paint coverage.
Areas on the shell that are being replaced are either being cut out or only mist coated to save cost on paint,
Cleaning
Cutting
Blasting
Epoxy Coat
0 members, 1 guests, 0 anonymous users