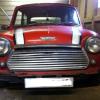
What Copper For Spot Weld Electrodes?
#1
Posted 24 March 2016 - 07:33 AM
Bog standard copper, C101, seems easily available and I wondered if anyone has any experience of using this for electrodes? Is it likely to cause me any problems, if I'm just looking to complete a few jobs with it?
Thanks
Chris
#2
Posted 24 March 2016 - 08:05 AM
I would guess this is to do with the temperature rating of the copper, you might find it will deform after several welds ??
Just found this http://www.cadicompa...cts.classA.html
Edited by I hate Brian, 24 March 2016 - 08:09 AM.
#3
Posted 24 March 2016 - 04:14 PM
I made some for a local company a few years ago and the drg specified Beryllium Copper for a piece of 60mm diameter x 1m long cost £700 ish
#4
Posted 25 March 2016 - 01:45 AM
Unless you plan on doing this for a living, use whatever copper you can readily find. Yes, the wrong grade may wear out quickly but you'll find it easier and cheaper to make many spares out of common grades of copper than to make a few tips out of a premium grade. Again, if you were doing this for a living my advice would be different.
#5
Posted 25 March 2016 - 02:17 AM
Apparently the main copper to stay away from is a Zinc mix as it can do nasty things.
Always wear the correct PPE
#6
Posted 25 March 2016 - 12:58 PM
Hmmm... zinc + copper = brass. Though used for a lot of electrical items, brass is not a particularly good electrical conductor compared to other copper alloys.
If you make your copper decision based on alloys that are used for various forms of electrical conductors you should be fine.
The link below is to a "convenience store" distributor of industrial supplies in the U.S. The page provides basic information on some of the grades of copper they can supply. It's not a complete list of alloys that are available but it is a list of some common materials that may be of use to you making spot welding tips.
EDIT: In your initial post you suggested using 101 instead of 182. Some of the contacts (not for spot welding) we make at work used to be made of 145 which is also sometimes hard to find. For home use, 101 will be fine for your spot welder. It is a relatively soft material so the tips may not last long but they will be relatively cheap to make. If you are turning these parts yourself on a lathe, you may find 101 a little "gummier" than 182 or 145 but the end part doesn't have to be pretty anyway.
Edited by dklawson, 25 March 2016 - 01:02 PM.
#7
Posted 26 March 2016 - 12:21 AM
Hmmm... zinc + copper = brass. Though used for a lot of electrical items, brass is not a particularly good electrical conductor compared to other copper alloys.
Ha ha I was waiting for somebody to say Brass. it's still used for welding electrodes but I'm not sure why, maybe cost...
Next you will be saying that copper alloyed with tin is called Bronze lol
Edited by dklawson, 26 March 2016 - 12:48 PM.
#8
Posted 26 March 2016 - 12:50 PM
I have seen a lot of welding ground clamps and electrode holders made of brass. A lot of industrial contacts are also made of brass and then silver plated. I assume in those cases brass is used because it is harder than copper. You could certainly use it for spot welding electrodes the difference in conductivity would probably be minimal with regard to the welding process.
#9
Posted 26 March 2016 - 02:35 PM
there is a place local to me that makes industrial spot welders and the electrodes, I have scrounged enough stock to make a few for my work projects but having spoken to the guy at length I would say it's a potential expensive suggestion that any copper will do. I can't remember the ins and outs but the stuff they use is harder and has higher resistance than most copper stock. If you use the cheaper types it can damage the spot welder as it allows a higher current flow. I remember him mentioning about it also fusing to the workpiece but can't remember the details. It's possible that they would sell off its to the public so I could dig out their details if the OP is interested.Unless you plan on doing this for a living, use whatever copper you can readily find. Yes, the wrong grade may wear out quickly but you'll find it easier and cheaper to make many spares out of common grades of copper than to make a few tips out of a premium grade. Again, if you were doing this for a living my advice would be different.
#10
Posted 26 March 2016 - 02:37 PM
#11
Posted 26 March 2016 - 05:43 PM
You won't get any argument from me that some grades of copper will be better than others for spot welder tips.
The resistance of the differing copper grades will be miniscule compared to the resistance across/between the panels being welded. For high-end production line spot welders the change in conductivity might affect the load sensing and timing circuits but that is very unlikely with a DIY home project spot welder.
The 182 grade copper is what we used a lot at work for electrical contacts. I stand by my statement that almost any copper will do for a small DIY project. If in doubt, select a grade of copper alloy (perhaps like 145) that has resistivity and machinability close to the 182 grade. Above all, practice your spot welds on scrap before working with the actual car panels.
#12
Posted 26 March 2016 - 05:48 PM
#13
Posted 30 March 2016 - 11:33 AM
thanks for your help guys,
as I've only got a run of about 1/2m to do with these I've opted to give C101 a go - I'll let you know how I get on.
#14
Posted 20 May 2016 - 10:00 PM
Any news on your C101 electrodes. I'm thinking of doing something similar and just wondered if it was a usable solution.
#15
Posted 20 May 2016 - 10:56 PM
Hi read this with interest as I also need to spot weld new drip rails on my '63 mk1. I have just purchased a s/h Miller Lectro-Spot welder and I think that the tips will be too big for the gutter.
I have been looking on the net at home made MOT spot welders and various options for welding tips. One guy had used copper mig welder tips which seemed like a potential solution, just need a way to make them fit the welder.
1 user(s) are reading this topic
0 members, 1 guests, 0 anonymous users