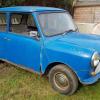
Idler Gear End Float
#1
Posted 10 February 2016 - 12:05 PM
#2
Posted 10 February 2016 - 12:17 PM
Yes you need to and the best practice would be getting two identical gaskets (they're not all the same thickness) and use one for measuring and the other one to be kept for the final assembly
#3
Posted 10 February 2016 - 12:52 PM
Yes you need to and the best practice would be getting two identical gaskets (they're not all the same thickness) and use one for measuring and the other one to be kept for the final assembly
The way I do it is to fit the new gasket to the transfer case using Blue Hylomar. Then fit the transfer gear onto the gearbox and put the4 transfer case onto the gearbox. At this stage the engine is not on the gearbox. Nip it up firmly and measure the float. Then so long as the float is OK I subtract 0.002" from the measured float and if this new figure is still within tolerance I go with that.
After fitting the transfer care and before fitting the primary gear it is possible to feel that the transfer gear rotates OK after the casing is finally torqued up. It always seems to work OK.
Or you can use two identical gaskets, but be sure to measure the pre-fitting thickness first to ensure they are identical.
#4
Posted 10 February 2016 - 12:55 PM
#5
Posted 10 February 2016 - 01:50 PM
True but I had to say that so you know why I'm checking it.Idler gear end float has nothing to do with the engine. But obviously a good idea to check idler gear end float whilst things are in bits.
#6
Posted 10 February 2016 - 02:57 PM
With engine off:
With engine on:
#7
Posted 10 February 2016 - 03:31 PM
I'm a firm believer in using the gasket you measured the endfloat with in the final build, removes ANY risk of a difference in thickness..
As a guide, I would aim for a 2-4 thou clearance on helical drop gears, and 4-6 on straight cut.
1 user(s) are reading this topic
0 members, 1 guests, 0 anonymous users