Do you have any evidence for this? For example actual documented cases of failure? Suggesting many cars may be driving around in a dangerous state will cause considerable concern to a large number of owners.Many of the non-genuine subframes are dangerous because they have less than the original carefully calculated number of spot welds, and will fail under instantaneous peak load, or fatigue after an indeterminate number of load peaks. They really need to be seam welded for safety, at the very least along the lap where the top and bottom of the side members join the front crossmember, between the middle web and the crossmember vertical face, and between the top and bottom of the side members and the middle web around the area of the suspension cone seating. Also, around the outer radius arm mounting area.
Due to the 5:1 lever ratio, the peak load on the suspension cone, and therefore the tension in the subframe side member, is over 3 tonnes. That has to be carried from the cone mount to the lever fulcrum, which is the radius arm pivot locations.The spot welds themselves may carry the load, but the metal around them will tear if they are not sufficient in number.
The welding is relatively easy on a bare, new frame. I would prefer TIG for the sake of appearance, but MIG (not gassless, which is not MIG anyway) is just as good.
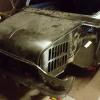
Non Genurine Subframe. How Bad Are They?
#16
Posted 31 January 2016 - 09:42 AM
#17
Posted 31 January 2016 - 10:51 AM
We are all doomed Captain Mainwaring.
#18
Posted 31 January 2016 - 10:57 AM
How heritage make the subframe. I'd like to see how the pattern parts are made and inspected without access to the original specs and drawings. I'm a firm believer in the phrase 'buy cheap, pay twice'.
#19
Posted 31 January 2016 - 12:22 PM
Do you have any evidence for this? For example actual documented cases of failure? Suggesting many cars may be driving around in a dangerous state will cause considerable concern to a large number of owners.Many of the non-genuine subframes are dangerous because they have less than the original carefully calculated number of spot welds, and will fail under instantaneous peak load, or fatigue after an indeterminate number of load peaks. They really need to be seam welded for safety, at the very least along the lap where the top and bottom of the side members join the front crossmember, between the middle web and the crossmember vertical face, and between the top and bottom of the side members and the middle web around the area of the suspension cone seating. Also, around the outer radius arm mounting area.
Due to the 5:1 lever ratio, the peak load on the suspension cone, and therefore the tension in the subframe side member, is over 3 tonnes. That has to be carried from the cone mount to the lever fulcrum, which is the radius arm pivot locations.The spot welds themselves may carry the load, but the metal around them will tear if they are not sufficient in number.
The welding is relatively easy on a bare, new frame. I would prefer TIG for the sake of appearance, but MIG (not gassless, which is not MIG anyway) is just as good.
And to add to this without any form of verified proof you are basically scaremongering and this will not be tolerated. To all members of the forum IF you have verified and certified proof of a safety critical items potential to fail due to poor manufacturing standards then this should be brought to the attention of the manufacturer making these items. If they fail to heed the warning then yes a general warning of a potential issue with an item being posted on here could potentially help our members.
NO PROOF equals heresay only. Please be careful what you post. It quite clearly states this in the forum rules.
#20
Posted 31 January 2016 - 02:14 PM
Nice video, thanks hadn't seen that before Steve.
How heritage make the subframe. I'd like to see how the pattern parts are made and inspected without access to the original specs and drawings. I'm a firm believer in the phrase 'buy cheap, pay twice'.
FS
#21
Posted 31 January 2016 - 02:34 PM
Never heard of a non gen subframe failing without rust being involved in large quantity's
also non genuine subs have been made since the 60's -
it would be obvious there was a problem by now
my non gen sub had all the spot welds of the original , & welds were good
thinner steel would be a problem - but haven't seen one (suspect some were made to cut costs over the years)
overloading on pickups & vans could cause a fail - even in a genuine subframe
if there have been any fails in recent times please list them tiger99 - and the supplier
Edit -
also the front genuine subframes crack at the front c section the lower cross member at the back
& they are genuine
Edited by sledgehammer, 31 January 2016 - 03:44 PM.
#22
Posted 31 January 2016 - 04:14 PM
Never heard of a non gen subframe failing without rust being involved in large quantity's
Like I said the non-genuine subframe on mine lasted 7 to 8 years before being swapped due to rust. So that's 7 to 8 years of daily use and abuse without a failure and I've been using polly not rubber mountings. In fact the only rear end related failure I have ever had was the end of an aluminium trumpet fracturing at the knuckle joint end.
ps. the mot man must obviously think its ok to keep passing it each year.
#23
Posted 31 January 2016 - 06:24 PM
When I first started working in garages we were replacing rear subframes when the mini was 7-8 years old, that was the MK 1s.
#24
Posted 01 February 2016 - 06:41 PM
Edited by Swift_General, 01 February 2016 - 06:42 PM.
#25
Posted 01 February 2016 - 06:45 PM
So some of you, doubtless running non-genuine subframes, imagine that BMC spent money putting in more spot welds than were actually needed? I don't think so. Just because a few did not break, there is NO reason to assume that they are all safe. Safety doesn't work that way, it works by proving that things are safe by analysing and/or testing the design thoroughly, and you can be very sure that cowboy spares manufacturers have neither the knowledge, experience or equipment to do that.
The argument you guys are advancing is like saying that because a smoker you know lived to 100, smoking does not damage your health, or because one person survived by not wearing a seat belt, we should never wear them. The fact that some cowboy manufactured subframes held together for a while (what mileage? needs to be about 200k to be an adequate test.) does nothing at all to prove that the next one will not fail catastrophically and kill someone.
Skimping on any safety critical part verges on criminal irresponsibility.
Edit: Wise choice, Swift_General. Please be sure to protect it well, with whatever paint system or other coating that you prefer, and enjoy it for a long time. It will not let you down if not allowed to rust.
Edited by tiger99, 01 February 2016 - 06:47 PM.
#26
Posted 01 February 2016 - 07:15 PM
#27
Posted 01 February 2016 - 07:41 PM
" Just because a few did not break, there is NO reason to assume that they are all safe"
And herein is the crux of the discussion, exactly how many non gen subframes do you actually know have broken and because of a so called inadequate number of spot welds???
I point you to this excerpt from the forum rules
Warning
Please be careful when answering peoples technical questions that you do not misguide them into taking inappropriate action. Not only is this annoying, but it can also be costly and could even be dangerous if the wrong information is given. This is why we ask that only first-hand and factual information is posted in reply to peoples queries. If you are not 100% certain of your reply, be sure to point out your uncertainty.
So as per the rules where is your definitive proof that these non subframes in your eyes are dangerous and likely to fail??
If you wish to go down this route then why is it then a 1986 Mayfair rear panel to quarter panel is spot welded whereas my 1974 Clubman had a roller spot welded rear panel. Surely going by your statement my sons cars is likely to fail because it has less spot welds holding it together???
#28
Posted 01 February 2016 - 07:57 PM
#29
Posted 01 February 2016 - 09:25 PM
If these non-genuine subframes really were so 'unsafe' then why would the like of minispares and others still selling them? Surely they would make more money buy simply only offering/selling the more expensive genuine ones.
#30
Posted 01 February 2016 - 10:09 PM
Tiger99's post is just not true at all - non genuine subframes are perfectly safe
I bet half of all mini's that were ever made used non genuine subframe's in the end - I don't recall ever hearing of one fail without rust
more likely to fail are the heel board mounts , that are rusted
my one had bolts that were stuck in with silicone , as the captive nuts were long lost to rust - now that is dangerous
I believe the expression is ' taken with a pinch of salt '
1 user(s) are reading this topic
0 members, 1 guests, 0 anonymous users