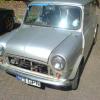
1999 Cooper Sportspack @ Mill Road Garage
#61
Posted 01 December 2015 - 09:04 PM
#62
Posted 01 December 2015 - 09:39 PM
Is there any reason you don't have a 'proper' spot welder given the amount of plug welds I've seen in your build threads... Are they expensive? I was given* one by my father in law.
*he nicked it from work
#63
Posted 01 December 2015 - 09:41 PM
#64
Posted 01 December 2015 - 09:47 PM
Is there any reason you don't have a 'proper' spot welder given the amount of plug welds I've seen in your build threads... Are they expensive? I was given* one by my father in law.
*he nicked it from work
I just don't like them to be completely honest with you.
When i worked at vauxhall, we had no choice, we had to use a spot welder to replicate all factory welds but now i have a choice, i opt for plug welding. i trust it more.
#65
Posted 01 December 2015 - 09:52 PM
Plus, as Jordie said, the arms would only reach certain areas so i would still need to plug weld alot of it anyway
#66
Posted 02 December 2015 - 07:19 PM
Today has been bitter sweet really.
On one hand, progress has been steady but on the other, a problem has been found with the other end of the heelboard so now both ends are going to need replacing.
Unfortunately, the rot was hidden under sealer on the outside and behind random skins of metal (which i believe to be parts of the old inner sill) on the inside.
This has set things back quite a bit as i have had to spend a big chunk of the day fabricating heel board ends and carefully cutting out the old ones but with it being such a safety critical area, i couldn't just leave it so it had to be done.
But before that, I began cutting out the other arch tub.
I cleaned back the sealer and marked out the spot welds before cutting it out. Ill do it in pictures as it is the same process as the other side which i have already been through earlier in the thread.
Next I removed the fillet piece that goes between the heelboard and boot floor
And here is the problem heelboard end
As you can see, there is a hole towards the bottom which was first thought to be flaky mud on the surface but with a scrape and a tap with a ball pein, it collapsed inwards.
The crusty area beside the subframe mount bolt holes is paper thin and has gone through in places so it had to go.
Here it is cut out
i have left the captive nut plate in place as it is still welded to the inner sill which will allow it to hold its position while i replace the outer skin. Obviously, the subframe will be trial fitted before being fully welded
And here is a close up of what has been going on inside the sill section. Lots of layers of crusty metal were found as well as remnants of old sill which hadn't been cleared out prior to fitting the sill last time they were done.
So i got cracking with a replacement heelboard end.
It starts in the usual way of tracing out the shape onto 1.2mm steel
Then cutting out and bending the edges over to create the ends.
The O/S one has a new captive nut assembly as the old one was beyond saving and the N/S one is the outer skin only and is shorter as less will be needed on that side.
The N/S one will be going in first so i trial fitted it prior to drilling for plug welding
And then clamping back into place on the car.
You can see in the first of the last two photos that i have not cleared out the sill cavity prior to clamping on the new heelboard end. There is no need as the inner and outer sills are coming off anyway.
The next job was to tack weld the piece into place. It was important to only tack in minimal places to allow for any adjustment of the panel when the subframe is offered up
It will most likely be fine as it is but i really would like to try in the frame to check alignment before committing to welding it up fully.
The captive nut set has movement but it is springy movement so although it moves from side to side, it always self returns to it's natural position which is where i have left it.
Tomorrow morning will see frame being offered up to check heelboard alignment and to mark out the rear mount holes.
Thanks for reading
Ben
#67
Posted 02 December 2015 - 11:06 PM
Great work on that panel there. Gunna be a solid car once again :)
#68
Posted 03 December 2015 - 02:28 AM
Can't see the pictures apart from the first one.
#69
Posted 03 December 2015 - 07:12 AM
Great work on that panel there. Gunna be a solid car once again :)
Cheers Jordie.
Can't see the pictures apart from the first one.
I don't know why that is. I can see them fine.
Can anyone else not see them?
Cheers
Ben
#70
Posted 03 December 2015 - 09:29 AM
#71
Posted 03 December 2015 - 12:44 PM
They take a while to load, especially on a mobile device - maybe the file size is big and the browser is resizing them to fit the screen?
Edit - just opened one up and they are pretty huge at full size!
Edited by GraemeC, 03 December 2015 - 12:45 PM.
#72
Posted 03 December 2015 - 01:28 PM
Can't see the pictures apart from the first one.
I had that problem, but only due to the quality of my internet here in Denmark. If you see a small square on the left of the thread with a serial number type thing, then right click on it and click show picture and they will show. You will have to do them individually tho.
#73
Posted 03 December 2015 - 04:20 PM
Amazing how the mpi rots so bad
#74
Posted 03 December 2015 - 06:13 PM
Sorry about the problems with pictures.
I am using the same camera and upload process as i always have so i dont know why?
Anyway, more progress today, updates to follow
Ben
#75
Posted 03 December 2015 - 06:47 PM
I started the day by stripping out the old subframe to loose some of the weight from it to enable me to easily lift it into position to check the heelboard position before welding.
The using a block of wood and a transmission jack, i raised it up under the car
And good news! The trunnions lined up perfectly with all mounting points so no need for any adjustment
Whilst the subframe was on, i took the opportunity to mark the rear trunnion positions so i can drill new mounting holes in the new section of boot floor.
Then i took the subframe away and welded up the new heelboard end
And then ground it all up
With that done, i drilled the holes for the rear trunnions and then lifted the frame back in to enable me to position the arch tub to boot floor stiffeners.
With it all bolted up, things were looking good
So i welded in the O/S stiffener. This is a new one as the old one was not worth repairing
The other side will be done once the inner arch is fitted.
A random shot of the new frame
and the new radius arms which are going to be painted due to surface rust.
Next up was to prepare and weld in the new arch tub.
Same process as the other side so again, ill show you in pictures
The back end is nearing completion now so after the valance has been fitted, i will get on with the sills
Cheers
Ben
1 user(s) are reading this topic
0 members, 1 guests, 0 anonymous users