I got a new 60 gallon compressor as my 26 gallon was constantly running when using die grinders and had overheated a few times. Heres my 3 compressors for size comparison.
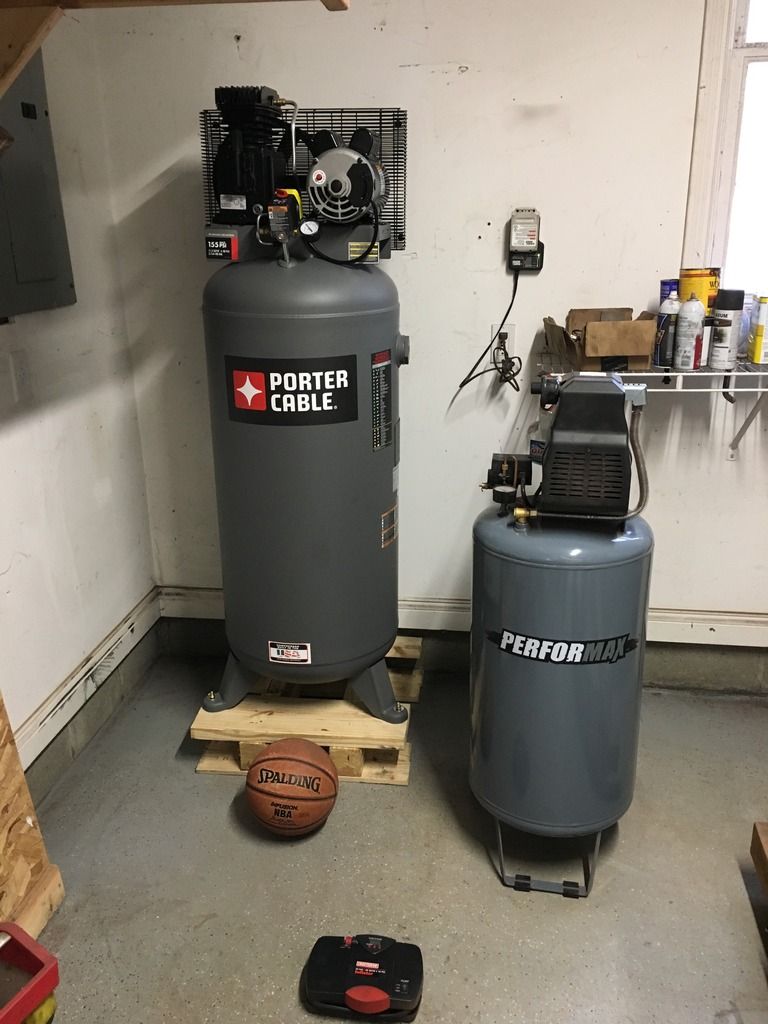
I had read about aftercoolers for removing water from the air for sand blasting and painting. So I thought Id have a go at building one.
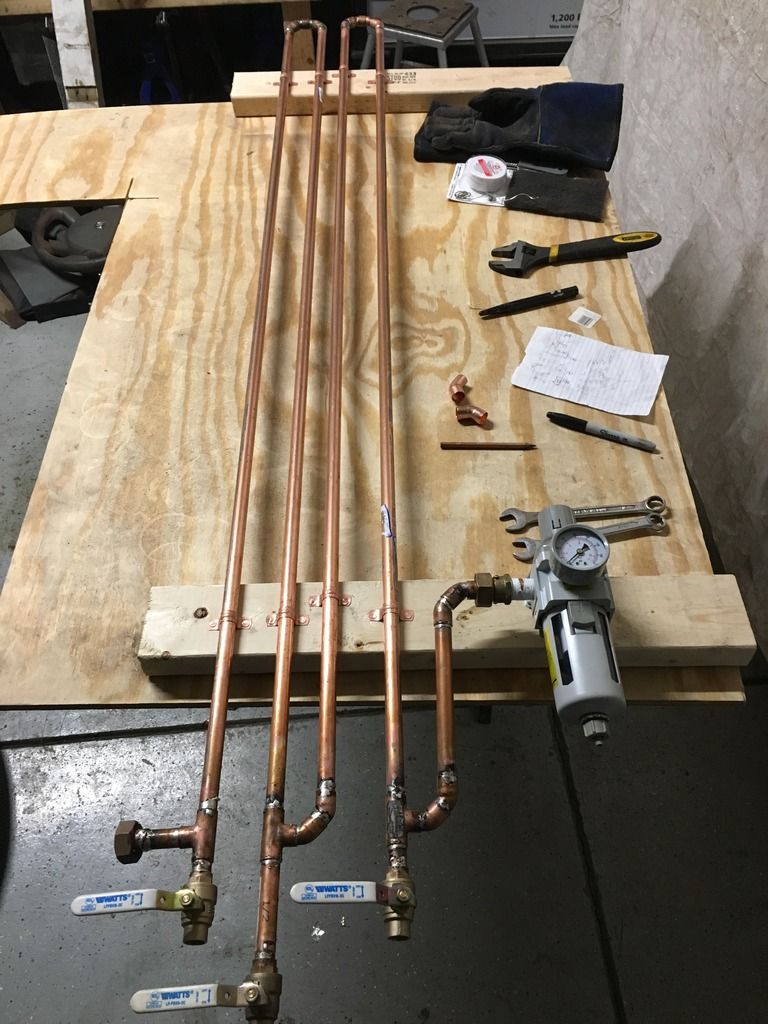
It has a few ball valves for water vents and then a filter/regulator.
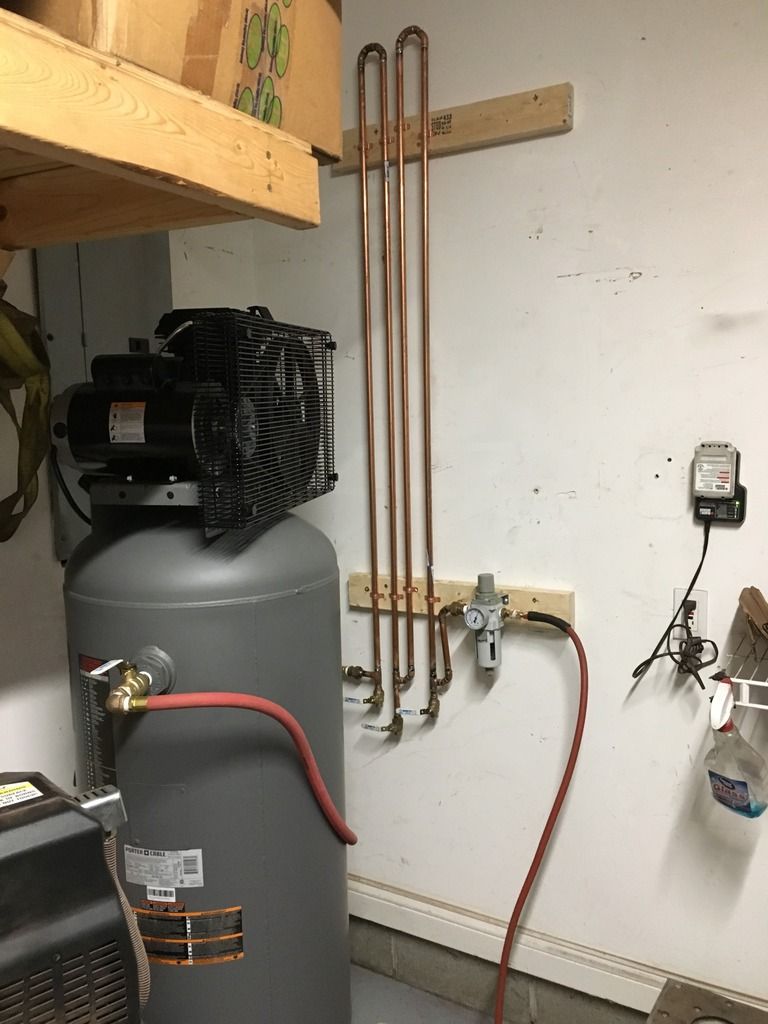
Positioned behind the compressor like so, I can still get at the ball valves and see the gauge.
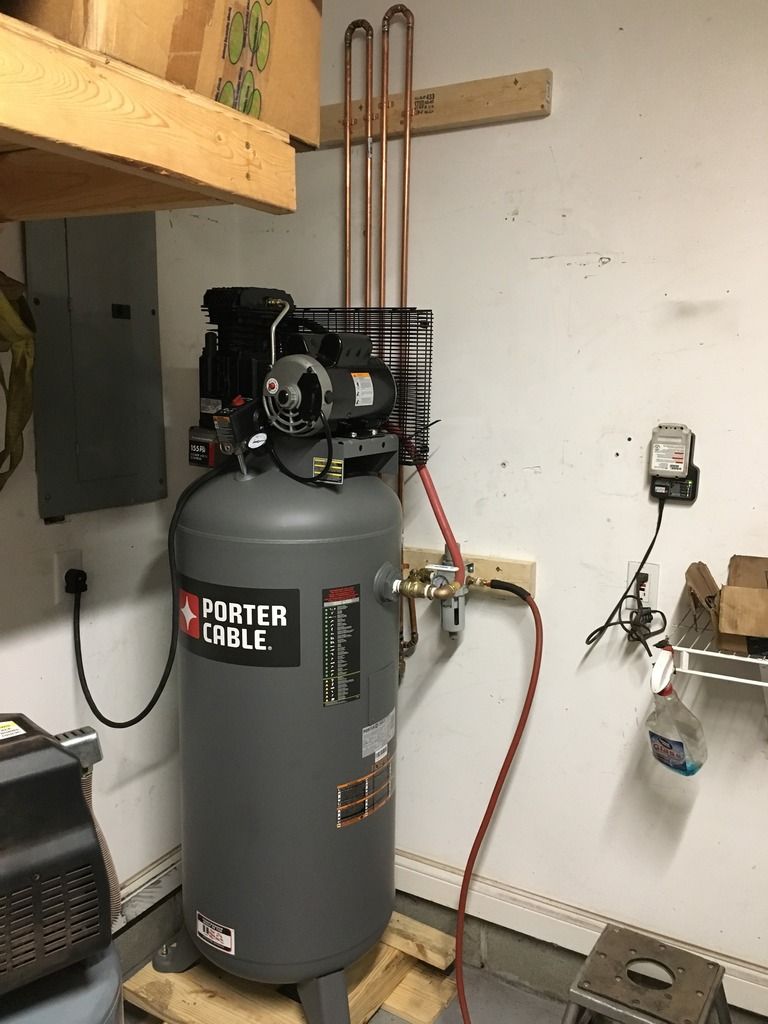
Also waiting on some rubber isolator pads for the feet, and I can take it off its pallet.
So far its passed the soapy water test and is currently holding 150psi!
Time will tell if it works I guess.
Ive tried out a die grinder on this compressor and its a beast!
Speaking of die grinding, thats tomorrows job..