Spotwelded reinforcing plates where I could, I have ordered some longer arms for future panel work as it's a bit awkward with the 120mm arms that came with it.
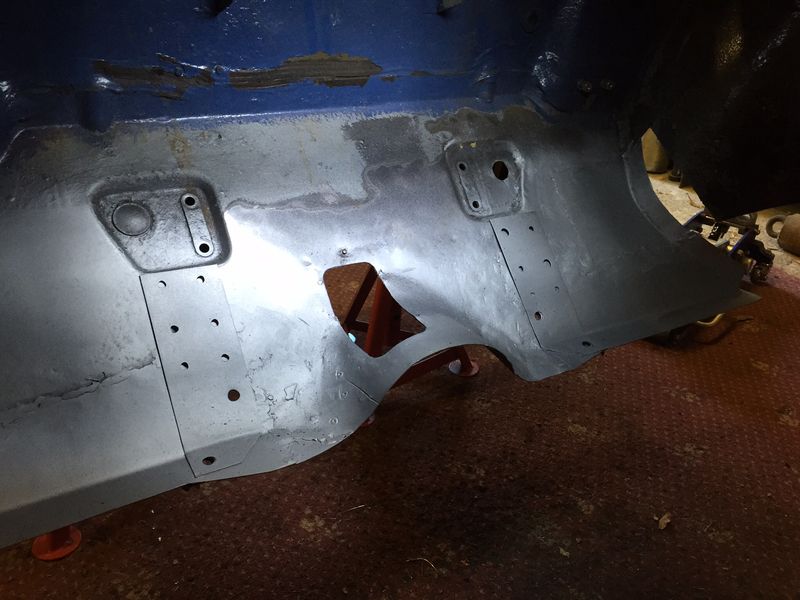
I then plug welded the remaining area and linished smooth
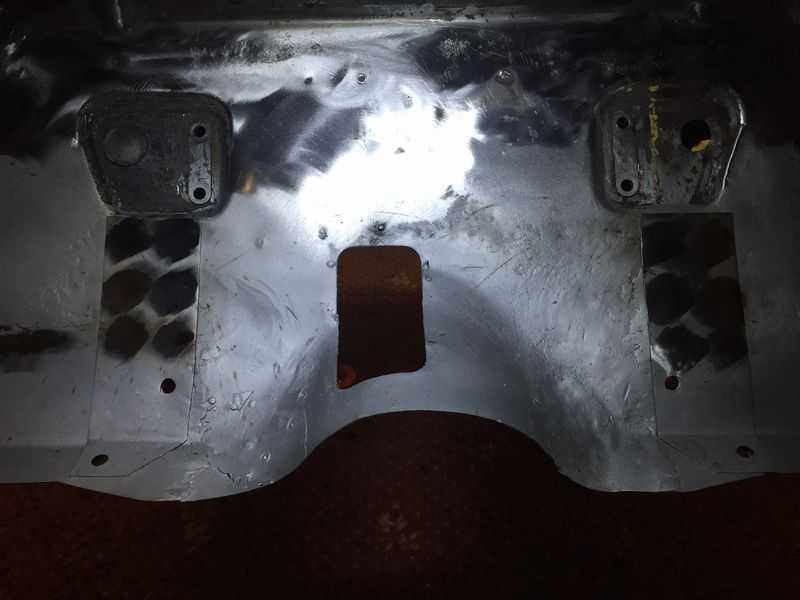
Then I removed all paint from bulkhead while I had easy access and fitted floor and rear subframe, then spent a while checking dimensions, I also painted cold galvanising spray inside the sill areas to ensure they have a chance against future rust
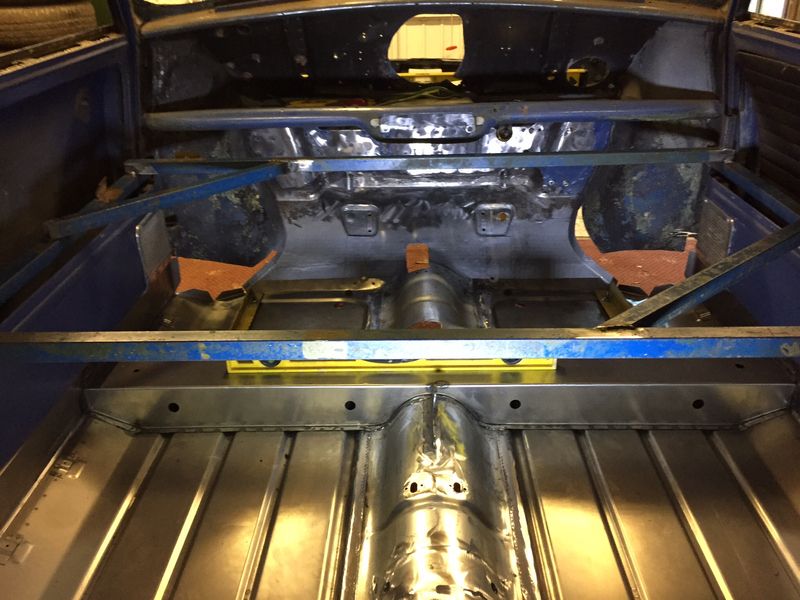
I now have to clamp the tunnel to correct shape and plug weld it in position, the rest will be spot welded when I get the longer arms
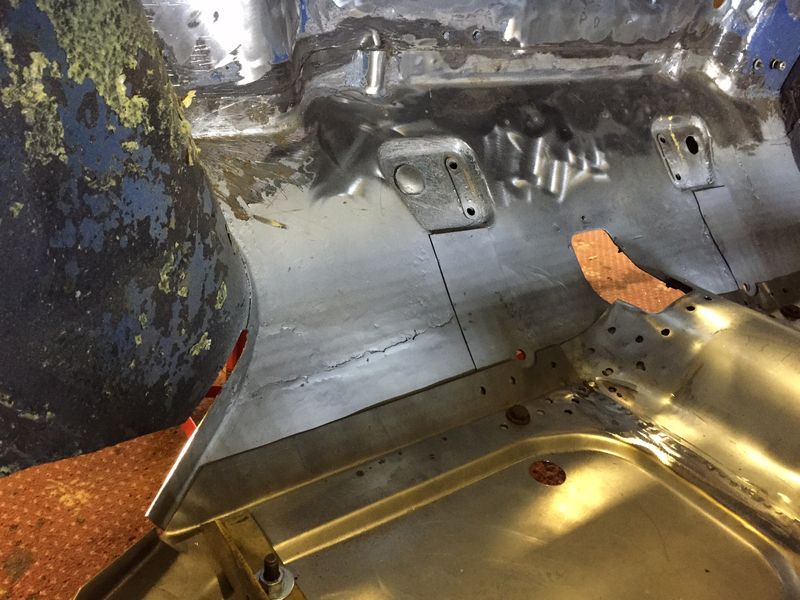
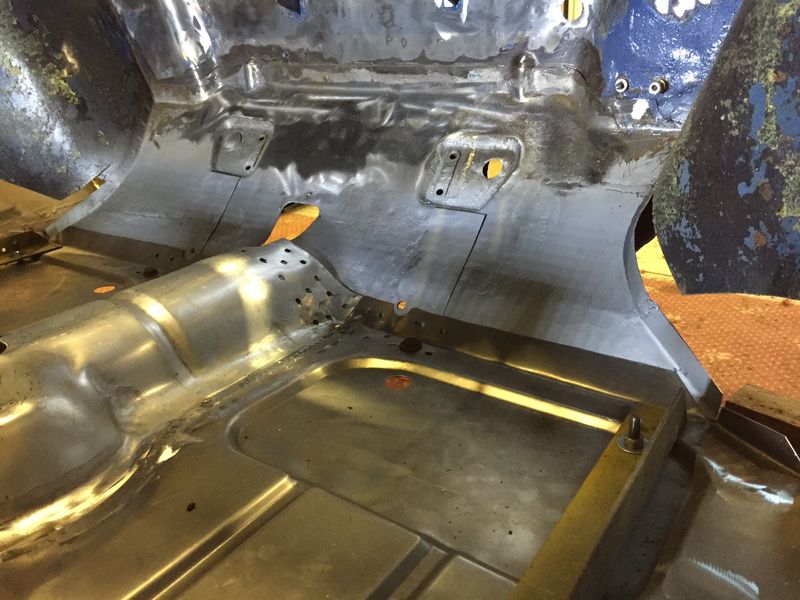
The toe board needs a little more grinding before filling but welds are strong so happy with repair so far.
Looking forward to cutting out boot floor now