What annoys me is a company goes to the trouble to have something reproduced and it is good for nothing except the bin why not make it properly if it cost a little more as far as I'm concerned who cares much out ways all the time spent trying to make it fit
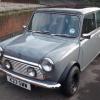
Rear Quarter Panel Replacement
#16
Posted 03 July 2015 - 10:32 AM
#17
Posted 03 July 2015 - 10:57 AM
What annoys me is a company goes to the trouble to have something reproduced and it is good for nothing except the bin why not make it properly if it cost a little more as far as I'm concerned who cares much out ways all the time spent trying to make it fit
Because their presses are worn out.
Also, don't forget that many of Magnums panels are 'repair panels' so are designed to fit over the top of the existing panel. Like the boot floor repair panels, door steps, budget floor pans, inner sills just to name a few.
That is why they always appear to be oversized.
at the end of the day, you pays your money you takes your choice
Edited by Ben_O, 03 July 2015 - 10:58 AM.
#18
Posted 03 July 2015 - 11:25 AM
Are the photos in your build thread somewhere? Ill have a gander through.
Thanks
#19
Posted 03 July 2015 - 11:29 AM
That does make sense thank you Ben_O! Much easier to visualise when its described rather than trying to figure it out from pictures!
Are the photos in your build thread somewhere? Ill have a gander through.
Thanks
Yes mate. towards the point where i am now. I have only just fitted my quarter panel. It is a reclaimed one which i repaired etc
#21
Posted 03 July 2015 - 11:38 AM
I dont mean to hijack this thread, however seeing as i was going to ask this on anoher thread i may as well ask it here.
"How hard is it to change the quater panels and the inner (top bit) arch?"
I mean, ive attempted to tub my arch but want to backtrack. I can weld of some sorts, and know its just plug welds but is it something an amature welder could attempt?
ThanksThe only thing that can be tricky is splitting the seam between the quarter panel and rear panel as there are lots of closely spaced spot welds, most of which are right on the edge of the seam.
It often pays to grind the spot welds away carefully with a grinding stone before splitting the seam.
What you can do is cut just in front of the seam, then remove the panel and get in there with a grinding stone on the spot welds. Be careful not to thin the back panel seam which you need to retain
#22
Posted 03 July 2015 - 12:19 PM
Ben did you joggle the B & C pillars ?
#23
Posted 03 July 2015 - 12:52 PM
Ben did you joggle the B & C pillars ?
No.
There is absolutely no need to do that at all.
Just lay the new panel over and get it into the right position and then mark the cut lines using the top join of the new panel.
Once you have cut along your line, try on the panel again. You are looking for around 1mm gap between the joins and then just tack then corners/ends and carefully go the rest of the way using pulse welding.
On newer cars where the C pillars are usually wide, I usually cut off a piece of the C pillar for the old quarter and tuck it behind with a fewplug welds above the cut line to hold that.
The only reason for that is so that less distortion occurs but on the Mini, no need
#24
Posted 03 July 2015 - 01:23 PM
Would you use copper at the back and Frost cold front ??
#25
Posted 03 July 2015 - 03:12 PM
Would you use copper at the back and Frost cold front ??
There really is no need to mate.
It's such a short tun and as long as you take your time and have your welder set up properly, it will be fine.
Ben
#26
Posted 03 July 2015 - 04:23 PM
Use cold front along the bottom of the quarter panel. This is the one place it will warp.
#27
Posted 06 July 2015 - 05:39 PM
Hi again can't believe the difference when offering the BMH 1/4 panel which came today, the shape is completely different please see pics for more advice on where to cut and weld
IMAG0225.jpg 48.75K
19 downloads
IMAG0222.jpg 37.55K
17 downloads
IMAG0223.jpg 34.41K
13 downloads
IMAG0224.jpg 46.31K
20 downloads
#28
Posted 06 July 2015 - 06:30 PM
You need to make sure you remove all of the old quarter panel lip from the rear panel.
Clamp the new panel in place along the rear of the arch and front of the arch. With that done at the very front of the panel along the bottom there is a small angle that should fit nicely in the joggle at the bottom of the B pillar.
If all of that is good and with panel gently pressed in place mark on the remaining parts of the old quarter on the B and C pillar. Tkae the panel off and remove the excess off the pillars. Dont go mad trim slightly under.
Now put the panel back in place and clamp along the rear panel, arch and lower quarter panel flanges. Run some clamps along the waist rail. Now you will be able to see how it sits. Some gentle tweaking maybe needed.
#29
Posted 06 July 2015 - 07:38 PM
Genuine panels make a huge difference but the cost is the problem which slows down progress.
Would you use the new BMH panels finished edges on the B and C pillars to cut and weld as they go quite a bit further up than I expected ? than the sh@te magnum panels.
#30
Posted 06 July 2015 - 09:53 PM
Would you use the new BMH panels finished edges on the B and C pillars to cut and weld as they go quite a bit further up than I expected ? than the sh@te magnum panels.
I would. It's easier to grind up and finish higher up the posts.
In the trade, particularly on modern cars, the common practice is to lay the new over the old post remains and the cut through both together with an air saw to get the perfect match with the perfect 1mm gap every time.
1 user(s) are reading this topic
0 members, 1 guests, 0 anonymous users