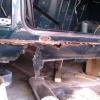
Some Advice On Rivnuts
#16
Posted 03 March 2015 - 08:49 PM
#17
Posted 03 March 2015 - 08:53 PM
True... though you would need to secure the captive nut to the body - with rivets?
#18
Posted 03 March 2015 - 09:00 PM
True... though you would need to secure the captive nut to the body - with rivets?
Captive nut would be welded in place normally, an anchor nut would need riveting but then you would use Monel rivets. Same process as mentioned earlier though ie wet install.
#19
Posted 03 March 2015 - 09:02 PM
#20
Posted 03 March 2015 - 09:03 PM
But what I am looking for is not the same as yourselves in work or play.
#21
Posted 03 March 2015 - 09:04 PM
Clik Bonds would be ideal but they are harder to get hold off unless you're in the industry but they use a liquid shim or similar to mount the anchor nut to the panel which involves no rivets and prevents disimilar metal contact.
Ohhhh tell me more. Links?
#22
Posted 03 March 2015 - 09:06 PM
My blanking plates i made for my lad, sealed anchor nuts riveted in place with monel rivets
#23
Posted 03 March 2015 - 09:12 PM
Nice. I bought some vent blanking plates online today. You should make and sell those!
#24
Posted 03 March 2015 - 09:12 PM
Clik Bonds would be ideal but they are harder to get hold off unless you're in the industry but they use a liquid shim or similar to mount the anchor nut to the panel which involves no rivets and prevents disimilar metal contact.
Ohhhh tell me more. Links?
No need found some Infos on YouTube.
Looks like my type of adhesive.
#25
Posted 03 March 2015 - 09:12 PM
Clik Bonds would be ideal but they are harder to get hold off unless you're in the industry but they use a liquid shim or similar to mount the anchor nut to the panel which involves no rivets and prevents disimilar metal contact.
Ohhhh tell me more. Links?
They are rarely used in the uk but alot of Boeings use them. We use them on the Dassault Falcon 5X Flaperon covers which have a load of anchor nuts on so it saves time and weight.
They use a rubber insert that is pulled through a centre hole and holds the anchor nut at 5psi over the whole contact area, they paste has very wide range of work temperatures. http://www.clickbond...t&categoryid=88
#26
Posted 03 March 2015 - 09:18 PM
Clik Bonds would be ideal but they are harder to get hold off unless you're in the industry but they use a liquid shim or similar to mount the anchor nut to the panel which involves no rivets and prevents disimilar metal contact.
Ohhhh tell me more. Links?
They are rarely used in the uk but alot of Boeings use them. We use them on the Dassault Falcon 5X Flaperon covers which have a load of anchor nuts on so it saves time and weight.
They use a rubber insert that is pulled through a centre hole and holds the anchor nut at 5psi over the whole contact area, they paste has very wide range of work temperatures. http://www.clickbond...t&categoryid=88
Not seen these fitted on Boeings yet but the no doubt our new plastic pig the 787 may well have them.
#27
Posted 03 March 2015 - 09:21 PM
Click bond stuff looks ace. Probably not something folks are going to splash out on for attaching mini wheel arches mind you! Actually, I suppose probably just attaching some nut plates with structural adhesive would work fine and be fairly easy. The adhesive would provide an insulating layer against galvanic corrosion too.
Edited by carlukemini, 03 March 2015 - 09:22 PM.
#28
Posted 03 March 2015 - 09:26 PM
Clik Bonds would be ideal but they are harder to get hold off unless you're in the industry but they use a liquid shim or similar to mount the anchor nut to the panel which involves no rivets and prevents disimilar metal contact.
Ohhhh tell me more. Links?
They are rarely used in the uk but alot of Boeings use them. We use them on the Dassault Falcon 5X Flaperon covers which have a load of anchor nuts on so it saves time and weight.
They use a rubber insert that is pulled through a centre hole and holds the anchor nut at 5psi over the whole contact area, they paste has very wide range of work temperatures. http://www.clickbond...t&categoryid=88
Not seen these fitted on Boeings yet but the no doubt our new plastic pig the 787 may well have them.
I've not either the rep said Boeing were the only big customer theyve had. They're also used for electric wiring swival holders.
No haha not with all the kit you need to install them using the correct shim haha yeah probably would if you could hold the whole anchor nut down evenly a few clamps would suffice.
#29
Posted 04 March 2015 - 09:47 AM
All this talk of the various metals and potential for problems if they are dissimilar..........
And no-one has mentioned the type of bolts you are going to use.
Personally I'd be using mild steel riv-nuts and stainless set-screws. The riv-nuts would go in wet and be painted over too. The sets would go in with a decent amount of copper grease each time they were removed to keep moisture out of the threads. This is how I've done it on a good number of cars and not had a problem so far.
I don't use splined riv-nuts in small sizes like M4 as they very seldom pull up straight and that just results in mandrels for the tool becoming a consumable item. On the bigger stuff where the mandrel is beefy enough to keep everything in line then yes maybe. The only riv-nuts I've ever had spin on me are the ally ones where they actually snap the threaded part off and pull it inside the front part to expand it and I use riv-nuts quite a lot and have done for many years.
Look carefully at a "restored" Land-Rover for the results of ally and steel. Quite often they don't get the isolation right between the Birmabright alloy panels and the galvanised body cappings and the result is that the famous non-rusting bodywork turns into white powder around the edges. Their door skins are folded over a steel frame and that's another area where you see it when the skin splits because it's corroded away at the fold.
Iain
#30
Posted 04 March 2015 - 12:39 PM
I'd use 5mm stainless. I think the head size of the fastener will be more appropriate for the arches. I used them for my grill and contrary to popular belief they don't magically corrode. I drilled the holes and painted the bare edges with POR-15 before I installed them. If possible use a step drill they drill a rounder hole than a twist drill. I bought the rivnuts and tool from a company in the UK named Cheapest Rivnuts. I've also used 4mm on the screws for some of the door hardware and the sun visors it makes life so much easier than sheet metal screws.
1 user(s) are reading this topic
0 members, 1 guests, 0 anonymous users