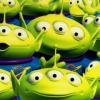
Engine Removal
#1
Posted 20 November 2013 - 10:29 PM
After a quick browse around, i cant seem to find a step by step guide on removing the engine and gearbox.
If someone could point me in the right direction or give me a few pointers, i'd really appreciate it
Cheers
Rob
#2
Posted 22 November 2013 - 12:47 PM
This is one I copied off one of the forums, and used to remove mine. I can't claim any credit for it, so can't take any credit for any mistakes in it either. I think it either came of pistonheads or retrorides. (EDIT - IT CAME OFF RETRORIDES, THE LINK IS AT THE END OF THE REFITTING SECTION IN THE NEXT POST. THANKS GO TO THE ORIGINAL POSTER)
Mini Engine Removal and Refitting
Notes
1. Before you start, get a big plastic box to put all the bits you take off into. A smaller one with a lid is a good idea for the nuts and bolts you take off. Loads of rags will also be useful for wiping, mopping up oil etc.
2. References to spanner sizes are both imperial and metric. In most cases the fixing are imperial so imperial spanners will be a slightly better fit.
3. Make sure you have plenty of beer in the fridge. You might need it later.
Stage 1: Preliminary work.
There is no need to do any of these steps in any particular order but removing the bonnet before doing anything else will stop you gashing your head on the catch.
1. Remove the four 11mm/7/16” nuts and washers and remove the bonnet. Put the nuts and washers back on the studs so they don’t get lost.
2A. remove the air filter housing by undoing the wingnuts on the top of it.
2B. If your car is fitted with a K&N filter or similar it will be held on by two nuts which face the bulkhead. Undo these, taking care not to drop them down the back of the engine, then remove the top cover and the filter from the carb.
3. Remove the grille. This is usually held on by about 8 self tapping screws, 4 along the top and 2 at either end. Chances are, if your car is getting on a bit, they will be a cheery mix of cross and flat head screws.
4. Remove the splashguard (if fitted). This is held on by 3 clips, 2 at the top which hold it to the rocker cover, and one at the bottom behind the front valence. Twist the clips through 90° and pull the guard away.
5. Disconnect the battery. This will either have screws going into the tops of the terminals or nuts and bolts clamping around them. Either way you may have to prise the leads off.
6. Remove the horn by disconnecting the purple/black wire and undoing the 13mm/1/2” nut holding it to its bracket. You may need to hold the horn to stop it turning.
7. Drain the oil (necessary because the otherwise oil will p*ss out when you remove the pot joints from the diff later). It is sensible to use latex gloves or a barrier cream as old engine oil is carcinogenic (gives you cancer). For this reason make sure your hands are clean before you use
the little boys’ or girls’ room. Dispose of the oil at the tip not down the drain.
Stage 2: Removal of engine components and controls:
Again, there is no particular order to follow with this.
Carburettor and inlet manifold
1. Loosen the 11mm/7/16” nut on the end of the throttle linkage and withdraw the cable. Once you have removed the cable, tighten the nut up again so you don’t lose it. Tuck the cable behind the brake and clutch master cylinders out of the way. The end of it will hurt like hell if it goes in your eye.
2. Using a 5mm socket undo the choke cable retaining bolt. You can hold the sleeve that the nut screws into to minimise turning. If you don’t have a socket or spanner small enough, you can use pliers here too. Remove the bolt and sleeve and put in your nuts and bolts jar or they will drop out never to be seen again.
3. Remove the fuel pipe from the carb. This will be retained either by a cheapo wire clip that you undo with pliers or a jubilee clip. Having removed the clip, pull the pipe off (some fuel will spill out).
4. Remove the fuel overflow pipe. This just pulls off.
5. Remove the crankcase breather pipe. Again, this will just pull off. (If your car has an aftermarket air filter and inlet manifold, this may no longer be fitted.)
6. Remove the vacuum advance pipe from the carb and distributor and put on your pile of bits.
At this point you have a choice. You can either remove the carb and manifold as one unit or remove the carb first. Removing them as one unit is more fiddly but probably quicker and means you don’t need as many gaskets when you put it all back together. Removing the carb first gives better access to the manifold nuts.
Removal of carb and manifold as one unit.
7. Remove the 6 13mm/½”inlet and exhaust manifold securing nuts. To
undo the one behind the exhaust heat take off an angled/wobbly extension on your socket might be needed. A long extension makes life easier but the nut behind the float chamber on the carb is a swine to get to.
8. Remove the exhaust heat take off.
9. Slide the carb and manifold off the studs and withdraw. You may have to slightly bend the throttle return spring mounting and use a certain amount of industrial language to get clearance.
Removal of carb and manifold separately
7. Remove the 13mm/1/2” nuts and washers holding the carb to the inlet manifold. There may be either 2 or 4 depending and the carb and manifold fitted. Disconnect the fuel pipe and overflow pipe from the carb.Don’t worry about plugging the fuel line as you will be disconnecting the fuel pipe from the pump shortly.
8. Slide the carb of the studs and add to your pile of removed bits.
9. Remove the 6 13mm/½”inlet and exhaust manifold securing nuts. A long reach socket and extention will make access easier.
10. Slide the manifold off the studs and add to the growing pile in the corner.
Alternator
1. Loosen the two top mounting nuts and bolts. These are usually 13mm/1/2” but could be 14mm/9/16” and the 14mm/9/16 nut and bolt at the bottom. Push the alternator down to slacken the fanbelt and remove it from the pulley.
2. Undo the metal clip which hold the multi-pin wiring plug into the back of the alternator and pull the plug out.
2. Remove the nuts and bolts and withdraw the alternator through the grille opening.
Starter Motor
1. Disconnect the thick brown wire with the red tracer by pulling off the large spade connector.
2. Undo the 13mm/1/2” nut on the end of the motor and remove the thick black wired and two bunches of brown wire. Put the nut back on the stud for safe keeping.
3. Disconnect the white cable with the yellow trace by pulling off the spade connector. All the wiring connections to the motor should now be undone.
4. Loosen but do not remove the 14mm/9/16” top mounting bolt. This will be tight and it is not easy to get at so watch your knuckles
5. Remove the bottom bolt (same size as the top one) then remove the top one. Support the motor to stop it falling then remove through the grille aperture. If the motor is stuck a sharp tap with a block of wood will shift it.
6. Replace the bolts in the housing.
Note: You may find, as I did, that the bolts were too tight to undo with the engine in-situ. If this happens don’t panic. The engine will come out with the starter attached but you might need to remove the horn bracket for clearance.
Distributor (dizzy).
Note. It is not essential to remove the distributor but doing so will stop it getting damaged. Even if you leave it on you should remove the cap and rotor arm.
1. Number the plug leads with Tipp-ex and mark where plug number one is attached to the dizzy.
2. Pull the leads off the plugs and the coil.
3. Release the spring clips holding the cap to the dizzy and remove the cap and leads.
4. In the centre of the dizzy you will see the rotor arm. Remove this and put it in your nuts and bolts jar.
5. To remove the dizzy itself, first, clean around it with a rag and mark the both the engine block and the dizzy where it enters the block with tipp-ex so that you can realign it for timing purposes when it goes back in.
6. Loosen but do not remove the bolt on the clamp which holds the dizzy and slide the clamp out of the way. (Note: if your car does not have an A+ engine the clamp will be different. Check your manual for the removal procedure.)
7. Wobble the dizzy from side to side whilst pulling gently. When it comes free remove it through the grille aperture.
8. Plug the hole in the block with kitchen roll, a rag (or you wife’s best tea towel) to stop dirt or small woodland creatures getting into your engine.
Coil
1. Remove the two spade connectors noting which colour wire goes to which connection on the distributor. The connections should be different anyway but may not be.
2. Undo the upper and lower 13mm/1/2” bolts holding the coil clamp to the bracket and remove the coil.
3. Put the bolts back in the bracket for safe keeping.
Clutch slave cylinder
1. Undo the two 9/16” bolts holding the slave cylinder on the bracket on the clutch housing. One is very close to the subframe and tricky to get to. A universal joint on your socket will make it easier.
2. Pull the cylinder away from the pushrod, leaving the rod attached to the clutch cover. Tie the cylinder to the brake pipes on the bulkhead with string or wire.
3 Refit the bolts into the bracket.
4. Note. You may need to transfer the bracket to your new engine. If so, undo the 14mm/9/16” bolts on the top of it and the 11mm/7/16” bolt and spacer at the side and remove the bracket. Refit the bolts for safe keeping.
Washer bottle
1. Disconnect the two spade connectors.
2. Pull the bottle upwards off the bracket on the inner wing. Empty the water out before it empties itself in your toolbox.
Note: Watch you hands on the bracket, the edges are sharp.
Engine stabilizer
1. Remove 13mm/1/2” bolt securing the stabiliser to the engine.
2. Remove the 13mm/1/2” bolt that secures the bracket to the block. Put the bracket on your pile of bits.
3. Remove the nut and bolt securing the stabliliser to the bulkhead. You may need to tap the bolt through from underneath. Put the bolts back in place and throw the stabliser on the pile.
Bottom engine stabiliser. (attached to engine block under the starter motor).
This is easier to remove with the car on axle stands.
1. Undo and remove the 14mm/9/16” bolt securing the stabiliser to the bracket on the gearbox.
2. Pull the bracket down slightly out of the way and put the bolt back through the stabliser for safe keeping.
Heater air intake.
The big plastic tube thing on the nearside inner wing.
1. Working under the inner wing, pull the plastic corrugated pipe off the intake.
2. Using brute force and a certain amount of industrial language, pull the intake out of the hole. Don’t worry about breaking it as it is quite sturdy. A fair amount of wiggling and pulling might be needed.
Exhaust Manifold
If your car is fitted with an LCB you should just about be able to get the engine out without taking the LCB off. I managed to and others have too. However, if you don’t want to chance it, or if it’s mullered anyway…..
1. separate the two parts of the LCB at the Y-piece underneath by undoing the clamps (usually 13mm or ½” bolts but not always).
2. Remove the two parts upwards through the engine bay. These can be a nightmare to get apart. Your swearing gland will really work overtime.
Heater valve
1. Loosen the jubilee clip securing the hose to the heater valve.
2. Pull the hose off the valve and tuck it out of the way. Some water will come out at this point.
3. Using a ¼” socket or spanner loosen but don’t remove the securing bolt at the end of the heater cable.
4. Loosen the screw on the clamp around the cable sleeve.
5. Remove the cable from the tap and tighten up the clamp so that you don’t lose the screw.
Odds and sods
Remove the crankcase breather hose from the flame trap (the black cylinder on the timing chain cover and/or clutch housing).
Undo the jubilee clip securing the heater hose to the bottom radiator hose.
This might be tight so swearing at it will help. Be careful not to spill water down the flame trap.
Pull the battery cable out of the rubber grommet on the clutch housing and pull though the grille opening out of the way.
Disconnect the fuel pipe from the fuel pump. It’s not a bad idea to plug the line from the tank with a bolt or something to stop petrol siphoning out.
Gear selector removal
Note: for this job you need maximum swearing capability. Blinking flip will not be sufficient. If vocabulary of swearwords is limited, try to get a coarse Lancastrian to help out.
1. Chock the back wheels then jack the car up and place axle stands under the front subframe. You should never venture under the car relying solely on the jack. Put the car into reverse.
2. Get under the car and find the point where the gear selector shaft and stabliser connect to the gearbox. The rod connected to the gearlever and the rod which enters the ‘box are joined by a sleeve secured at each end by a roll pin. You need to remove the rollpin nearest the gearbox.
2. The theory is that you use a small bolt, a punch, a nail or some other small implement to tap the pin out of the shaft. In practise you will fart about for ages and the thing won’t budge. Get some light under there, by means of a torch or leadlight, to make sure you are hitting the pin. Once I made sure I could see properly, mine came out fairly easily using a punch.
3. Undo the 13mm/1/2” bolt holding the stabliser bar just above the selector rod.
4. Remove the bolt and pull the selector rod off the gearbox and lower it to the floor.
5. Go and have a brew and a sit down because it is almost time to start lifting.
From this point, you will need to carry out each step in sequence.
REMOVING ENGINE
A. Attach your rope or chain. There are probably four dozen different ways of attaching the engine to the crane but the following method is tried and tested. When you lift the engine it comes up nice and straight with no tendancy to tip. To put it another way, Flamey does it this way and when I did it I managed not to drop an engine on my foot.
1.Attach one end of your rope of chain to the left hand (when viewed from the front of the car) manifold stud. Use a nut and a decent sized washer to ensure the your rope/chain cannot slip off.
2.Attach the other end to the rear alternator mounting bracket on the front of the block. You can either remove the bracket and use bolts and washers or use the bracket as I did.
Note: Be sure to leave enough slack in the rope/chain so that you can lower the engine to the ground once you have removed it. (Guess how I worked that one out!!)
B. Engine mounts
B1. Driver’s side: located behind the wheel. Wire brush the nuts and spray with penetrating oil before you start. The 13mm/1/2” bolts are on the engine bay side at the bottom of the clutch housing and will require a spanner holding them in place whilst a socket is used to undo the nuts under the wheelarch.
You can’t see the bolts so will have to feel for them. Put the nuts and bolts in your jar.
B2. Passenger side: Same size as the other side. The bolts are underneath the radiator and are very hard to get at. You will need some help for this.
i) Get someone with skinny arms to hold a spanner on the bolts (access via the back of the radiator) whilst another helper to pull the engine forward.
ii)Whilst this is going on, undo the nuts under the wheelarch. Put your nuts and bolts in your jar.
Note 1. If you can’t find two willing helpers you can get at the mounts a lot easier by removing the radiator. This isn’t necessary to get the engine out as it mounts to the engine mounting which comes out with the engine but will make like easier if you you are a Billy-no-mates.
Note 2. If your car has had a recent engine change you might find that it has engine mountings fitted with captive nuts on the engine bay side and bolts going through from the inner wing. These are much easier to remove because you don’t need to hold a spanner in the engine bay.
You are now ready to start lifting the engine out but there are a couple of things you need to do as you lift.
C. Release the pot joints from the differential.
Note: this method is not that shown in HBOL but DOES work.
i) roll up your hoist and lift the engine a couple of inches.
ii) get underneath the car and lever the one pot joint off the spline in the diff using a tyre lever or a small crowbar in the gap between the joint and diff housing; or If you can’t get it using a tyre lever there is a special Rover tool which most mini specialists sell a version of that you can use; or If you can’t get hold of that, take a scissor-type ball joint splitter and separate into its components. Take the forked part and hammer it into the gap to separate the joint and diff. A forked type ball-joint splitter will also do this job as long as it is one with fairly sharp forks.
iii) Lever the joint completely off the diff whilst pushing the engine away from the joint.
iv) Repeat the process on the other side.
D. Disconnect the speedo drive: located on the end of the engine on the passenger side.
i) Check that everything (except the speedo drive) is disconnected and that wiring etc. is tucked out of the way so it cannot snag. You can now lift the engine up until you can get at the speedo drive (where the thick black cable connects to the engine). As you lift, either get a helper to make sure that everything is clear, or stop frequently and check yourself. Note, if you left your LCB on the car check that it isn’t hooked up on the diff housing. You may need to pull the engine slightly towards
the front of the car as it goes up for clearance.
ii) Once the drive is accessable, undo the knurled nut holding it to the gearbox. You will probably need to use molegrips for this.
iii) Once it is undone, raise the engine until it is clear of the front panel, keep checking that nothing is snagged or caught.
iv) Once the bottom of the engine is higher the front panel, pull the crane back so that the engine is away from the car. Once clear, slowly lower the engine until it is about 12 inches from the floor. You can then move the engine to where you want it as it will be more stable in this lower position. Slowly lower the engine to the floor (do it fast and you will crack the sump).
Job Done. All you need to do know is fit another engine!!!
Edited by humph, 22 November 2013 - 12:49 PM.
#3
Posted 22 November 2013 - 12:48 PM
Refitting
As they say in the best workshop manuals, refitting is the reverse of removal.
That might be the case when bolting starter motors back on or refitting plug leads, it doesn’t apply quite so well when refitting an engine. These notes will point out some of the pitfalls of putting the engine back in your beloved Mini to, hopefully, make it go that bit more smoothly.
1. The first stage is to attach your rope of chain as described above. If you are working in a garage or anywhere else where headroom might be restricted, put your crane as low as the hook will go and have as little slack in the rope/chain as possible. This will ensure that you have enough room to get sufficient height to clear the front panel without hitting the ceiling.
2. Once the rope/chain is on start lifting the engine, making sure that it goes up level rather than being higher at one end or the other. Once high enough, roll the crane so that the engine is roughly in the right place over the engine bay and lower it until you can reconnect the speedo drive. DON’T
FORGET TO DO THIS BEFORE YOU LOWER THE ENGINE INTO PLACE.
Access is very difficult with the engine bolted in.
3. Once the speedo drive is connected, you can begin to lower the engine. If you left your LCB in place, make sure that the engine is going down past it rather than on top of it. Keep lowering until the engine is almost in position.
4. You now need to put the driveshafts back into the diff housing. To do this you have to push them onto the splines in the diff past the snaprings which hold them in place. The theory is that you push the shaft towards the diff and pull the engine towards the shaft. Once one side is in you can do
The other side. However, I failed miserably.
5. Instead, I followed the Haynes procedure for releasing the balljoint on the passenger side to get one driveshaft out of the way. I then put the other shaft onto the spline and lowered the engine into place. The weight of the engine was enough to push the shaft past the snapring and into place. The other shaft was pushed into place once the engine was fully lowered and the suspension bolted up again.
6. Engine mountings. Once the engine is almost in place, you might find it helpful to push a screwdriver through the mounting bolt hole in the inner wing and through the corresponding hole in the mount itself. Once the holes are aligned you can refit the bolts. The earlier comments about the passenger side mounting apply equally when refitting.
7. Once the engine is physically bolted in you have to refit everything you took off earlier. There is no particular order in which you have to do this but you might find it easier to refit the gear selector and stabiliser before you refit/bolt up the exhaust manifold as you will have more room to work.
8. If you are re-using the old Roll Pin for the gear linkage, Philster recommends that you use a small jubilee clip to cover the holes where the roll pin goes in place. These pins have been known to work their way loose and fall out. Leaving you stranded at the roadside, in the dark at daft o'clock
in the morning, miles away from home.
9. Once everything is refitted check that everything is connected up as it should be then you are almost ready to fire up. Before you do, make sure that you have remembered to put some oil in the engine. Cranking it over with the ignition system disabled will allow some oil pressure to build up before you go for launch. Charging the battery is not a bad idea either because if the engine you have put in is freshly rebuilt, it might be quite tight and unwilling to spin on the starter.
If it won’t start refer to the notes on breaking down in the technical area
Read more: http://retrorides.pr...3#ixzz26fdSw0oJ
#4
Posted 22 November 2013 - 02:01 PM
#5
Posted 22 November 2013 - 02:28 PM
Good luck with it. The above really helped me as it was my fisrt time. Came across a few issues as I was trying to do the job, mostly with getting at fixings and my infamous lack of patience!
#6
Posted 22 November 2013 - 02:49 PM
#7
Posted 22 November 2013 - 02:50 PM
#8
Posted 22 November 2013 - 04:25 PM
When removing the pin from the rod change....have the car in reverse and be sure to use a 3/16" punch
#9
Posted 22 November 2013 - 06:42 PM
#10
Posted 25 November 2013 - 07:42 PM
BUMP! Thankyou for this. Extremely helpful :)
#11
Posted 26 November 2013 - 09:33 AM
keeping this
#12
Posted 02 March 2015 - 07:57 PM
I'm revving myself up for this at weekend beer is already in the fridge
#13
Posted 02 March 2015 - 08:14 PM
Always, always forget it......stretch it and knacker it....
1 user(s) are reading this topic
0 members, 1 guests, 0 anonymous users