It can also be done by putting a large socket in the timing "window' on the clutch cover to chock a pre-verto strap bolt. Dunno if you could do similar with Verto. Also make sure the lock tab has been properly flattened if it puts up a fight.
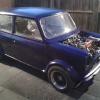
Pulley Removal
#16
Posted 15 October 2013 - 12:05 PM
#17
Posted 19 October 2013 - 11:09 AM
Odd way of doing something when the proper way is rather simple...
Stick to Zik's method, and if you some how get it wrong you're unlikely to damage the flywheel
The rope method in the bore is neither odd nor improper. It is merely old-school. I should have elaborated. As Steve pointed out, you feed the rope in while the piston is near TDC with the valves closed. Continuing on with the elaboration, it's a good idea to put a knot in the rope to prevent you from putting the whole piece in the bore.
#18
Posted 19 October 2013 - 02:19 PM
Odd way of doing something when the proper way is rather simple...
Stick to Zik's method, and if you some how get it wrong you're unlikely to damage the flywheel
The rope method in the bore is neither odd nor improper. It is merely old-school. I should have elaborated. As Steve pointed out, you feed the rope in while the piston is near TDC with the valves closed. Continuing on with the elaboration, it's a good idea to put a knot in the rope to prevent you from putting the whole piece in the bore.
I don't question that this would work but would there ever be a risk of bending a valve if it were to try and shut on the rope before the engine rotation were halted?
#19
Posted 19 October 2013 - 02:49 PM
No. Done at the right time in the cycle there is no threat to the valves, crank, piston, rods, etc.
The point that Steve was making and is outlined in the link below is that the rope is inserted while the valves are effectively closed. If you feed the rope in when the engine is on the intake stroke as opposed to compression then yes, you could do damage.
Using cylinder #1 makes it easy to do correctly. All you need to do is pull the spark plug for #1, bring the piston up so it is visible through the plug hole, the timing marks are lining up AND ( important! ) the rocker arms above #1 are "loose" (which means the valves are seated). (You can also verify this by removing the distributor cap and confirming that the rotor is pointing at the #1 spark plug wire on the cap). Then you turn the crank a little more clockwise or counterclockwise (depending on whether you want to loosen or tighten the crank bolt) then feed a short bit of soft rope in through the plug hole. Use a wrench on the crank bolt to loosen or tighten as desired. The valves will be closed when the piston pinches the rope against the head and this prevents crank rotation while the torque is applied.
This is not a new procedure or a bodge. It is old-school and probably goes back to the earliest internal combustion engines.
http://www.brickboar...ounterhold.html
EDIT: By the way Zik, I am not discrediting the bearing shell method either. That is also a tried and true method that has been used for years. The "rope trick" method just involves a bit less work and removal of fewer components.
Edited by dklawson, 19 October 2013 - 02:57 PM.
1 user(s) are reading this topic
0 members, 1 guests, 0 anonymous users