That's impressive! So it was all surface rust on that panel?
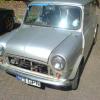
Mini 25 Full Rebuild
#1306
Posted 22 August 2015 - 03:44 PM
#1307
Posted 22 August 2015 - 04:10 PM
That's impressive! So it was all surface rust on that panel?
It was remnants of old floor, sealer and lots of flaky paint/rust.
The bracket is made of quite thick steel and it hasn't really thinned at all overall,
i may still replace it yet but if it comes up ok, it might go again
#1308
Posted 22 August 2015 - 06:48 PM
Great progress there Ben
#1309
Posted 23 August 2015 - 10:21 AM
I haven't been on here for a while but just caught up with your thread
Looking good mate wish id have replaced my boot floor now as yours looks very neat
Keep,up the cracking work
#1310
Posted 23 August 2015 - 10:37 AM
Hi Ben
I haven't been on here for a while but just caught up with your thread
Looking good mate wish id have replaced my boot floor now as yours looks very neat
Keep,up the cracking work
Cheers Mark.
It's getting there. Not only was the boot floor neater, it is really easy to replace. The worst bit is removing the old one.
Ben
#1311
Posted 23 August 2015 - 11:43 AM
Hi Ben
I haven't been on here for a while but just caught up with your thread
Looking good mate wish id have replaced my boot floor now as yours looks very neat
Keep,up the cracking workCheers Mark.
It's getting there. Not only was the boot floor neater, it is really easy to replace. The worst bit is removing the old one.
Ben
Now that is reassuring, might be getting to finishing this thing quicker than I imagine!
#1312
Posted 23 August 2015 - 12:05 PM
Hi Ben
I haven't been on here for a while but just caught up with your thread
Looking good mate wish id have replaced my boot floor now as yours looks very neat
Keep,up the cracking workCheers Mark.
It's getting there. Not only was the boot floor neater, it is really easy to replace. The worst bit is removing the old one.
Ben
Now that is reassuring, might be getting to finishing this thing quicker than I imagine!
I wouldn't say removing the old one was difficult, it is just time consuming to do well.
I turned the car on it's side and cut the bulk of the floor out from just behind the rear bulkhead and just inside of the arch tubs and split it from the back panel and that gave good access to the seam welds that hold the centre seat belt mount to grind them away.
Then it was just a case of drilling the spot welds on the bottom of the rear bulkhead to floor seam and the seat base to heelboard and then cutting inbound of the rear companion bins to get the bulk of the seat base part out.
then drill out the remains of the seat base to the companion bins. the same on the arch tubs and that's about it apart from linishing the seams etc prior to fitting.
#1313
Posted 23 August 2015 - 03:41 PM
You make it sound so easy Ben
I thought about it but I think if I do change it I'll never get mine finished
At least the rot has gone . can't believe I'm into my 3rd year now !!
#1314
Posted 23 August 2015 - 05:21 PM
I took a step back today. There is a previous repair that i was never happy with so it had to go. Not only was it ugly, since fitting the boot floor and back panel, it had now twisted where i have pulled panels together etc.
Here is the offending part..
Not too bad (apart from the wobbly seam) but this was presenting a bit of a problem..
I could have extended it to meet the floor but it was still the wrong profile and would still have looked crap.
I decided to make up a larger repair section this time to extend further up the quarter panel so that i could renew some of the wobbly seam at the same time.
Now i need to mark up where to cut so i clamped it over the top of the existing bit and marked it up for cutting. I made the first cut line below the final cut to allow me to trim it for the final fit without removing too much.
You can see that i have marked inbound of the seams and i will remove them after.
With the bulk cut out, i clamped the repair piece back in for final fit.
Much better...
Next job was to remove the edges of the old piece. One bit from the arch rub and the other from the rear external seam. I decided to cut the seam from the back panel out altogether and ill make up another one in a bit..
Then i clamped it all back in ready for welding
First, I welded the join slowly to avoid distortion and ground it up
Then i plug welded the arch tub to the arch seam leaving just the rear seam to mend.
Obviously,its going to need rebuilding to match the seam on the repair and blend into the rear panel too.
In fact, this method could be used to re-seam a de-seamed mini.
So here is the piece of seam i made up. I forgot to get pictures of the process but it basically involved taking a scrap of steel long enough, placing it between the quarter seam and the seamless rear panel but in far enough so there is steel in front and behind. Then mark the shape of the repair piece to match the curve with a marker pen.
Here is the other seam prepped ready
The eagle eyed will see that the back panel beside the light is a bit out of shape so i need to carefully mold it to shape as i weld it.
You can also see a gap between the rear panel and the quarter seam.This is needed to ensure i get enough penetration of weld into the repair as this is a critical area for strength.
I then Zinc primed the seams.
Whilst i waited for the paint to dry, i cleaned up the plug welds on the arch tub - boot floor join
Back to the other repair, here is the seam section tacked and plug welded into position making sure the wobbly bit on the rear panel was pulled to the correct shape
It looks extremely messy and the repair seam section is over sized but bare with me....
And then a quick tickle with the stone and trim the seam to the correct size and we have the makings of a decent repair
I couldn't get anything into the bottom of the seam to clean back the seam weld.
I used to have a Dremel but now i don't but till have some of the little stones left over so i improvised with the drill and painstakingly spent the best part of 30 minutes grinding the final bit of seam to shape
That's half hour i'm never getting back
No matter, almost there now
And then outside for a splash of zinc
It's still a long way from finished but that is all it needs for now. the rest will be fettled when i prep for paint.
while i had it outside, i put it back onto it's side to have a look at the under side of the new boot floor
All of the plug welds seem to have penetrated nicely so it's all good and strong
I also need to seam weld here
Once i have plug welded the seat base to the heel board, i will also add some seam welds on the back edge between the heel board and boot floor.
So that's it for today.
I can't say the car looks any different than earlier but at least i know that the quarter is sorted properly.
Cheers
Ben
#1315
Posted 23 August 2015 - 05:46 PM
Looks very tidy
#1316
Posted 23 August 2015 - 05:47 PM
I also checked and wire brushed the fuel tank retainer bracket and changed the Vinegar
Not too bad so far
#1317
Posted 23 August 2015 - 05:55 PM
What are you using to grind the welds down and in what order ?
Looks very tidy
I start off with a thick grinding stone held square on at the panel like this
You are aiming to just go back and forth along the length of the welds with very little pressure (just enough to stop it skipping) until you have taken the welds down evenly. They should now be proud of the surface by about 1mm.
It's hard to avoid the welds being ground flush in places at this stage but it doesn't matter, as long as you keep your eyes on things so you done come off of the actual weld and onto the surrounding metal and start thinning it
Next i use a thin grinding stone held at about 45 degrees to the panel
Again, very little pressure is needed and at this stage, you are looking to blend the welds into the surrounding steel.
This disc is better as you can get a much finer detail with it.
then finish off with a good ol flap disk
Again, with very little pressure.
take your time (and it does take ages) and all will be well.
the worst thing you can do is put loads of pressure on the stone as it will just introduce too much heat and you will probably thin it down too much
Hope that helps.
Ben
#1318
Posted 23 August 2015 - 06:05 PM
I've no shortage of worn out flap discs so will give your method a try
Cheers
Mark
#1319
Posted 23 August 2015 - 06:33 PM
Top drawer repairs there Ben. I assume you needed to introduce a little bowl curve into the new quarter repair section?
#1320
Posted 23 August 2015 - 06:41 PM
Top drawer repairs there Ben. I assume you needed to introduce a little bowl curve into the new quarter repair section?
Same method as the other one, Just marked and turned up with mile grips and then straightened and stretched with hammer and dolly.
Cheers
Ben
1 user(s) are reading this topic
0 members, 1 guests, 0 anonymous users