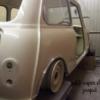
Austin Mini Mk1 Super Deluxe Restoration
#136
Posted 01 August 2013 - 09:11 PM
Darren
#137
Posted 01 August 2013 - 09:11 PM
Just aswell then that you don't need the door post haha
,
I might be interested in the drivers door post/hinge section....
#138
Posted 01 August 2013 - 09:16 PM
It looks ok but I would avoid doing beads on top of the sheet and just concentrate on the welds you will use like plug overlap and butt. The best tip I can give you for setting up your welder is put the welder on power setting two, turn the wire speed to zero and hold the torch to the sheet as you would to weld then pull the trigger with the trigger still help slowly turn up the wire speed until you get the good crackle sound. If you keep blowing holes turn the power down and repeat when you get the sweet spot note the settings for that thickness of steel. If the wire is too slow it will burn back up the torch if its too fast it will just poke the workpiece and splatter
Darren
thanks darren i will try that method tomoz and give it ago sometimes it would make a nice noise and if i welded somewhere else it made like a noise spit spit spit spit going slow? and i didnt change the setting at all? could it be the way i was holding it with out two hands?
#139
Posted 01 August 2013 - 09:17 PM
Just aswell then that you don't need the door post haha
,
I might be interested in the drivers door post/hinge section....
its here if you want it mate once i start chopping i will let you no?
#140
Posted 01 August 2013 - 09:23 PM
#141
Posted 01 August 2013 - 09:25 PM
dont suppose you no what ones i need for mine? as i have never brought them before and ebay do packet deals. cheers tom
#142
Posted 01 August 2013 - 10:23 PM
dont suppose you no what ones i need for mine? as i have never brought them before and ebay do packet deals. cheers tom
Best bet on that is to take it to your nearest machine mart or similar hardware store and enquire about it
#143
Posted 02 August 2013 - 06:04 AM
I use 0.6mm tips in my Clarke mig.
The Ebay listing has part numbers in it; you could Google the part numbers if you do not want the full kit?
http://www.ebay.co.u...=item232d7fb49a
"WECS Product Ref 1,2,18,24or30
Cebora Pocket Turbo 130 and Snap-On 130 Mig Torch Consumables Kit.
Consisting of
5580004 Cebora Liner
3160315 Gas Nozzle Shroud
1459 Contact Tips x 5 Please Select Size Above"
#144
Posted 02 August 2013 - 02:08 PM
dont suppose you no what ones i need for mine? as i have never brought them before and ebay do packet deals. cheers tom
Best bet on that is to take it to your nearest machine mart or similar hardware store and enquire about it
yes ile pop there when i can what do you think of my first welds?
#145
Posted 02 August 2013 - 02:09 PM
I use 0.6mm tips in my Clarke mig.
The Ebay listing has part numbers in it; you could Google the part numbers if you do not want the full kit?
http://www.ebay.co.u...=item232d7fb49a
"WECS Product Ref 1,2,18,24or30
Cebora Pocket Turbo 130 and Snap-On 130 Mig Torch Consumables Kit.
Consisting of5580004 Cebora Liner
3160315 Gas Nozzle Shroud
1459 Contact Tips x 5 Please Select Size Above"
cheers pal
#146
Posted 02 August 2013 - 02:26 PM
What a great project.
Personally if I was you though, I would have tried to stretch to the new floor rather than a donor floor. The floor is defiantly the correct place to start though whatever you do. I was cringing a bit when I read your plans to re-shell. Yes you could get all the detail and end up with a Nice looking Mk1 but you would always know it was a Mk3 with bits of Mk1 welded to it!
Defiantly not a job for the faint hearted and will need thousands and thousands spent on it but will be worthwhile.
I would defiantly been interested in repairing this shell for you as I love to do that kind of work but to be honest, you would only probably find someone to do it if you could keep the new panels coming so the project could keep moving which it sounds like you wouldn't be able to do.
Anyway good luck with it.
Cheers
Ben
#147
Posted 02 August 2013 - 03:05 PM
What a great project.
Personally if I was you though, I would have tried to stretch to the new floor rather than a donor floor. The floor is defiantly the correct place to start though whatever you do. I was cringing a bit when I read your plans to re-shell. Yes you could get all the detail and end up with a Nice looking Mk1 but you would always know it was a Mk3 with bits of Mk1 welded to it!
Defiantly not a job for the faint hearted and will need thousands and thousands spent on it but will be worthwhile.
I would defiantly been interested in repairing this shell for you as I love to do that kind of work but to be honest, you would only probably find someone to do it if you could keep the new panels coming so the project could keep moving which it sounds like you wouldn't be able to do.
Anyway good luck with it.
Cheers
Ben
hi ben for a welder to do this he would easily charge £2500?? if i can do it myself all i need to do is pay for the panels and equipment so i should save there and i dont mind getting stuck in. the floor panel ino its a mk4 floor panel but when it been changed and the right panels fitted you am not going to tell the difference plus a new floor panel is £500-£700 i just brought this shell for £150 and if i can sell the bits of it and get my money back then i say thats a good saving. i am not rich to go out there and buy brand new heritage panels and spend thousands on panels where i can make something work and fits in the budget. i just hope i can get the welding bang on and nice and neat. we shall soon see cheers tom
#148
Posted 02 August 2013 - 03:26 PM
Welding looks not half bad tom to be honest aasuming this is your first time welding, even the "Pro's" turn crap if they don't weld for a while, its just a case of getting into the groove of it haha
Me and you are basically doing the same conversion tom apart from i'm doing it in bits as apposed to slotting it on top in a big chunk haha
Best of luck, will be following like a Hawk
Cliff
#149
Posted 02 August 2013 - 03:31 PM
Welding looks not half bad tom to be honest aasuming this is your first time welding, even the "Pro's" turn crap if they don't weld for a while, its just a case of getting into the groove of it haha
Me and you are basically doing the same conversion tom apart from i'm doing it in bits as apposed to slotting it on top in a big chunk haha
Best of luck, will be following like a Hawk
Cliff
lol cheers mate i am going to fetch some rear quarters in the morning and if i get enough time i am going to get the drivers rear quater tacked in place and then i will move on to the drivers door post with then the door step is that the way you would do it pal?
#150
Posted 02 August 2013 - 04:21 PM
lol cheers mate i am going to fetch some rear quarters in the morning and if i get enough time i am going to get the drivers rear quater tacked in place and then i will move on to the drivers door post with then the door step is that the way you would do it pal?
The rear 1/4 sits over the top of the door step. I just did these jobs on mine. I did 'A' post, door step then rear 1/4 in that order.
Edited by Wise Old Elf, 02 August 2013 - 04:22 PM.
6 user(s) are reading this topic
0 members, 6 guests, 0 anonymous users