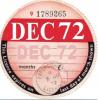
Verto Clutch Removal ?
#1
Posted 12 April 2013 - 04:28 PM
#2
Posted 12 April 2013 - 04:52 PM
once the bolts out remove the keyed washer below (some people miss this)
put the fly wheel puller on (which should look something like the one in the link below) I think you need the silvery/gold coloured bolts with the coarser thread for the verto flywheel ( they should screw in by hand, if not try the other ones) they should go in a good 8-10 turns
make sure you use the black metal block, this sits against the crankshaft, if you leave this out the big puller bolt can go up the crank bolt hole and knacker the thread. turn the engine over a couple of times to check the flywheel is aligned, you want all three outer bolts the same lenght so they pull evenly.
do up the centre puller bolt tight, again you'll need to lock the flywheel, give it a good heave, leave a few mins and heave again and hopfully it will pop off. some can be VERY stubborn though,
http://www.comparest...mini--metro.jpg
#3
Posted 12 April 2013 - 05:17 PM
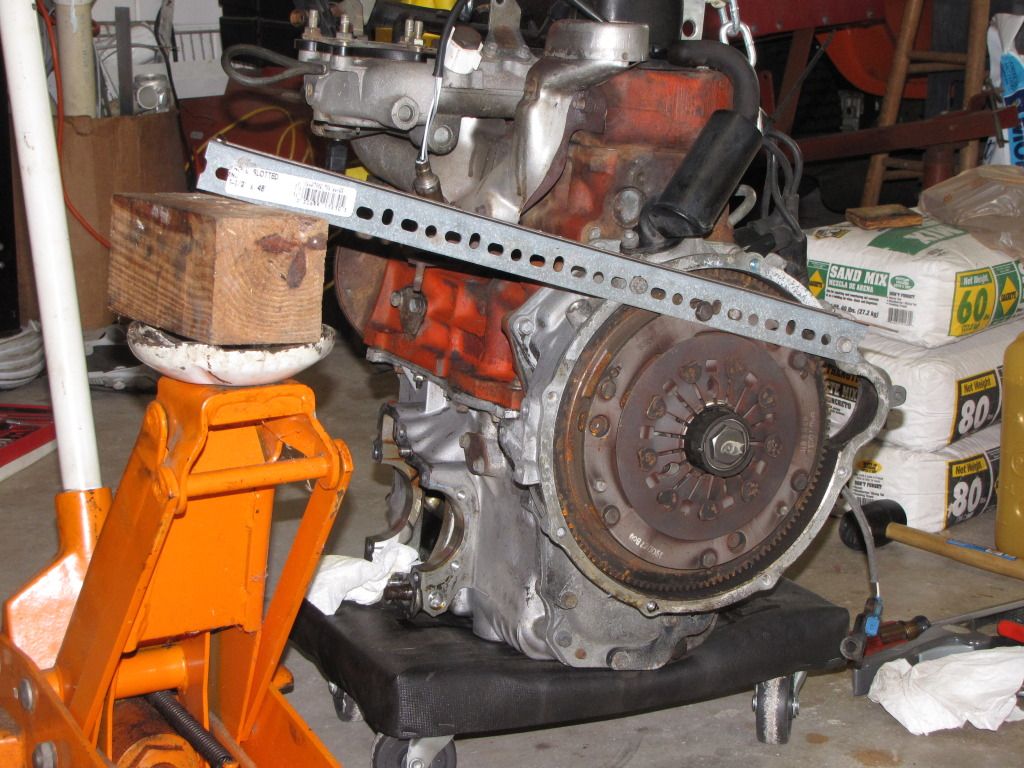
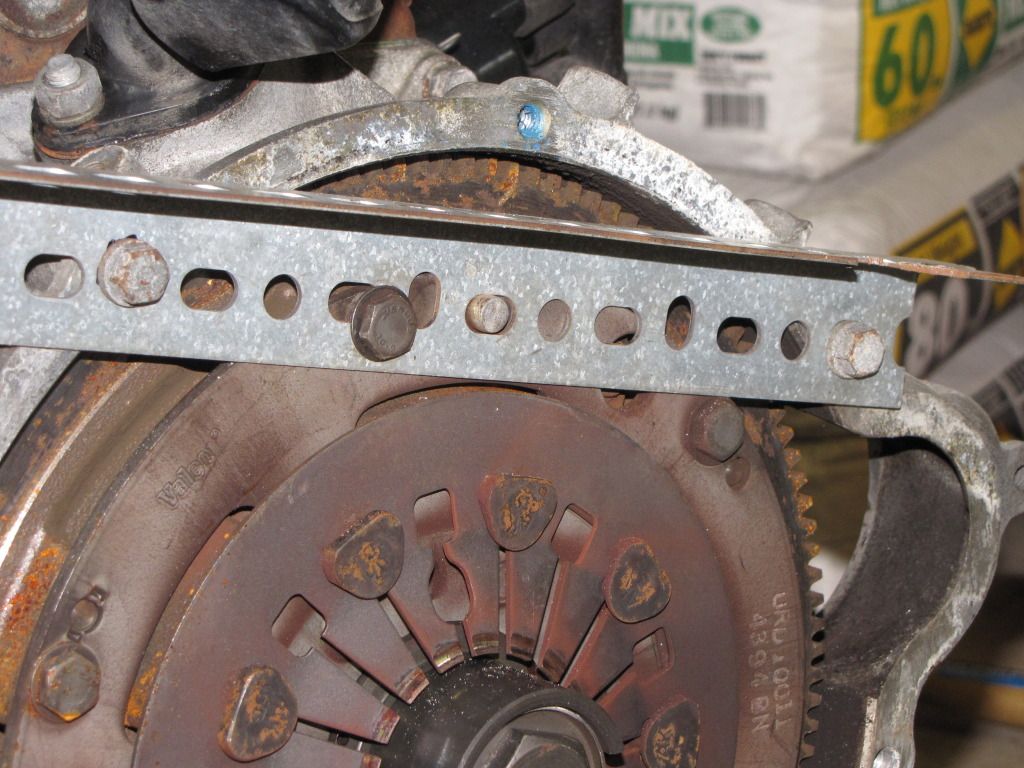
You need the slots for the nut locking tabs to be horizontal to prevent dropping the "C" shaped washer that would make the removal impossible. Lock the flywheel and bend back (if possible) the lock tabs and then remove the nut. With my setup it came out easily. Next I used some penetrating oil (not WD40) between the crankshaft and the clutch hub after removing the keyed washer. I greased the threads of the puller and the bearing plate that pushes against the crankshaft. Installed the puller as stated above by mini13.
While loading the puller, you might need to hit the center puller bolt. I used a 2 lbs. a hammer but I did not hit really hard. The flywheel lock I used also prevented the flywheel from flying off when it broke loose. It came out in about 5 min.
Edited by xrocketengineer, 12 April 2013 - 05:19 PM.
#4
Posted 12 April 2013 - 06:13 PM
#5
Posted 12 April 2013 - 08:10 PM
#6
Posted 13 April 2013 - 01:03 AM
The next thing is the condition of taper on the crankshaft if it is rough. It is recommended to use fine valve lapping compound to smooth out the surface between the crankshaft and the clutch hub. This needs to be done lightly and carefully to prevent the compound to get in the primary gear bushes or they will be ruined and also not to wear the taper to the point that the clutch and flywheel end up too far in on the taper. Mine looked like this after all the lapping compound was removed and cleaned with the primary gear off.
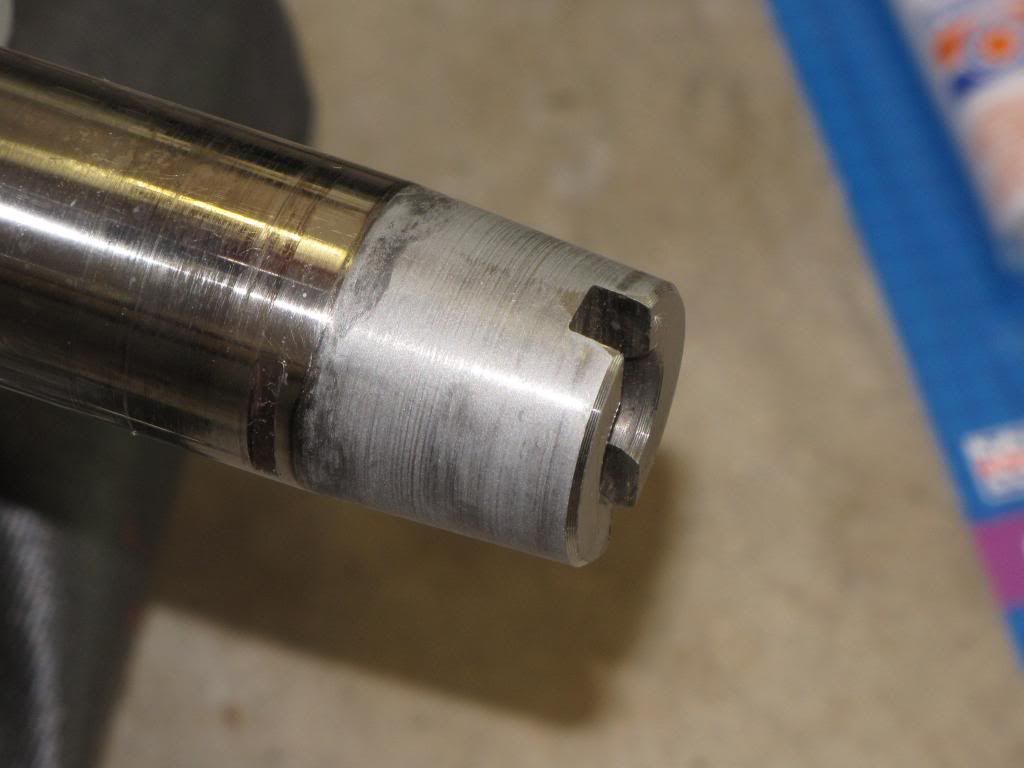
The clutch pressure plate, disc and and flywheel need to be assembled loosely and slipped over the primary gear and crankshaft for disc centering then removed and torqued outside. On the SPI the pressure plate and flywheel fit together in only one way, I do not know if that is the case for the 998.
When finally installing the assembly I used a bit of grease that came with the disc on the internal disc splines and rubbed some WD40 with a rag on the crankshaft taper to reduce friction as the asssembly seated into the taper while torquing. Also notice that the slot on the end of the crankshaft is offset so the pressure plate has to be installed accordingly together with the keyed washer.
Edited by xrocketengineer, 13 April 2013 - 01:05 AM.
#7
Posted 13 April 2013 - 10:22 AM
#8
Posted 13 April 2013 - 04:39 PM
I made a holding tool today out of some thick strap, its all bolted up, but had to go and help my mate with his MG carbs, so hopefully tomorrow it will be off!! Thanks for all the advice. Martin.
#9
Posted 14 April 2013 - 03:54 PM
#10
Posted 14 April 2013 - 05:33 PM
get some penetrating fluid on there, are you using a 1/2" drive bar? if so get a bit of tube on oit to get you up to about 3ft and give another heave.
are you going to use this flywheel again? if not give it some abuse with a blow torch.
#11
Posted 14 April 2013 - 05:35 PM
#12
Posted 14 April 2013 - 06:20 PM
also as its a 998 ods on it should come off ok, its usually the longer stroke 1098's and 1275's that give an issue .
#13
Posted 14 April 2013 - 10:12 PM
And like the guys said, be patient. Don't over tighten the puller, just a little bit at a time after hitting it with mallet. You might want to back off on the puller and tighten it again while hitting with the hammer. Dynamic loads are better than static to shock the joint apart.
Edited by xrocketengineer, 14 April 2013 - 10:16 PM.
#14
Posted 15 April 2013 - 03:45 PM
#15
Posted 15 April 2013 - 04:08 PM
1 user(s) are reading this topic
0 members, 1 guests, 0 anonymous users