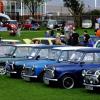
Welding Help Please
#1
Posted 11 February 2013 - 07:22 PM
#2
Posted 11 February 2013 - 07:30 PM
#3
Posted 11 February 2013 - 07:35 PM
#4
Posted 11 February 2013 - 07:39 PM
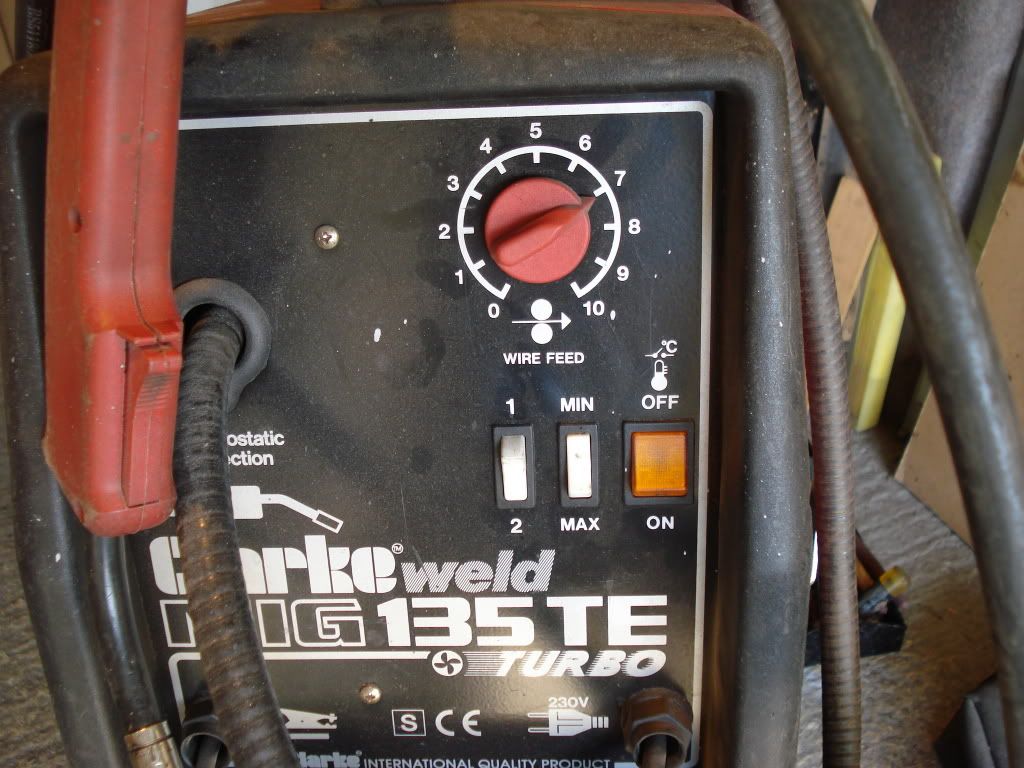
#5
Posted 11 February 2013 - 07:42 PM
#6
Posted 11 February 2013 - 08:19 PM
end of the day, its all metal, you can replace it!
#7
Posted 13 February 2013 - 08:40 AM
The very latest "intelligent" (and expensive!) MIG welders actually measure the voltage and use it to control the wire feed, so you can store the settings for various different jobs and recall them easily. I think that some may have a setting for the metal thickness that you are welding, so everything that you need is set automatically.
#8
Posted 13 February 2013 - 10:02 AM
Do you know if its possible to get some kind of spot welder attachment for these, or is that a completely different sort of machine?
A mate of mine is scraping a bonnet off his Saab 900 turbo so I was gonna cut some bits off it to practice welding with.
#9
Posted 13 February 2013 - 05:47 PM
A similar attachment was available for arc welders, using a carbon electrode, and as well as not being much good, it was dangerous to the eyes because a carbon arc is very much brighter than a metallic arc.
A true spot welder is basically just a transformer that puts out several thousands of amps at maybe 1 to 2 volts, and a mechanism for pinching the workpieces between a pair of electrodes, so there is ideally no arc, and only resistance heating occurs. Good machines are more complex than that, as they time the weld cycle to allow for lower current if the metal is not perfectly clean or the mains voltage is a bit low. A spot welder is a very heavy thing to have to hold in your hands.
#10
Posted 13 February 2013 - 06:30 PM
#11
Posted 13 February 2013 - 07:40 PM

#12
Posted 13 February 2013 - 07:42 PM
#13
Posted 13 February 2013 - 07:48 PM
#14
Posted 13 February 2013 - 07:48 PM
I think that some may have a setting for the metal thickness that you are welding, so everything that you need is set automatically.
A fabricator friend has one that does that, you set the metal thickness and type of weld (corner, edge, overlap etc). and just weld. It was somewhere in the region of £8k though!
#15
Posted 13 February 2013 - 08:00 PM
The wire feed tension is the 2 rollers that push the welding wire up to the torch, it also needs to be the correct roller as well.
If you look at the roller(usually the bottom one), its got 2 grooves in it, a 0.6mm and a 0.8mm, which groove you use depends on the size of welding wire you use.
Once this is correct you can then set the wire tensions, if you look at the rollers theres an adjuster knob, this controls the pressure that the top and bottom roller are squeezed together at. Too little pressure and the rollers will slip and not drive the wire properly, too much and the wire can 'bunch' or jam up easily.
- Push the trigger and let some wire come out of then end of the torch(don't let it go near the welding earth or you'll get burned!!)
- Whilst pushing the trigger try and stop the wire from coming out the end with your thumb and forefinger, if its stops easily then add more pressure to the roller, too much pressure and the rollers will continure to try and drive 'bunching' up the wire by the rollers.
- Ideally it should just start to slip a bit when you squeeze tightly on the wire.
1 user(s) are reading this topic
0 members, 1 guests, 0 anonymous users