Edited by Pigeonto, 12 February 2013 - 08:12 AM.
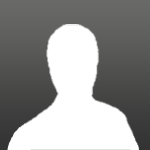
Cylinder Wall Pics....the Dreaded Bore Wash?
#31
Posted 12 February 2013 - 08:09 AM
#32
Posted 12 February 2013 - 05:41 PM
AC
Edited by ACDodd, 12 February 2013 - 05:43 PM.
#33
Posted 12 February 2013 - 09:58 PM
You certainly have me concerned now about the clearance.I am happy tho that the bores are not atall oval or worn so if it is undersize then fair chance it will hone out to size.Doesnt that mean the piston can tip and the rings then arent 90 deg to the cylinder wall??
#34
Posted 12 February 2013 - 10:16 PM
AC
#35
Posted 12 February 2013 - 10:29 PM
#36
Posted 13 February 2013 - 12:09 AM
AC
#37
Posted 13 February 2013 - 07:58 AM

#38
Posted 13 February 2013 - 04:26 PM
If it helps I add 0.0007" to my finished bore sizes in summer to allow for winter cold starts.
There is a lot more to bore sizing than just the correct diameter when machined.
Ac
Edited by ACDodd, 13 February 2013 - 04:29 PM.
#39
Posted 13 February 2013 - 10:03 PM

#40
Posted 13 February 2013 - 10:45 PM
It's surprising how many people don't realise the difference in thermal expansion between aluminium alloy and cast iron.
#41
Posted 17 February 2013 - 08:31 PM
.Going to run it in stupidly weak,then a trip down to ML for setting up.
Beware of running stupidly weak too
#42
Posted 17 February 2013 - 10:21 PM
AC
#43
Posted 17 February 2013 - 10:57 PM
#44
Posted 17 February 2013 - 10:59 PM
AC
#45
Posted 17 February 2013 - 11:02 PM
If it is stupid lean you will be at full load before you know it to make any sort of progression
2 user(s) are reading this topic
0 members, 1 guests, 0 anonymous users
-
Bing (1)