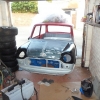
The Wifes Worst Nightmare 83 Full Resto
#61
Posted 10 September 2012 - 05:18 PM
#62
Posted 11 September 2012 - 05:38 PM
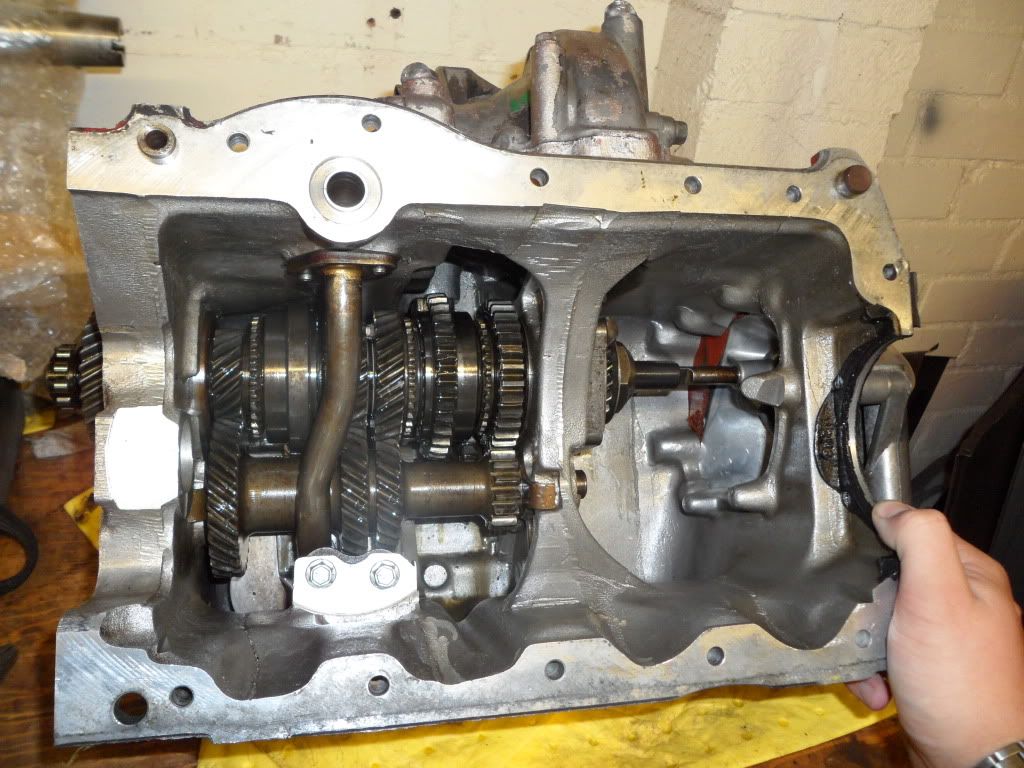
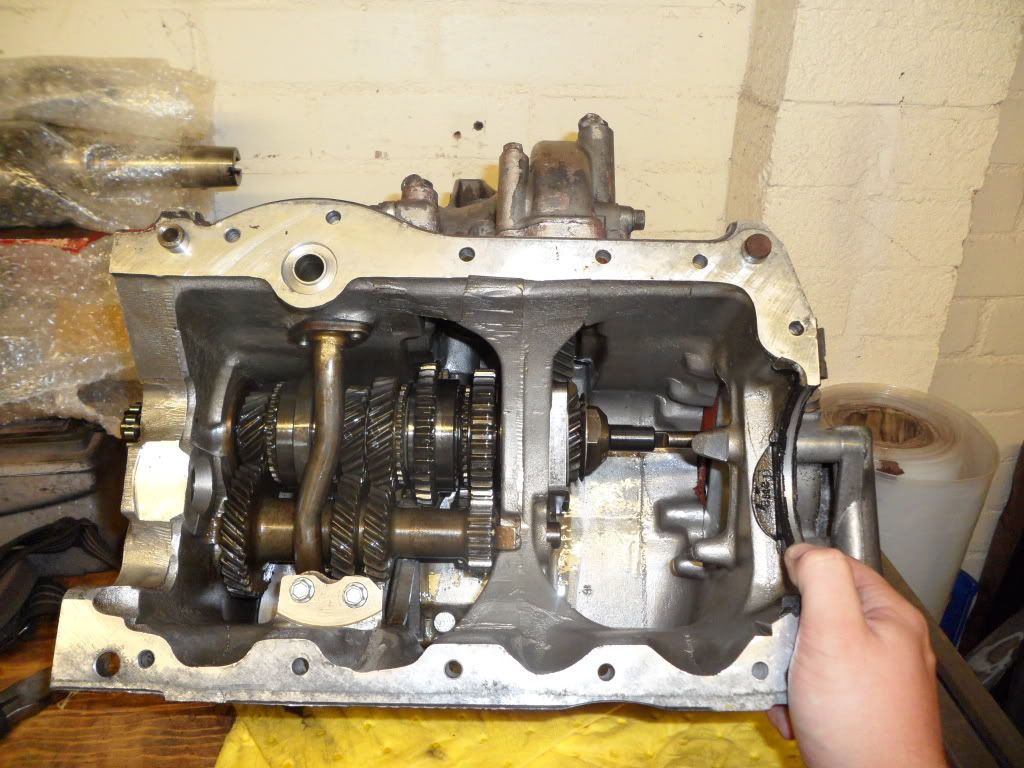
also gave the outside of the casing a good scrub and is ready for some silver now
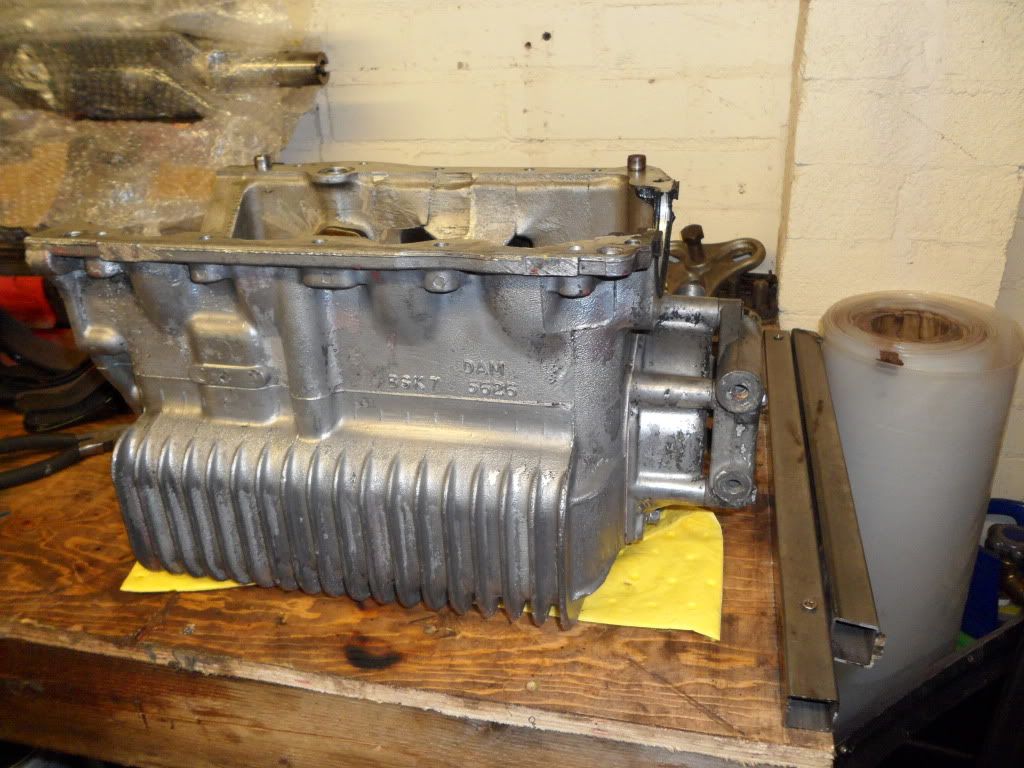
after that i got the final coat on the front subby but no pic as its just the same as the last post i should be able to start building that up soon as ive got most of the bits including my fiesta brake conversion just need new bearings for the hubs then its all complete
this could be my last update for a while as i have to send my laptop away for repair or maybe ill just update with my phone and put the pics on later or something but more soon maybe lol
darren
#63
Posted 11 September 2012 - 06:54 PM


#64
Posted 11 September 2012 - 07:11 PM
nasty looking over sill you have there, but you are getting so good at fabrication and welding that it will be fine soon. The gearbox looks nice, Have you had a very close look at the dog teeth on all synchro sides to check for wear, just in case. As for the block, the bores look pretty good where the pistons have been and unless you are going to over bore it then try a home honing tool. I did with mine and the bores came up very nicely. Are there any ridges on the bore walls??
Graham
#65
Posted 11 September 2012 - 09:47 PM
I'd definitely take a look inside the diff. Here's what I found when I took mine apart:

As well as loads of swarf in the sump, I also found a tooth from a planet gear jammed in the selector lever - that was why I couldn't get 3rd. All fixed now though - used a diff upgrade kit from Guessworks (£55).
Bob
#66
Posted 12 September 2012 - 02:00 AM
Hi Darren,
nasty looking over sill you have there, but you are getting so good at fabrication and welding that it will be fine soon. The gearbox looks nice, Have you had a very close look at the dog teeth on all synchro sides to check for wear, just in case. As for the block, the bores look pretty good where the pistons have been and unless you are going to over bore it then try a home honing tool. I did with mine and the bores came up very nicely. Are there any ridges on the bore walls??
Graham
Hi Graham like you say the welding side of things should come together although I now thing a new inner wing is needed not sure I can fab a new one up just yet, I need to get in there with a good torch but from what I can see all the dogs look good well they are all the same shape no missing teeth all gears select and when in gear the synchro hubs and baulk rings look to be good to. Unluckily for me although most of the bores look to be ok it seems the pistons at one point were siezed in there and honing until the marks are gone I feel will push it overbore so I will just go up a couple of sizes make it a little more fun plus it needs new cam bearings so a trip to the machine shop is unavoidable
As always your input is welcome cheers Darren
#67
Posted 12 September 2012 - 02:07 AM
Hi Darren, Some great work on the repairs there!
I'd definitely take a look inside the diff. Here's what I found when I took mine apart:
As well as loads of swarf in the sump, I also found a tooth from a planet gear jammed in the selector lever - that was why I couldn't get 3rd. All fixed now though - used a diff upgrade kit from Guessworks (£55).
Bob
Hi bob from reading your thread a while ago it was my first thought that the diff could be the source of all the metal swarf in the case I'm just building up the courage to to start pulling the box apart lol maybe I'll just whip off the diff and see what I find before stripping the rest of the box but lots of pictures and labeled bags I'm sure it will all fit back in
Thanks for popping along darren
#68
Posted 12 September 2012 - 03:59 PM
#69
Posted 26 September 2012 - 08:50 AM
Darren
#70
Posted 26 September 2012 - 08:59 AM
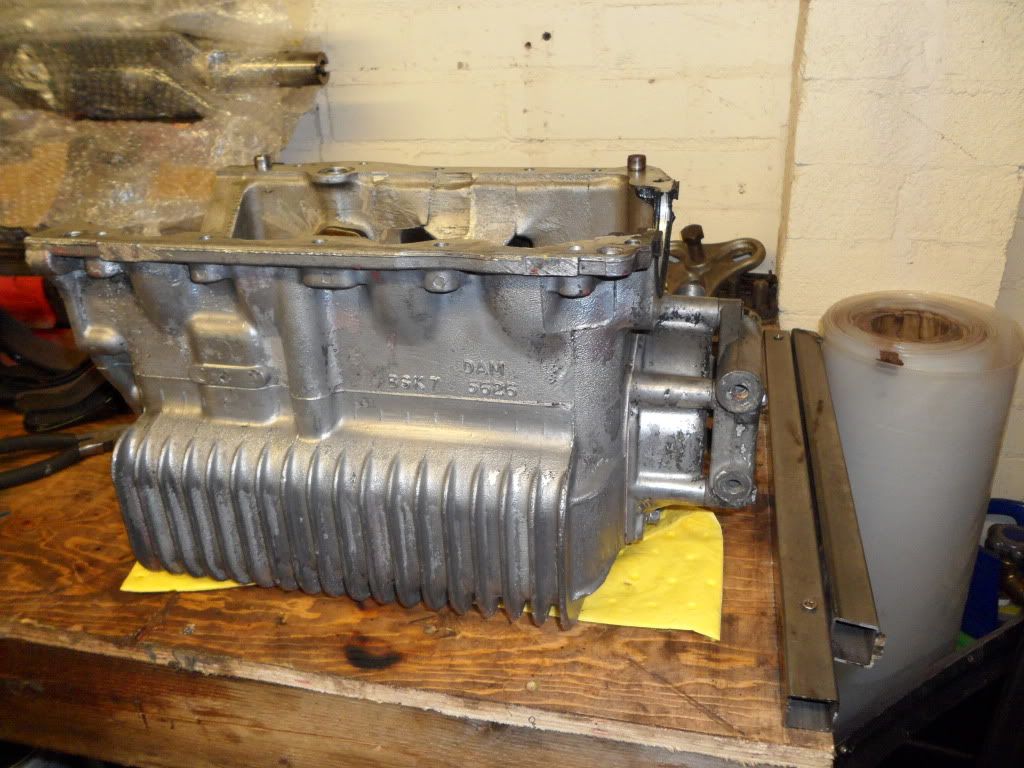
#71
Posted 27 September 2012 - 06:11 PM
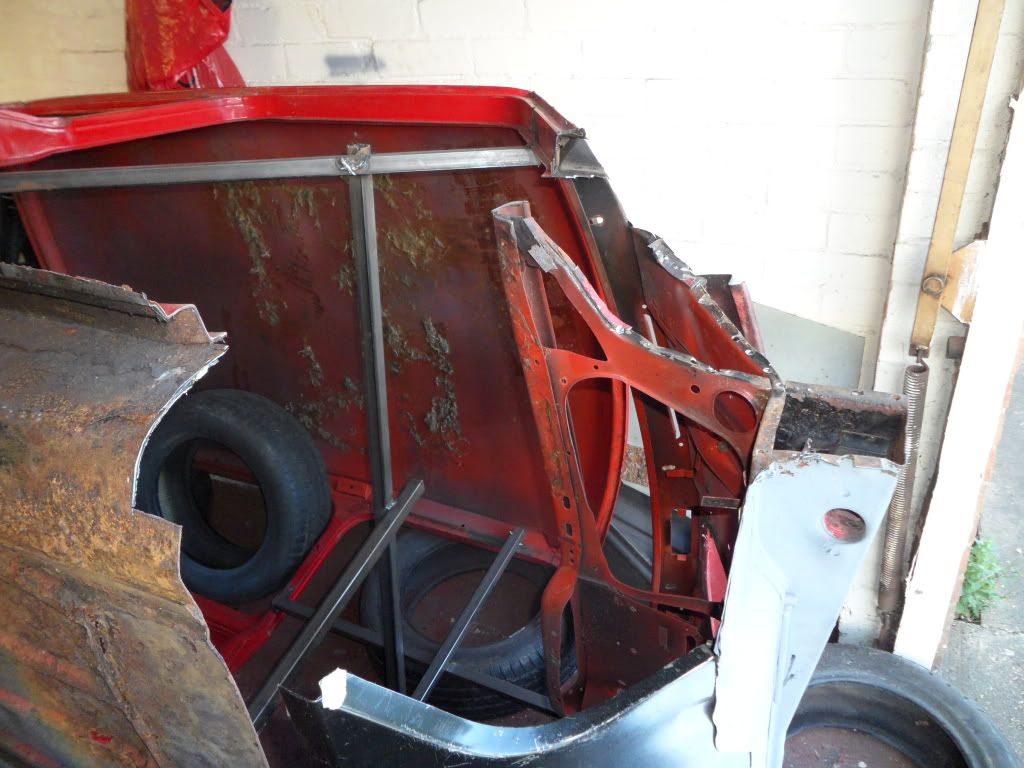
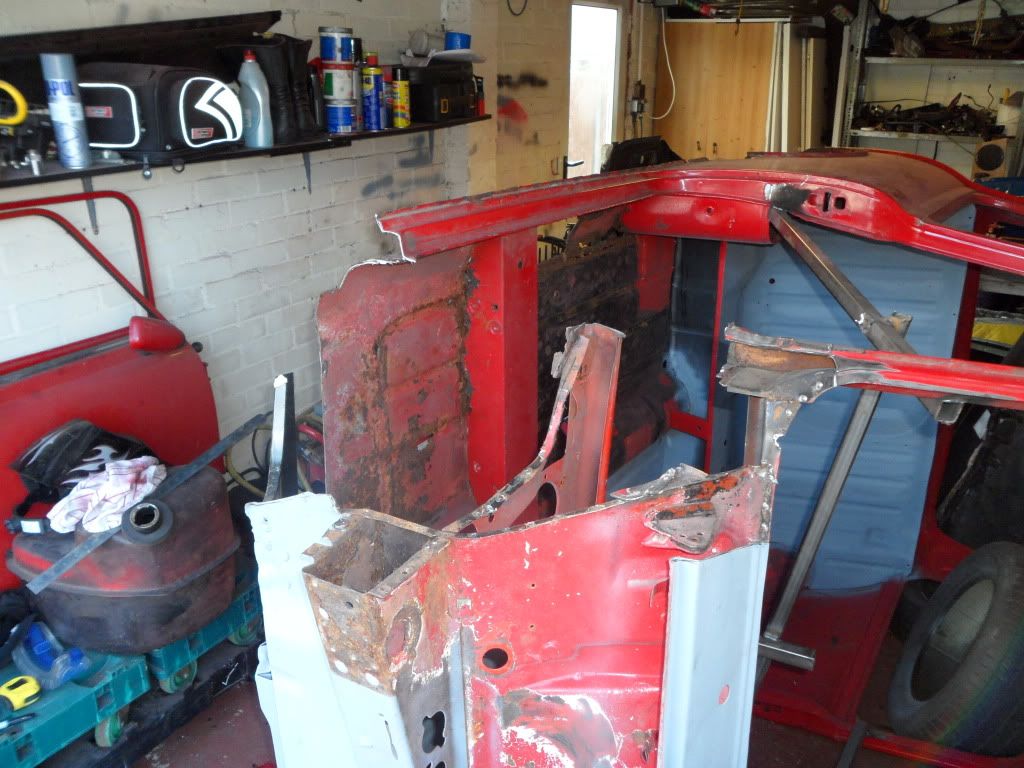
i made up a new inner a post boxing plate going from what was left of the old panel
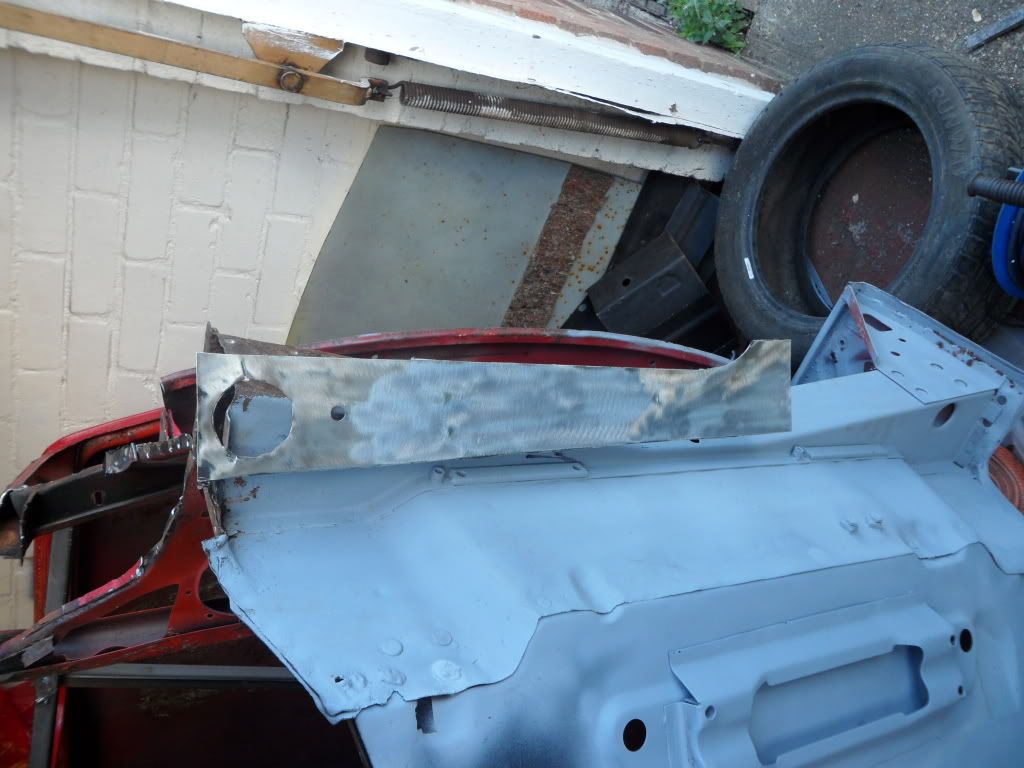
got the donor door post all cleaned up
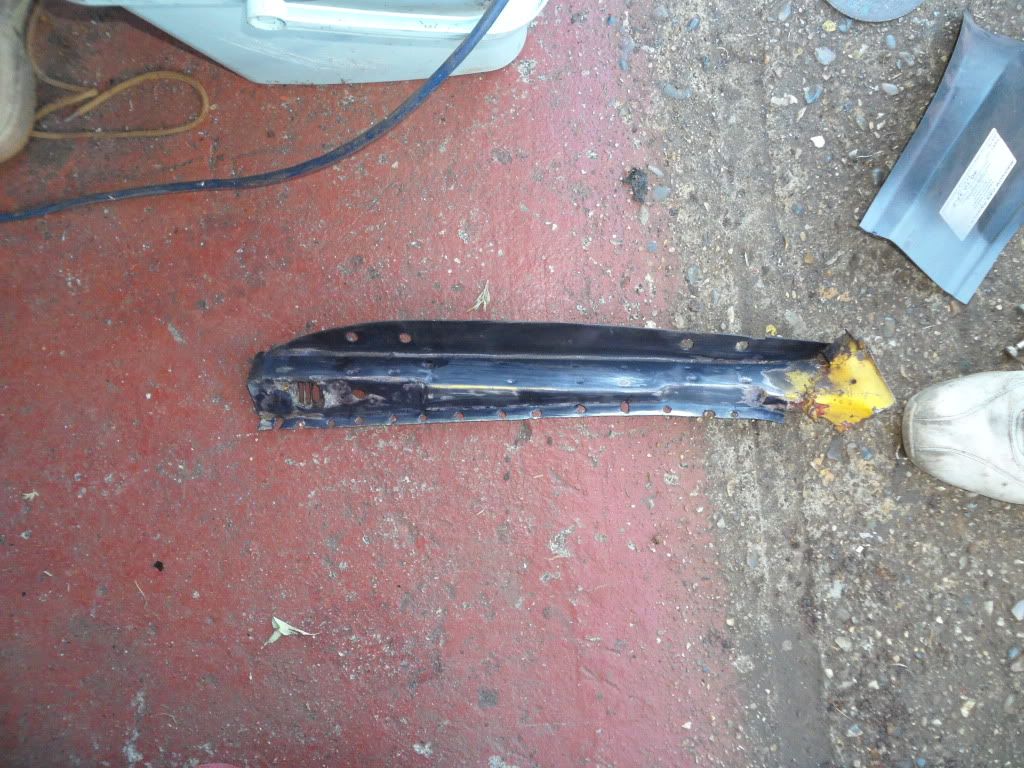
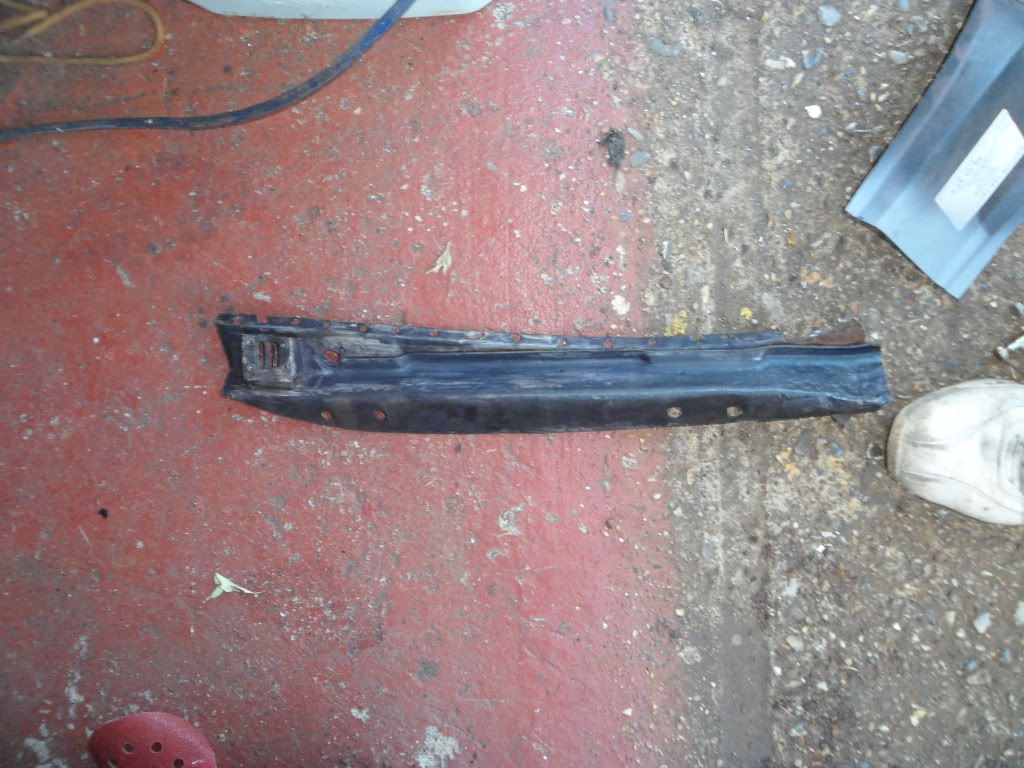
and then clamped the two together and welded and cleaned off turned out pretty well and i will put the flange for the flitch when i fit that
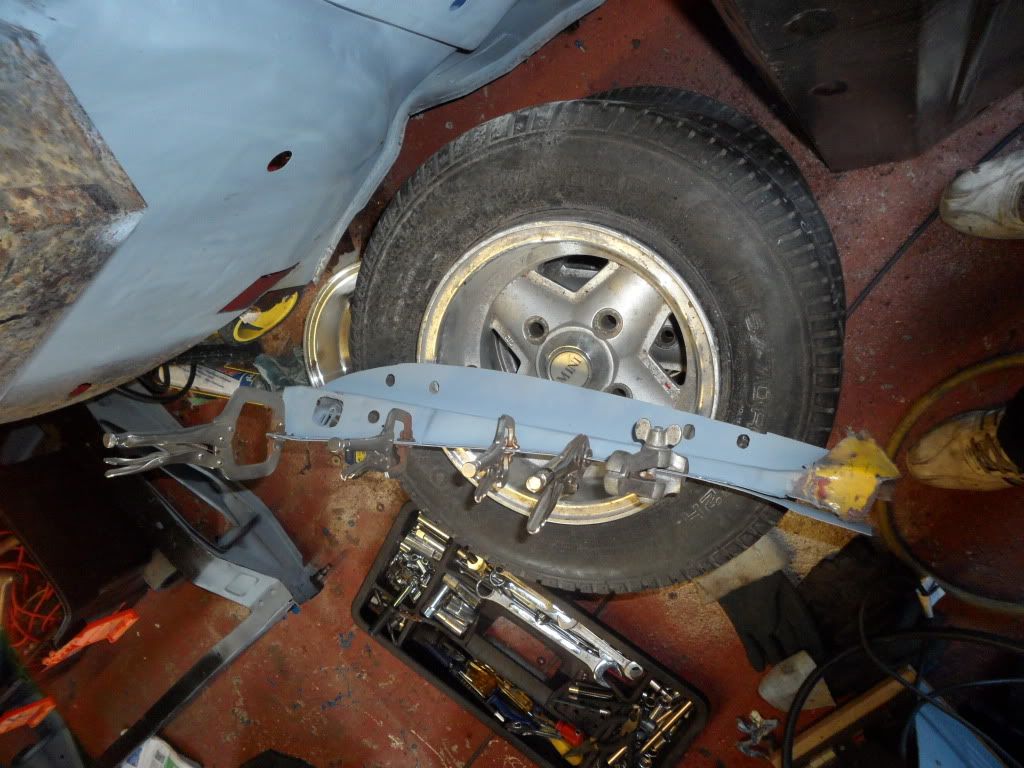
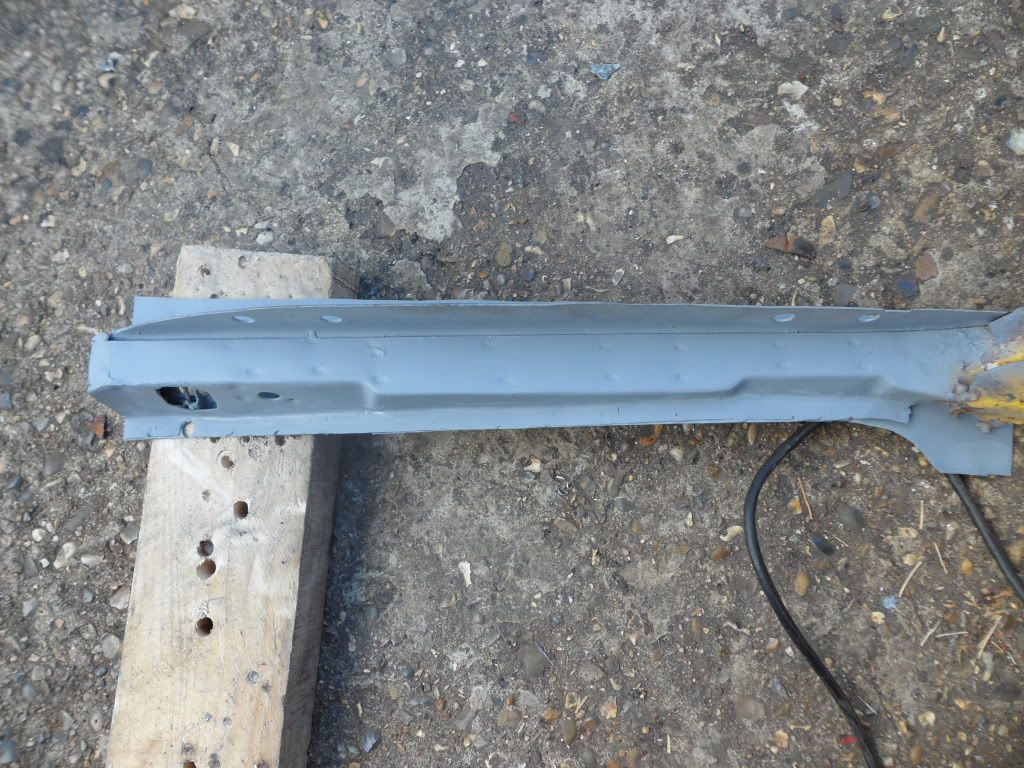
then welded in the door post using the door itself to make sure it was strait also using the previous measurements taken
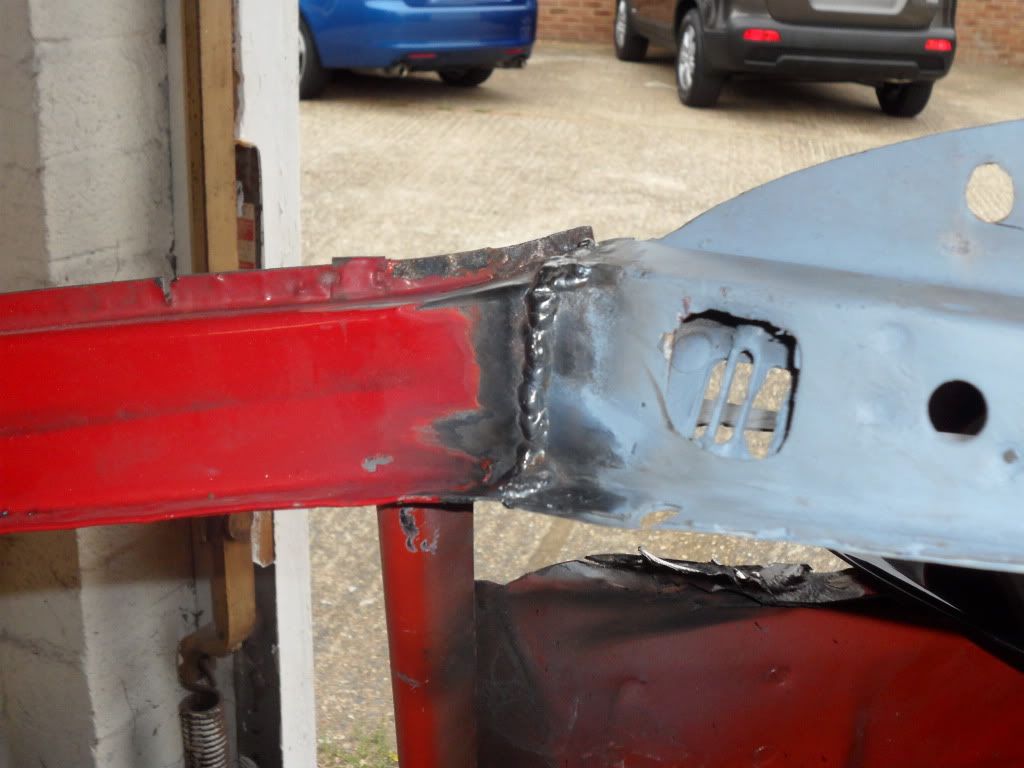
and the rear for penetration
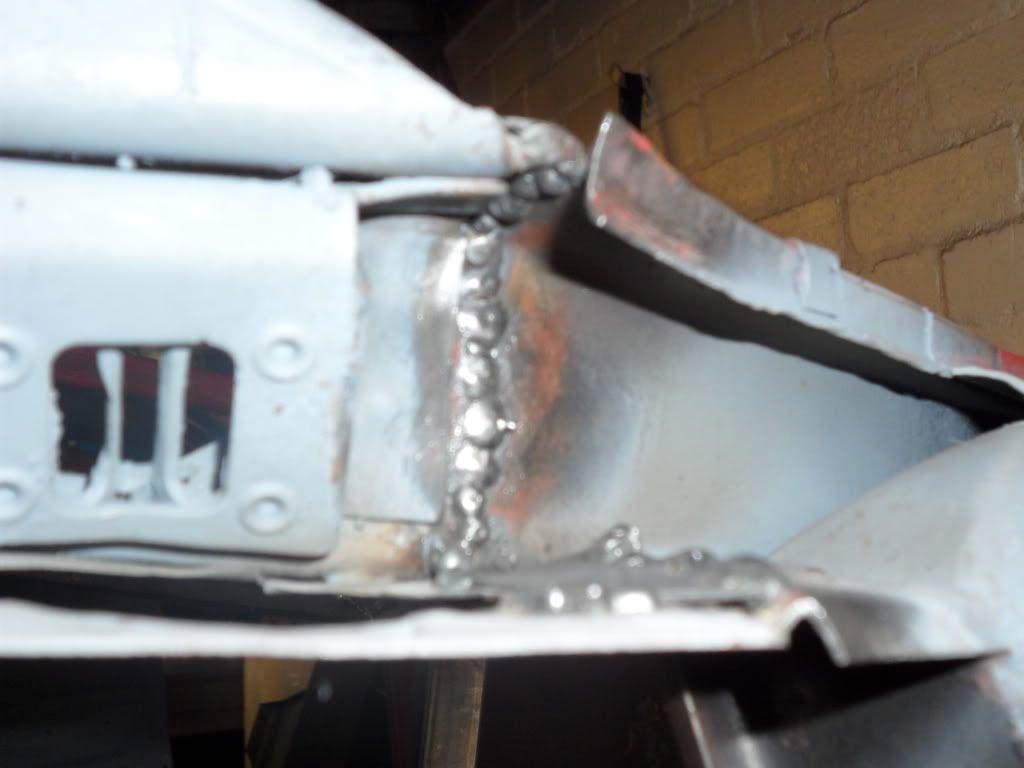
and then all ground down cleaned up and a little primer and as it turned out well i took a couple of pics
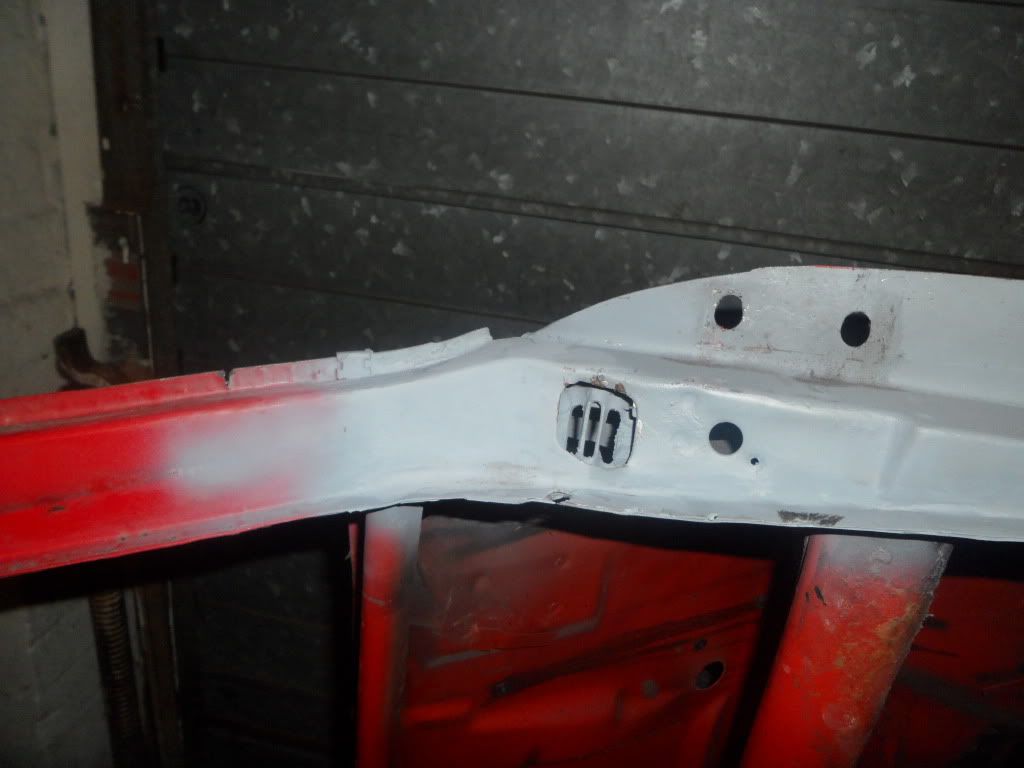
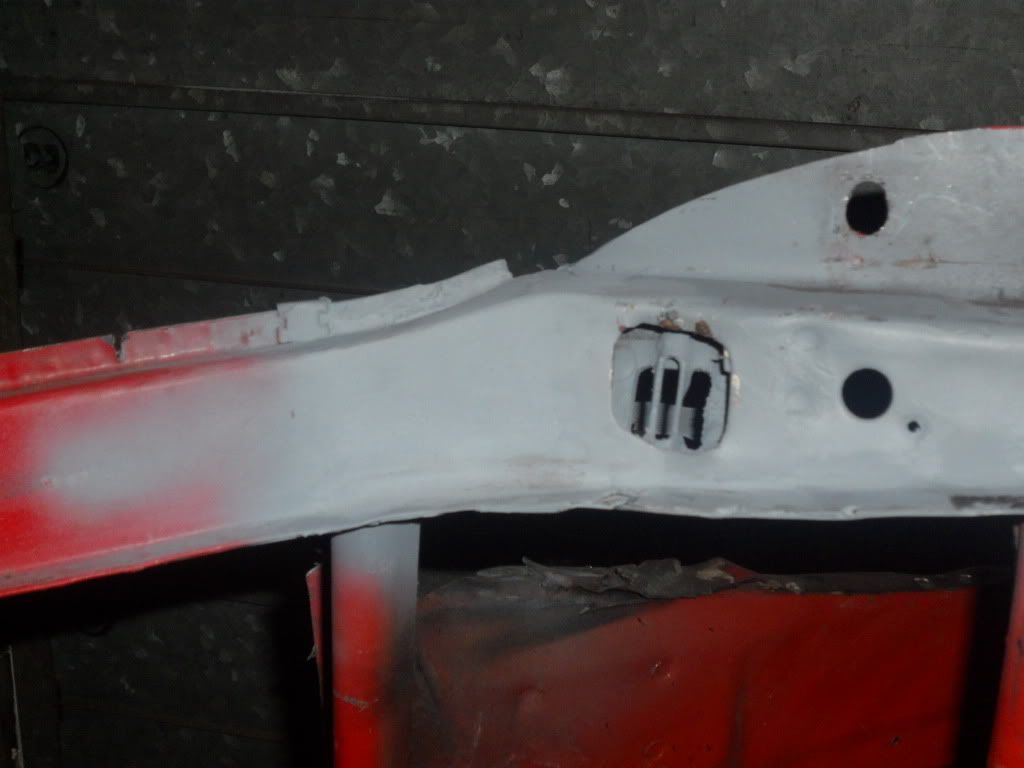
i then fitted and welded the doorstep in again using the the door to check for the gaps but got no pics with bare welds only when it was ground down

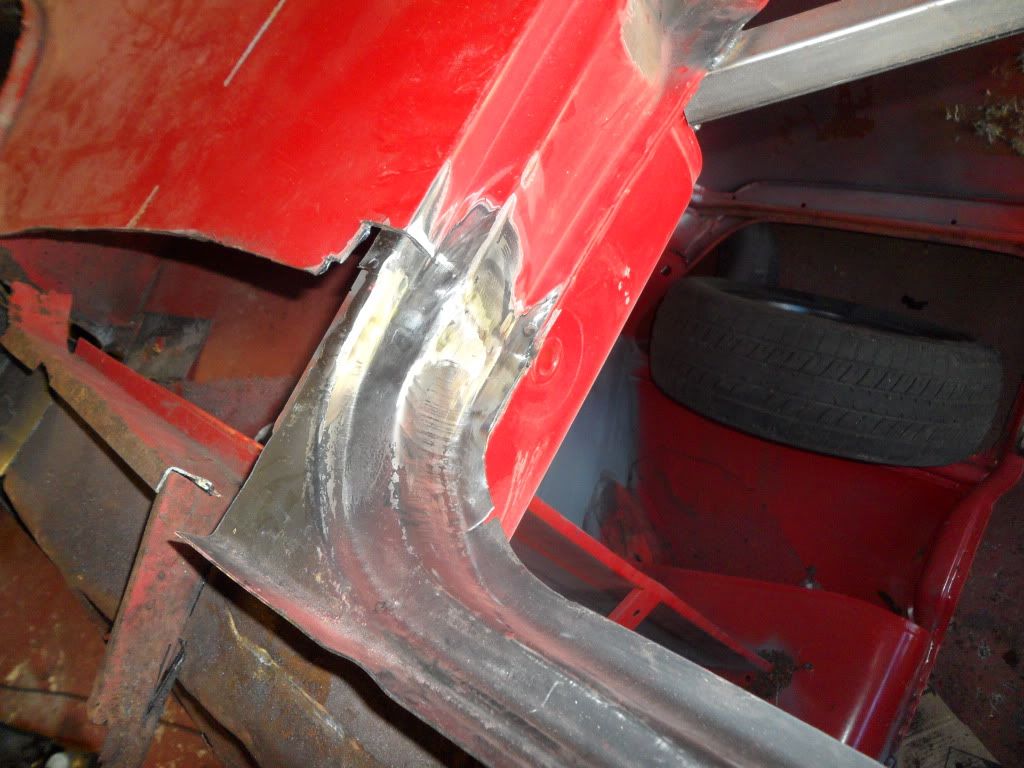
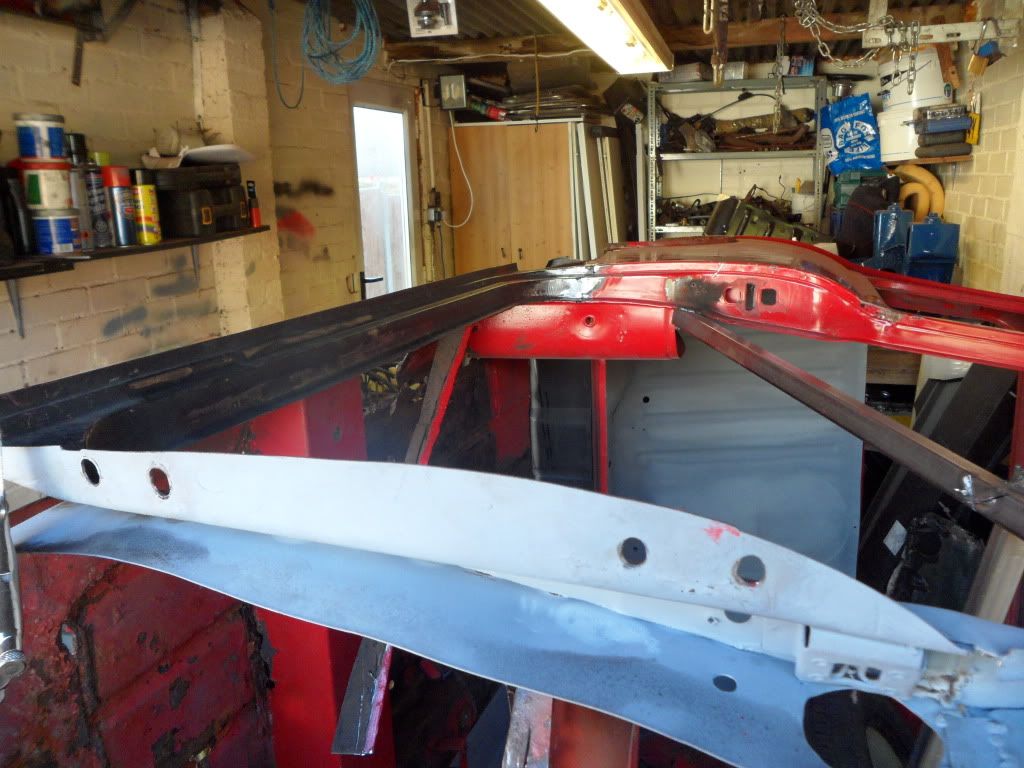
and as i have set my door gaps fairly tight there were a couple of welds on the door that were just touching the door frame so flatted them of also i stripped the door down as it was propa heavy putting on and off all the time and was supprised to find an mpi door so well chuffed
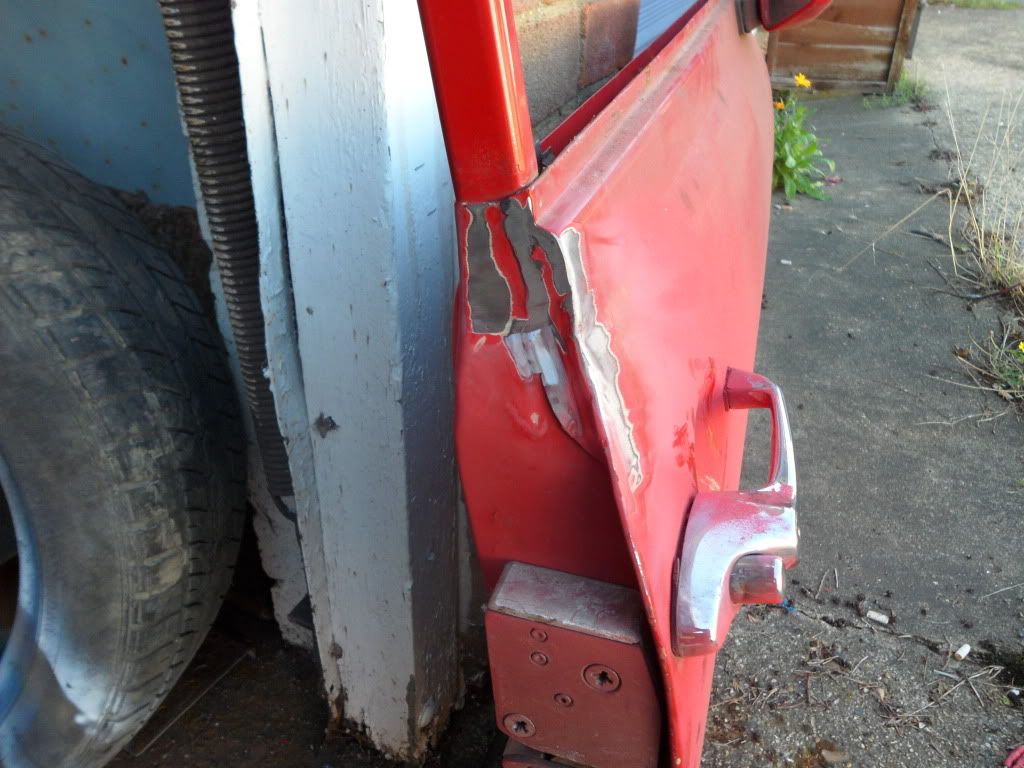
thats all for now should be starting on the floor removal over this weekend so more coming just need to save up for a new inner wing and front crossmember half
darren
Edited by Minidarren83, 27 September 2012 - 06:17 PM.
#72
Posted 27 September 2012 - 08:17 PM
nice work on the major cut out and reweld. Glad you used the door to check all the gaps as they can go off so easily. You are getting good at beating the rust into submission !!
Graham
#73
Posted 27 September 2012 - 08:34 PM
Ben
#74
Posted 28 September 2012 - 03:09 AM
Darren
#75
Posted 02 October 2012 - 07:47 PM
well it has been a fairly good week so far on the mini ive got most of the drivers floor cut out all the way down to the tunnel just need a final trim with a strait edge then its ready for the new heritage half floor that i picked up of ebay for £41 bargain the only problem is it is for a later mini with the small footwell but i can live with that
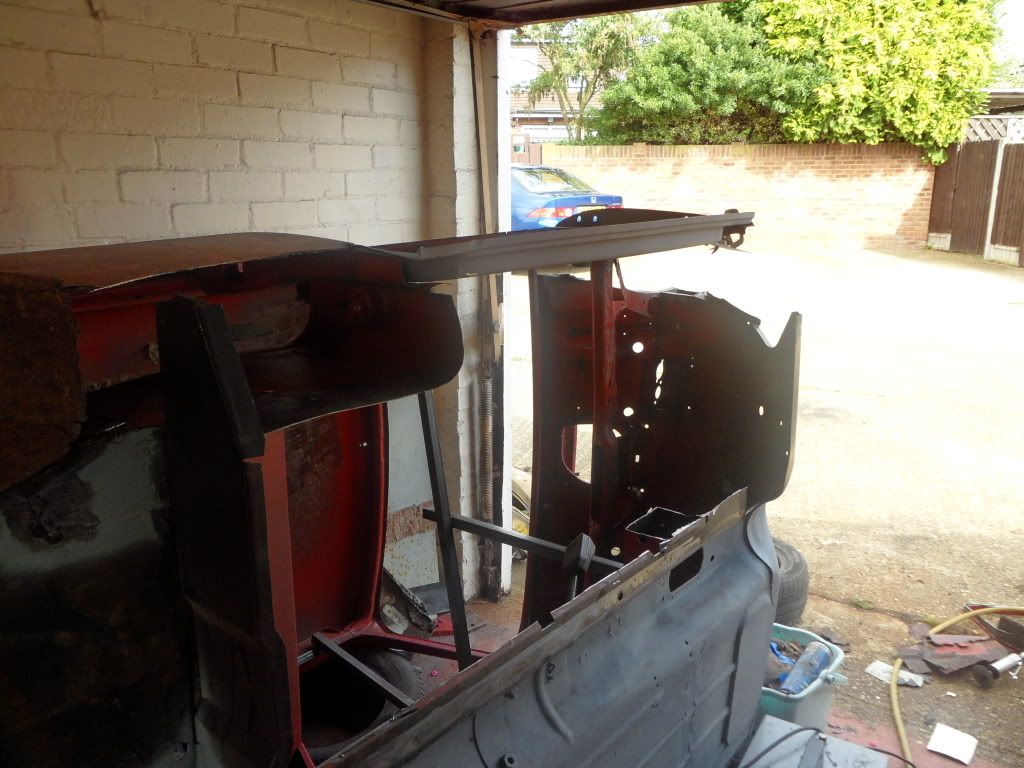
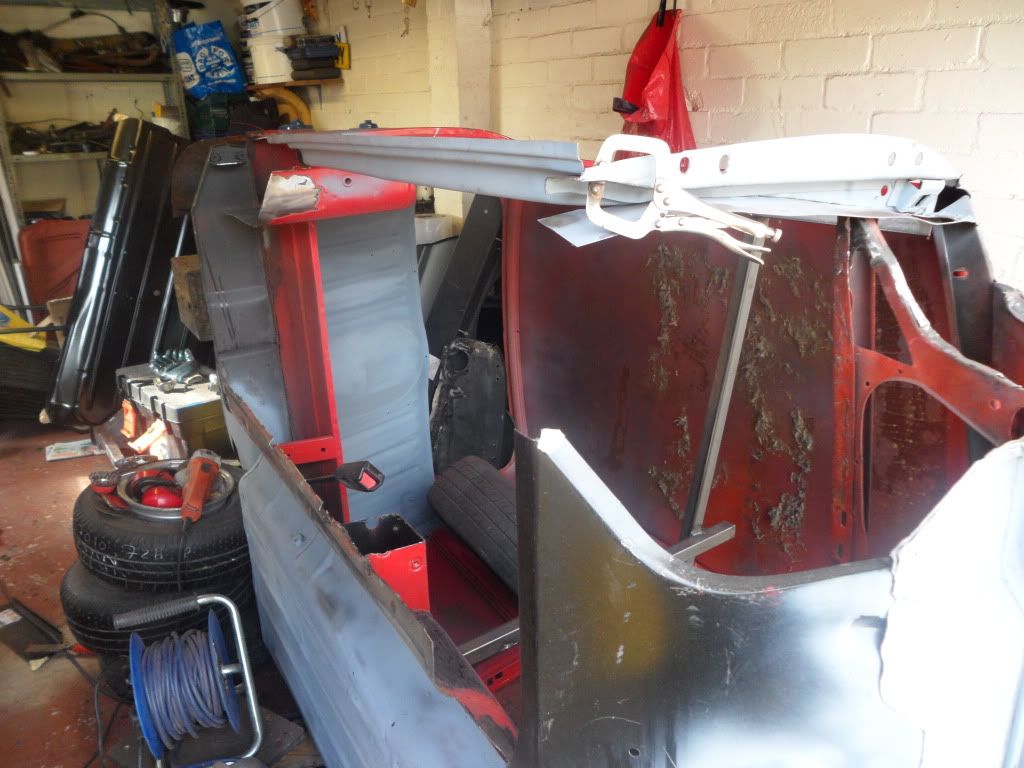
but before the floor goues on i need to tidy up the lower 2-3 inches of the companion bin as this area was pretty crusty and the flange that meets the floor was non existant and over the years of repairs and patches was just ugly so out it came
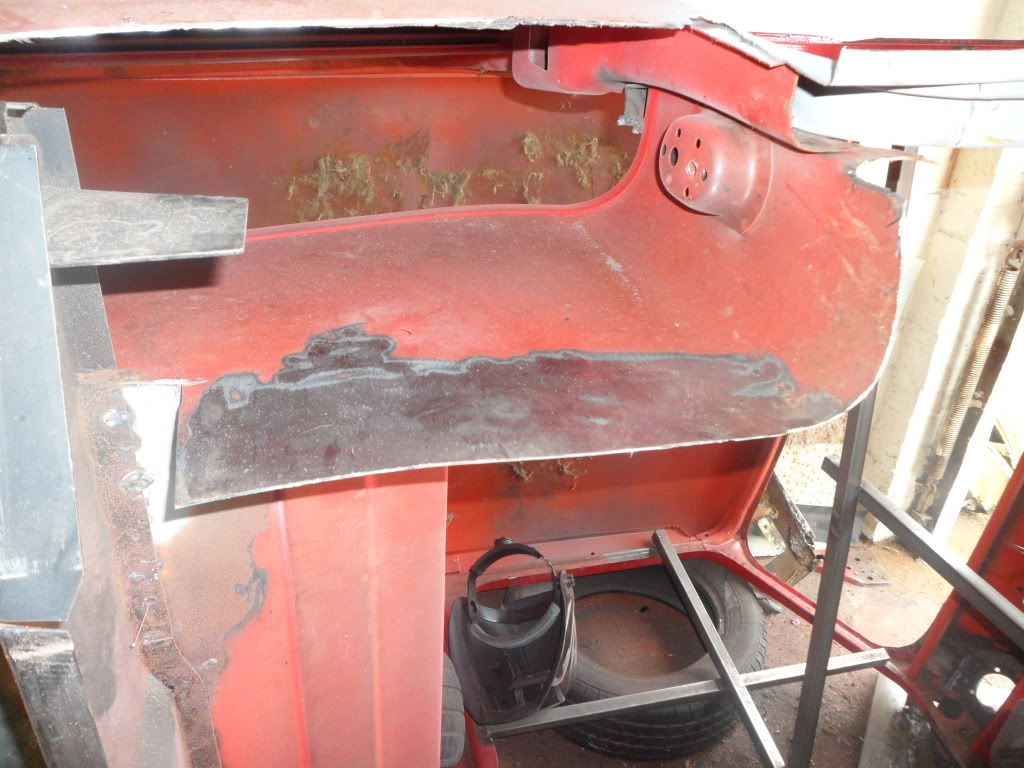
i then bashed the piece flat so that o could make a template of it
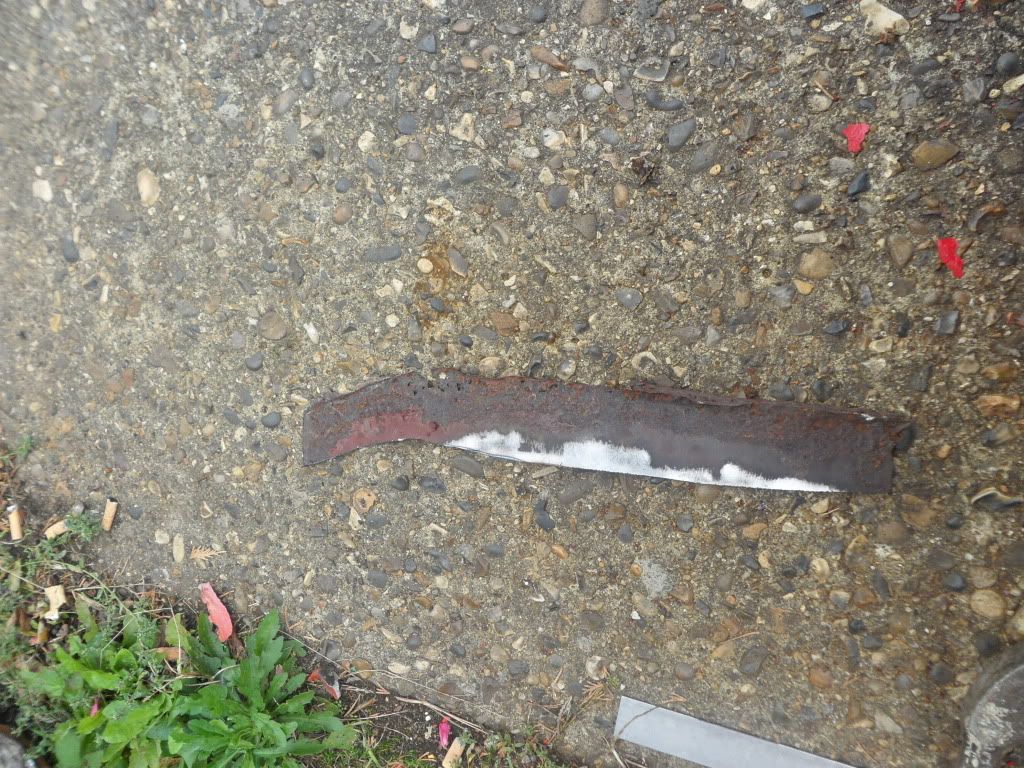
Then traced it out on a piece of steel and added the flanges and started cutting out
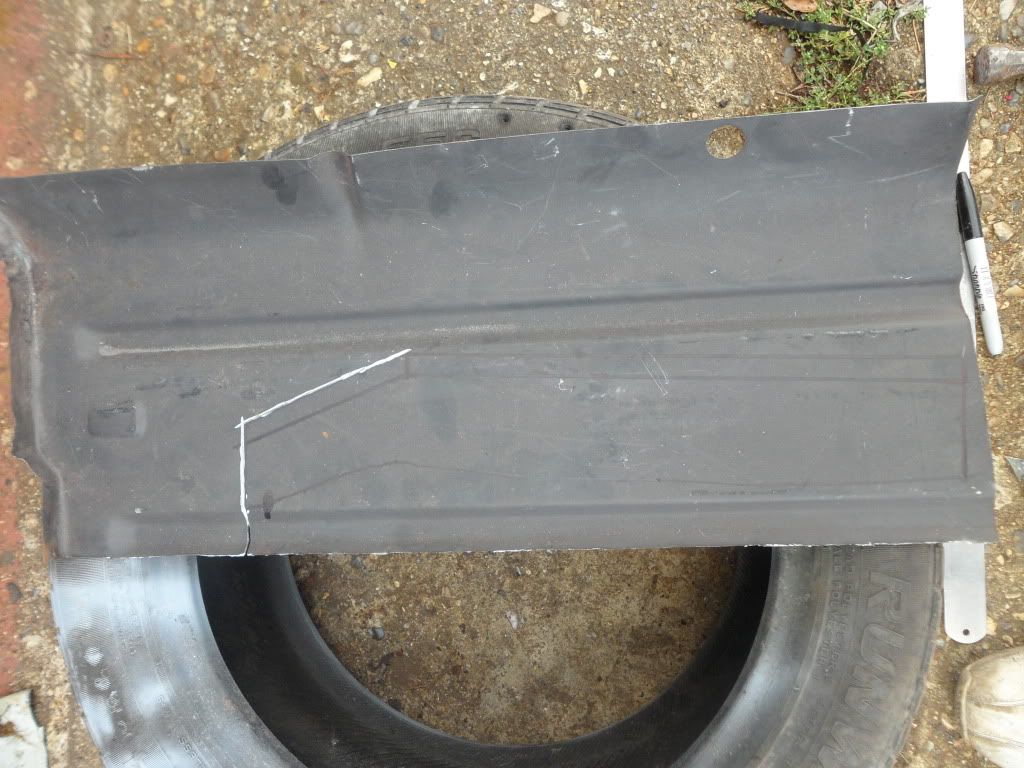
i find the best way to cut out a line that is not straight it to follow the line with the grinder or cut off wheel to score the metal and then bend and flex until it snaps off then trim the edges with the sanding disc. i then used a peice of angle and clamped it to the panel and bit by bit hammered over the flanges until they sat flat and did the same for the smaller flange but i forgot to take a pic of this process im sure you can all imagine
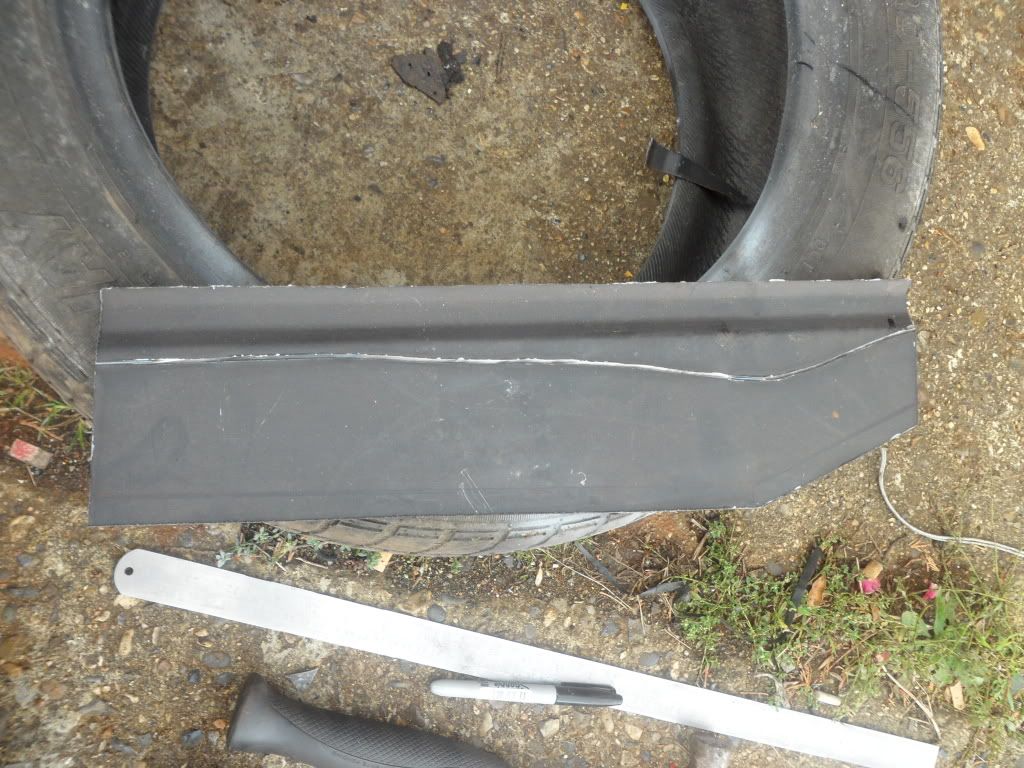
the part was then tacked in and for the curved part i just clamped and tacked as i went to follow the line which turned out better than i could of hoped for although the main section dropped a little when i welded it probably from the heat
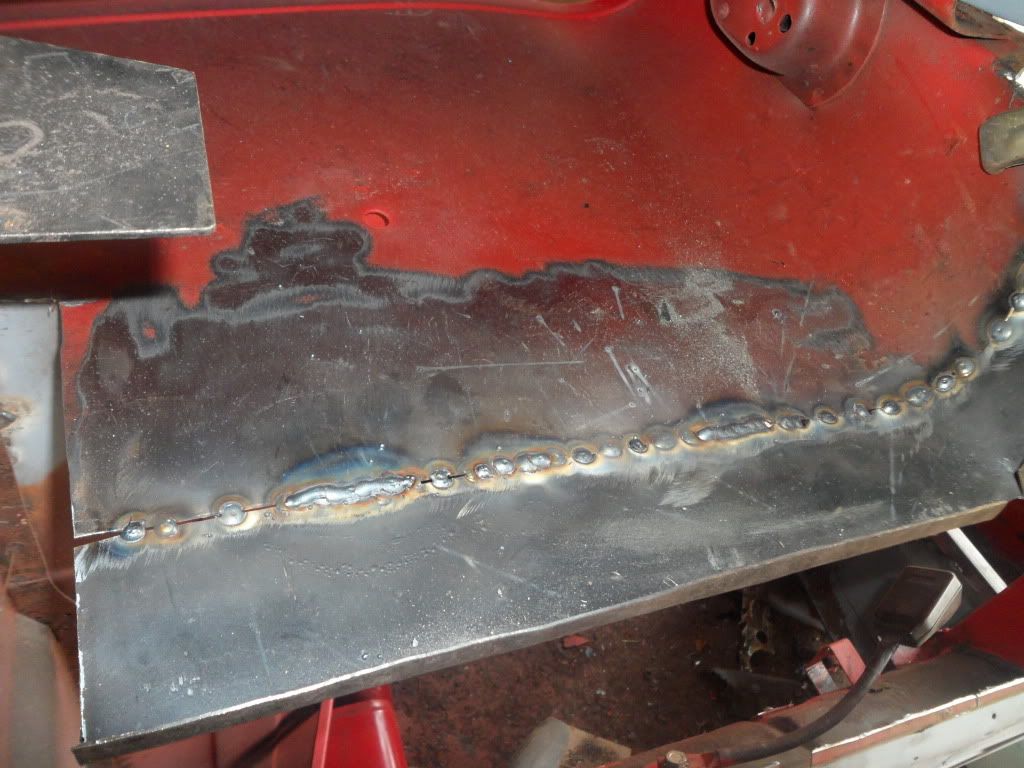
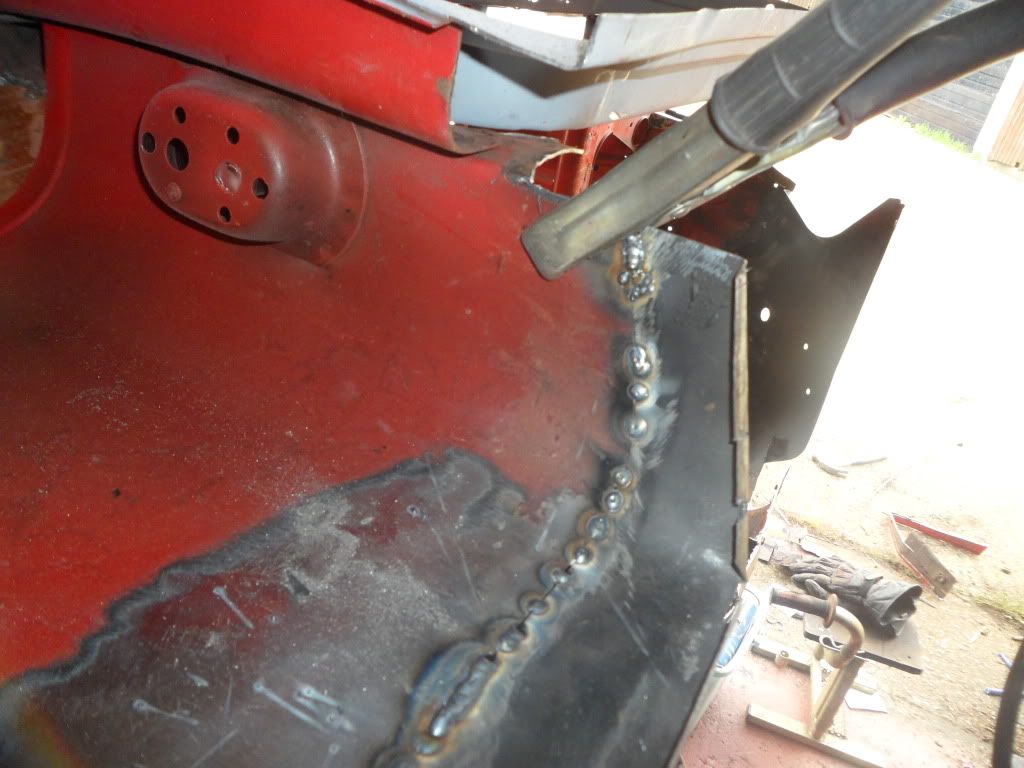

and then fully welded in getting better i think only blew two small holes and the penetration was spot on
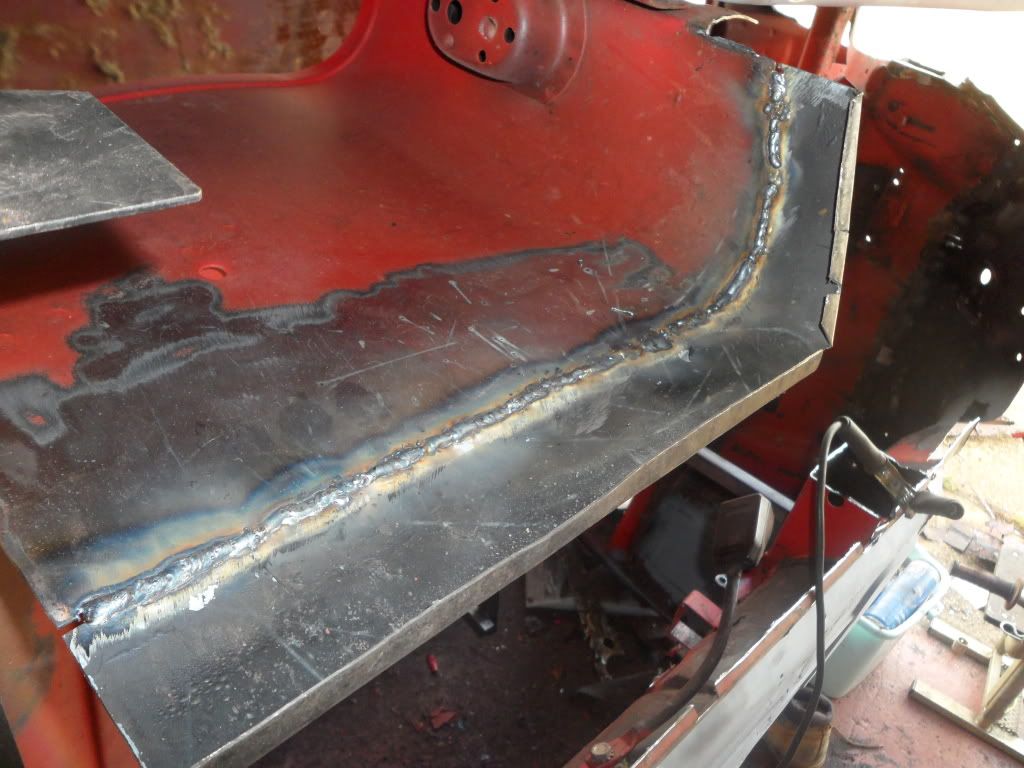
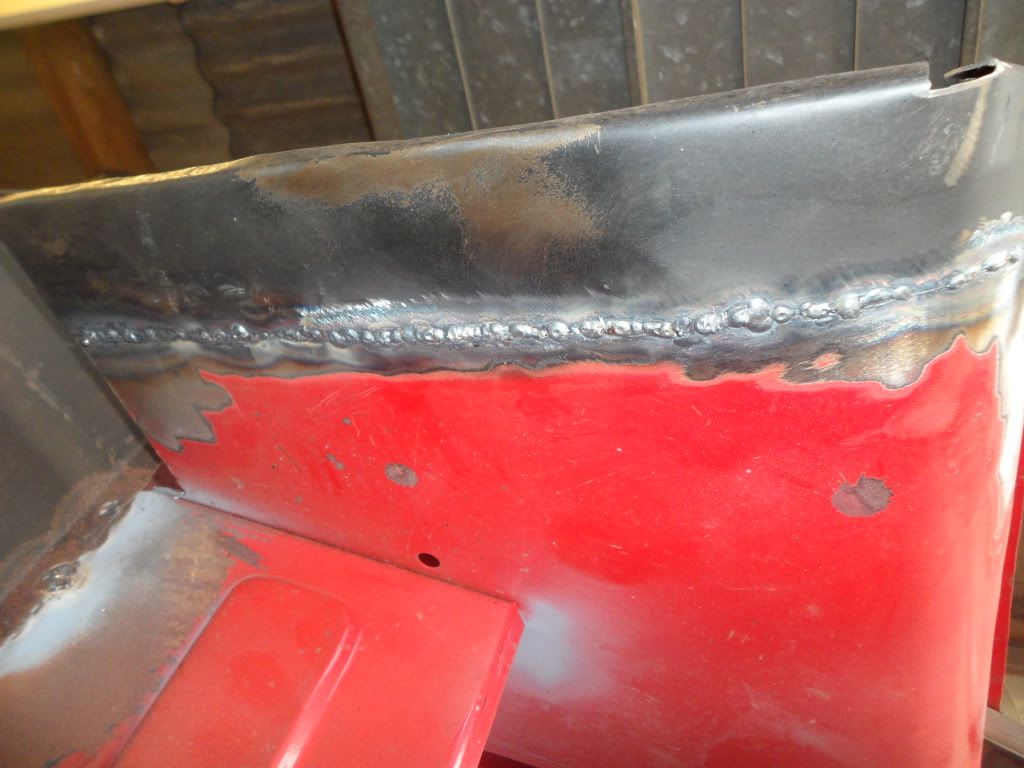
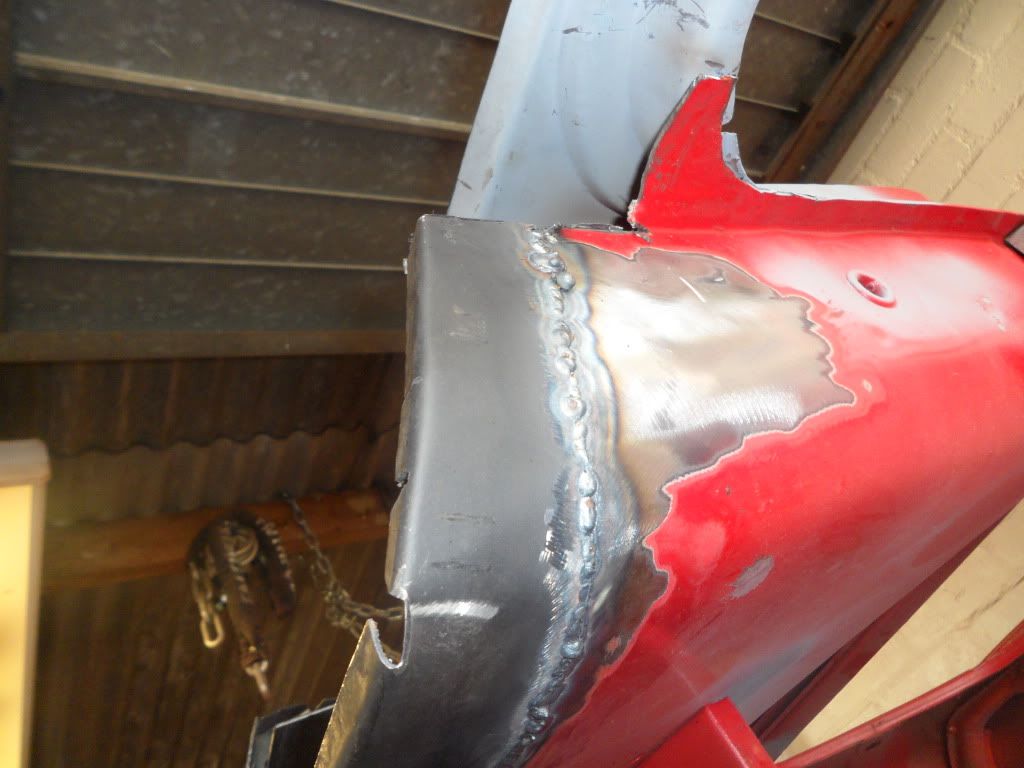
then started the grinding i am more than pleased with how the front turned out and the middle that you wont see didnt drop too much but i need more clamps in the future
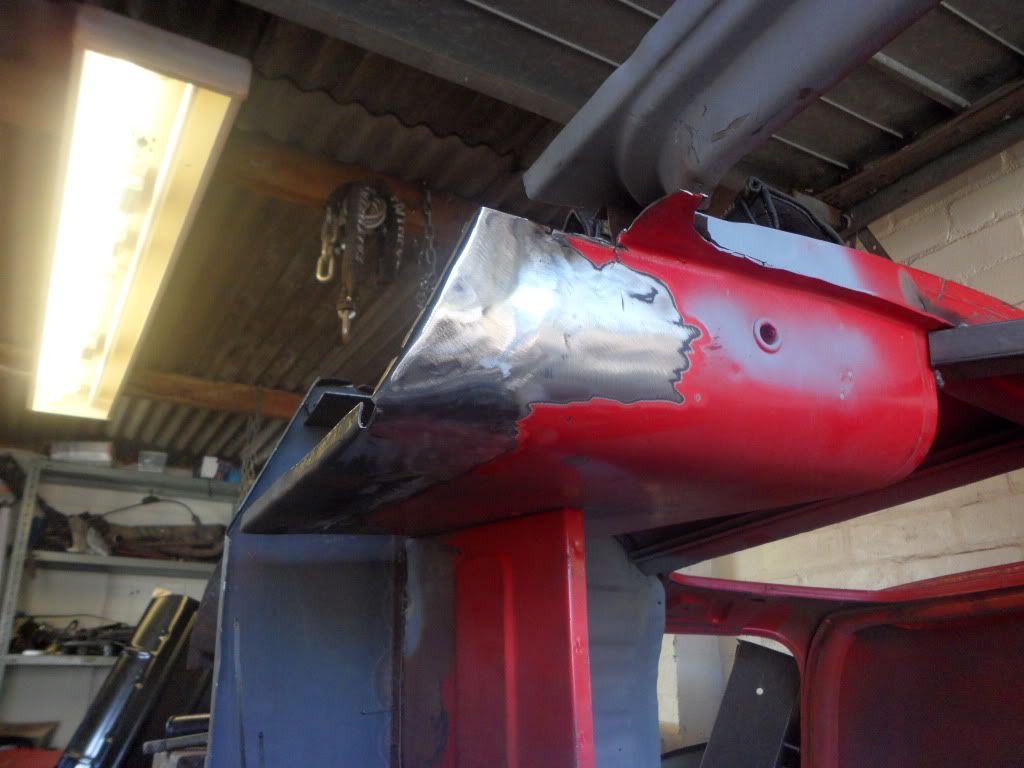
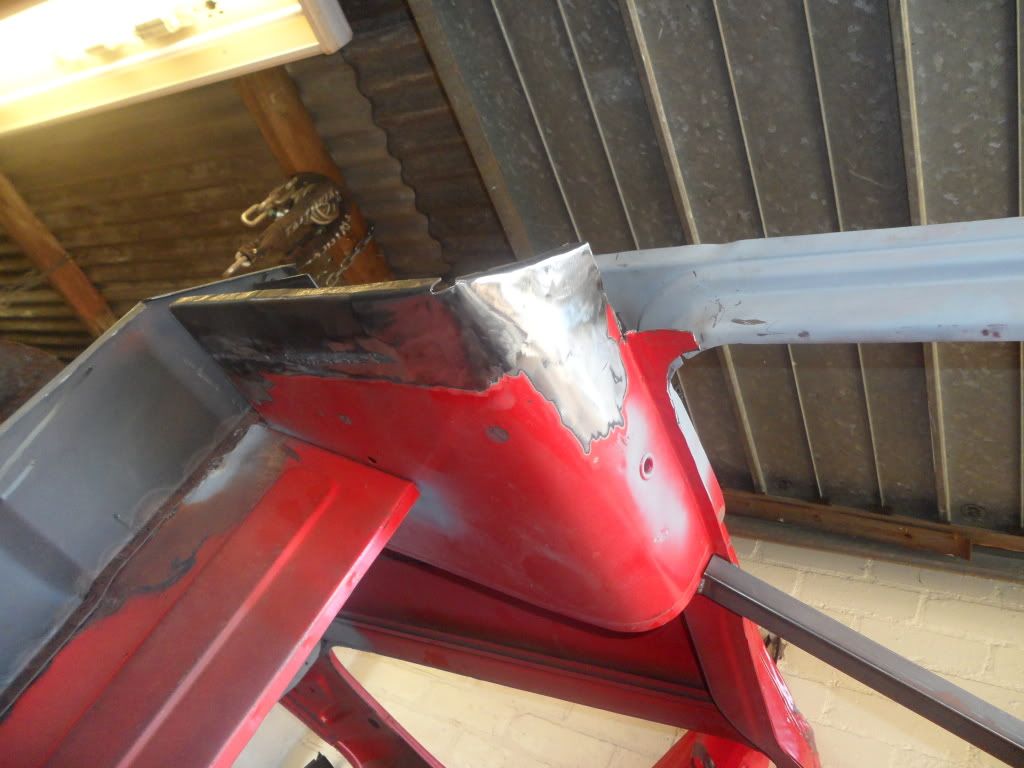
a small skim of filler will be needed this part to make it look perfect but i am happy as larry
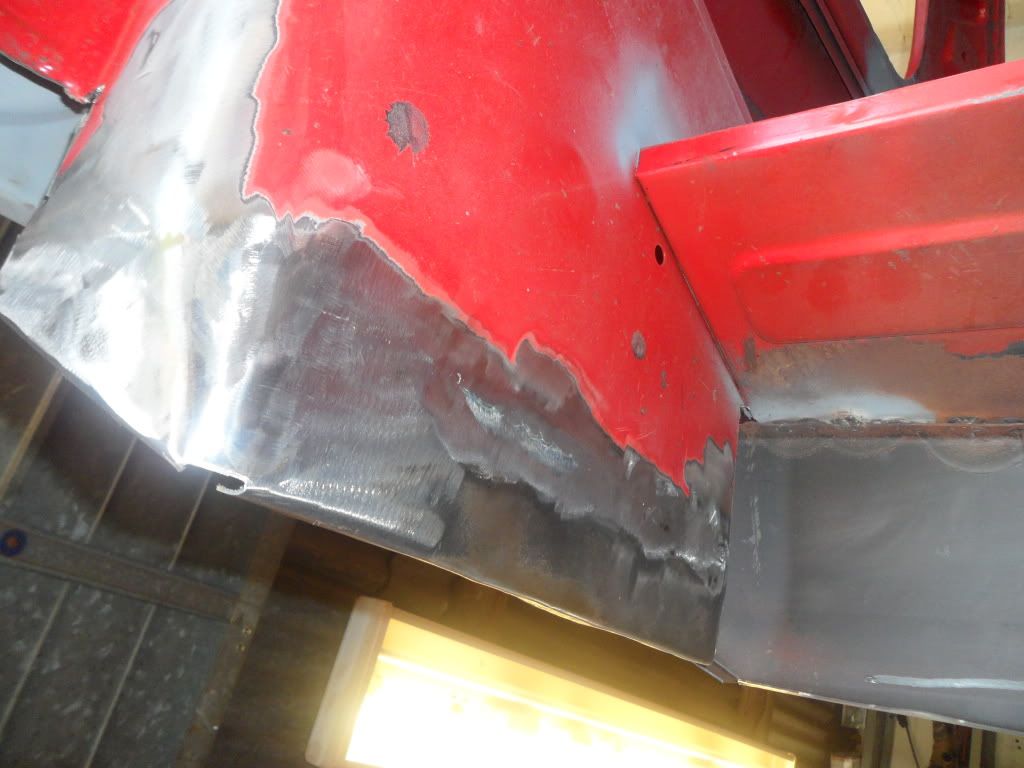
then with a bit of primer on it looks good i will filler when i bare metal this area
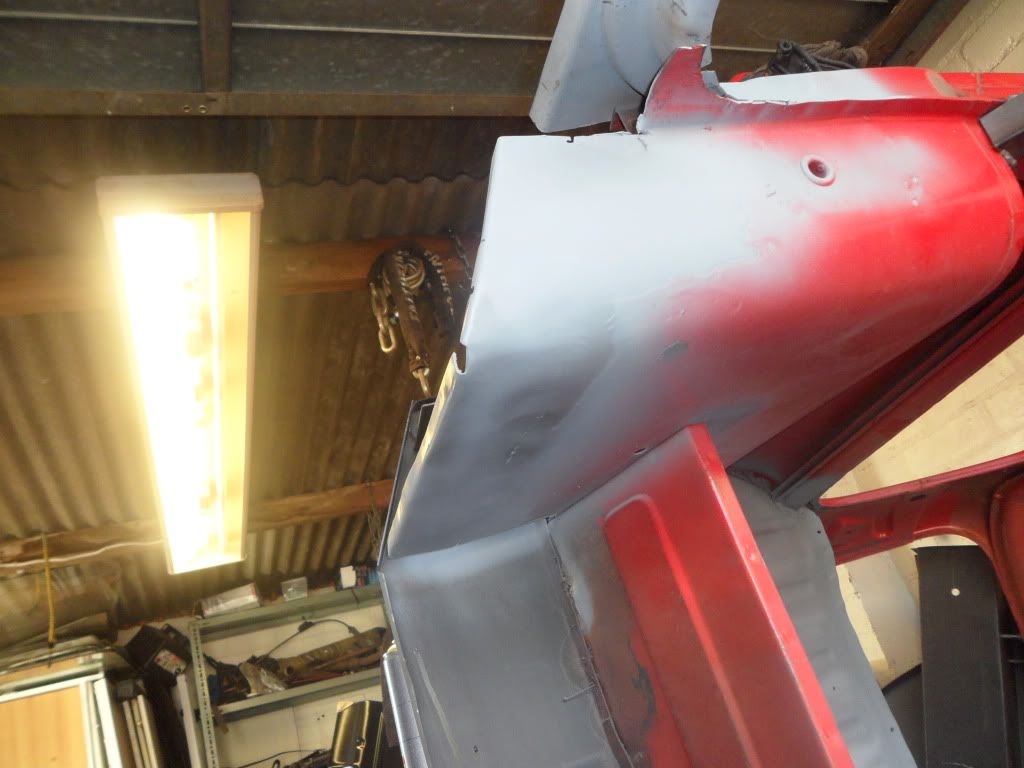
just one more patch on this area then i can start lining up the floor which i should have done by tomorrow so more to come
cheers darren
1 user(s) are reading this topic
0 members, 1 guests, 0 anonymous users