so a little later than promised but here are the pics of the inner sill stiffner
started with what was left of what came off
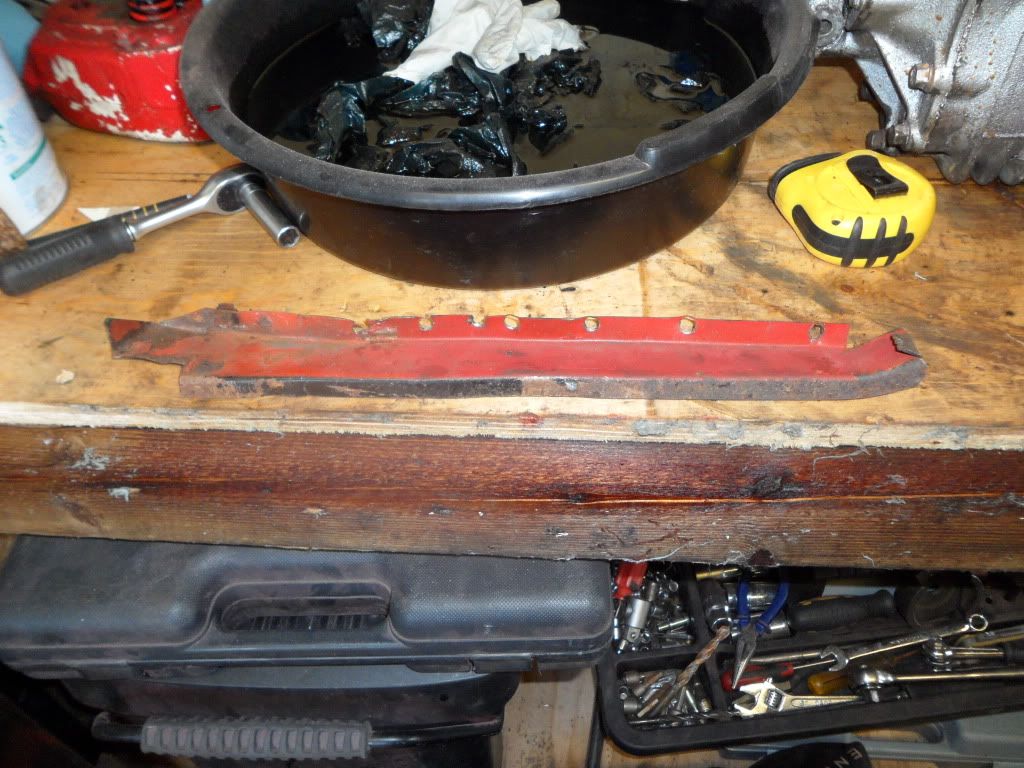
took some dimensions of the piece and it turns out that it gets wider towards the front of the car being 1,1/4 at the heel board and 1,1/2 at the doorstep end, only one pic we all know how to measure
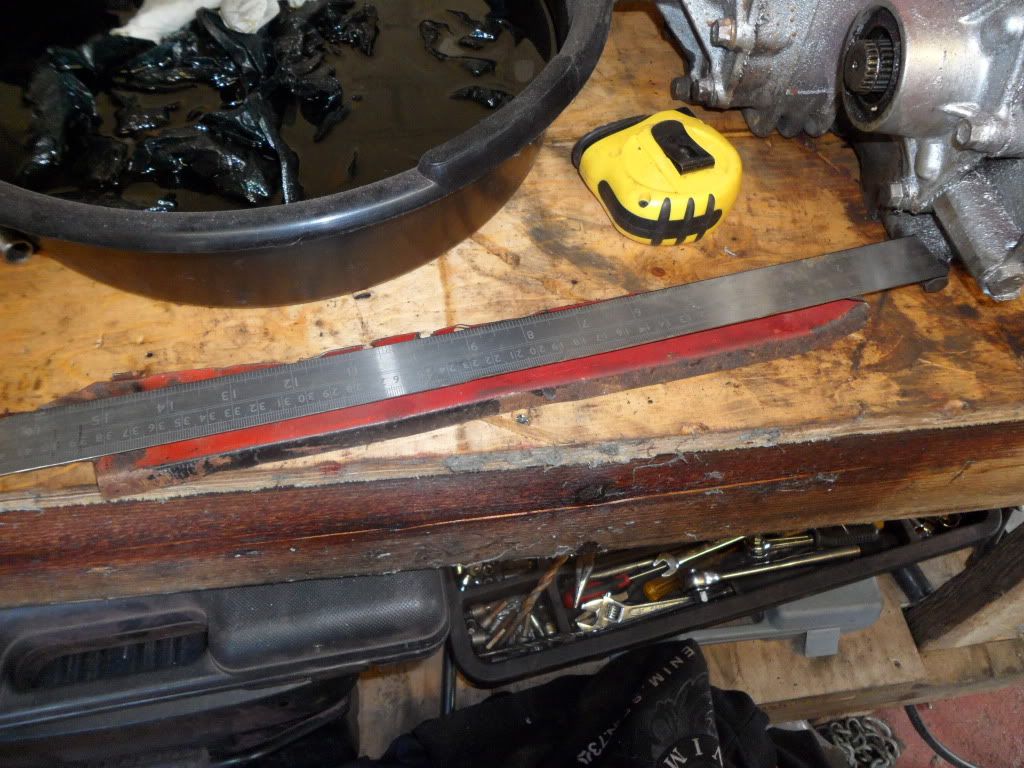
then transfered all the dimensions onto steel with all the fold lines and areas to be trimmed marked out
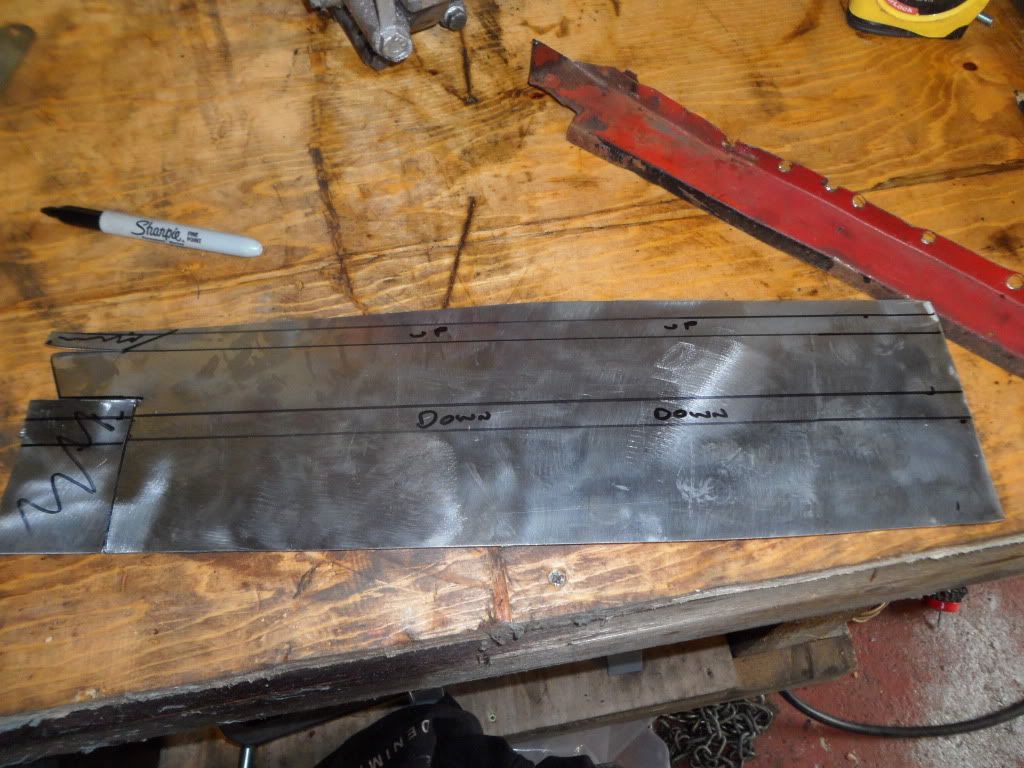
then folded trimmed and cut to shape i forgot to take picks of it before fitting but here it is all plug welded to the inner sill i have not tacked it to the heel board as yet so i can still get the arch close out panel under the tang
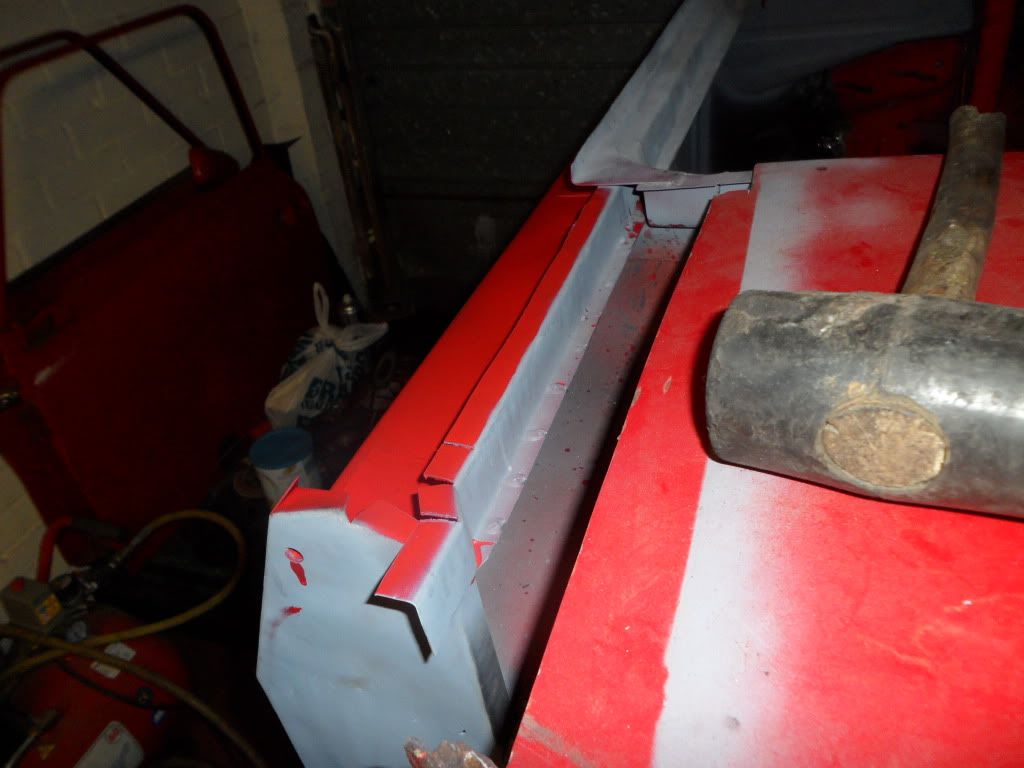
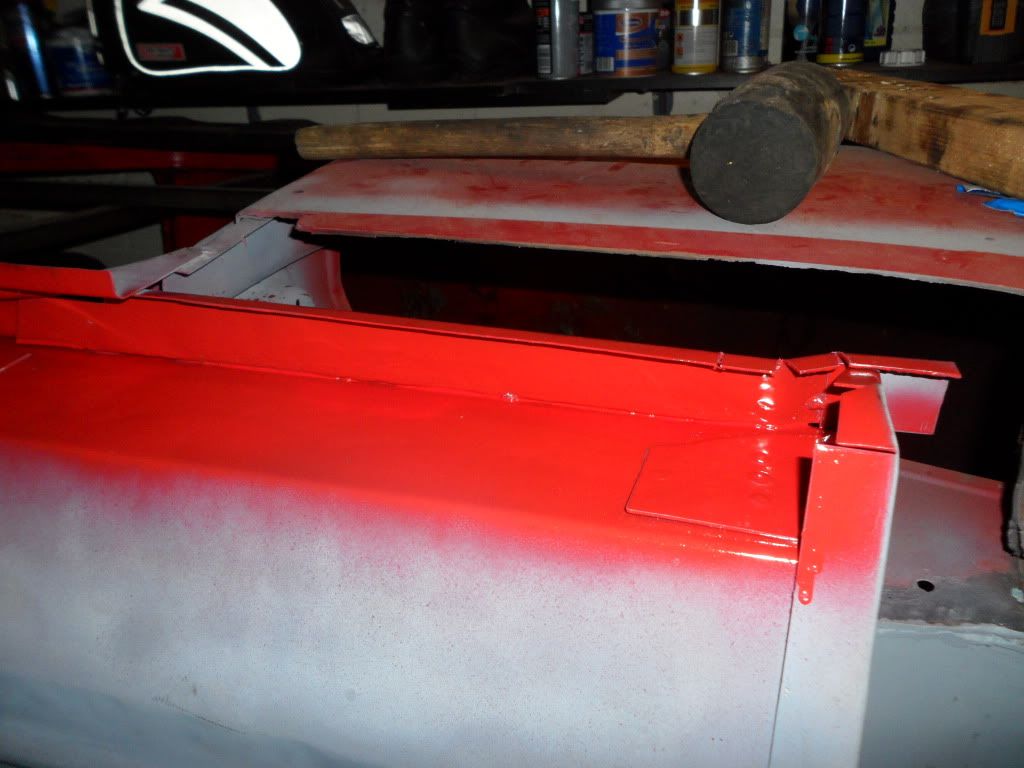
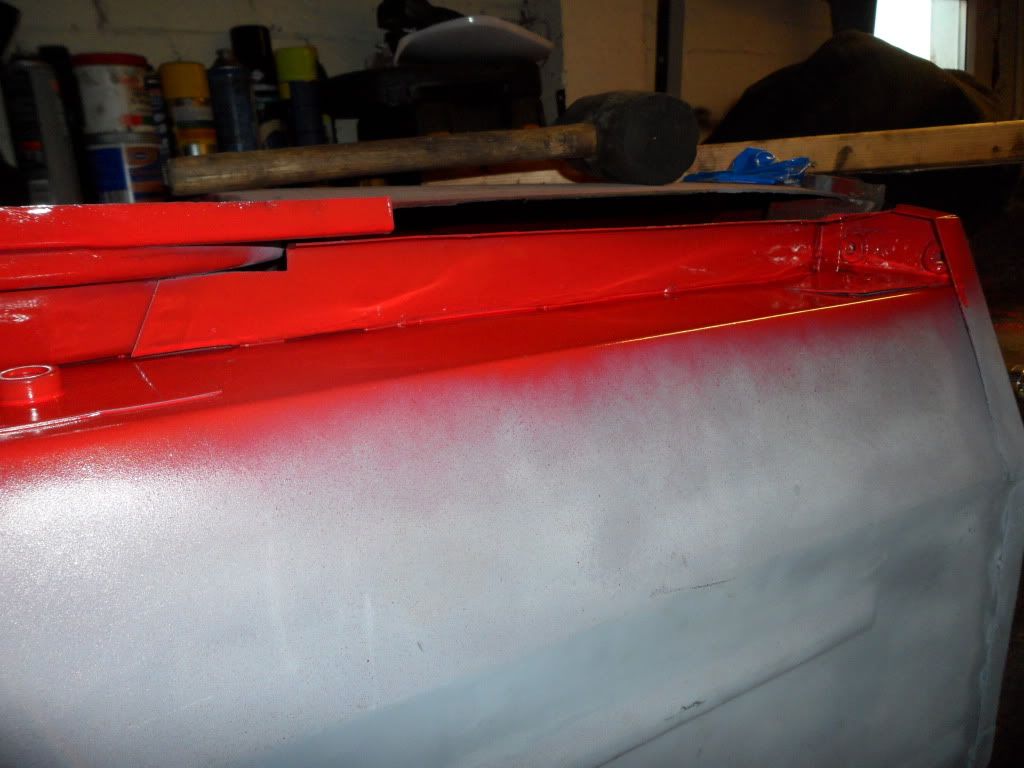
not sur if its right or not but my origional item had a little tang that sat under the doorstep but was not welded to the step so thats how i left it.
and with the depression of the whole doorstep saga i needed something else to take my mind off it for a while so i decided to deal up all of the welds i have done so far and it went ok but with everything mini was a lurning curve and as with everything on this car the otherside will be better i did not wet my finger when smothing it out so it is a little messy,
can seam sealer be sanded when it cures fully?
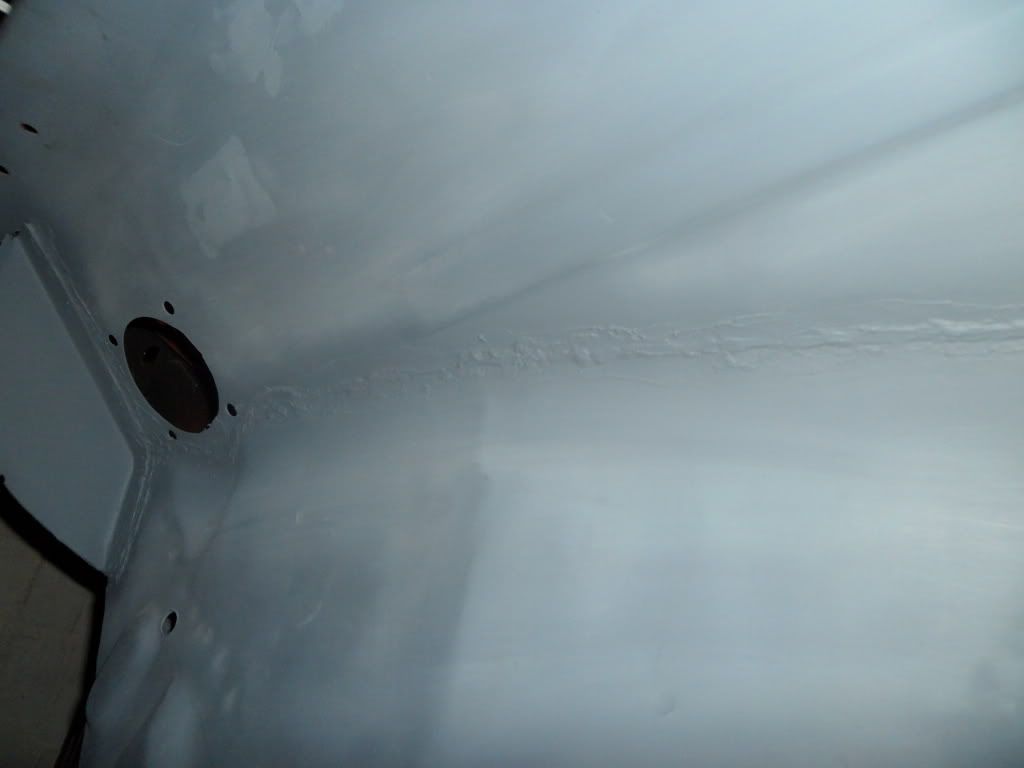
oh and also had another oopps as the car will be white when its done i wanted the inner sill cavity to be white so sploshed on some white over the hammerite red i had put on as a protection measure and it reacted almost instantly so will probably rub it back as best as i can and leave this side red but more lessons learned
Edited by Minidarren83, 06 August 2012 - 08:09 PM.