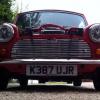
Do You Have To Use High Tensile Nuts On Suspension Parts?
#16
Posted 07 February 2012 - 11:13 PM
#17
Posted 08 February 2012 - 08:45 AM
Yes, and 8mm is useless, but so is a 5/16" unless it is torqued up correctly. The bolt may seem to be carrying all the load in double shear, but in practice it needs to be causing there to be friction between the tie rod fork and lower arm, so there is no fretting, which would cause rapid wear.
This is true, but what is the torque setting compared to what the low-tensile bolt is capable of?
#18
Posted 08 February 2012 - 09:13 AM
The point about using the correct nut, property class 5 (not grade 5) if it is a US bolt,or property class 8 on the European ISO ratings, is that the bolt will break before the nut strips, which is a safety feature to guard against over-torquing, because a broken bolt is very obvious. The wrong grade of nut may be on the point of stripping when what seems to be the correct torque is applied, and that is what the problem here is all about. That condition is dangerous, because it is not visible, and failure may occur without warning when driving the car.
So it does not matter what torque it will actually stand, the point is that you must use the correct nut and bolt, or a higher grade of both, always.
There are significant legal implications in the event of an accident if you have used the wrong part. Youi may well find that you are uninsured, and if the accident is sufficiently bad that the police do a full investigation, with forensics, and spot the wrong material, it could get even worse.
In any case, the correct grade of nut is easy to find.
#19
Posted 08 February 2012 - 10:01 AM
The difficulty as has already been discussed, is the quality of the bolts you get from where you buy them. Propper Engineering stores are the only place i'd buy any bolts from, and if you are really anal about it you can pay a little more and get traceable fastners gauranteeing it is what it says it is.
#20
Posted 08 February 2012 - 11:09 AM
However, whilst I would never advocate using anything but the highest spec bolts for suspension, I must say that in my years of rallying I've seen some quick repairs using whatever was to hand for fixing suspension. I've seen a 5/16" screw used to fit the tie bar to the lower arm on a very long and hard rally and the sort of shock loads put into that bolt are as high as you'll get with any Mini. It didn't break either. Actually I've never seen one of those tie rod to lower arm bolts shear. I have seen failure at the other end of the tie rod where the 'ear' virtually fractured off the sub-frame under rally conditions. That was before the 'ears' were always reinforced with a triangular steel plate welded on.
Anyway, just always buy top quality nuts & bolts and failure wil not be an issue.
#21
Posted 08 February 2012 - 11:10 AM
There are significant legal implications in the event of an accident if you have used the wrong part. Youi may well find that you are uninsured, and if the accident is sufficiently bad that the police do a full investigation, with forensics, and spot the wrong material, it could get even worse.
Now this is scaremongering.
But I was wrong about the 8mm and 5/16 size, should have checked rather than use my memory. Still I always like to use imperial where I can, just keeps everything the same.
#22
Posted 08 February 2012 - 11:19 AM
This is unlike an aircraft where each and every part fitted, down to a nut & bolt, has to be recorded and have a release note to confirm its spec and origin. There is no such requirement for cars and if/when there is none of us will be able to even use a spanner on our cars without formal inspection and sign-off afterwards.
#23
Posted 08 February 2012 - 12:03 PM

Wouldn't the ends of the rod rip through before the bolt sheared? I don't know if that is the correct bolt, but it does suggest one of the lugs will be doing more than the other. I wonder if failures of the subframe end are at least partly down to fatigue from being levered by the arm? A case against more solid arms and bushes???
#24
Posted 08 February 2012 - 01:34 PM
I never like the poly-bushes some fit to the front of the tie bars and there needs to be a bit of compliance on raod cars to take out the shock loads on bumpy roads. They are easy to change.
Now, more controversial, on rally cars the bolt is fitted upwards with the nut on top. If this is not done and a tie rod needs to be taken off to be replaced or straightened, the bolt cannot be removed. That is why I once saw a 5/16" UNF screw used as the bolt head had to be quickly cut off and there was no 'proper' bolt to replace it. When the nut is fitted on top a Nyloc or, better still, a castellated nut and split pin must be used.
#25
Posted 08 February 2012 - 01:40 PM
Tiger, the metric/ISO bolts are referred to as Class (Class 10.9, Class 12.9, etc). Inch/SAE bolts are by Grade (Grade 2, Grade 5, Grade 8).
(See Page 79 of the guide I linked to earlier).
The bottom line is, the fasteners (nuts or bolts) you use do not need to exceed what the factory used. No harm done if you do... but not necessary.
EDIT: Cooperman, how about the bolt pointed up and crossdrilled so a safety wire can be looped through the bolt above the nut to prevent it from loosening?
Edited by dklawson, 08 February 2012 - 01:42 PM.
#26
Posted 08 February 2012 - 01:55 PM

In real terms, I agree with what Doug and Effel have said. The bolt itself (IMO) isn't the weak link, the nut even less so. I think the whole testing of bolts for being under-spec in comparison to OE is a moot point really. I gueesssss that the safest thing to do in this kind of scenario is always match or better the original specification though.
The problem I have seen on tie-rods though is the problem that Effel hints at. The forked end of the rod appears to me to be the weaker and I have seen (on MOT inspection) elongated holes in those (one instance was where someone had fitted uprated poly-bushes to the front of the tie-rod). The fork shouldn't necessarily be pinched to the bottom arm, but it shouldn't be free to move. A shouldered bolt of the correct length would be FAR better than having one side of the fork on a shoulder, the other on a thread. That's asking for trouble!
#27
Posted 08 February 2012 - 02:08 PM
In aircraft design a fork-end fitting must only be clamped on one of the forks to avoid putting a bending pre-load into the base of the fork. A better design would be a stepped bolt with the plain portion at 5/16" diameter being about 0.030" longer than the width of the fork, then coming down to a 1/4" UNF thread with a 1/4" ID and a 1/2" OD 1/16" thick washer, followed by a castellated nut and split pin. The fork does not need to be clamped to the lower arm and if fact a slight amount of movement would be fine.
Maybe I'll draw that bolt and get some machined up in a high grade steel.
#28
Posted 08 February 2012 - 11:34 PM
I see your point about not deforming the fork, however this is almost mild steel, not aircraft grade alloy which would crack, and will plastically deform, once at least, without harm when you tighten the bolt. I believe that when the bolt is correctly torqued, friction helps to balance the load on both sides of the fork, which is why they need to be tight. Worn forks and/or lower arms are most likely due to the bolts being too loose. There may be a serious problem on some "uprated" tie rods, where the fork end is made differently. Talking of which, one I saw had spanner flats for adjusting with rather sharp radii, not where you want a stress raiser!
But I am with you on redesigning the whole thing. Probably long overdue, although for acceptable life (say 100k miles) I would expect that some kind of self-lubricating bush would be needed, not just a loose steel bolt in a steel hole. The angular movement would be tiny, so poly would do. And while we are at it, how about redesigning the front end of the tie rod. Rubber bushes work best in torsional shear, those on the front of the tie rod are subject to some rotation, and are probably not tightly enough clamped to deform in shear, but rather slip, which is bad. But also there is the angular component of the movement, which causes assymetric compression, which they handle rather badly. A dreadful bodge carried over from the Morris Minor, where it must have had similar problems, and I have never seen it on any other vehicle.
And what is a poly bush at the front of the tie rod, as some people use, going to do to bending loads, and fatigue? Can polyurethane handle compression? I have my doubts, but I have always had doubts about poly bushes, since most of them come with stainless steel inner sleeves, and as the material can't handle a lot of shear, unlike rubber, they must rotate on the sleeve. Just how long is that really going to last?
Polyurethane is a great material, but like all materials it is worse than useless if used where it is unsuitable. And as for poly subframe mounts, well the upper ones give a little bit of resilience fairly harmlessly, but the lower rears look like a solid poly moulding, which is going to stretch, and fail. I have not seen the teardrops closely enough to form an opinion about them, but give me solid mounts all round, every time!
Considering the amount of work done in many engine conversions and other modifications, it does not seem to me to be all that difficult to make new one piece wishbones and adapt the front mounts on the subframe so that normal bushes are used, getting rid of the tie rods. I seem to recall that the Metro has one piece lower arms, perhaps they could be adapted?
#29
Posted 09 February 2012 - 12:01 AM
A re-design is long overdue and maybe a front mounting sort-of like a damper mounting could be fabricated on the sub-frame with really strong side plates and a 3/8" bolt.
The other end at the lower arm mounting could use a re-think too. A stronger end fork fitting would be good, but I wonder if there would be enough land left on the lower arm if it was bored and reamed out to 3/8" to take a fitted bolt. Probably not and a new lower arm would be necessary. I don't have one to hand to measure as I'm nice and warm in my house!
#30
Posted 09 February 2012 - 12:52 AM
2 user(s) are reading this topic
0 members, 2 guests, 0 anonymous users