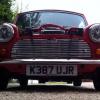
Do You Have To Use High Tensile Nuts On Suspension Parts?
#1
Posted 06 February 2012 - 12:03 AM
I've lost the 5/16 nut which attaches the lower arm and the tie bar and need to get new ones. Does it have to be a high tensile nut or will a normal nyloc nut be fine?
cheers, dave
#2
Posted 06 February 2012 - 12:07 AM
#3
Posted 06 February 2012 - 12:21 AM
#4
Posted 06 February 2012 - 12:24 AM
#5
Posted 06 February 2012 - 06:59 AM
The strength of the nut MUST be matched to that of the bolt, which does not actually mean that they are the same grade of steel. The nut material will actually be softer. The nut should be marked "8" meaning it is property class 8, and suitable for a grade 8.8 bolt. If you use a grade 10.9 bolt, the nut should be marked "10".
You can use a higher grade nut, but never lower, than the bolt. That is because it is unsafe to have a situation where the nut may be on the point of stripping due to too much torque. It is considerd to be safer to arrange things so that the bolt breaks, always, if overtorqued, to give a very obvious warning.
It is likely that if you buy a 5/16" nyloc in Halfords etc it will be property class 8, but you must check for the correct marking.
#6
Posted 06 February 2012 - 10:06 AM

#7
Posted 06 February 2012 - 11:23 AM
Minispares are reasonable, especially if you're buying other bits.
#8
Posted 06 February 2012 - 07:24 PM
But will anyone be selling SAE bolts in the UK? I would expect ISO to be more common nowadays.
My first two Minis had bolts with a circular recess and the letter S, and nuts with a line of circles stamped up one side, which were grade S in the old BS system. I think the third had a mixture.
Personally I would buy a pack of 10 nuts, on the basis that I would need them all, sooner or later, probably sooner with a Mini....
#9
Posted 06 February 2012 - 09:03 PM
Invest in the high-strength nuts if you want to. It will not hurt anything. However, they are not going to buy you any better performance. The regular nuts are NOT going to catastrophically split and fall off. Nuts typically fail by thread pull-out under high tensile load. That is not present on these components.
EDIT: Those curious can download the fastener guide from Unbrako using the link below. The file is 3.4 Meg so it takes a few moments to download. See page 79.
http://unbrako.com/docs/engguide.pdf
Strength of fasteners is covered by industry standards. In this case SAE J429
Grade 5 in sizes up to and including 1" are rated for an ultimate tensile strength of 120,000 PSI.
Grade 8 in sizes up to 1-1/2" have an ultimate tensile strength of 150,000 PSI.
So... Grade 8 is about 25% stronger than Grade 5 but both are well above what is needed in this application.
Edited by dklawson, 06 February 2012 - 09:17 PM.
#10
Posted 06 February 2012 - 11:04 PM
I don't think the original question was about using grade 10.9, it was about using high tensile as opposed to mild steel, and both 8.8 and 10.9 are high tensile. A mild steel nut, which are available cheaply, would be extremely dangerous in this application, or just about anywhere else on a car. A "property class 8" nut is matched to an 8.8 bolt and is ideal, a property class 10 nut is just wasted money, but can be used if it is what is available. A property class 5 nut should not be used on any mechanical or structural part, and is only marginally stronger than mild steel..
#11
Posted 07 February 2012 - 01:14 PM
Hardness and toughness are not equivalent. Hardness is not typically desired in a fastener (nut or bolt) as hardness typically equates to brittleness. What is desired is higher toughness. Toughness defined in its simplest explanation is the ability to absorb energy prior to failure. (I make no attempt here to provide the stress/strain definition here). The application guides I use in my work focus not on bolt failure (snapping) but thread pull out.
Regardless, from a geometry standpoint, fasteners theoretically develop their full strength in three threads. In practice, steel bolts in steel tapped holes develop acceptable industry standard strength in "one diameter". That is to say, if you have a 5/16" bolt, you will develop full thread strength in a tapped hole 5/16" deep. With aluminum, the hole depth is typically 1.5x the diameter.
Will a Grade 5 nut strip before a Grade 8 when subjected to equal high levels of torque? Yes... assuming the bolt does not fail first. Does it matter in this application? No. The steering joints are held into their respective arms by the taper lock of the components. The torque level applied to the nuts is typical of other bolted joints on the car. If you choose to use higher-strength nuts... fine. You are not hurting anything. However, you are not gaining anything either.
Edited by dklawson, 07 February 2012 - 01:15 PM.
#12
Posted 07 February 2012 - 05:01 PM
dave
#13
Posted 07 February 2012 - 05:58 PM
Sure, use the high tensile stuff, but in thus case it will not be a problem using lower spec nuts. It is a little anoying that there is so much doom-mongering in this thread, when there is no risk. It seems that the doom-mongers do not fully understand what is specifically being asked.
As it happens, you should use a 5/16 UNF bolt, and not an 8mm. The 8mm will rattle about a bit.
#14
Posted 07 February 2012 - 09:19 PM
On safety critical parts, always use the correct nut and bolt, and torque them up correctly. The original designer knew what he was doing, but you and I do not necessarily have all the facts.
#15
Posted 07 February 2012 - 09:36 PM

Edited by Surfbluegarage, 07 February 2012 - 09:36 PM.
1 user(s) are reading this topic
0 members, 1 guests, 0 anonymous users