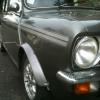
Space Frame Tubing
#1
Posted 16 December 2011 - 09:26 PM
Thinking about designing the frame, but unsure of what size tubing to use and also what material.
Any thoughts/ advice on tubing?
#2
Posted 16 December 2011 - 10:54 PM
I would go for mild steel. If you spoil a few bits, it does not break the bank.
As to size, look at other projects for some idea. There are books on the subject too, but calculations can be rather complex.
#3
Posted 17 December 2011 - 12:25 AM
I think your bigger issue is going to be in the cost of the equipment to build the frame and knowing how to use it though. You're looking at the thick end of £3K for the welder, tube bender, frame table and the many other sundries needed and you've still got to learn how to do it all.
#4
Posted 17 December 2011 - 12:53 AM
How the basic input loads would be decided on is another matter and you would need to speak to a qualified automotive desigtn consultant. My son does this type of work in F1 and le Mans car engineering.
Remember, the space-frame structure is the primary source of strength and failuere due to incorrect stress analysis could prove fatal.
I used to own a design consultancy and this was the sort of work we did all the time. It is both complicated and expensive.
#5
Posted 17 December 2011 - 12:58 AM
#6
Posted 17 December 2011 - 12:59 AM
#7
Posted 17 December 2011 - 12:59 AM
You really need CDS (cold drawn seamless) or T45 for space frames. I believe you and weld CDS with standard MIG wire but you need a specialist wire for T45, both would benefit from being used in a proper pulse MIG machine or you could TIG. Get an MSA blue book, all the info you need on materials will be in there.
I think your bigger issue is going to be in the cost of the equipment to build the frame and knowing how to use it though. You're looking at the thick end of £3K for the welder, tube bender, frame table and the many other sundries needed and you've still got to learn how to do it all.
Where can i get the blue book from?
#8
Posted 17 December 2011 - 01:03 AM
The very fact that you have had to ask these questions suggests to me that this is well beyond your present knowledge and capabilities! Not to damp your spirits - but there's a bit more to it than just sticking a few tubes together and welding them up. You may want to break yourself in by trying your hand at a Locost - at least get the Haynes book and read all about it!
I have knowledge of engineering, its my job, but i have never built a cage or a space frame before and so wanted some advice.
My skills are more in the CAD and CNC machining department.
I understand what you say and will take your advice, thanks.
Edited by M_Brown_Mini, 17 December 2011 - 01:13 AM.
#9
Posted 17 December 2011 - 01:08 AM
#10
Posted 17 December 2011 - 10:25 AM
I don't think you necessarily need a tube bender. A genuine space frame carries all significant loads in tension or compression, and it follows that you can't have any stressed members which are curved. That is not to say that you can't make a frame with curved parts, just that they will necessarily be used inefficiently, and it will be a multi-tube frame, not a space frame.
If you use round tube, which does result in a slightly lighter and/or stiffer frame than using square section, you will need a tube notcher for cutting the joints, but that is not terribly expensive, being just a jig which guides a holesaw.
I would advise paying no attention whatsoever to the Haynes "Build Your Own Sports Car on a Budget" manual. I bought one a while back, complete waste of money, and I would never, ever drive such a car. It may have been designed by computer, which means that all the bits should fit, but it was clearly never subject to a proper stress analysis, and is dangerously weak and lacking rigidity in places, bit in other places it uses far too much metal. No lateral bracing on many of the suspension mounts, which carry lateral cornering loads, no vertical bracing on the engine mounts, a transmission tunnel which uses a lot of steel and adds no rigidity whatsoever, etc. And, he suggests making the wishbones fron hydraulic tubing, which is CDS, but omits to specify the wall thickness, while there are 4 or 5 widely varying thicknesses available. Which one is correct, and which one do people use? The sad thing is that when they start having fatigue fractures, the owners will think that it was their own lack of welding skill, when in fact the design ia a disgrace. Look at the web sites of the several "seven" type manufacturers to see spaceframes which do address these points and in some cases are not very expensive. Just because something is written in a book, it does not follow that it is correct, or safe.
Also, beware of using stress levels, g forces etc, from any book used for track cars on the road. Admittedly, you don't thrash a car so hard on the road, but nowadays there are dreadful bumps and potholes to contend with. If in doubt, make it stronger. And, a track car may not be allowing a sufficient margin for fatigue, as it may only need a relatively short life.
As others are saying, it is not going to be easy. There are a lot of projects around, some quite successful, where they likely have not done all the stress calculations and got away with it. They probably take inspiration from other things that work, and to an extent you can do the same by looking at other designs. The web sites of kit car manufacturers may give some idea of what is possible, as many of those use spaceframes.
#11
Posted 17 December 2011 - 11:03 AM
Just to clarify, CDS is a good but fairly easy type of steel to weld, it only means cold drawn seamless, and depending on wall thickness, will weld with MIG or even arc, although TIG would be neater.
I don't think you necessarily need a tube bender. A genuine space frame carries all significant loads in tension or compression, and it follows that you can't have any stressed members which are curved. That is not to say that you can't make a frame with curved parts, just that they will necessarily be used inefficiently, and it will be a multi-tube frame, not a space frame.
If you use round tube, which does result in a slightly lighter and/or stiffer frame than using square section, you will need a tube notcher for cutting the joints, but that is not terribly expensive, being just a jig which guides a holesaw.
I would advise paying no attention whatsoever to the Haynes "Build Your Own Sports Car on a Budget" manual. I bought one a while back, complete waste of money, and I would never, ever drive such a car. It may have been designed by computer, which means that all the bits should fit, but it was clearly never subject to a proper stress analysis, and is dangerously weak and lacking rigidity in places, bit in other places it uses far too much metal. No lateral bracing on many of the suspension mounts, which carry lateral cornering loads, no vertical bracing on the engine mounts, a transmission tunnel which uses a lot of steel and adds no rigidity whatsoever, etc. And, he suggests making the wishbones fron hydraulic tubing, which is CDS, but omits to specify the wall thickness, while there are 4 or 5 widely varying thicknesses available. Which one is correct, and which one do people use? The sad thing is that when they start having fatigue fractures, the owners will think that it was their own lack of welding skill, when in fact the design ia a disgrace. Look at the web sites of the several "seven" type manufacturers to see spaceframes which do address these points and in some cases are not very expensive. Just because something is written in a book, it does not follow that it is correct, or safe.
Also, beware of using stress levels, g forces etc, from any book used for track cars on the road. Admittedly, you don't thrash a car so hard on the road, but nowadays there are dreadful bumps and potholes to contend with. If in doubt, make it stronger. And, a track car may not be allowing a sufficient margin for fatigue, as it may only need a relatively short life.
As others are saying, it is not going to be easy. There are a lot of projects around, some quite successful, where they likely have not done all the stress calculations and got away with it. They probably take inspiration from other things that work, and to an extent you can do the same by looking at other designs. The web sites of kit car manufacturers may give some idea of what is possible, as many of those use spaceframes.
Thanks for the help.
Info like this is really helpful.
#12
Posted 17 December 2011 - 05:43 PM
As above, you can't just weld some tubes together on an 'it looks about right' basis.
That's why kit cars are popular as the stress analysis has already been done and establishes as OK.
Some on here know my views on 'flip fronts' and the fact that the added tubing on them has probably not been correctly stress analysed either (someone prove me wrong by pasting in the stress analysis calculations - if you can!).
#13
Posted 17 December 2011 - 05:47 PM
#14
Posted 17 December 2011 - 08:00 PM
Those who are not sure about what they are doing could perhaps copy, exactly, something that has been proved to work.
When I get around to building my turbo diesel Mini, I think I will need to strain gauge the modified structure. In the meantime, I would be very interested in knowing the peak loads on the rubber cones, shockers and suspension mounts, if anyone has ever measured them. I fully expect them to be somewhat higher than most people imagine. 5G peak is not unreasonable, fortunately the subframe feeds a lot of that directly to the largest mass, the engine, so it is not all reacted on the bulkhead cross member. But the engine mass is ahead of the "springs" and dampers, so there is a lot of dynamic load trying to rock the subframe, which is resisted by the rear mounts (which often fail) and the front teardrops. And so it goes on....
And some people think that neither inner nor outer wings are important.
When the Mini was designed, the technology did not exist to do a full stress analysis by computer, and not surprisingly, the early "orange box" prototypes suffered fatigue fractures, which is why the front subframe was introduced. It would be good if we could get access to a set of drawings for the Mini, and the appropriate software, to examine the actual stress distribution. That would settle a lot of arguments!
#15
Posted 17 December 2011 - 08:22 PM
The idea of 'designing' any sort of primary structure for a vehicle by guesswork is very unwise.
I saw some data once which showed that the torsional rigidity of a Mini body-shell is very high when compared to more modern cars. This, of course, may not equate into safety, but it does indicate a sort-of raw strength.
Coming from the aerospace design side of engineering, but having worked on high-performance vehicles and heavy commercial stuff as well, I cannot envisage driving something which has not been properly designed and stress analysed against established design loads, then fully tested for design compliance in a controlled development environment.
A competition-only vehicle may be different, but even race cars are now designed with specific design criteria in mind. In fact, my son works as a design consultant in motorsport engineering (currently working on a new petrol-electric hybrid le Mans car for a major manufacturer) and they use the CATIA CAD system, as used by Boeing, Lockheed, Airbus, etc., to carry out all the design and analysis.
Maybe coming from a high-integrity design background I'm biased, but how can a value be put on safe design. It's not something that can be guessed on a 'looks about right' basis. If it breaks you can end up dead!
1 user(s) are reading this topic
0 members, 1 guests, 0 anonymous users