looks like a great project so far, keep up the good work
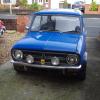
1275Gt - Its A Mini Adventure!
#31
Posted 01 February 2012 - 09:27 PM
#32
Posted 02 February 2012 - 08:55 AM
missed this one before I think. Great work you're doing. Well worth stripping things down to check, diff was an eye opener for me. I have already stripped mine and in good nick , but didn't know the pins wore that badly !! You are also a brave man cutting that much roof out in one go ! Have you tried the door and window again after the repair, which turned out very nicely by the way.
Keep progress comming,
Graham
#33
Posted 02 February 2012 - 10:19 AM
Graham,
It was a great surprise to see the diff pin worn that much. However, I think the previous owner was into Autotest which might explain it

I've held the windscreen up against the aperture to check consistency of the gap and it looks OK but not tried to fit it yet (too cold at the mo!). I also made sure to take plenty of measurements before cutting then re-checked several times while doing the repair. Also kept an eye on straightness. Will be re-fitting the door as soon as the temp gets above freezing!
Bob
PS
Love your thread!
#34
Posted 02 February 2012 - 11:59 AM
#35
Posted 03 February 2012 - 01:09 PM
#36
Posted 27 February 2012 - 07:55 PM
Thanks for the comment minima92 - I wish I could weld too!
Rich - I've had a look at your project and to be honest it puts mine in the shade. You really have set a standard to aspire for - its just awesome!
This update mainly shows work in the boot area. Firstly I repaired the boot hinge area. I would have liked to use a genuine full width repair panel but at £150 it was too much. Even a genuine hinge panel is £62. I eventually went for repro boot hing panel repair at £9.62 from Mini Sport (yes I am a tight wad!). This must be one of the best value repro panels - it fits perfectly! Here it is clamped into position for welding:
And welded in:
I reached the stage where I needed good access to the underside so I thought about desiging and building my own rollover jig. However, when I added up the cost of the steel it was looking like false economy comapred with buying one ready made. After a quick survey of whats available I eventually bought a flat-pack self assembly jig from MK2MANIA in Bolton for £110, little more than the cost of the steel - and its a proven design.
You have to weld it up yourself but this is pretty easy and within a couple of hours this is what I had:
In the photo above you can also see that I've cleaned up the front bulkhead and treated the bare steel with Phoskleen.
Its now so easy to get access to just about every part. You can even get into the interior by stepping through the windscreen or rear window openings!
Here I've tacked in a boot floor repair section. This is not a nice panel to fit - it took a lot of cutting, trimming and hammering to get the profiles to match. I had to use pop-rivets and screws to hold it together for tacking-in:
Because the boot floor steel is so thin I decided to do a lap joint. This meant I had to weld both sides. Here you can see how thin the material is:
I had decided to put the floor repair in first to give me a reference for fitting the various patches to the lower rear panel. In practise however, the boot floor section is too flimsy and I might have been better using a wooden batten or something jacked up to the boot floor level. The way I did it made it awkward to dress the welds:
And another repair round the side:
Next it was time to make and weld in new lip sections. The gap that was shown in the photo above has been filled with weld:
With a 5mm grinding disc you can reproduce the original radius between the lip and the panel:
Once the boot floor repair was welded in I trial fitted the valence closing panels:
Then it was time to check the fit of the subframe. Removing the radius arms allows you to easily lift and manoeuvre it. Fitting it this way was quite easy comapared to jacking it up from the bottom. I might use this method when I get to the final reassembly stage. I was quite relieved to find that the subframe fitted reasonably well - the left hand rear trunnion was out by about 1/4 hole diameter but this was easily drawn into position thanks to the elasticity of the bush.
I made up and fitted repair patches for the rear of the wheelarches (perfectionists and experts look away now!):
Also needed to fabricate the fuel tank restraint bracket. First some origami:
Then transfer to metal:
The last structural item in the boot area is the rear valence. Not much drama fitting this just a lot of drilling and welding - 8mm holes for plug welds in this case. I used quite a high power setting on the welder to make sure I got good penetration through 3 layers of metal. Its a Clarke 135TE and I had the power setting at 2 (always use this anyway) and the wire feed at MAX with the fine adjust set to 5/6.
So, now I have a solid rear end just needing some detailing with a carbide burr when I get one. The boot lid fits fine also.
I sent the front subframe to a local dipping & stripping company in Preston. Here's how the subframe looked when I got it back. I was very pleased with the condition and cleanliness of the stripped bits. At £54 it was well worth it:
Thats it for now, thanks for looking!
Edited by miniBrain, 17 August 2013 - 10:08 AM.
#37
Posted 27 February 2012 - 08:03 PM
lovely work you must be very pleased. Nicely ground back, just needs a lick of paint now !!
Graham
#38
Posted 27 February 2012 - 08:11 PM
Hi,
lovely work you must be very pleased. Nicely ground back, just needs a lick of paint now !!
Graham
Graham - it looks better in the photos, lol! Aaah paint - I dream about painting it - it just seems so so far away though!
#39
Posted 27 February 2012 - 10:11 PM
I'm going to need a rollover jig shortly too, and that one you've got looks really good for the money. :)
#40
Posted 27 February 2012 - 10:46 PM
#41
Posted 29 February 2012 - 09:58 PM
Thanks mini_in_progress. Had a look at your project - sooo familiar!
#42
Posted 02 March 2012 - 09:31 PM
#43
Posted 08 March 2012 - 07:46 PM
Thanks jmini22!
Update:
Added the outer sills. Have covered up the unused holes for the slinging brackets and jacking point since I've not fitted these.
Next was to repair the lower quarter panels that I cut out to get access to the heelboard, sill, etc. I made up new repair panels from the cut out sections with any rotten bits replaced with new steel and a new lip welded on. Trial fitting/trimming in progress:
Welded up and seams partly ground down:
I got three of these Garryson tungsten carbide burrs for use on tighter inside radii. Excellent tools but need to be used with care as they remove metal very quickly:
I don't think I'll ever be able to join unsupported panels seamlessly. Even though I took great care to clamp along the joint and tried to avoid excessive heat build up, I still ended up with some significant buckling/warping. I'll need about 2mm depth of filler along the joint line to get the correct panel contour.
After I repaired the roof section I needed to add a new drip rail since the new roof section did not have a drip rail fitted. So I set about removing the remnants of the old one.
I really don't know what this drip rail does. Its as if someone decided there wasn't enough moisture traps at the top as there are at the bottom and came up with the drip rail idea! Well I've now removed both drip rails and I'm not putting new ones back on. It does not seem to be a critical item so why store up more rust problems for the future?
Incidentally, until now I've been using a spot weld drill with the sprung centre point (shown on the left below) mainly because this is all I can buy locally. These are terrible to use - they skate about all over the place 'cause the sprung centre point just cannot bite into the metal to hold the drill in place. And the sprung point usually gets stuck as it is here.
I ordered one of the other types as shown on the right. This is a bit like a milling cutter but with a pip in the centre. These are much easier to use, cheaper and cut cleanly.
I've now got to get on with a lot of detail work mainly on the interior. After that I'll get back to the front end and hopefully the next update will show the scuttle, wings and front panel in place.
Thanks for looking!
Edited by miniBrain, 17 August 2013 - 10:09 AM.
#44
Posted 23 March 2012 - 08:32 PM
Hi Folks,
In this update I had hoped to show you front end completed but when I trial fitted the front panel I realised that I had the wrong one. I had the pre-76 type for a solid mounted subframe but my car is a 77 with rubber-mounts. So here's just a small update while I wait for the correct front panel.
I've seen a couple of people do this, so not wanting to be left out, I removed the steering column bracket to have a look underneath and sort any rust problems lurking behind. Not much drama here – just some surface rust to deal with. The worst damage were the holes I made during removal!
I gave the roof repair its first skim of filler. Not bad but more work to do, especially at the gutter joint:
Refurbished the radius arms:
Prepared the underside for paint – a very messy and laborious task! Here's what I did:
- Use twisted wire brush to remove bulk of tarry underseal & loose paint.
- Clean off remainder of underseal using white spirit (from a hand spray bottle) and steel scourer, wiping off with paper towels.
- When dry, went over with a Scotch Pad.
- Wiped down with panel wipe degreaser.
- Repeated above a couple of times until completely free from any oily residue, loose paint, etc.
I could then apply epoxy mastic as per instructions (I used a foam roller mainly):
I'm quite pleased with this epoxy mastic – its sticks well, its tough (I've tested it with a twisted wire brush), and its flexible. Of course I'll only know how well it performs in practise in about 5 years.
Lastly, I've fixed the scuttle panel in position with nuts & bolts. I've set it so that the windscreen aperture is 415mm top to bottom, mainly because an internet search showed that's what most folk have or aim for. And also because the height of the glass is 394mm leaving a gap of (415-394)/2 = 10.5mm which is about the same as the inner width of the rubber seal. So should be a snug fit with some sealing compound.
Thanks for looking!
Edited by miniBrain, 17 August 2013 - 10:10 AM.
#45
Posted 23 March 2012 - 09:24 PM
Keep it going
Hugh
1 user(s) are reading this topic
0 members, 1 guests, 0 anonymous users