
Smooth seams
Started by
minilady
, Feb 05 2006 11:51 PM
9 replies to this topic
#1
Posted 05 February 2006 - 11:51 PM
You know those ugly seams where the wings join the scuttle and front panel...
Has anyone tried filling these in to make it all nice and smooth?
Or would it just look silly?
Has anyone tried filling these in to make it all nice and smooth?
Or would it just look silly?
#2
Posted 06 February 2006 - 09:17 AM
lots of people fill them but with conventional filler it will crack and will rot out the join in no time! the only true way to do so is to lead fill and this apparently is a VERY hard thing to master!
#3
Posted 06 February 2006 - 09:23 AM
would it not be possible to will them with a weld then grind it smooth?
#4
Posted 06 February 2006 - 09:54 AM
Yes, I was planning to weld them. I don't trust filler where flexing is possible.
I didn't think of lead-filling, that must be like soldering?
I didn't think of lead-filling, that must be like soldering?
#5
Posted 06 February 2006 - 09:58 AM
I didn't think of lead-filling, that must be like soldering?
Not quite, as far as I know (and I could be wrong) It involves some nice molten lead which you wipe onto the surface to make it nice and smooth.
#6
Posted 06 February 2006 - 11:23 AM
i used fibreglass and it works a treat, didnt even crack when i hit a curb and damaged the a panel! looks neater also and stops the water from collecting an d rotting the panels!
#7
Posted 06 February 2006 - 05:42 PM
mine was done when the new wings and front panel were fitted, i don't know how, so i hope it lasts.
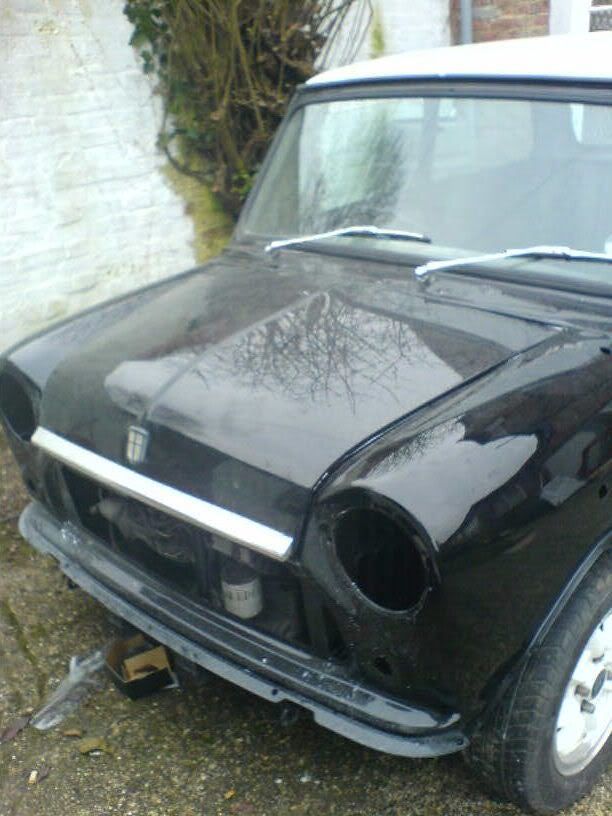
#8
Posted 07 February 2006 - 12:21 PM
Thanx for the replies. Conclusions so far:
- It's not a daft idea to fill seams
- Molten lead, weld or fibreglass filler are all ok.
I think I'll weld them, it's less work than filling, sanding, re-filling, smoothing etc. and you don't have to wait weeks for the filler to dry
)
- It's not a daft idea to fill seams
- Molten lead, weld or fibreglass filler are all ok.
I think I'll weld them, it's less work than filling, sanding, re-filling, smoothing etc. and you don't have to wait weeks for the filler to dry

#9
Posted 07 February 2006 - 12:41 PM
hi all
this should be done with a product call stickaflex or a suitible flexible panel sealant
(pushing the material into the joint) and leaving it just under flush with the bodywork to keep the original look but sealing the joint .and if the wing needs replacing at some point will not need a new scuttle at the same time IE dont weld them!!!!
or yes lead loading the seam is a very good method very popular with restorers
of the earlier mk s of mini
NO FILLER NO FIBREGLASS NO WELDING SHOULD BE DONE TO THIS AREA
to everyone in the know this is not a good look
any advice needed on anything mini msn me [email protected]
thaks eddie
this should be done with a product call stickaflex or a suitible flexible panel sealant
(pushing the material into the joint) and leaving it just under flush with the bodywork to keep the original look but sealing the joint .and if the wing needs replacing at some point will not need a new scuttle at the same time IE dont weld them!!!!
or yes lead loading the seam is a very good method very popular with restorers
of the earlier mk s of mini
NO FILLER NO FIBREGLASS NO WELDING SHOULD BE DONE TO THIS AREA
to everyone in the know this is not a good look
any advice needed on anything mini msn me [email protected]
thaks eddie
Attached Files
#10
Posted 07 February 2006 - 03:57 PM
Lead loading is not that hard..
and provides a flexible and removeable method.
I have done this many times on small pedal cars i have restored and on full size cars, E types, Rolls Royce etc..
If you want to go down the lead route.
you need body solder (lead)
Tallow (flux )
Tinning paste
and a paddle to push the lead around
You can get a basic kit from frost £28
Clicky
and a heat gun (paint stripper)
have a look at the restoration section of my site clicky pic below
you will see a shot of a pedal car standing beside an E type if you look at the etype rear wing you see the different colours of the metal, thats lead used to get the final shape.
Basically wave the heat gun between the panel and the lead keep touching the lead on the panel and when it sticks push a bit onto the panel..
Warm the lead and push it into shape with the paddle..
thats basically it
if you want more info/pics let me know
cheers
shaz
and provides a flexible and removeable method.
I have done this many times on small pedal cars i have restored and on full size cars, E types, Rolls Royce etc..
If you want to go down the lead route.
you need body solder (lead)
Tallow (flux )
Tinning paste
and a paddle to push the lead around
You can get a basic kit from frost £28
Clicky
and a heat gun (paint stripper)
have a look at the restoration section of my site clicky pic below
you will see a shot of a pedal car standing beside an E type if you look at the etype rear wing you see the different colours of the metal, thats lead used to get the final shape.
Basically wave the heat gun between the panel and the lead keep touching the lead on the panel and when it sticks push a bit onto the panel..
Warm the lead and push it into shape with the paddle..
thats basically it
if you want more info/pics let me know
cheers
shaz
Attached Files
1 user(s) are reading this topic
0 members, 1 guests, 0 anonymous users