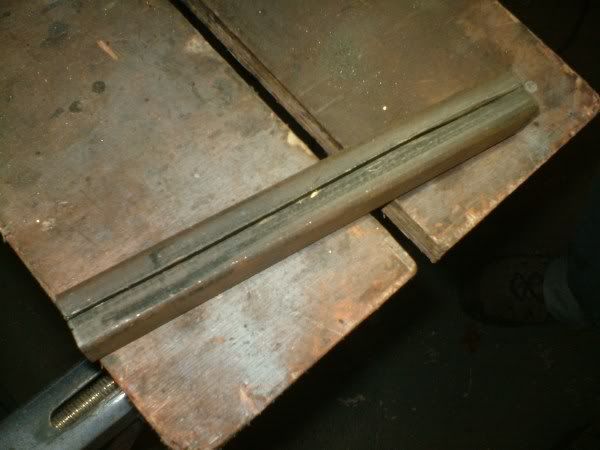
Measure 2cm lengths
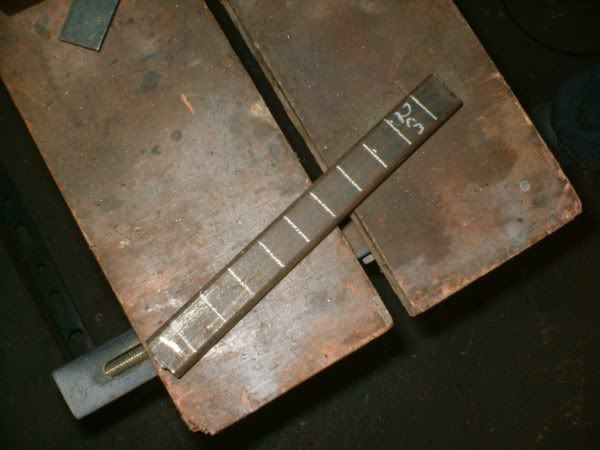
Cut the box section and then mark centre for a hole
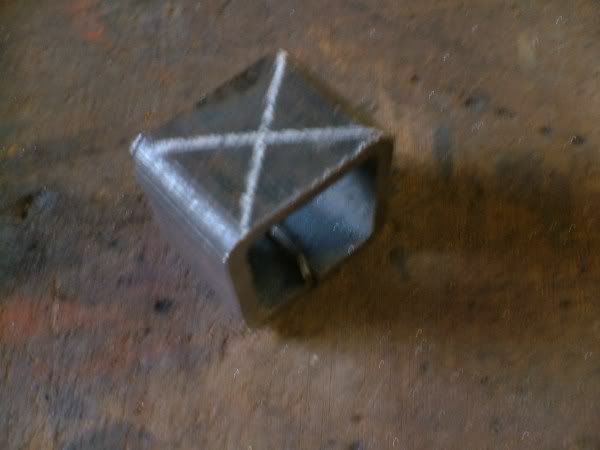
Drill a 6.5 mm hole in the centre
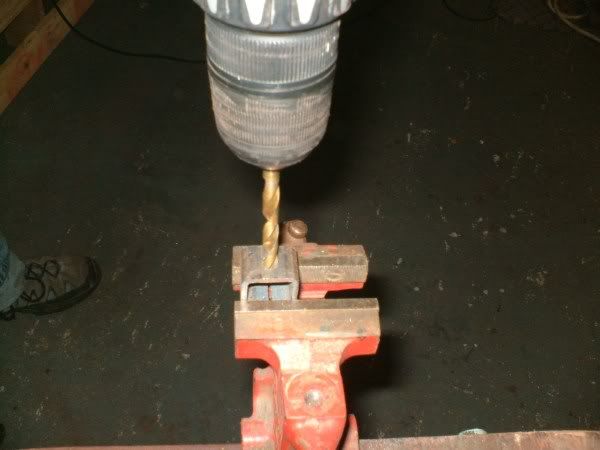
Then Drill at an angle inline with the slot, so the bolt can be inserted
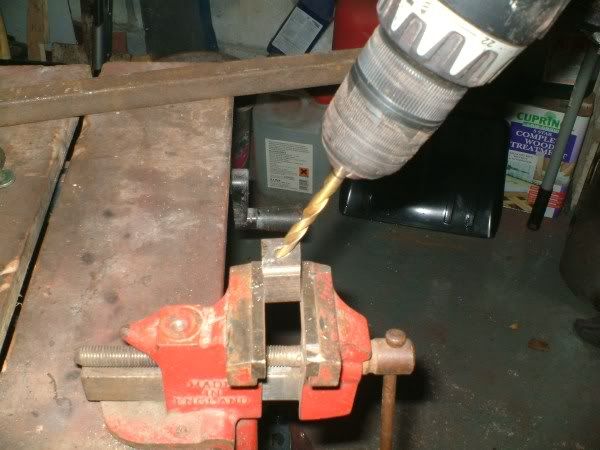
Cut a groove in a bolt for the metal to slot in
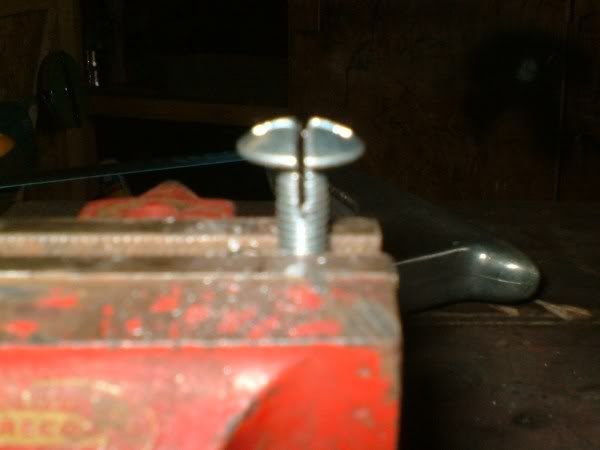
mark out a 20mm wide by 25mm long on a piece of metal
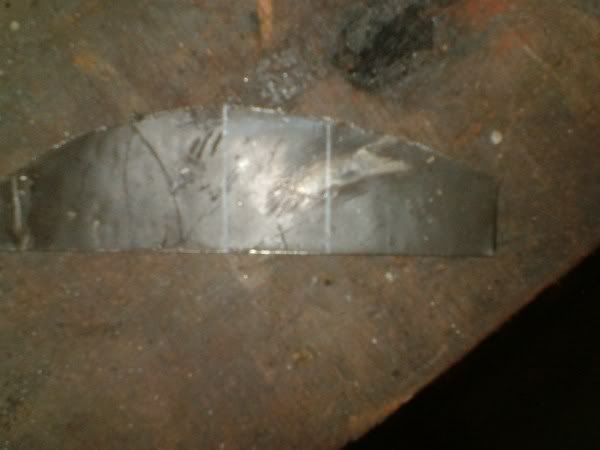
chop off the bolt head and cut metal
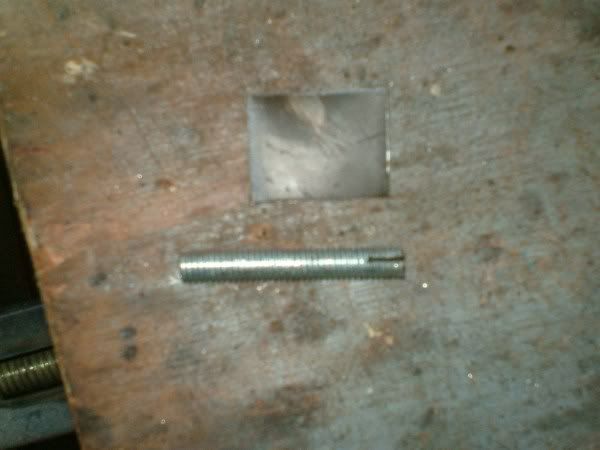
Put the metal in the slot then weld together
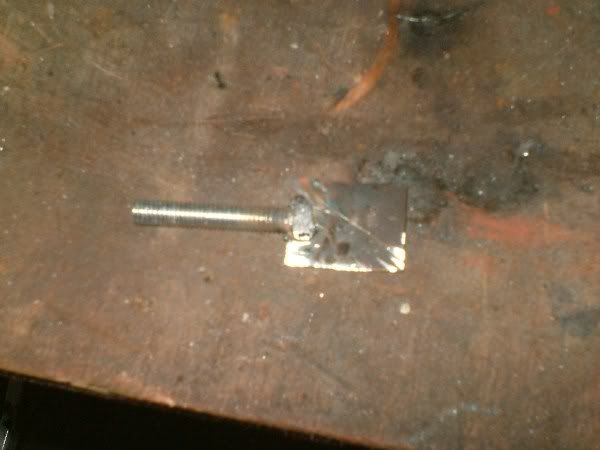
file the bolt and drill a 6.5mm hole in the metal for the round bar to slot in
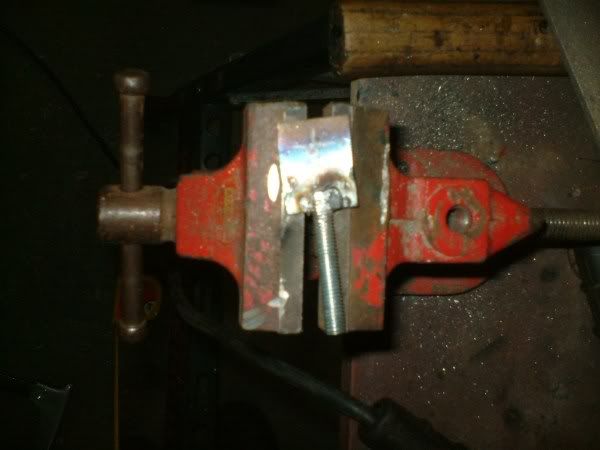
Cut 6mm round bar or a bolt about 2cm long
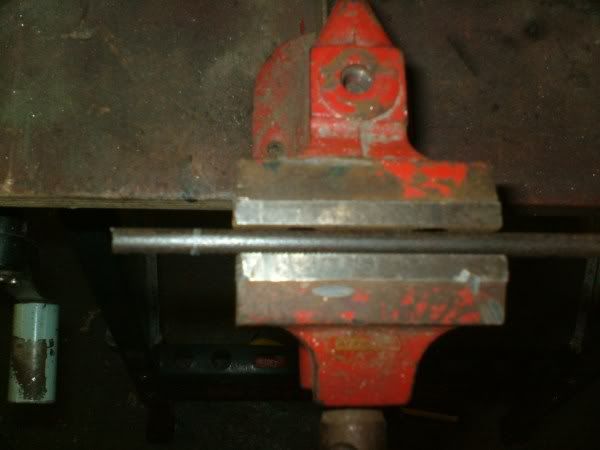
Fix together
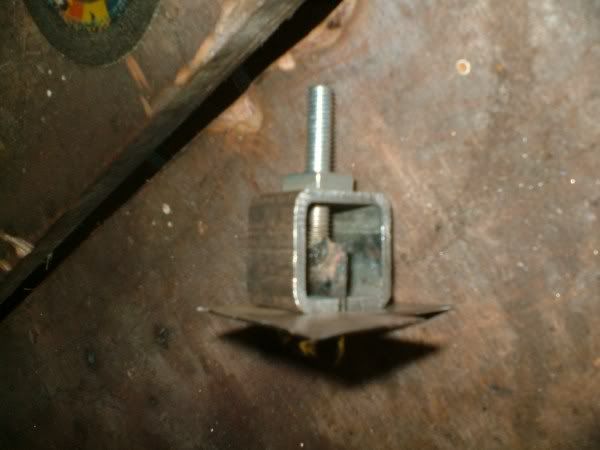
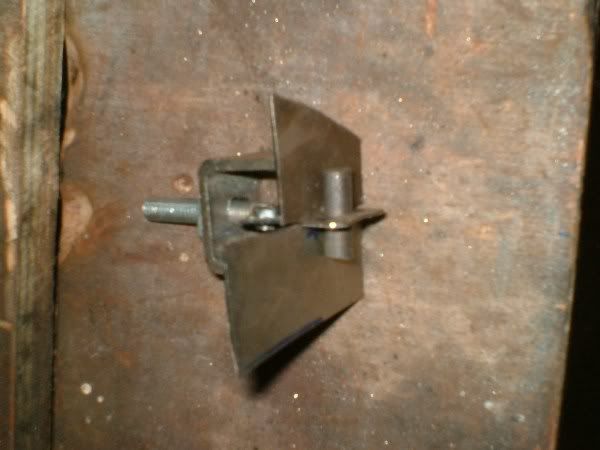

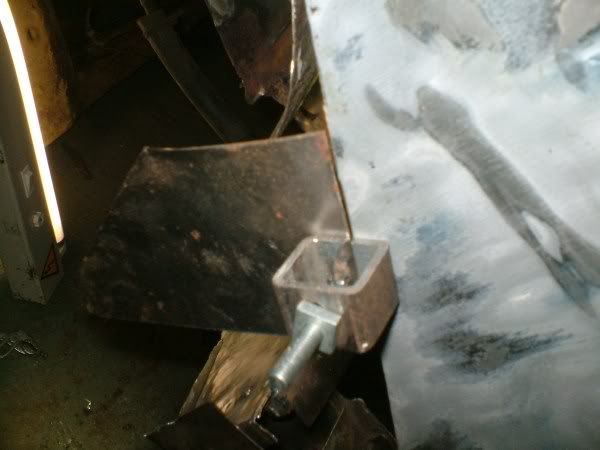
Alex