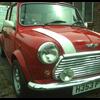
Fiber Glass. How Do You It And What Do You Need?
Started by
E-Tizzle
, Sep 04 2011 06:56 PM
10 replies to this topic
#1
Posted 04 September 2011 - 06:56 PM
does anyone one here make their own fiberglass panels and projects.
if so, how do you do it.
im interested in making some of my own panels for my car.
is it hard to get right? and is there anything you need other than a fiberglassing kit?
thanks
if so, how do you do it.
im interested in making some of my own panels for my car.
is it hard to get right? and is there anything you need other than a fiberglassing kit?
thanks
#2
Posted 04 September 2011 - 07:26 PM
I am also interested in doing some custom panels using fibre glass hope someone can instruct we
#3
Posted 05 September 2011 - 12:44 PM
The big part is going to be making the mould. In principle it's not hard but in practice it's damn fiddly on something as big as a panel.
Basically assuming you have a mould.
You apply release wax to the mould. You need to use proper stuff or you'll have trouble at the next step. It needs to be buffed to a shine.
Apply PVA release agent (poly-vinyl-alcohol). It's blue and looks and smells a bit like anti-freeze. You can paint or spray it on. If the wax isn't applied correctly or has any silicone in it the PVA will just fish-eye. Let it dry.
Now mix the correct amount of catalyst with the correct amount of gel-coat and stir. Brush the gel-coat on to the PVA trying to get an even coat and max 1mm thick. The gel coat will take days to completely cure on the exposed side so once it's gone hard enough that it's tacky but none comes away on your finger if you touch it you can carry on.
Mix a batch of resin and catalyst. Brush a coat of resin on the gel-coat and then apply a layer of chopped-strand-matting (CSM). Apply more resin and roller/stipple it in until the matting is completely soaked. Let it mostly cure and then repeat. CSM comes in different weights which roughly equates to thicknesses so how many layers you want depends on what CSM you are using and how thick you need the panel to be (whether it's structural or not). Large areas might be more than you can cover within the set-time of a batch of resin so you might need to work production line fashion - I sometimes set out several sets of catalyst and resin in seperate cups/tubs so that as I'm finishing one set I can just pour the next set together, mix and carry on rather than having to worry about proportions. Large areas might need several sections of CSM to be overlapped which can need thinking about/planning. Large panels might need stiffeners. Let it cure for at least 24 hours when you think it's finished.
Once cured stick a plastic scraper between the mould/form and your new bit of fibreglass and seperate them. The PVA will mostly be stuck to your new piece but it's water soluble so wash it off.
In principle it's dead easy but in practice it can get tricksy and you don't want to be working out a solution to a problem whilst you've got a batch of resin going hard in a tub and on your brush. There are lots of books on the subject.
Moulds can be fibreglass too so to make a GRP bonnet for example you would want an original bonnet. Follow the above process to make a mould on the outside of it. Repeat once again to make your GRP bonnet on the inside of the mould you made. With a bit of care you should be able to make several bonnets from one mould.
Iain
Basically assuming you have a mould.
You apply release wax to the mould. You need to use proper stuff or you'll have trouble at the next step. It needs to be buffed to a shine.
Apply PVA release agent (poly-vinyl-alcohol). It's blue and looks and smells a bit like anti-freeze. You can paint or spray it on. If the wax isn't applied correctly or has any silicone in it the PVA will just fish-eye. Let it dry.
Now mix the correct amount of catalyst with the correct amount of gel-coat and stir. Brush the gel-coat on to the PVA trying to get an even coat and max 1mm thick. The gel coat will take days to completely cure on the exposed side so once it's gone hard enough that it's tacky but none comes away on your finger if you touch it you can carry on.
Mix a batch of resin and catalyst. Brush a coat of resin on the gel-coat and then apply a layer of chopped-strand-matting (CSM). Apply more resin and roller/stipple it in until the matting is completely soaked. Let it mostly cure and then repeat. CSM comes in different weights which roughly equates to thicknesses so how many layers you want depends on what CSM you are using and how thick you need the panel to be (whether it's structural or not). Large areas might be more than you can cover within the set-time of a batch of resin so you might need to work production line fashion - I sometimes set out several sets of catalyst and resin in seperate cups/tubs so that as I'm finishing one set I can just pour the next set together, mix and carry on rather than having to worry about proportions. Large areas might need several sections of CSM to be overlapped which can need thinking about/planning. Large panels might need stiffeners. Let it cure for at least 24 hours when you think it's finished.
Once cured stick a plastic scraper between the mould/form and your new bit of fibreglass and seperate them. The PVA will mostly be stuck to your new piece but it's water soluble so wash it off.
In principle it's dead easy but in practice it can get tricksy and you don't want to be working out a solution to a problem whilst you've got a batch of resin going hard in a tub and on your brush. There are lots of books on the subject.
Moulds can be fibreglass too so to make a GRP bonnet for example you would want an original bonnet. Follow the above process to make a mould on the outside of it. Repeat once again to make your GRP bonnet on the inside of the mould you made. With a bit of care you should be able to make several bonnets from one mould.
Iain
#4
Posted 05 September 2011 - 01:15 PM
Sorry - didn't include a shopping list. This is the absolute basics.
Natural bristle paintbrushes (plastic bristles will likley melt in the acetone).
Gel-coat.
Resin (generally polyester).
PVA mould release
Release wax
Acetone (brush cleaning).
Chopped strand matting.
Catalyst (usually supplied as a matter of course with the gel-coat and the resin).
Walk into a shop with this list though and they'll hit you with a load more questions as there are umpteen different types of resin and gel-coat, numerous waxes etc. so find somewhere friendly that will talk to you and can tell you which resin/gel is best for what and then you can make your own decision.
Iain
Natural bristle paintbrushes (plastic bristles will likley melt in the acetone).
Gel-coat.
Resin (generally polyester).
PVA mould release
Release wax
Acetone (brush cleaning).
Chopped strand matting.
Catalyst (usually supplied as a matter of course with the gel-coat and the resin).
Walk into a shop with this list though and they'll hit you with a load more questions as there are umpteen different types of resin and gel-coat, numerous waxes etc. so find somewhere friendly that will talk to you and can tell you which resin/gel is best for what and then you can make your own decision.
Iain
#5
Posted 05 September 2011 - 01:28 PM
Good advice from Iain,
All you really need is a paint brush and a decent pair of scissors to get started. Gel coat provides a nice finish and fills sharp corners, so isn't essential to get you started. You can also use wax polish as a release agent and make moulds out of anything that's stiff enough to take a jab from a stippling brush - plasticine it really useful for getting rid of the sharp corners that glass mat doesn't like.
It's not so pleasant to work once it's cured, wear a face mask, goggles and cover up when cutting and sanding it.
http://www.ecfibreglasssupplies.co.uk/
All you really need is a paint brush and a decent pair of scissors to get started. Gel coat provides a nice finish and fills sharp corners, so isn't essential to get you started. You can also use wax polish as a release agent and make moulds out of anything that's stiff enough to take a jab from a stippling brush - plasticine it really useful for getting rid of the sharp corners that glass mat doesn't like.
It's not so pleasant to work once it's cured, wear a face mask, goggles and cover up when cutting and sanding it.
http://www.ecfibreglasssupplies.co.uk/
#7
Posted 05 September 2011 - 03:59 PM
If i bought a fibre glass front end and boded brackets in is it the same priciple but without using realeasing agents
#8
Posted 05 September 2011 - 04:24 PM
thanks for your great advise!
iain - you say you can make a mould out of fiberglass, this was what i was thinking of doing so im glad youve said that, but how thick would i need to make it for it to be strong enough. i dont want it flopping around when im trying to apply the new fibreglass? would 1 layer be enough to stay rigid whilst appyling the new fg?
also thats a great website minimender thanks
oh yeah, i cant get the notification emails to work either, i havent recieved and email since the website changed. is there a problem with it?
thanks a lot
elliot
iain - you say you can make a mould out of fiberglass, this was what i was thinking of doing so im glad youve said that, but how thick would i need to make it for it to be strong enough. i dont want it flopping around when im trying to apply the new fibreglass? would 1 layer be enough to stay rigid whilst appyling the new fg?
also thats a great website minimender thanks
oh yeah, i cant get the notification emails to work either, i havent recieved and email since the website changed. is there a problem with it?
thanks a lot
elliot
#9
Posted 05 September 2011 - 04:26 PM
also ethel have you used that company, would you recommend them, are they reasonable?
cheers
cheers
#10
Posted 06 September 2011 - 09:07 PM
One layer of fibreglass won't be strong enough for a mould (or anything much really) two minimum for the panels themselves but more for the forms ideally (and this also depends on the weight of CSM used). You would really want some sort of frame to keep your form rigid. Once the gel-coat and the first layer of CSM has been laid-up you can add some stiffeners to the rear of the mould. Lengths of paper rope or foam strips are good and once you laminate more layers over the top they effectively become box sections (also works well on the panel). Wooden/metal frames are also good on the form stage.
Iain
Iain
#11
Posted 08 September 2011 - 08:40 AM
oh thanks i didnt know you could put supports in, sounds like a good idea.
cheers
cheers
1 user(s) are reading this topic
0 members, 1 guests, 0 anonymous users