With all the panels test fitted I began to fit the scuttle panel. Again Heritage panel, HMP441001. I cleaned all of the edges where I would be spot welding down to bare metal and primed with zinc rich weld through primer. Then aligned and put a few spot welds in and rechecked the fit.
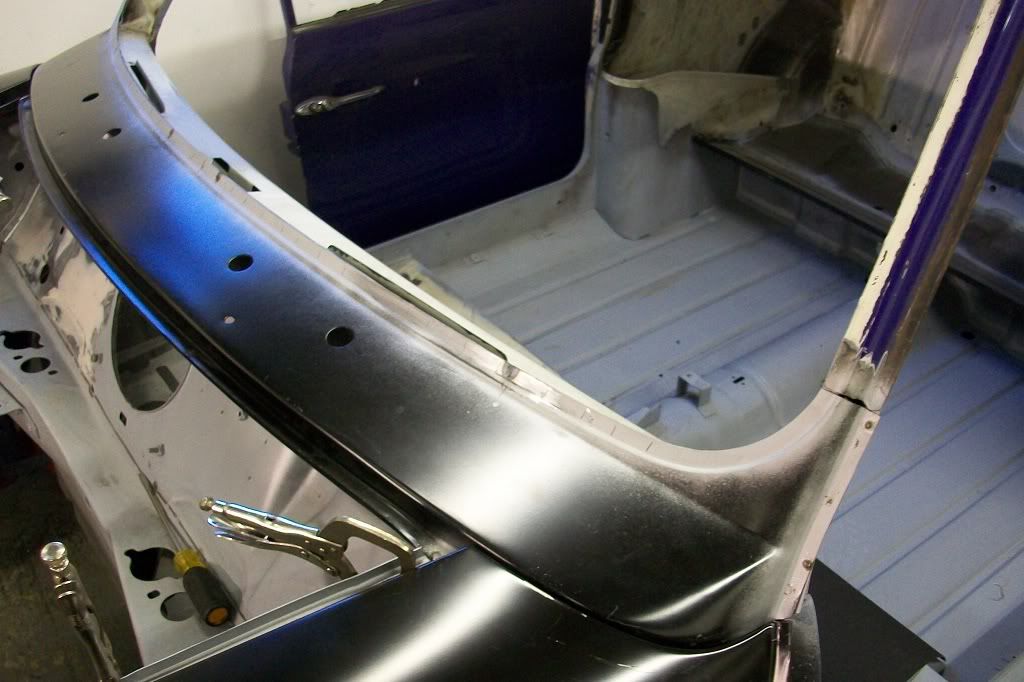
Then fully spot welded.
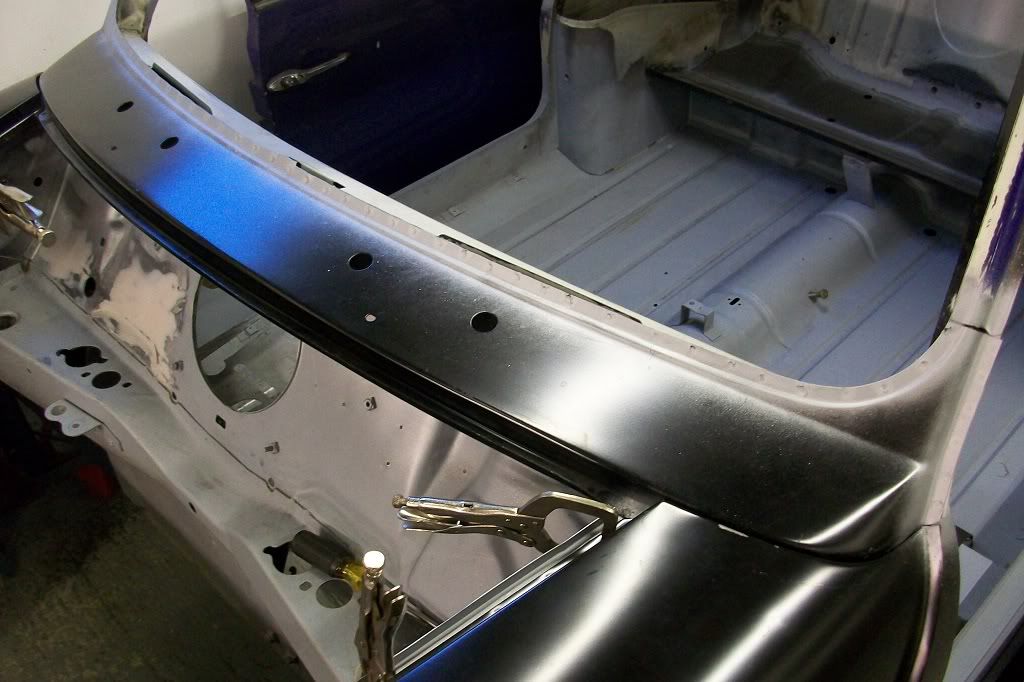
Mig welded the joint in both pillars and ground down.
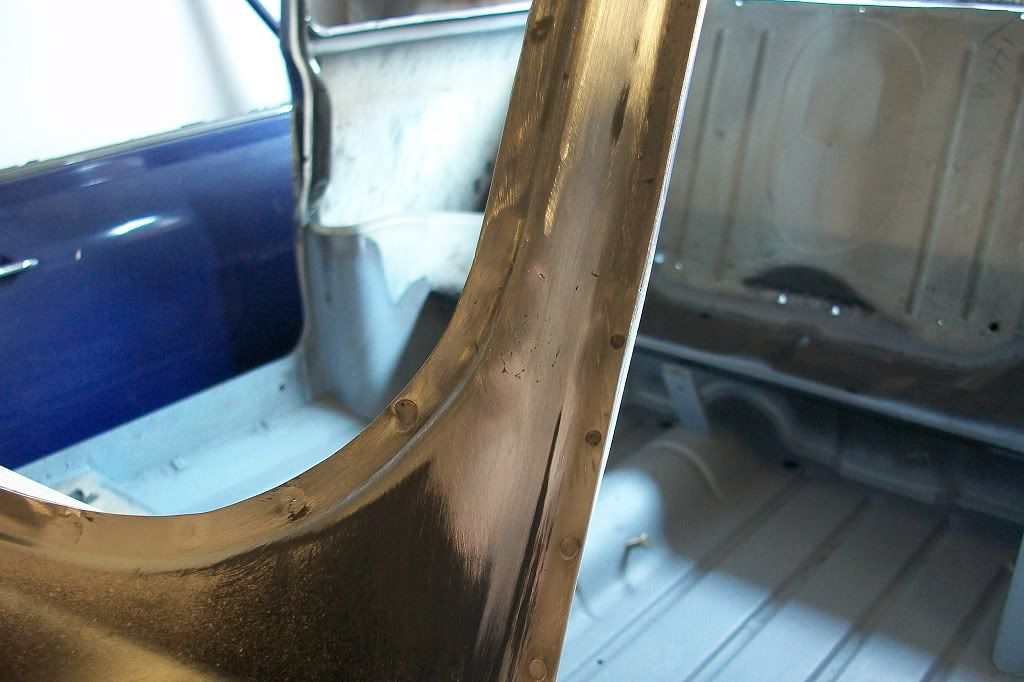
Just needed a slight skim of filler to level up.
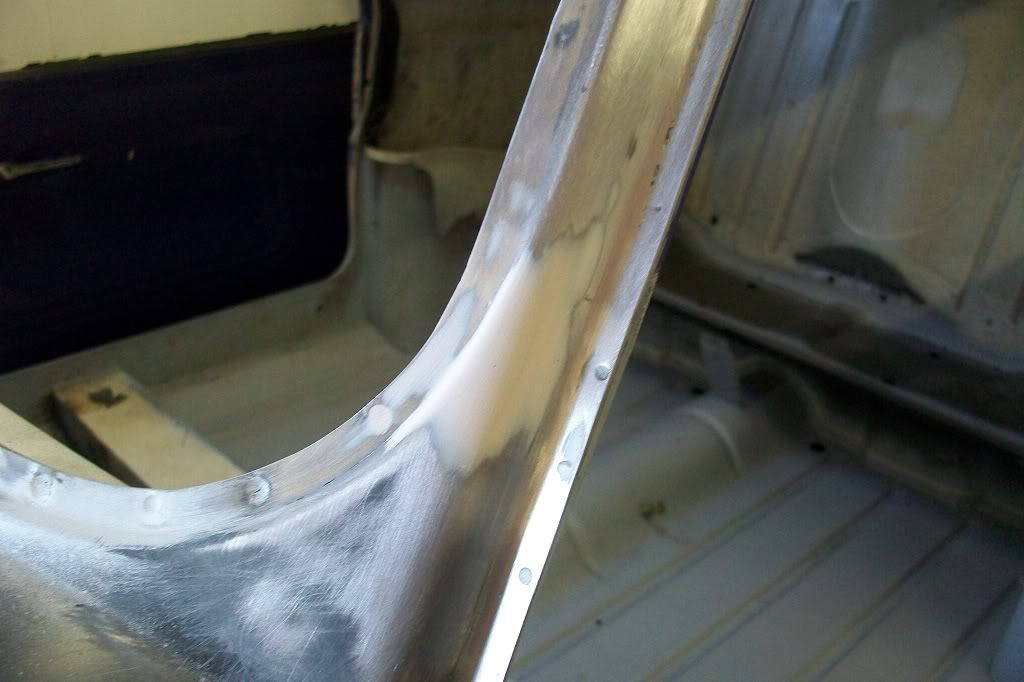
Next I test fitted each wing in turn to get the gaps at the scuttle right and to pull the wings in a bit at the top corner of the bonnet. This took about an hour per side to get them to a point where I was happy with them.
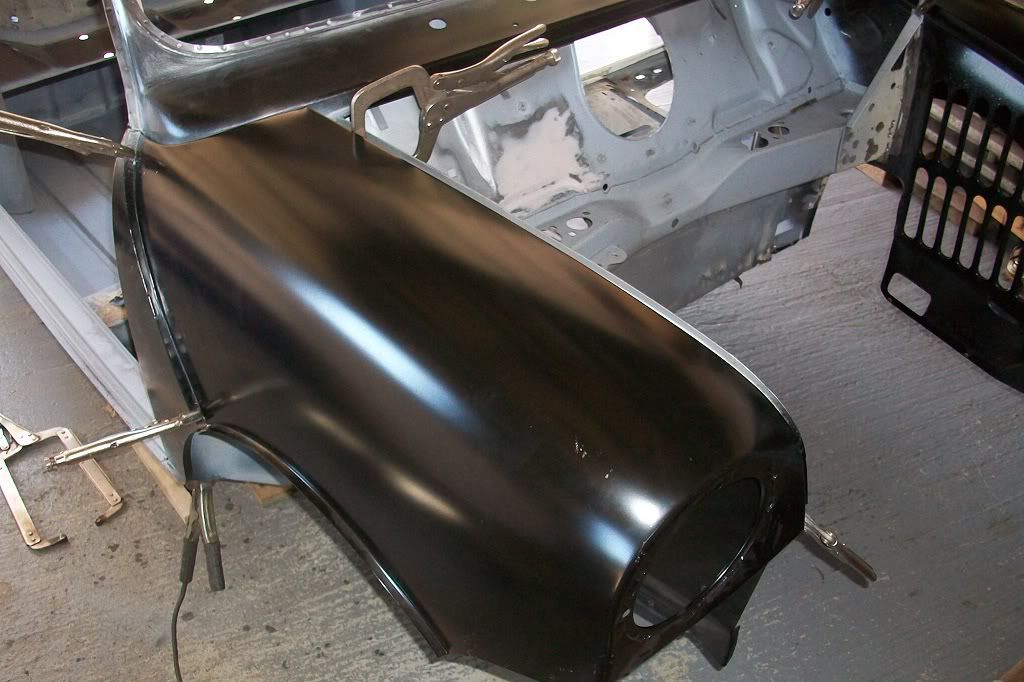
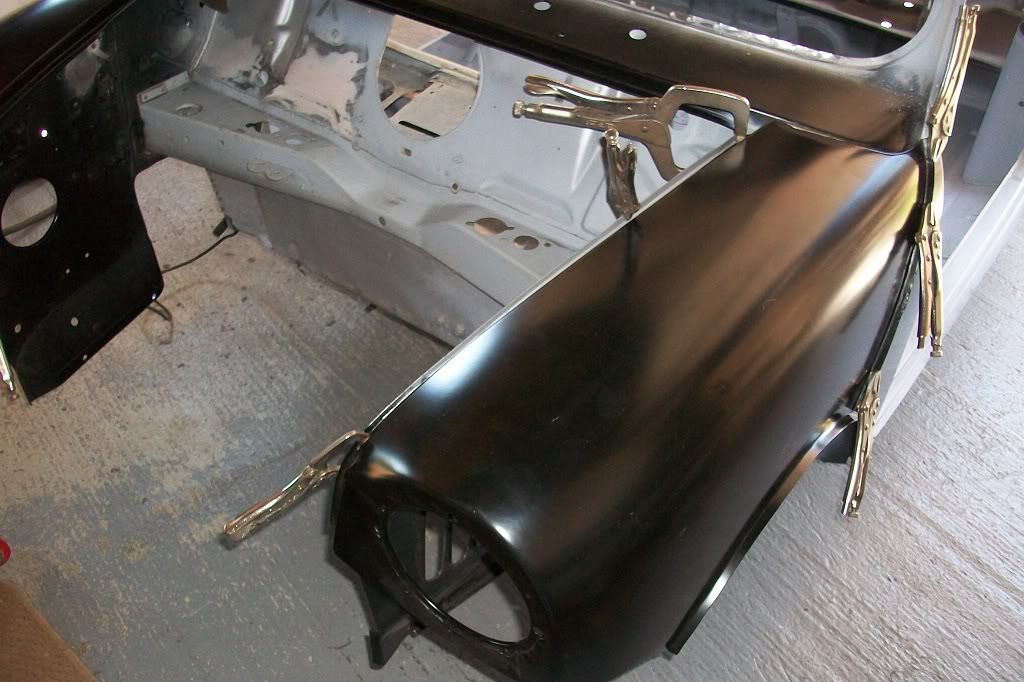
This Is how the gaps turned out before fitting the wings.
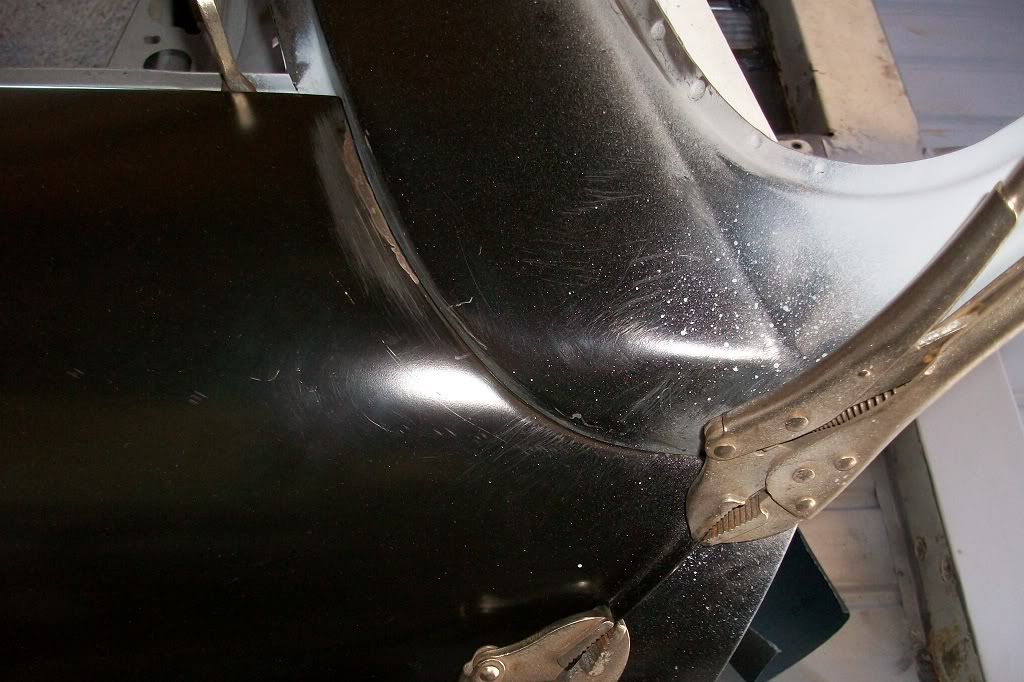
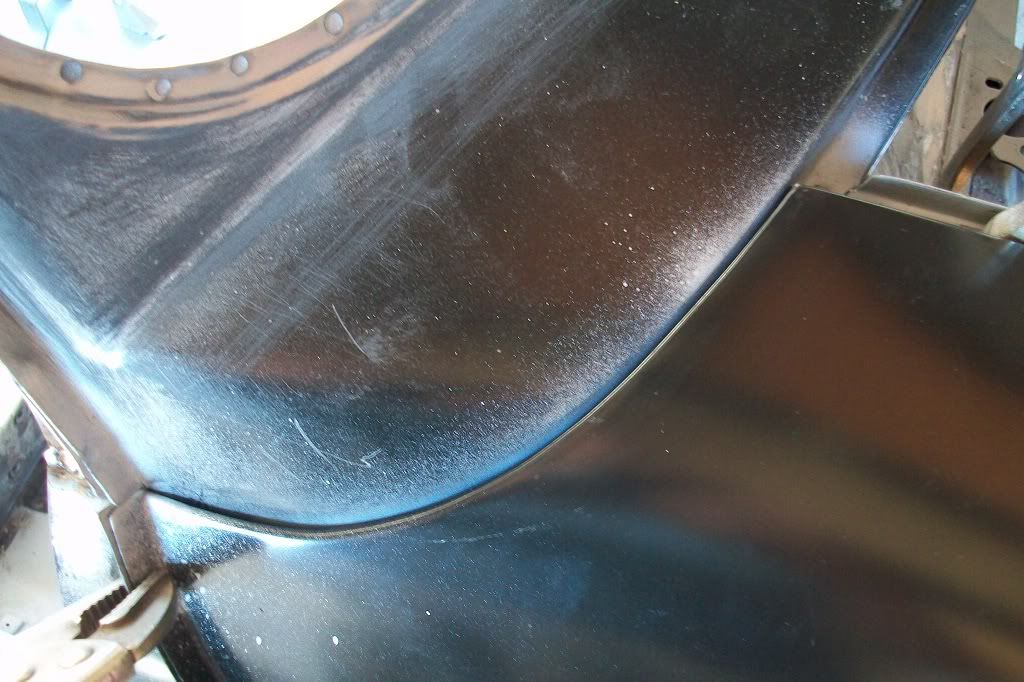
Next job before fitting the wings and whilst I still had easy access to both sides, was to fill some unrequired holes and replace the later bonnet stand bracket with the earlier type. I marked any hole I wasn't sure about although I haven't blanked them all off. These were things I didn't do on my previous project and have regretted since.
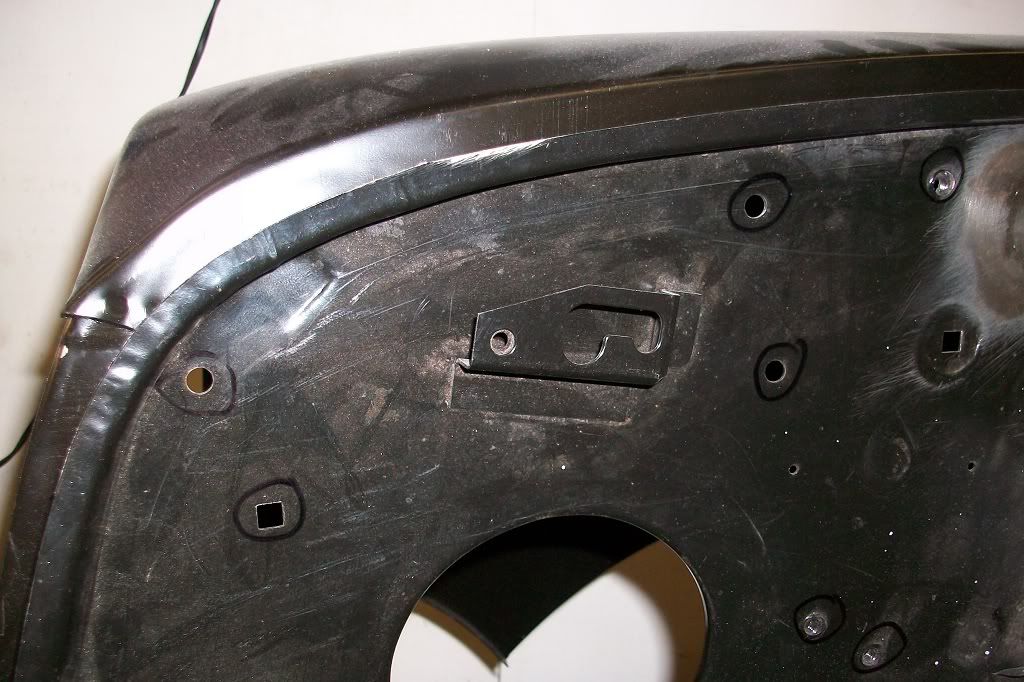
A template was made of the bracket position from the old inner wing and then the bracket was removed, cleaned and spot welded back onto the new wing.
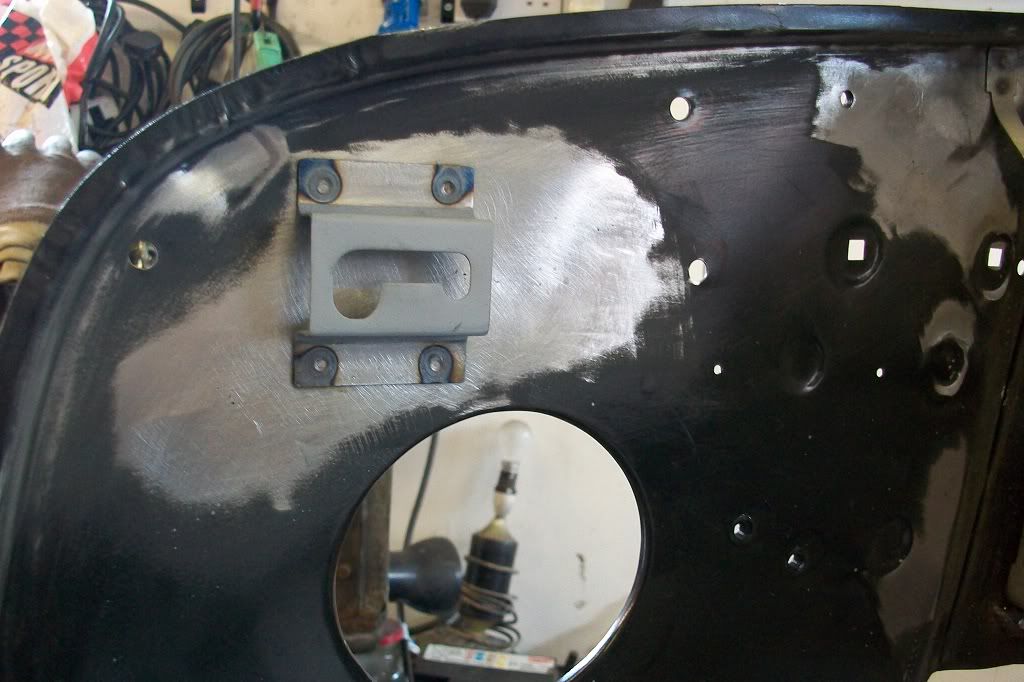
Some holes welded.
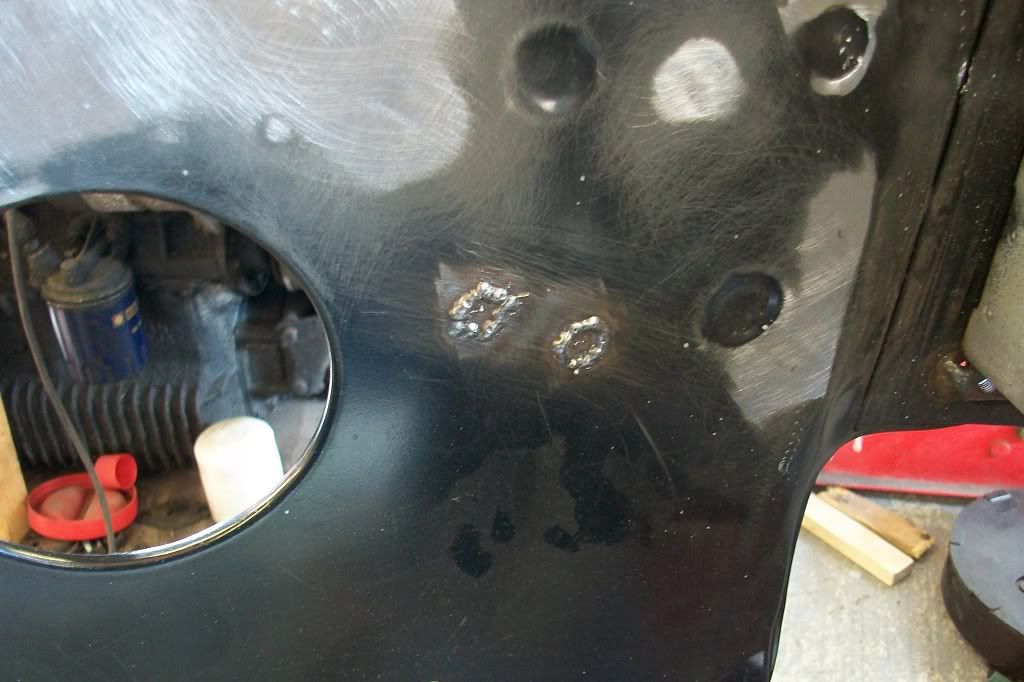
The finished inner wing with correct bracket and holes welded up. I also removed the engine ECU bracket supports (see pictures from last post) that looked like small looped handles as these were also not needed. You can also see the wiring harness tag that I added as copied from the old wing.
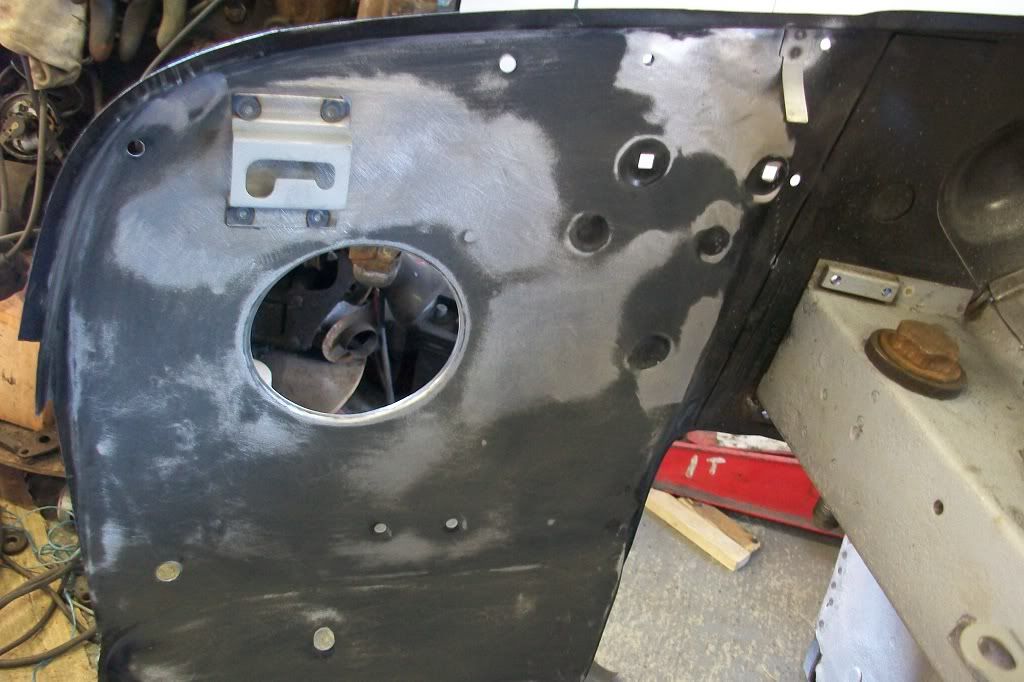
Thats it again so thanks for looking.
Edited by minifcd, 02 January 2012 - 05:56 PM.