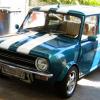
#1
Posted 15 August 2011 - 08:03 AM
#2
Posted 15 August 2011 - 09:18 AM
- either you'll have to tap new thread (which will have to be somewhat bigger than before, like 3/8" -> 1/2"),
- or insert a Helicoil
I personally think the latter is best...
Edited by yellowmonster, 15 August 2011 - 09:20 AM.
#3
Posted 15 August 2011 - 10:42 AM
#4
Posted 15 August 2011 - 11:51 AM
Edited by bmcecosse, 15 August 2011 - 11:52 AM.
#5
Posted 15 August 2011 - 07:32 PM

#6
Posted 15 August 2011 - 09:19 PM
#7
Posted 15 August 2011 - 09:24 PM
what if I just treat it as a 9 stud and ignore the fact that I have 2 extra studs in the block? what's the real benefit of having two extra studs?
#8
Posted 15 August 2011 - 09:31 PM
Yes that's the front stud, the weakest one. Did you torque in the correct order? This stud should be torqued last so it's not pulling the head down as it's tightened.
Yes I torqued the 9 main studs.. then left the two extra studs for last... it didn't even feel as if it was very tight when I heard a click that wasn't the click from the wrench... I first thought the bolt snapped but then slowly turned it out to find that thread pulled out the block...
I have another 11 stud block that's probably in better shape than this one... but I really don't want to have to rebuild the engine.... Again... this one's been standing for a few years... but only did around 100km before it stood...
#9
Posted 15 August 2011 - 10:17 PM
#10
Posted 15 August 2011 - 10:28 PM
You will probably find that the existing hole is already right through into the water gallery, so simple not fitting that bolt would not be possible in such a case.
Just drill, tap and Heli-Coil, then fit the correct bolt - if necessary with a bit of instant gasket sealer if it's through to the water way. Torque it to 25 lb.ft and the job has been done properly and is not 'bodged' in any way.
#11
Posted 15 August 2011 - 10:39 PM
#12
Posted 16 August 2011 - 02:40 PM
What's the best way(with the engine still in the car) to drill and tap straight?
#13
Posted 16 August 2011 - 10:00 PM
#14
Posted 16 August 2011 - 10:12 PM
Any reason why you can't glue a stud in with loctite and use a nut? Would a rocker pedestal stud do?
I have a thread maker for high heat application but I'm not sure what kind of torque pressure it will hold...
#15
Posted 16 August 2011 - 10:51 PM
1 user(s) are reading this topic
0 members, 1 guests, 0 anonymous users