
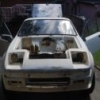
Project Zippy - Mk1 1981 Midas Project.
#61
Posted 18 January 2012 - 12:17 PM

#62
Posted 22 January 2012 - 04:11 PM

The sides, sills and footwells were covered in the remains of some horrid sort of foam cloth, which had obviously deteriorated over the 11 or so years of standing idle. Did I have a suitable power tool to remove it? No. So out with the wallpaper scraper it was. It took 2 hours. Still, a pint of Dr Pepper, several Jaffa Cakes and a lot of scraping and swearing later, it was all off. And in the footwells. So I emptied the Manroom vacuum and sucked up everything I possibly could from the floor. All except that large piece of underlay which had been stuck to the bottom of the dash shelf with what appeared to be underseal. It was disgusting...
I also took the time to properly remove that horrible old aerial which ran through the sill into the wiring loom. I cut the old stub off so it would pull through more easily and threw it all away, along with the doubtless useless by now speaker wires.
I then dug out the "new" Mini handbrake I'd bought from Ebay. The plan was to simply swap over the connection on the back but when I put them side-by-side, I realised that the brackets and the holes drilled to mount them were totally different. I really didn't want to go back to using the nasty old handbrake as it had now usable internal release mechanism - the missing button was a good indicator of this! I also don't know what the handbrake lever was from - I am guessing something like an Allegro so I am not planning to try tracking a direct replacement down.
After a bit of lateral thinking and measuring, I realised I could use one of the mounting bolts by making a bracket and mount the rear end by drilling one hole and using a 1 1/4" spacer. I cut the end off the bottom mounting bracket I had for an old A-series weather shield and smacked it about a bit in the vice until it was the right shape. What to use for a spacer? I had an old chrome steering column drop-bracket in my "bits" box which was looking a bit pitted but was otherwise fine. A bit of cutting and shaping with Harry Hacksaw and my trusty Dremel had it exactly how I wanted it. I cleaned up the connection and all seems to fit together nicely. I will drill the hole properly once the subframe and beam are off and the car's in the air.
I now feel like I am getting somewhere

Horrible nasty foam cloth

All scraped off and on the floor

Hoovered out (again...)

Aerial finally removed!

Aerial stub. I reckon that can be used again...


Handbrakes together, with very different mounting brackets...

Modified Mini handbrake with spacer and scratchbuilt bracket. Bolt is not the one I will be using!

Edited by MrBounce, 22 January 2012 - 04:17 PM.
#63
Posted 31 January 2012 - 05:16 PM
It was always my intention to get more than one quote and I chucked everything into the boot (except the camshaft) and headed off to see my preferred engineer. I spent a while chatting to him about my needs - he remembered me from when a friend and I had popped in for a couple of valves 10 years ago! He made some interesting discoveries when he looked at what was in the boot. The engine block itself is in pretty good nick; the cam bearings will need to be replaced and a rebore would be best as there are some rust marks (which I already knew about). He agreed with the other shop about the camshaft possibly needing just a polish.
The interesting details were the cylinder head and the flywheel. The head has definitely seen porting work - he thought it was a pretty good job - although the valves were still standard size. He thinks it had been set up for turbocharging (not my intention) as the chambers themselves were quite large. I had thought it was a standard low-compression Metro engine, but because the head has seen work it's likely it wasn't the original one. The flywheel was the non-verto item I had taken off the spare engine that came with the car. He took one look at it and told me it had been lightened. It's not superlight by any means, but is certainly not a standard weight.

I have explained what I am looking for and he'll give me quote later in the week. This means: rebore, new higher-compression pistons, polish crank (regrind if necessary), new bearings, thrusts and cam bearings and a bottom end balance. As an aside I am also looking to have the head changed to match with larger inlets (possibly bigger exhaust valves too), hardened inserts and having the inlet manifold matched to the ports. I think it's going to be expensive!!!
I have however discovered that my A+ Primary Gear has deep scoring on the inside and will need replacing. Why didn't I know this on Sunday when I was at Bingley??? As far as Bingley goes I picked up a few small items, including a roll of soundproofing, an A+ flywheel housing, a fuel gauge and a cheap steering wheel so I can sell the Astrali to someone who can mend it...
Dodgy A+ Primary Gear with deep scoring. I need a new one.


#64
Posted 02 February 2012 - 05:48 PM
Anyone who has used a standard Mini heater will know that the blower is rubbish. I have been given some suggestions to what I could do, one of which was to transplant a completely different heater into the car - not ideal as there's not a lot of space. I found my answer on a website where a guy has restored a GTM Coupe (http://www.ken555.plus.com/gtm/) - he changed the Mini Heater blower for one from a Ford Sierra. Some surgery is required - changing the fans over for one, but all in all it looks very doable, and I should be able to incorporate a multiple speed switch removed from something in a scrapyard.
I won a Sierra blower on eBay for 99p and proceded to remove it from its housing. It is slightly wider (once the double fans have been removed) but should fit within the housing with a little jiggery pokery. Getting the Mini fans off was easy - with a bit of WD40 they simply twisted off. The Ford fans were somewhat more difficult, but a bit of work with the Dremel had them on the bench. The next issue was the size of the spindles - the Mini spindles measure 6.5mm, whereas the Ford items were just over 8mm. Out came the drill and I gradually drilled out the centres to first 7, then 8mm. They went on with a little bit of persuasion, but unfortunately I wasn't concentrating and managed to destroy one. Luckily for me there was a spare from the other heater. I was a bit more careful with this one... I used the original blower mount, screwed to the remains of the Ford housing to mount it. Time ran out so it's yet to be finished, but a quick reassemble shows it still needs some work. More to follow...
Disgusting housing. Loads of road grime and old oil.

Something tells me there was an oil leak in there once...

Well it's a bit cleaner now, but needs more work.

Sierra Blower, from a Cosworth, allegedly.

Big fans vs little fans

Fans removed

Big spindle

Little spindle

In the Mini housing, still with most of the plastic Sierra housing attached

Using the Mini bracket

Broken fan. Oops...


Edited by MrBounce, 02 February 2012 - 05:51 PM.
#65
Posted 16 February 2012 - 11:29 PM
Haven't been in the garage much as although I have a heater, it's still been a bit chilly so have stayed inside. I did however manage to get some more funds for the project. Remember this?

The old wood-rimmed steering wheel (wrapped in electrical PVC tape when I got it) where the wood had split? The one I didn't particularly like anyway? Well I cleaned it up (it was an Astrali wheel & boss) and chucked it on eBay to see if anyone wanted it. 3 people did and had a bidding war. It eventually finished at £113, so that will help pay for the replacement fuel tank, if nothing else. More later

#66
Posted 01 March 2012 - 07:38 PM
Parts on workbench

I also have a new something for the engine bay. I won a big-valve cylinder head on Ebay after the winning bidder didn't read the postage details properly. He lived in Italy. I don't. I win. I love second chance offers


Here's the head!

#67
Posted 03 March 2012 - 05:05 PM
Meanwhile, back at the Manroom I still had that new-found enthusiasm so I set about removing all the glass. As all the rubbers are going to be replaced I had no qualms about using "my friend Stanley" whenever the need arose. The side 3/4 windows were first. A quick poke with a screwdriver removed the trim in the centre of the rubber then I cut down one side of the rubber. I was easily able to push it out; I then repeated this on the other side with equally successful results.
Next up was the rear hatch. This was secured by 2 bolts each side which go through the body into the higes on the outside. Let's just say I am probably good at the game "Snap"... All 4 bolts went but it did of course allow me to remove the hatch. I've taken the hinges off and will look at drilling out and retapping the threads where the bolt shanks currently sit. The hatch has been carefully stored by the fridge...
Moving swiftly on to the sunroof - I was on a roll! However, I needed to figure out how it was attached as it was not clear by any means. After some investigation I found the outer frame was screwed through the roof to little plastic triangular brackets, but firstly I had to remove the (knackered) seal on top of the screws, which was held in place by mastic. Amazingly, every single screw came out easily. And there were an awful lot of them! Once they were gone the frame simply lifted out. I had to use the scraper to get the remaining sealant off the roof. Nasty stuff. It will still take me AGES to remove asll the old mastic from the frame, but it will be done in due course.
And finally, on to the windscreen. Again, as there was no likelihood of me ever reusing the rubber (brittle, cracked and just plain nasty) I didn't call a friend. I simply ran a Stanley blade down the sides and over the top and gently pushed the screen forward. Perfect! I have put it somewhere where it can't get knocked for safekeeping. More later!
New swtiches & gauges. I will be losing the wood trim.

Side windows out - Offside...

...and Nearside

Hinge bolts conveniently all snapped...

...allowing me to remove the hatch easily.

How the hell do I get this out??

Screws hidden under seal and goo.

All screws out, ready to go...

...and GONE! Numerous screws visible.

Monumental pile of crap from the sunroof.

Split the rubber down the side, push the screen...

...and there it isn't.

#68
Posted 03 March 2012 - 06:13 PM
The plans for my Dads mk1 it to eventually turbo it, since my Dads owned it's got progressively slower, starting with a worked 1293 'S' engine, now to a asthmatic 998 (might be because I 'borrowed' it's engine


#69
Posted 03 March 2012 - 10:13 PM

#70
Posted 01 April 2012 - 05:14 PM
I had reached the stage where I couldn't really progress too much further without taking the car off its wheels; the question was: which end to start with? The car was purchased back in June last year, with previous owner Andy stating "Condition of Rear Beam is unknown". I had tapped it with a screwdriver (seemed solid enough...

First thing was first - I put the rear end on axle stands and set about undoing the main brake pipe to splitter union. Amazingly it undid after a hefty bit of pressure on the spanner, and a minor amount of fluid dripped on the floor. I also undid the unions on the flexi-pipes and took the splitter and pipes off entirely. The plan was to try to remove the beam and radius arms in its entirity.
Next up were the main bolts holding the beam to the heelboard. As it was just me working on the car, I had to make sure the bolts were clamped (I used Molegrips on the ones in the middle) and managed to jam a spanner on the top of each of the end bolts. The bottom end bolts were somewhat more complicated. Thankfully, one side was easy and the washer inside the car is "D" shaped, which allowed me to undo it without any issues at all. The driver's side however just turned and the only way I could get anything on the nut was to use the open-end of the spanner vertically above it; I needed to hold it there, which meant I couldn't turn the nut on the other end. Massive thanks to Mrs Bounce who had her first encounter with a ratchet spanner and coped admirably!
Next up were the nuts on top of the coilovers. Driver's side was a piece of cake. No issues at all. Other side? Hopelessly rusted solid. After several attempts to try to get them shift without any luck, I reached for the good old Dremel and cut them off. What the hell - they're being replaced anyway. I love Power Tools...
Using copious amounts of leverage with the "F" screwdriver and supporting the beam on the jack, I eased it off the car. I then removed one wheel and the coilovers and it was off. Inspection revealed it to have no more than surface rust. I am exceptionally happy about this and I actually believe it may have been replaced at some point as it appears in pretty good condition. I will strip it down, treat the rust and see what else needs reconditioning apart from the brakes. The radius arms, although rusty, are well-greased and look in fairly good order! Woo-hoo!
The beam - you're comin' off sonny!

Brake splitter - may need to be renewed...

Splitter and pipe now off.

Driver's side nuts no problem...

...but I had to resort to power tool violence with the other side.

Beam lowered

Coilovers off. I have no idea what they are as they're so rusty. Maybe I'll pressure wash them to find out?

One side with minor surface rust...

...and the other. I am a happy boy!!

#71
Posted 01 April 2012 - 06:31 PM
One of the projects on here I look forward to reading the updates on!
Makes a nice change from seeing panels welded on!
#72
Posted 01 April 2012 - 06:34 PM

My next task is sourcing a set of new coilovers and springs, ideally lowered, so the height can be dropped, aswell as sorting the rear beam out so toe/camber can be adjusted on it

#73
Posted 01 April 2012 - 06:43 PM
I'll take a look one day if thats ok.
#74
Posted 03 April 2012 - 05:48 PM
#75
Posted 06 April 2012 - 10:10 AM

Some bits have been replaced along the way but it's a long job...

1 user(s) are reading this topic
0 members, 1 guests, 0 anonymous users