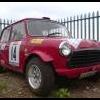
Sleeving Pushrod Holes
#1
Posted 06 July 2011 - 03:44 PM
#2
Posted 06 July 2011 - 03:55 PM
Hi, schoolboy error of breaking into the pushrod holes whilst porting my inlets the other day, I'm planning on sleeving them with 13mm steel tube, the holes are 13mm at the biggest points (both ends as they seem to get smaller diameter towards the middle) and just wanted to see what wall thickness I should use if people have done it before, I plan to locktite them in place once everything is done.
A lot of head porting experts used tyo grind away until they broke through, then bore and sleeve with a piece of steel tube. About 1.5 mm wall thickness is fine, so you would bore and ream the holes out to 16 mm for a snug fit. The 'Loctite' to use is the bearing locking stuff, can't remember the number and I've run out so can't check the bottle.
#3
Posted 06 July 2011 - 04:22 PM
#4
Posted 06 July 2011 - 07:19 PM
#5
Posted 06 July 2011 - 07:43 PM

#6
Posted 06 July 2011 - 08:35 PM
I have used this before, and silver soldered it in place.
http://cgi.ebay.co.u...em=120708771752
bearing fit to hold it in place and with a ball bearing about 5/8" diameter... CV one will do
tap it in the end of the tube to bell it out, do this both ends and it will lock in place, you may need to chamfer one or both holes first though....
Great thanks guys, that brass tube looks like it may do the trick along with locktite, 17/32 is about 13.5mm which should be fine, the 1/2" may even just fit so will test it out by drilling one through with a 12.5mm bit to see how it looks first.
Martin thanks for that- I was thinking of swaging the tops out slightly as a secondary restraint but forgot since I've been thinking about it again!
#7
Posted 06 July 2011 - 10:36 PM
#8
Posted 07 July 2011 - 03:29 AM

#9
Posted 07 July 2011 - 05:51 AM
#10
Posted 07 July 2011 - 06:35 AM
With a good sharp reamer you could take it out in one hit .... on a machine anyway

#11
Posted 07 July 2011 - 10:22 AM
1 user(s) are reading this topic
0 members, 1 guests, 0 anonymous users