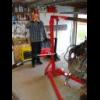
What Do You Need Tool Wise For Welding
#46
Posted 22 August 2011 - 01:24 PM
#47
Posted 22 August 2011 - 01:35 PM
This is a very good product that helps to produce a nice clean weld.
You can use CO2 pub gas as well (waiting for the flak) although the weld may not be quite as clean but i used it for a very long time with no issues what so ever.
Try this web site www.mig-welding.co.uk/forum/index.php there is info on there as to where you can get welding gas from.
#48
Posted 22 August 2011 - 02:43 PM

#49
Posted 22 August 2011 - 02:44 PM

#50
Posted 23 August 2011 - 08:00 AM

#51
Posted 23 August 2011 - 09:28 AM
#52
Posted 24 August 2011 - 02:54 PM
Also, just another silly question, is there any particular wire i should be using?
Personally i use .6mm wire although other people use .8mm. Due to the particular thickness of metal on the the mini which ranges from approx .9mm to 1.2mm the .6mm wire i find is more than enough.
And yes having a fire extinguisher to hand would be advisable but if you have removed all flammable items away then sometimes a damp rag will do.
Remember though before you start welding is to check underneath or behind where you are going to weld as there is nothing worse than ruining your interior or burning a wiring loom. Pay attention to the underside as well. You may only be welding a patch to the floor but under your floor runs the brake lines, battery cable and most important your fuel line.
Also if there is any sort of waxoyl, Bitumen etc this will ignite so pay careful attention to this.
Sealant is another area that can be very nasty as it gives off toxic fumes and believe me it will make you ill if inhaled. Try to remove all of it if possible even if it looks far enough away (i'm talking at least four inches away to be safe but don't forget the area you are going to weld gets hot very quickly)
#53
Posted 30 August 2011 - 12:00 PM
Does anyone have any suggestions where to get some sheet steel for practising and repairs? Internet or Warwickshire / west-mids based.
really helpful thread!!
cheers
Chris
#54
Posted 30 August 2011 - 01:39 PM
Thanks for all this information, its a great help. I think you've answered my first questions, which was what gauge are mini panels generally? 0.9 - 1.2mm? Have you got any suggestions for what MIG welder would do the job? It needs to be single phase, capable of running of 13amps (if possible) and need not be any more powerful than being capable of welding mini panels. I've had a look at there is a vast array of different specs etc, not really sure where to start.
Does anyone have any suggestions where to get some sheet steel for practising and repairs? Internet or Warwickshire / west-mids based.
really helpful thread!!
cheers
Chris
Hi Chris
there are numerous welders out there that would suit your needs but beware some have got poor feedback. Personally i would buy as a starter one of the Clarke range.
They are reasonably cheap, reliable, easy to use plus there are a lot of TMF members who use them myself being included.
I had a few issues to start with namely a damaged sleeve but once i found out the reason for the damage it has not missed a beat since.
I have the Clarke 135TE Turbo which i believe retails somewhere around the £250 mark although i have had mine for quite a few years now.
This runs happily on a 13amp single phase electrical system and has never overheated on me and i do thrash my welder on a regular basis.
If you do decide to purchase one of these i would recommend you ditch the small 1kg spool of wire it comes with or keep it as a back up and buy the larger 5kg spool. These you can obtain from any welders merchants. I bought my last reel from B.O.C.
As for wire size i personally use .6mm which is perfectly fine for what you need on a Mini as the metal is quite thin. If you were welding a lot of chassis's etc then .8mm would be better although i weld up to 1/4" steel with .6mm wire with no issues and get a decent weld especially at the highest setting.
As for obtaining sheet metal to practise with you could go to a scrappy and pick up a bonnet or any other large panel and practise on that to start with.
For sheet metal have a look in your local Thomson book or yellow pages to find some local machine / fabrication shops. These will have sheet metal and will normally sell you either a complete sheet which they will cut down to a manageable size or smaller sections.
I normally pick mine up from a place in Hailsham both 1.2mm and .9mm for about £30 to £40 a complete sheet.(a sheet is normally 4ft x 8ft)
Hope this helps
Neil
#55
Posted 31 August 2011 - 11:42 AM
thanks for all the advice
#56
Posted 01 September 2011 - 06:03 PM

#57
Posted 03 September 2011 - 04:16 PM
There are a whole list of do's and don't about the different types so i will not go into them. The main thing is DO NOT USE WATER GAS on a fuel fire or electrical fire. (if you want to find out more about them have a look at this website http://www.fireextin...herguide.co.uk/
Before you start welding on your car i always disconnect the battery and the alternator as a precaution. Any open fuel lines or tanks either remove or cover up.
Also remember when grinding sparks will fly everywhere so again fuel lines tanks etc loose paper or anything flammable will need to be removed or covered.
If you have a small fire in the car ie burning paint underseal etc then use a damp cloth. I always keep one to hand.
With regards to grinding, if your glass is still in the car the grinding dust will damage it along with welding spatter so be careful to protect any fitted glass.
You can buy welding shields but as for cost i'm not sure.
Oh and for us married chaps if you have upvc double glazing installed especially the white plastic variety grinding dust will embed itself and turn the white a nice shade of rust when it gets damp. Its a real sod to remove so think carefully about where you work.
(I'm fed up of my missus nagging me about it)
This is just a rough guide and is not meant as anything else.
And something else that has just happened to another member on this forum is NEVER grind or weld in the vicinity of a lead acid battery on charge. If its been charging for a while there is a chance there is sufficient hydrogen build up for an explosion to occur. Very lucky really it was on the drive and not inside a garage etc.
#58
Posted 14 September 2011 - 07:12 AM
12:-Power setting on a Clarke 135 TE Turbo, this setting is for pulse welding and seam welding on .8mm steel sheet
Is that really 8m m steel? Where is that likely to be found on a mini? Or is it a typo

Very good source of information though

H
#59
Posted 14 September 2011 - 11:05 AM
Is that really 8m m steel? Where is that likely to be found on a mini? Or is it a typo
Very good source of information though
H
I think its 0.8mm
#60
Posted 14 September 2011 - 04:34 PM
Edited by AndyMiniMad., 14 September 2011 - 04:35 PM.
1 user(s) are reading this topic
0 members, 1 guests, 0 anonymous users