1:- 4 1/2" angle grinder, straight cut tin snips, stainless steel cutting disc 1mm, standard metal cutting disc, standard metal grinding disc, twisted wire cup (please note there should be a guard fitted to the angle grinder.)
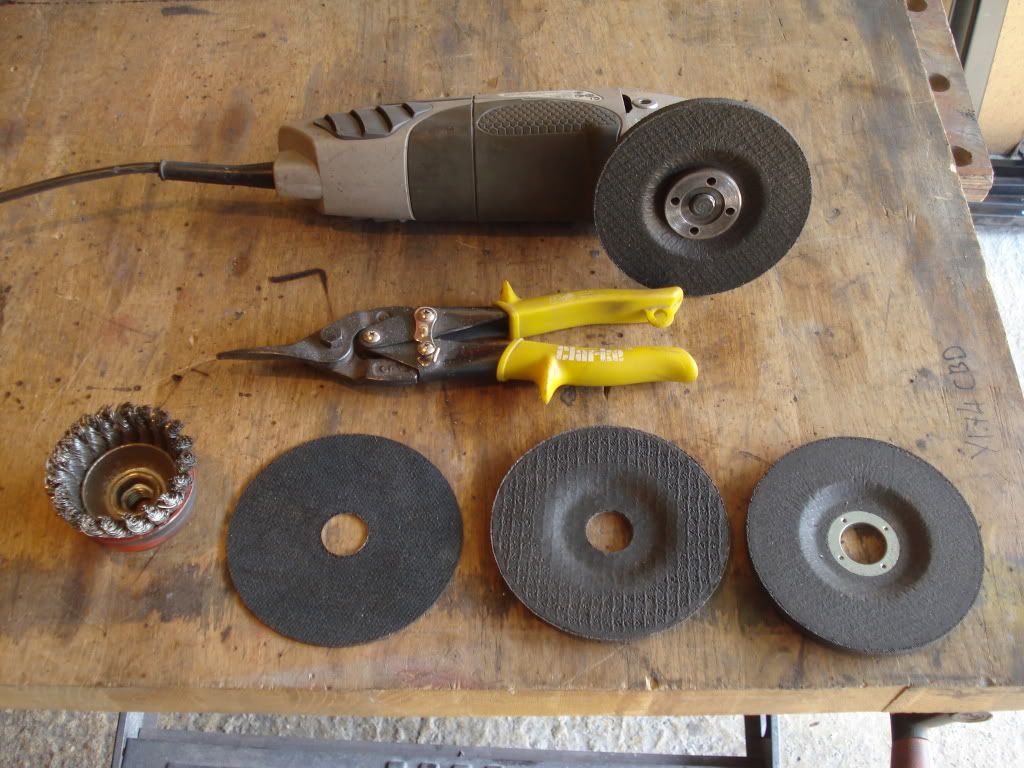
Close up of the various disc's
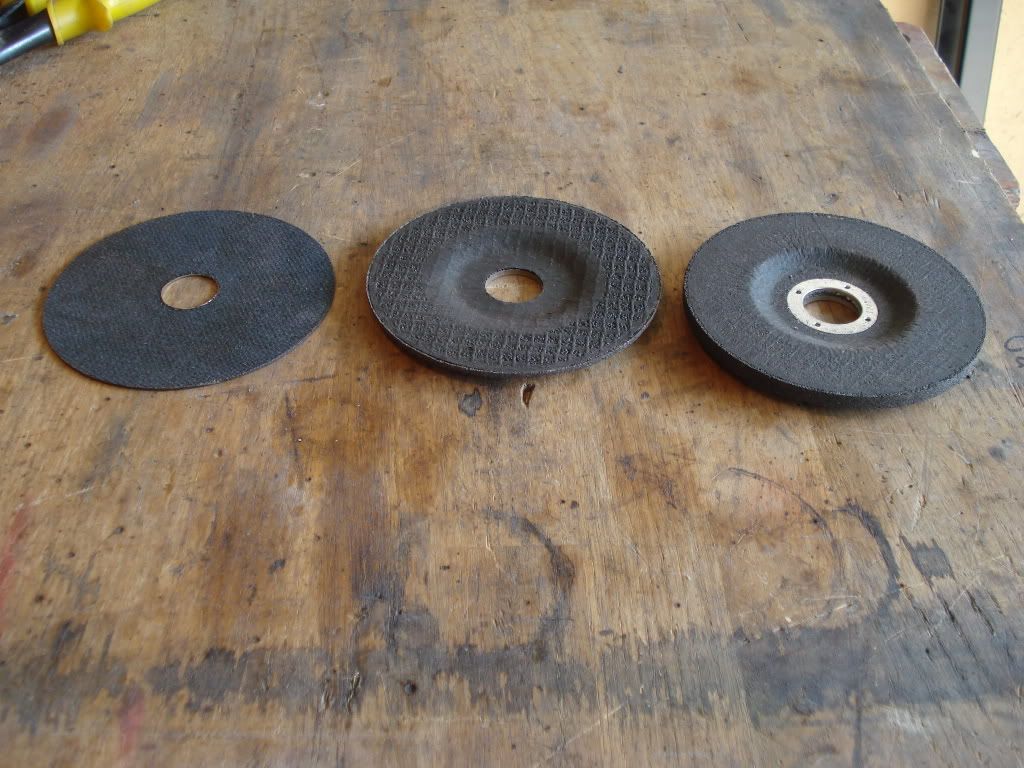
Forgot to add this a Flapper disc less intrusive than a grinding disc
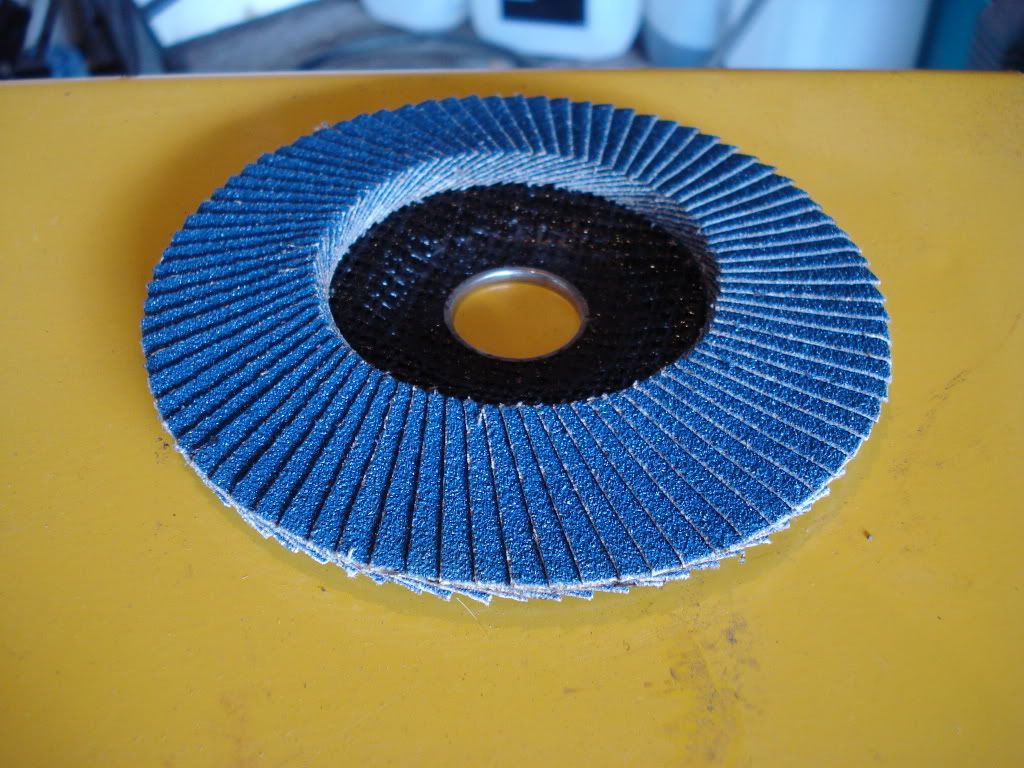
2:- Air driven tools, Straight drill, pistol drill, right angled grinder, straight grinder, small air file.
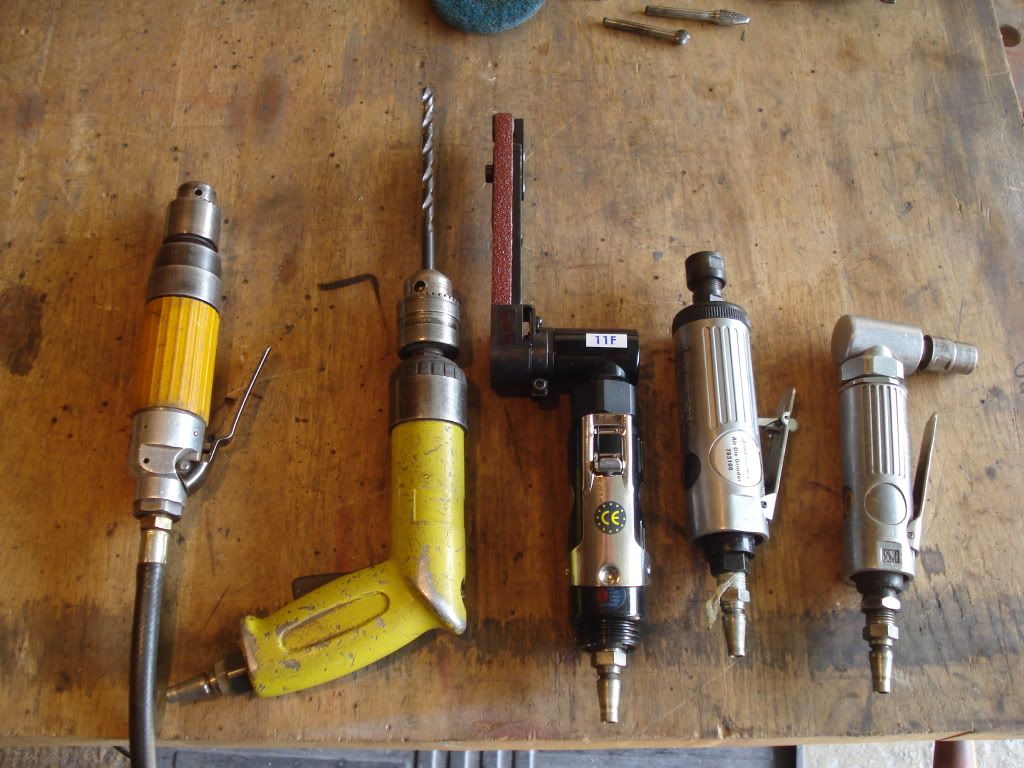
3:- Grinding burrs, 3" and 1" Roloc holders, 3"cutting disc holder and disc, skin pins 1/8th and 5/32, Cleco pins, 1/8th, 5/32, Cleco pliers, inter grips.
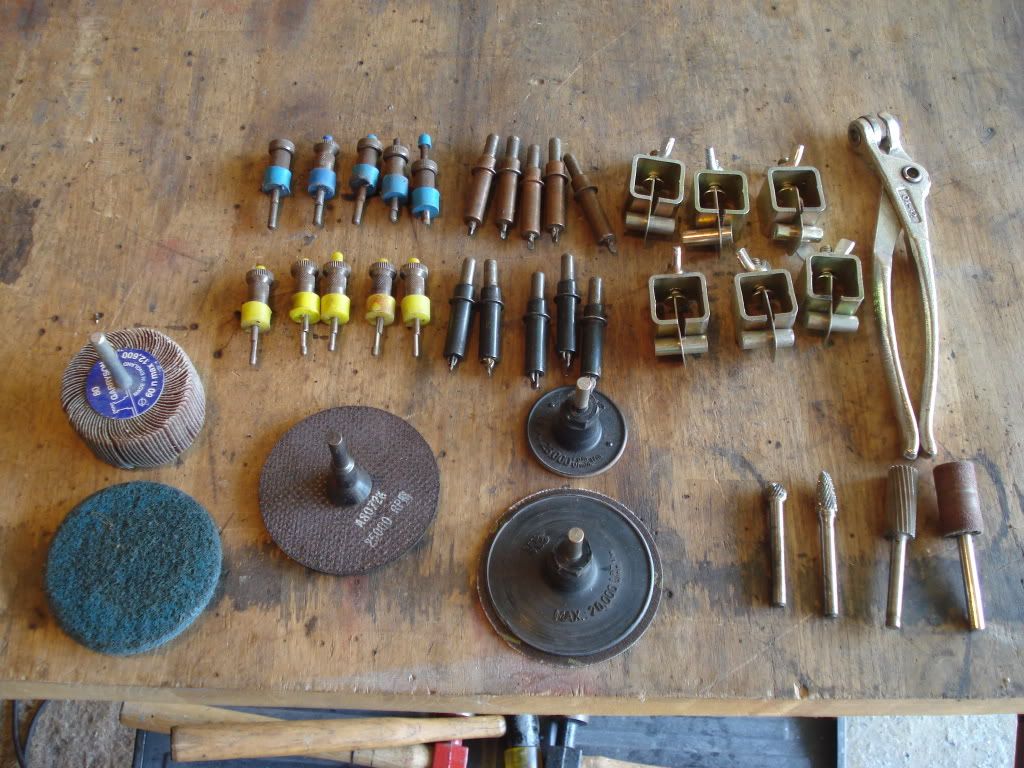
4:- Clamps various, 'C' clamps small and large, mole grips, welding clamp.
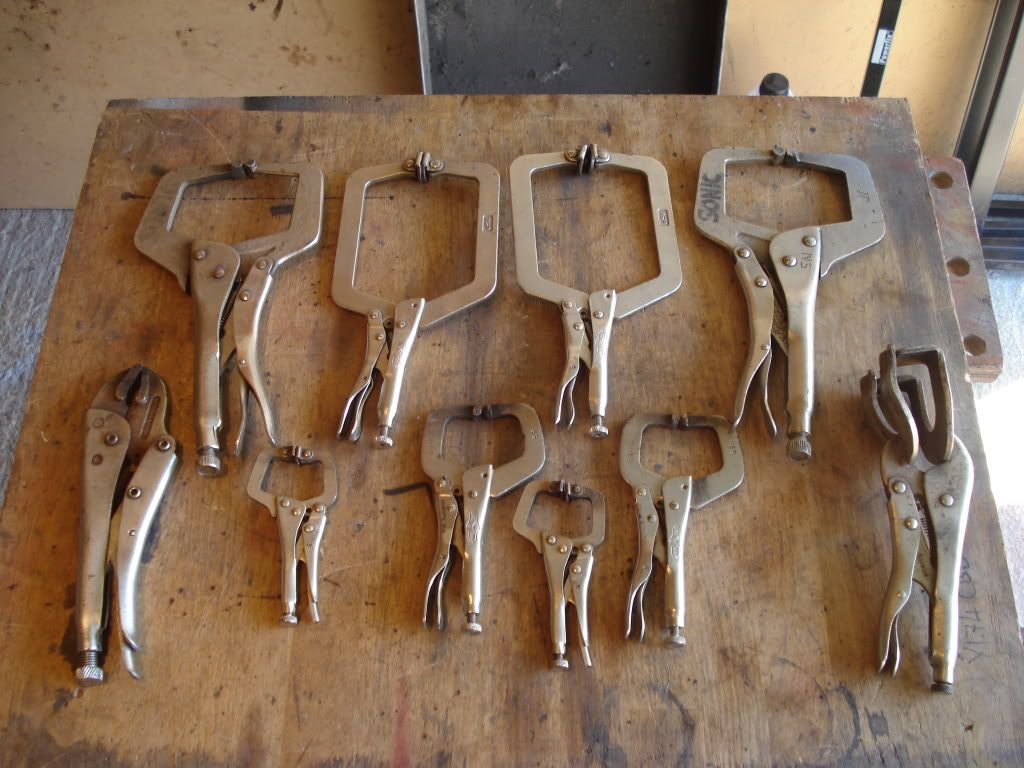
5:- Hammers various, door skin/ A panel flange folding tool, hole punch / joggling tool, various dollies.
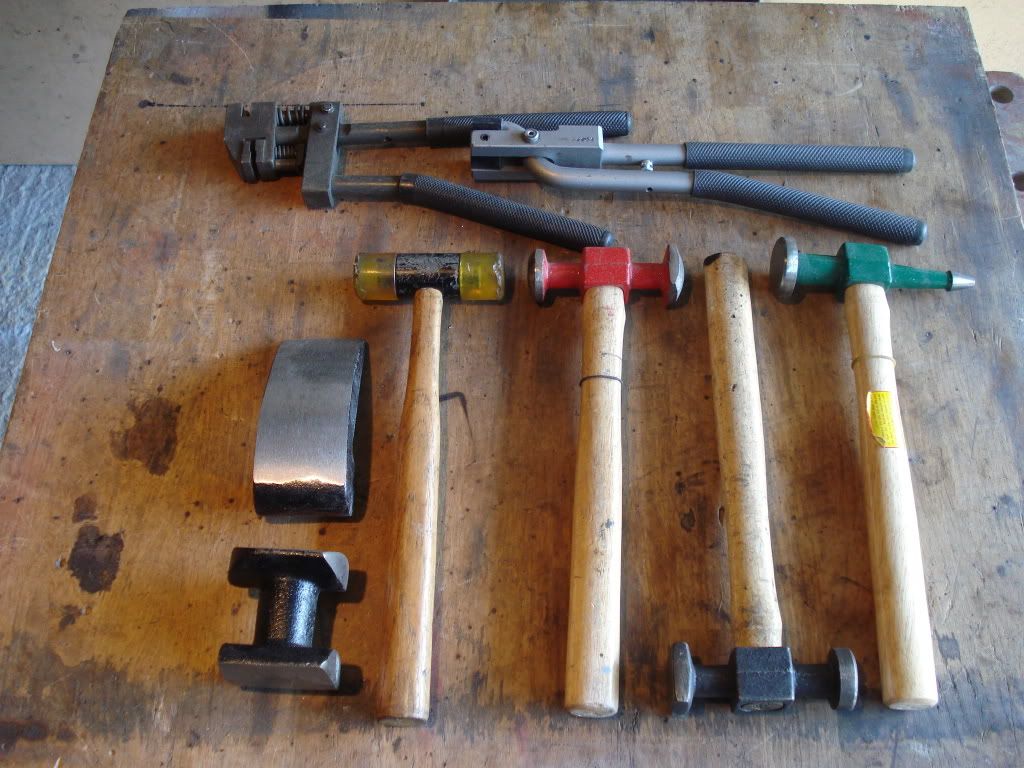
6:- Eye and ear protection, Reactive welding mask.
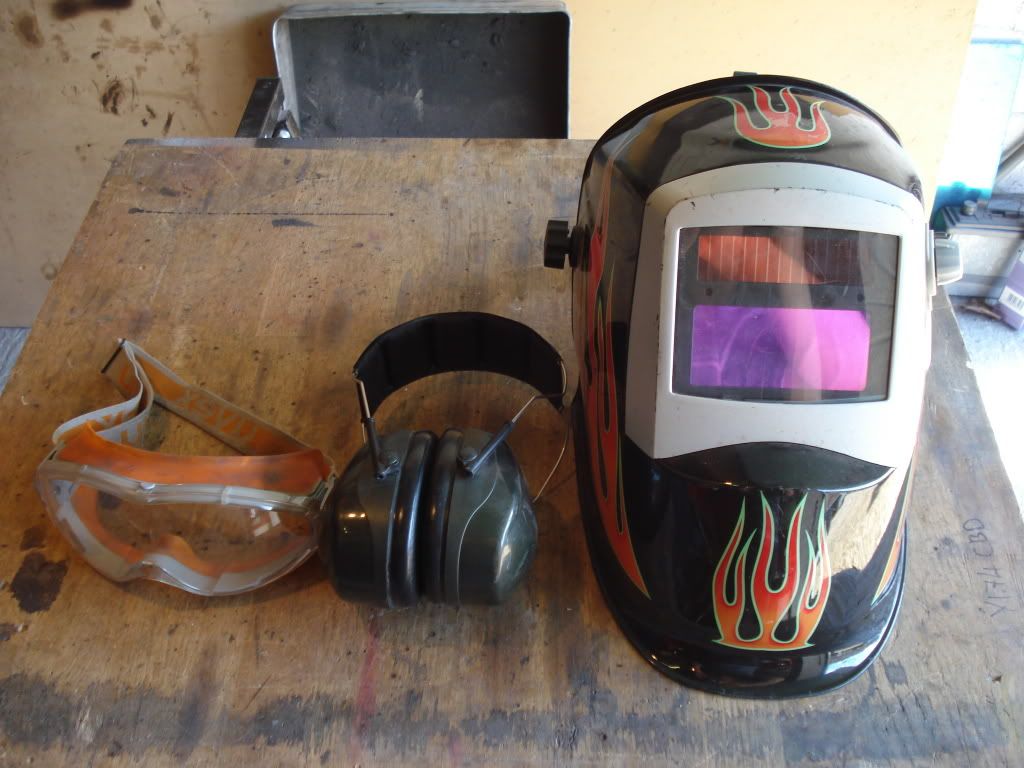
7:- Joggled edge on steel plate, ideal for doing small insert repairs to door skins, wheel arches etc
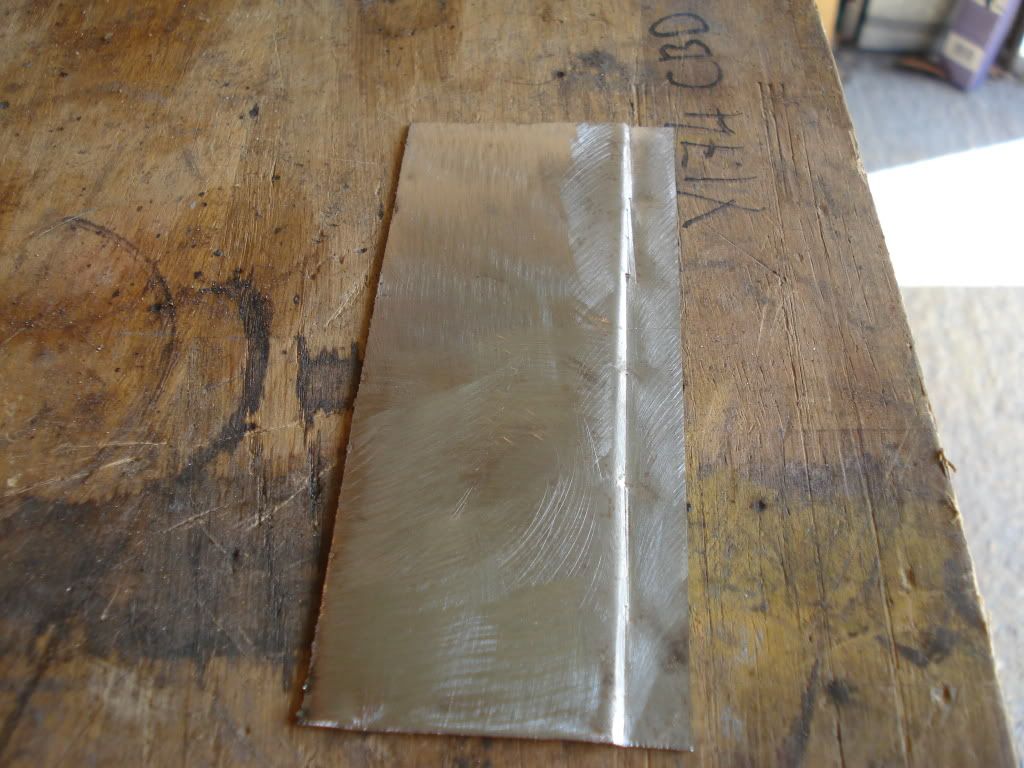
Joggled piece with new section laid in place creating a flat surface
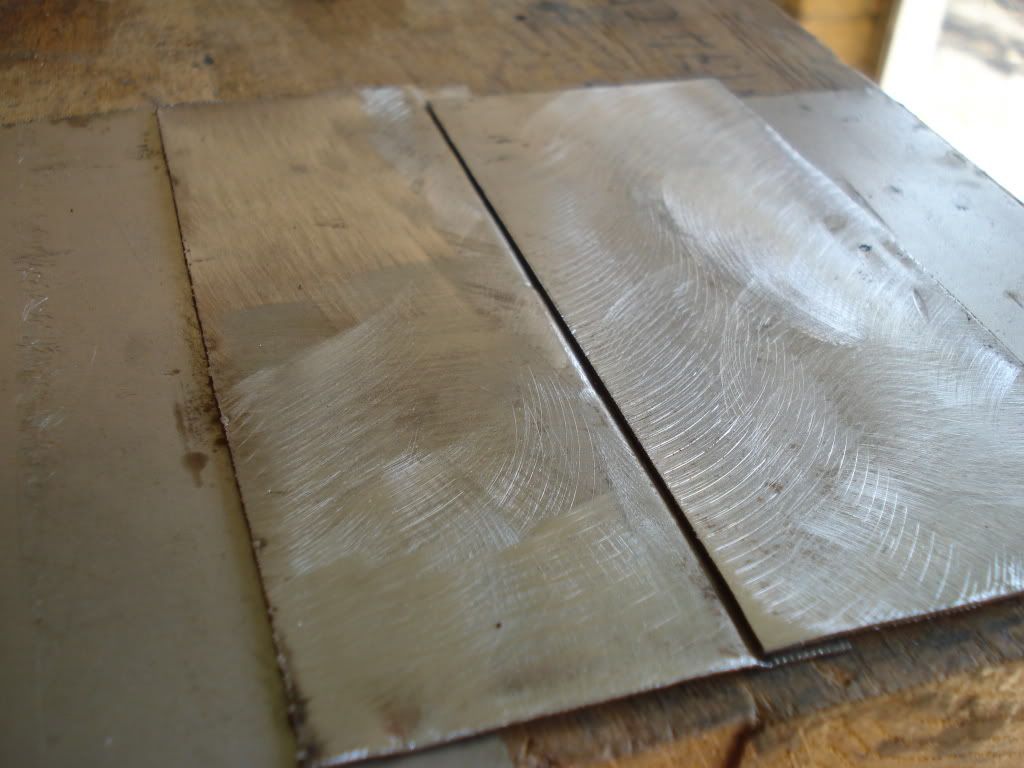
8:- Tack welding using Inter grips to clamp the two pieces. One tack every inch.
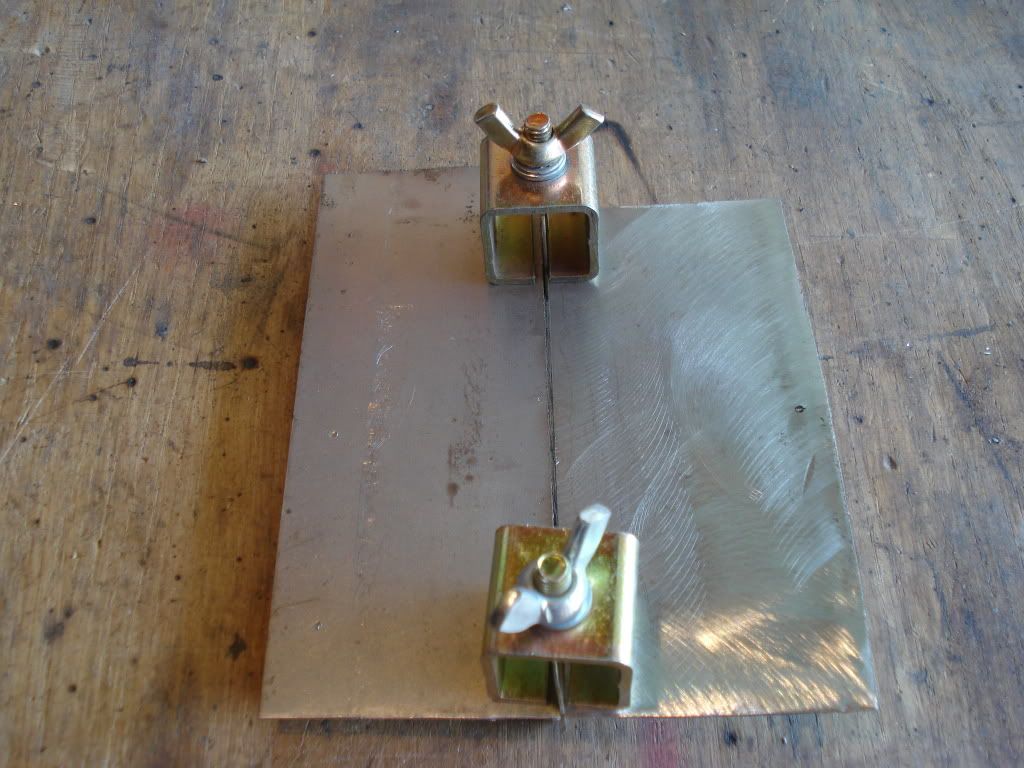
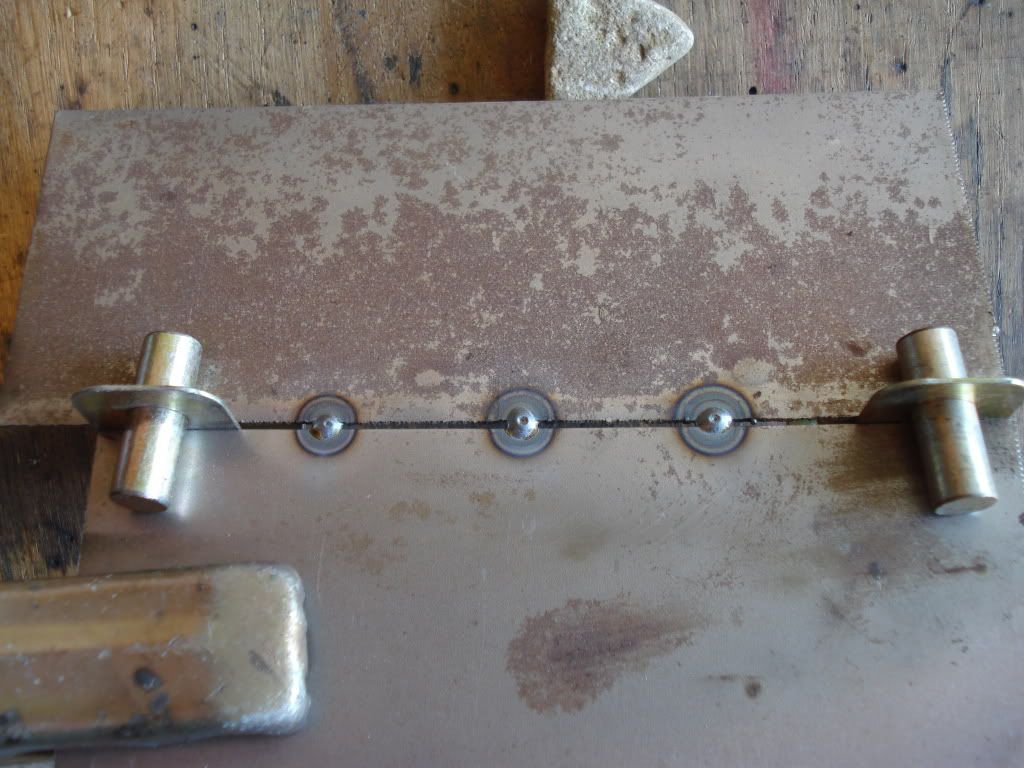
Edited by sonikk4, 01 July 2011 - 03:26 PM.