
Midland Wheels, And Just Cracked My Windscreen On A Drive!
#16
Posted 24 April 2011 - 03:50 PM
#17
Posted 24 April 2011 - 03:59 PM
What wheels are you exactly having trouble with and whats the problem with the tyres?What tyres are you trying to fit etc?
There 6x12 rally special wheels with yokohoma A539 165/60/12r
on alloys of that sort of size there is a groove in the middlish of the rim so the tyre sits in there to get it closer to the lip on the opposite side of they alloy so the wheel can get over the lip, however everyone that tried to fit the wheels said that groove is simply not deep enough to get the tyre anywhere close to going over the lip of the alloy, when we got back to the mini specialist we got an original alleycat wheel out and the groove on this wheel was about 1/2 to 3/4 of an inch deeper, the alloy wheel size were 6x12 and the tyres going on where 165/60/r12 which is the correct size, hope you can gauge what I mean from this description we even tried the trico of turning the wheel face side down and trying to mount the tyre from the backside etc etc we tried tyre bars and it was not even coming close to getting onto the alloy any harder and the tyre was going to rip, the machine turning the alloy putting the tyre on stopped and jammed because even the machine did not have the power/strength to turn the wheel any more because of how tight the tyre fitting made it.
Edited by speedy19902006, 24 April 2011 - 04:01 PM.
#18
Posted 24 April 2011 - 04:15 PM
in the end i had to ebay my wheels to get some of the cash back from buying them, which i know isnt right, but the guy i sold them to was going to MWS for new tyres anyway so they can get the tyres fitted for him.
i would also like to point out that the tyre machine you say they described on the phone, sounds just like all machines to me. 3 arms that clamp the rim (underneath) and an arm that pulls the bead of the tyre over the rim. if you get down there and have the tyres fitted ask to see this amazing machine and if you can take pics of it, as i would love to know how they do it!
i cant understand how any machine could fit a tyre to their rims, the bead of the tyre has a steel braided "hoop" which no matter what you do, doesnt stretch! if the well in the rim is not in the right place, the braid wont go around.
and finally i ahve heard from a few people who have had tyres fitted by them and still had problems after, involving bulges in tyre walls and even blowouts with tyres coming out the bead and scrapping the wheel, and all that within days of having them fitted.
MWS, how do you keep getting away with selling wheels with these design faults?
#19
Posted 24 April 2011 - 04:20 PM
i had this problem with MWS 6x10 ultralite ripoff wheels, no one could get tyres on in my area, and yes it is due to the position of the "well" inside the rim, it should be offsett to the rear (on this particular rim anyway) so that the tyre can be fitted, huddersfield ultralites however have a correctly positioned well which i noticed on a friends wheels.
in the end i had to ebay my wheels to get some of the cash back from buying them, which i know isnt right, but the guy i sold them to was going to MWS for new tyres anyway so they can get the tyres fitted for him.
i would also like to point out that the tyre machine you say they described on the phone, sounds just like all machines to me. 3 arms that clamp the rim (underneath) and an arm that pulls the bead of the tyre over the rim. if you get down there and have the tyres fitted ask to see this amazing machine and if you can take pics of it, as i would love to know how they do it!
i cant understand how any machine could fit a tyre to their rims, the bead of the tyre has a steel braided "hoop" which no matter what you do, doesnt stretch! if the well in the rim is not in the right place, the braid wont go around.
and finally i ahve heard from a few people who have had tyres fitted by them and still had problems after, involving bulges in tyre walls and even blowouts with tyres coming out the bead and scrapping the wheel, and all that within days of having them fitted.
MWS, how do you keep getting away with selling wheels with these design faults?
Your explanation was far better than mine, If I do get tyres fitted I will try and get pictures of this machine thats special, however this does go back to my points I outlined if it is a special machine before you buy on the site its should state on the site that their is special requirements for this products thus because there is not it warrants any contract of sale void.
#20
Posted 24 April 2011 - 04:41 PM
In the end I returned the wheel tyre combo and got the correct tyre fitted at my expense both ways £30. When they returned the tyre the F*** thing was on the wrong way round so I had to pay again to get the tyre correctly fitted. Kwik fit didn't have any problem turning the tyre and fitting though so that's good.
Never use them again and certainly would never recomend them to anyone for anything
David
#21
Posted 24 April 2011 - 04:45 PM
i wouldnt buy wheels from them though. and the aftersales service is just pants. they must get called at least once a week about this problem as it seems to happen on all their wheels? particular;y the deepdish ones
#22
Posted 24 April 2011 - 08:58 PM
#23
Posted 26 April 2011 - 07:16 AM

#24
Posted 27 April 2011 - 05:32 PM
http://i1214.photobucket.com/albums/cc494/speedy19902006/photo.jpg
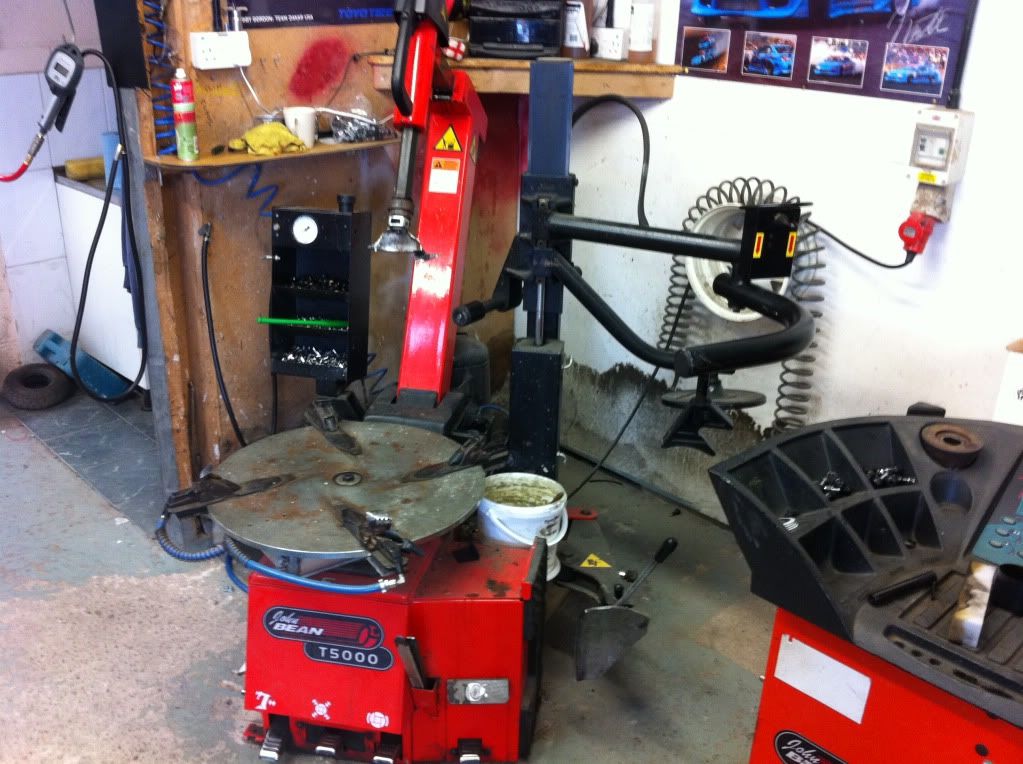
Cheers
Craig
Edited by speedy19902006, 27 April 2011 - 05:39 PM.
#25
Posted 27 April 2011 - 06:49 PM
as i said before, it doesnt matter what machine you have, it doesnt change the fact that the steel braid in the bead of the tyre isnt long enough to reach from the well in the rim to the outer edge of the rim during fitting.
even though they fitted your tyres for you on their "special brand new/3 year old" machine, i would still inspect the side walls on your tyres fairly regularly as i have spoken to folks who still ended up with bulges in the inner wall and even blowouts from the bead failing.
the "duck egg" in the side wall comes from the bead ripping and the braid in the bead failing, then it cant hold the pressure inside and you get the bulge.
MWS? no thanks.
Edited by cradley-heathen, 27 April 2011 - 06:50 PM.
#26
Posted 27 April 2011 - 06:54 PM
that machine is exactly what i thought it would be, thats the same machine the garages near me used when they tried to fit them!
as i said before, it doesnt matter what machine you have, it doesnt change the fact that the steel braid in the bead of the tyre isnt long enough to reach from the well in the rim to the outer edge of the rim during fitting.
even though they fitted your tyres for you on their "special brand new/3 year old" machine, i would still inspect the side walls on your tyres fairly regularly as i have spoken to folks who still ended up with bulges in the inner wall and even blowouts from the bead failing.
the "duck egg" in the side wall comes from the bead ripping and the braid in the bead failing, then it cant hold the pressure inside and you get the bulge.
MWS? no thanks.
cheers for the heads up mate I will do, don't worry I'm still very wary of using them I will run them and keep a very close eye. Any idea how long it took for the problems to happen or should it be apparent quite quickly?
#27
Posted 27 April 2011 - 07:51 PM
Where are they getting these duff wheels from?
As I said in an earlier post I got a set from them last year and haven't had a problem (two different centres has fitted tyres without any hassle).
Maybe I was lucky.
Mine are the John Brown ones if that makes a difference.
#28
Posted 27 April 2011 - 08:11 PM
Edited by samsfern, 27 April 2011 - 08:15 PM.
#29
Posted 27 April 2011 - 08:18 PM
#30
Posted 27 April 2011 - 08:41 PM
Edited by samsfern, 27 April 2011 - 08:46 PM.
2 user(s) are reading this topic
0 members, 2 guests, 0 anonymous users